Gear Hobbing Service by Xometry
High-quality Gear Hobbing Services in Days Not Weeks | Free Standard Shipping on All US Orders | Subject to availability. Xometry doesn't guarantee that we can provide this service at any given time.
Xometry offers the highest quality gear hobbing services and can deliver the full spectrum of tooth profiles, engagement forms, and ratios, custom-made to precisely fit your needs. Xometry gear cutting services specialize in the CNC manufacturer of gear “blanks” and the precision cutting and shaping of gear teeth on them, to create functional gears for your application. Our gear-cutting services employ the most appropriate techniques to create your required gear teeth, with the intended profile and dimensions.
Hobbing is a gear-cutting procedure that utilizes a cutting tool with multiple cutting edges (the hob) to “extract” the gear teeth from the blank. The hobbing progressively cuts the rotating gear blank, gradually forming the teeth profiles by material removal. Common tooth profiles include: spur gears, helical gears, bevel gears, and worm gears. Each tooth profile has unique characteristics and is suitable for different types of motion and power transmission requirements.
What Is Gear Hobbing?
Gear hobbing is a commonly utilized gear-cutting process that involves the use of a hobbing machine and multipoint hobbing-cutting tools to create precise and repeatable pinion teeth. It is an efficient and precise method for producing cylindrical, spur, screw, and helical gears.
The gear hobbing process starts with a hobbing machine. This consists of a rotating spindle that holds the gear blank (the workpiece) and a hobbing tool mounted on a movable carriage that runs perpendicular to the axis of the gear blank (for spur gears) or at the required engagement angle (for bevel gears). This rotating tool can be fed along its axis, along the radial axis of the blank, or in cooperating feeds on both axes, depending on the complexity of the required tooth forms. For screw gear teeth and curved bevel gear teeth, more complex relationships apply between the blank rotation and the hobbing rotation. Hobbing tools exist off the shelf for all standard gear profiles, and they are selected based on the gear type and specifications—particularly tooth size, tooth profile, and helix angle.
Types of Gear Hobbing Processes
The types of gear hobbing processes are listed below:
- Hobbing With Axial Feed
- Hobbing With Radial Feed
- Hobbing With Tangential Feed
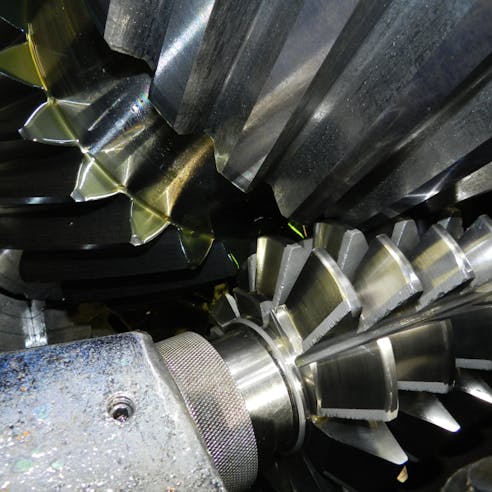
Hobbing With Axial Feed
Hobbing with axial feed is a type of gear cutting that uses a hobbing machine to cut gear teeth by feeding a hobbing tool axially along the outer face of a rotating gear blank. This process is commonly used for the production of cylindrical spur gears. It is simple to set up and operate, and it delivers high accuracy.
Axial-feed hobbing is the most widely used method for the manufacture of gears, as the great majority of demand is for basic, straight-toothed (non-helical) spur gears. It allows the output of gears with accurate tooth profiles, and the process is suitable for various gear types, sizes, and applications. This technique is commonly used in industries such as: automotive, industrial machinery, and aerospace. It finds application at a wide range of scales, from watchmaking to heavy equipment like steel bars and plate rolling mills.
Hobbing With Radial Feed
Gear hobbing with radial feed is a gear-cutting process that involves using a hobbing machine to create gear teeth by feeding a hobbing tool radially into the rotating gear blank. This method is commonly used for the production of gears with helical or spiral tooth profiles such as worm gears. This is also generally a cyclic process in which the radial offset of the hobbing gear is progressively reduced in multiple passes. Alternatively, the axial feed of a tapered hobbing tool will allow a progressive creation of the full tooth profile/depth.
Radial feed gear hobbing is a specialized method primarily used for producing gears with helical or spiral tooth profiles. These profiles are more common in high-speed gear systems and those in which meshing noise is considered a problem, facilitating the use of more costly tooth forms that alleviate the issue. The process finds applications in industries such as: automotive, aerospace, and machinery manufacturing—whenever gear noise and operational efficiency are critical factors.
Hobbing With Tangential Feed
Hobbing with tangential feed involves using a hobbing machine to create gear teeth by feeding a hobbing tool at a tangent into the rotating gear blank. This method is also used for cutting teeth on a worm wheel. In this mode, the hobbing is held with its axis horizontal and rotated to the desired angle toward the axis of the blank. The specialist hobbing tool for this method has its teeth oriented to compensate for the angle of attack of the tool axis, so the progressive feed in toward the axis of the blank produces tooth forms and profiles that are concentric with and perpendicular to the rotating axis of the blank. The hobbing is set at full depth of the final cut and then fed forward axially, to progressively cut the full tooth depth. The hobbing is fed tangentially to the face of the gear blank.
Gear Hobbing Materials
A wide spectrum of materials are used for gear manufacture. Some examples are listed below:
- Cast Iron
- Ductile Iron
- Aluminum
- Stainless Steel
- Steel and Alloy Steel
- Bronze
- Brass
- Titanium
- Magnesium
- Weldments
- Plastic
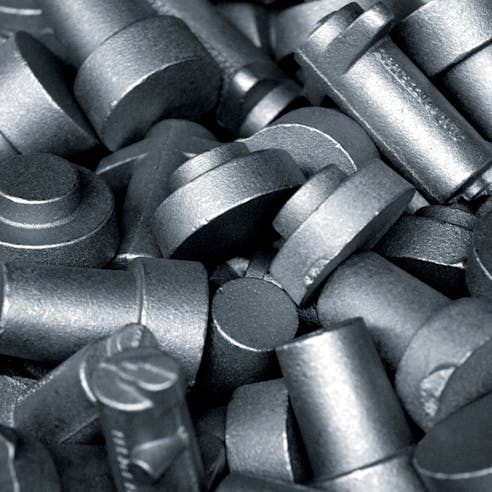
- Cast Iron: In its most basic type, gray iron can be cast and machined into high-quality gears. The application of cast iron is an alternative to phosphor bronze, as long as the material’s magnetic field is not an issue. Gray-iron castings are low-cost to produce and can deliver the complete net shape of the gear. Cast iron is selected for relatively low-speed and well-lubricated applications, offering low-cost and moderate wear properties.
- Ductile Iron: Ductile or nodular cast iron offers all of the advantages of gray cast iron, with improved toughness and wear properties—at a slightly higher cost.
- Aluminum: Aluminum alloys are a widely used option in applications that demand a high strength-to-weight ratio. They suit lower-stress applications or require exotic alloys and heat treatments to improve strength and wear properties. Passivation and anodizing also improve wear properties, by impinging a very hard and resilient coating onto the parts.
- Stainless Steel: 303 stainless is the most commonly used for gear manufacture. The alloy composition (of 17% chromium and 1% sulfur) allows tooth surfaces to be as-machined for many applications, offsetting some material costs by reducing finishing processes. For improved corrosion resistance, 316 alloy is a common choice. Both alloys are used for bevel, helical, and spur gears.
- Steel and Alloy Steel: A range of steel alloys and tool steels are used whenever high strength, wear resistance, and high speed are required. Steel alloys with additions of cobalt, molybdenum, tungsten, and/or vanadium benefit from greater heat resistance and durability than basic steel.
- Bronze: Bronze is generally more abrasion-resistant and rigid than brass, offering better corrosion resistance and improved dimensional stability. Phosphor bronze introduces phosphorus into the alloy, which serves to further improve wear resistance and the stiffness of the alloy. This increased resistance makes phosphor-bronze alloy an excellent choice for gear components in higher friction applications. Worm wheels are often made from it, as the part will better resist the wear generated by the higher friction of worm action.
- Brass: Gears generally made from brass alloys are spurring gears, and gear racks that will be used in low-load environments such as instrument drive systems. These have the benefit of being self-lubricating, making them well-suited to dry running in clean environments, where oil contamination may be an issue.
- Titanium: “Surgical” grade titanium stainless steel alloys are more practical and hard-wearing for gear manufacturing. These are low-titanium alloys that benefit from increased corrosion resistance.
- Magnesium: Magnesium offers only one major advantage in gear manufacture—its low density can serve to improve some specialist applications. Its terrible creep resistance above 200 °C and high wear-susceptibility make it unsuited to any but weight-critical and very short life components such as the gear trains in chemical propellant rocket engine fuel pumps, whose life span is measured in tens of seconds and whose weight is absolutely critical.
- Weldments: The manufacture of gears from weldments can allow optimized use of materials in the various components of the gear, rather than the compromise of one material for all parts.
- Plastic: Thermoplastics are a great choice for gears in circumstances where either weight or quiet running are the most important criteria. One of the more common gear thermoplastics is acetal (POM, polyoxymethylene). POM offers high strength and great dimensional stability over wide temperature ranges; it has a low coefficient of friction and excellent resistance to creep. For applications subject to shock loading, Nylon 6/6 shares many of the properties of POM and offers greater elasticity under sudden impacts.
Benefits of Gear Hobbing
The benefits of gear hobbing are listed below:
- Cost Effective
- Fast and Continuous
- Lower Production Cycle Time
- Wide Capability
- Variety of Batch Sizes
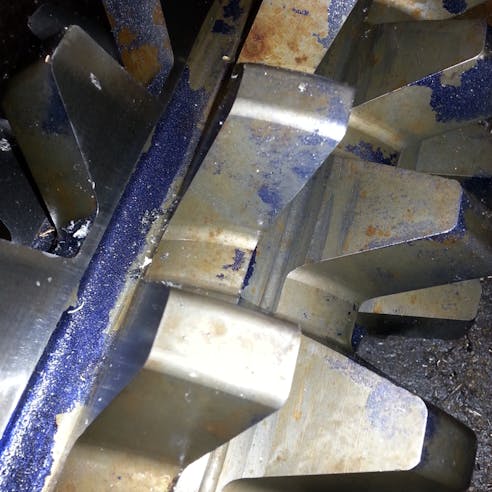
Cost Effective
The equipment to perform gear hobbing is relatively simple and low-cost, and even when CNC-controlled, the machines are easy to set up and run. Though the cutters used in gear hobbing are relatively expensive, they have a long usable life as they respond very well to sharpening (when made from steel). The class adapts well to the use of carbide inserts, bringing them up to date in cutting-edge terms.
Fast and Continuous
Gear hobbing is a quick turnaround process that can be automated for large-volume mass production and near-hands-off operation. Multiple blanks can be set up on a single machine axis, allowing true mass production—a technique that is nearly as old as gear hobbing itself.
Lower Production Cycle Time
Individual cycle times are generally shorter than for most alternative processes for tooth cutting. The stacked machining of multiple blanks immediately amplifies this productivity.
Wide Capability
The process is extremely flexible, so the same basic tools can switch from a simple iron spur gear to an aluminum bronze davit gear in a brief reset. All materials and a wide range of sizes, tooth profiles, and tooth-form options are simply setup variations on the same equipment, using the same skills.
Variety of Batch Sizes
Hobbing of gears is good for one-off or mass production using the same or very similar setup/equipment. The only requirement for large volumes is longer axis motions and capacity for a long stack of blanks.
In need of custom gear hobbing services?
Drawbacks of Gear Hobbing
The drawbacks of gear hobbing are listed below:
- Bevel Gears Limitation
- Size Limitations
- Difficult To Produce Internal Gears
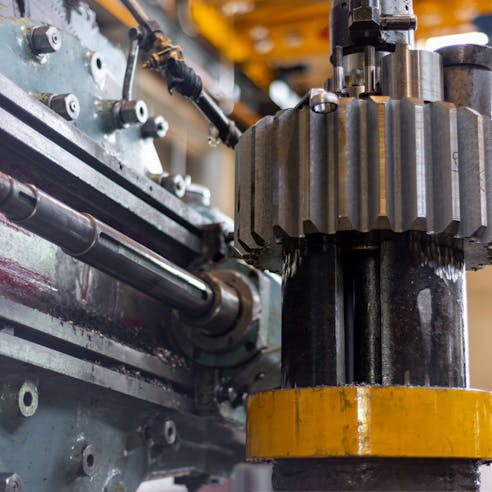
Bevel Gears Limitation
Episinoid bevel gears (with curved teeth) are a little harder to make by hobbing, so a single-tooth and indexing approach is common. In the 1920s, Klingelnberg Germany introduced the Palloid cutting method, using continuous processing and a tapered hobbing tool. Indexed, single-tooth machining is still widely used for bevel gears with curved teeth.
Size Limitations
For larger gears, the equipment for hobbing becomes impractically large, making an indexed, single-tooth process lower cost. It’s also worth considering that hobbing is best adapted to larger production runs of smaller components—and very large gears are rarely required in high volumes.
Difficult To Produce Internal Gears
Hobbing is unsuitable for the internally toothed gears that are increasingly common in epicyclic gearboxes. These are often manufactured either by CNC machining or indexing broaching processes.
Gear Hobbing Applications
The wide-ranging use of gear hobbing and the processes derived from it mean that most forms of gear, used in most industries, can be made in high volume, at restrained costs, by hobbing. Listed below are some of its applications:
- Sprockets
- Spur Gears
- Cycloid Gears
- Helical Gears
- Splines
- Worm Gears
- Involute Gears
- Ratchets
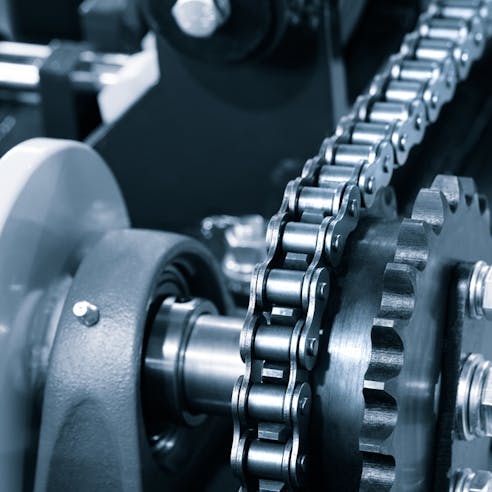
Sprockets
Sprockets are chain-drive components that are important in a wide range of applications in transport and power delivery. The tooth profiles on motorcycle and bicycle sprockets are suited to hobbing manufacture.
Spur Gears
Spur gears are widespread; machines that don’t use them are in the minority. Typical applications for hobbing cut spur gears are in the gearbox of a car, in which most of the pinions will be hobbed.
Cycloid Gears
Cycloid gears (as opposed to “normal” involute gear profiles) often use non-traditional tooth profiles such as sinusoidal shapes. These profiles lend themselves well to hobbing when the cycloid gear is external. They require particularly high tolerance manufacture but this is within hobbing capability. Cycloidal gears offer lower friction and wear on the tooth flanks due to their rolling engagement resulting in lower Hertzian stress at the tooth contacts. Great torsional stiffness and resilience to shock loads make them ideally suited to heavy industrial applications such as plate and bar mill drives.
Helical Gears
Helical gear profile is well-suited to several detailed variants in hobbing, and they’re made in a wide selection of materials. Helical-cut gears are used in automotive and other power transmission applications which require quiet and efficient power transfer.
Splines
Splines are a specialist variety of gear, though often not used as “gears” but as sliding engagements in power transmission systems in which some driveshaft length variation must be accommodated. Car and truck prop shafts typically have a spline-based sliding joint, to allow for suspension movement.
Worm Gears
Worm gears are used to deliver very high gear ratios in a compact space. Both parts of the gear pair can be made by hobbing. Common applications for worm drives are in printer paper-feed mechanisms and in automotive windscreen wiper motors.
Involute Gears
Involute gears have a particular tooth profile that manages the contact between two mating involute gear teeth that move along a fixed plane of contact, even when the center-to-center distance of the gears changes. Involute gears can handle center shifts or manufacturing run-out, and they allow greater assembly flexibility. Involute tooth profiles are common in many applications, such as automotive gearbox parts.
Ratchets
While ratchets are not strictly gears, they are often made by hobbing and share many characteristics of spur gears. Ratchets are used extensively in tie-downs and tensioners, for example in fence and power transmission wires.
Alternatives to Gear Hobbing
Xometry offers a wide range of processing options that can have gear manufacture applications;
- Shaping
- Broaching
- Gear Milling
- Gear Grinding
- Wire EDM
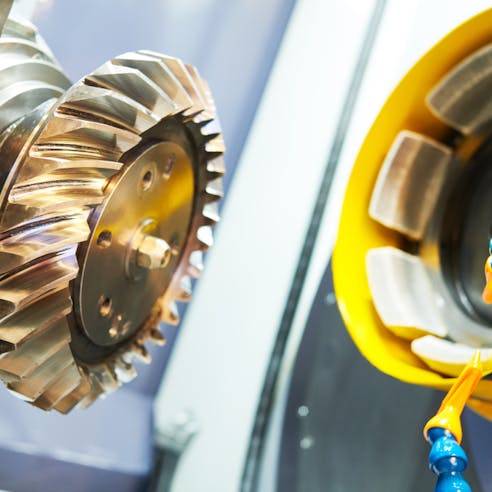
- Shaping: Shaping is the process whereby a linear moving tool, operated by a shaper, cuts gear teeth one at a time. The gear blank indexes as required and the shaper machine moves the cutting tool to plow the profile of each tooth.
- Broaching: Broaching involves using a specialized, elongated broach tool to cut gear teeth in a single pass. The broach has a series of incrementally larger cutting edges that remove the material as it is pulled through the gear blank, forming the teeth in a single pass.
- Gear Milling: Gear milling employs a variety of rotary cutters to remove material and form gear teeth.
- Gear Grinding: Gear grinding is a precision process that utilizes abrasive grinding wheels to remove material and create precise gear-tooth profiles. It is often employed for high-precision gears or gears made from pre-hardened steels, or for improving the surface finish and accuracy of already cut gears.
- Wire EDM: Wire EDM uses a CNC-controlled wire cut machine to follow the profile of a gear, cutting the exact tooth pattern and dimensions as required.
Why Choose Xometry for Gear Hobbing Services?
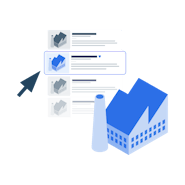
Endless Options
Choose from millions of possible combinations of materials, finishes, tolerances, markings, and certifications for your order.
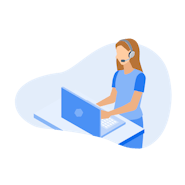
Easy to Use
Get started with our easy-to-use platform and let our experts take care of managing the project from locating the right manufacturing partner to delivery logistics.
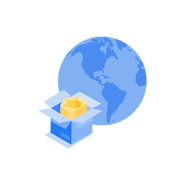
Vetted Network
We are ISO 9001:2015, ISO 13485, and AS9100D certified. Only the top shops that apply to become Suppliers make it through our qualification process.