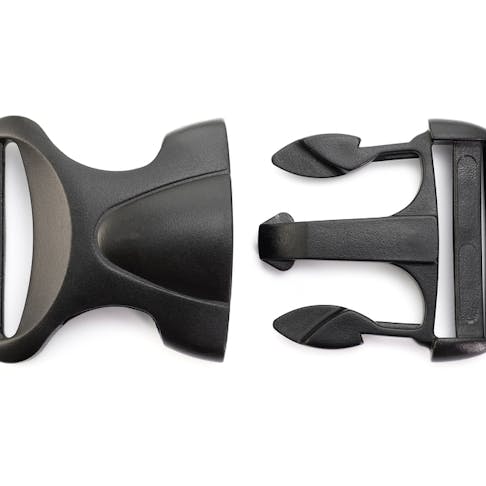
Snap Fit Joint Design: Types, Applications, Advantages, and Disadvantages
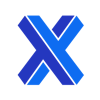
Snap-fit joints are everywhere around us. They’re a big part of why so many of the products we use every day are so easy and convenient to handle. Snap-fit joints make assembly and disassembly a breeze. This clever design feature has become incredibly popular because it cuts down on assembly time and reduces the need for extra bits and pieces like screws or glue.
This article takes a closer look at snap-fit joints and their designs, the different types, their applications, advantages, and disadvantages.
What Is Snap Fit Joint Design?
Snap-fit joints are a type of assembly mechanism that enables the easy joining of components without the need for screws, nuts, bolts, adhesives, or other fastening methods. It uses the elasticity of the materials involved to create a secure connection. Snap fits are designed with male features such as: hooks, ribs, or beads that interlock with a female component or depression when the components are pressed together. This provides a quick and easy method of assembly. and sometimes disassembly. The configuration of the male and female components influences the joint's ability to be disassembled and the amount of force needed for both assembly and disassembly. Different snap-fit designs can be chosen based on the application. Some popular designs include: cantilevers, U-shaped, torsions, and annular snap joints.
How Does Snap Fit Joint Design Work?
The mechanism of a snap-fit joint works through the interlocking of specially designed features on the mating components—typically a protrusion on one part (male) and a corresponding recess or undercut on the other (female). When the parts are pressed together, the male component flexes until it snaps into place within the female component, creating a secure fastening without the need for screws, glue, or other traditional fastening methods. The design of these features—such as their shape, size, and the angle at which they engage—dictates the force required for assembly and disassembly, as well as the joint's overall strength and reliability.
Snap-fit joints can be designed either as permanent or releasable/detachable, depending on the type of undercut and assembly. Permanent snap fits are intended for a single assembly process. In such applications, disassembly would likely damage the joint or the components themselves. Releasable snap fits, on the other hand, are designed for applications requiring the ability to separate and reattach the components multiple times, such as for maintenance or parts replacement.
Are Snap Fit Joints Only Applicable for Plastics?
No, snap-fit joints are not exclusive to plastic. However, plastics for snap-fit joints are predominantly associated with: ABS, PETG, PLA, and nylon, due to their inherent flexibility—an ideal characteristic for the snap-fit mechanism. Plastics can easily be designed to deform and return to their original shape, a critical feature for the engaging and disengaging actions of snap fits. Plastic-to-metal snap fits are also fairly common, in which case either the protrusion or the recess is made from metal and the other from plastic. Metal-to-metal snap-fits are also possible, but they are less common because metals typically have lower elasticity compared to most plastics, making them more challenging to design for snap-fit applications without risking material fatigue or failure. However, with careful design and the selection of appropriate metal alloys or by incorporating flexible features, snap-fit joints can be successfully applied to metal components.
What Are the Applications of Snap Fit Joint Designs?
Snap-fit joint designs find applications across a broad range of industries including:
- Consumer Electronics: They are used in gadgets like: smartphones, tablets, USB hubs, remote controls, and other devices for assembling cases, battery covers, and access panels.
- Automotive Components: Used for interior trim parts, such as: dashboard panels, door trims, strap buckles for baby car seats, and console assemblies.
- Packaging: Use snap-fit closures for tamper evidence, ease of opening, and secure reclosure. Examples include: food containers (e.g., tupperware lids), cosmetic compacts, and pill bottles.
- Office Supplies: Items like: staplers, paper punches, and pen caps use snap fits for assembly, ensuring parts are easily replaceable or refillable by the user.
- Toys: Toys need to be cheap, mass-produced, and lightweight. It is ideal to have a fastener that can form part of the toy’s mold, which is why snap-fit joints are used.
What Types of Snap Fit Joints Exist?
The differences among various types of snap-fit joints lie in their structural designs, the mechanism of action, and their application. Listed below are some common types of snap-fit joints:
- Annular Snap Fit Joints: These joints are characterized by a circular protrusion that interlocks with a corresponding circular recess in another part. The design is typically used for cylindrical components. The key feature that differentiates annular snap fits is the circular ridge that determines the force required for assembly and disassembly. The design can be adjusted for temporary or permanent connections by modifying the lead and return angles. A 45° return angle typically creates a secure yet detachable connection, while a return angle greater than 45° enhances joint strength but makes disassembly more challenging. A 90° return angle typically creates a permanent joint.
- Torsional Snap Fit Joints: Torsional snap fits involve a twisting action, utilizing a beam that acts similarly to a cantilever but is designed to rotate or twist under force. This type is unique because it employs a torsional (rotational) force for assembly. It is ideal for temporary connections in which components may need to be frequently detached and reattached.
- Cantilever Snap Fit Joints: Featuring a single beam that protrudes from one component and locks into place on another, cantilever snap fits are noted for their simplicity, cost-effectiveness, and ease of use. The beam often has a tapered head that transitions into a hook-like shape, securing the connection. Cantilever joints are particularly versatile, being suitable for a wide range of applications due to their straightforward design and ease of disassembly.
- U-Shaped Snap Fit Joints: A variation of the cantilever design, the U-shaped snap fit extends the beam length to reduce strain and increase flexibility, especially in applications in which space is limited. The U-shape allows for longer beams without compromising the integrity of the connection, distinguishing it from traditional cantilever designs by offering enhanced durability for repeated use.
- L-Shaped Snap Fit Joints: The L-shaped snap-fit features a design in which one component has a projecting tab that locks into an L-shaped slot on another component. This design is known for its easy assembly and disassembly. However, it has limitations, such as: a lower load-bearing capacity, sensitivity to manufacturing tolerances, potential for permanent deformation under stress, limited range of motion, and its effectiveness being highly specific to the application. Despite these drawbacks, its simplicity and reversibility make it a popular choice in many industries.
How Does the Type of Materials Affect Snap Fit Design?
The material choice for snap-fit designs affects their performance in several key ways. Materials for snap fits must have a balance between flexibility and elasticity to enable the parts to be snapped together without breaking, while also ensuring they can return to their original shape after deflection. Additionally, the chosen material must possess the necessary strength to withstand not only the forces applied during assembly but also those encountered throughout the product's use. Durability is another crucial factor, as the material should be resistant to wear, environmental conditions, and material fatigue, especially in applications in which the snap fit is subjected to repeated use or harsh environments. Moreover, the manufacturability of the material—its ability to be precisely molded or shaped into the required dimensions and its behavior during cooling or curing—significantly impacts the final fit and functionality of the snap-fit joint.
What Are Key Design Considerations for Snap Fit Joints?
Key design considerations for snap-fit joints include:
- Material Selection: Choose materials with appropriate flexibility, strength, and resilience to withstand repeated use without degrading.
- Stress and Strain Analysis: Understand the stress and strain the snap-fit will undergo during assembly and use to ensure durability and avoid failure.
- Dimensional Accuracy: Accuracy in the dimensions of snap-fit features is crucial for functionality, as slight deviations can significantly impact performance.
- Deflection and Engagement Forces: Calculate the deflection needed for assembly and the force required to engage and disengage the snap-fit to ensure ease of use without compromising security.
- Environmental Considerations: Consider the impact of environmental factors such as: temperature, humidity, and exposure to chemicals, which can affect material properties and joint performance.
- Ease of Assembly and Disassembly: Design for straightforward assembly and, if needed, disassembly, without requiring special tools or excessive force.
- Fatigue Resistance: For snap fits intended for multiple uses, ensure the design can withstand fatigue from repeated flexing.
- Aesthetics and Functionality: Ensure the snap-fit design complements the overall product design without interfering with functionality or aesthetics.
- Cost Efficiency: Optimize the design for cost-effective manufacturing, considering factors like: material use, production time, and the need for additional hardware.
How Do Tolerance and Clearance Factor in Snap Fit Design?
In snap fit design, tolerance and clearance are critical for ensuring proper fit and function. Tolerance dictates the permissible variation in dimensions, impacting how tightly or loosely parts fit together. Clearance defines the gap between parts, affecting the ease of assembly and the strength of the connection. It’s crucial to strike a balance between assembly ease, serviceability, durability, and aesthetics. Employing a Design of Experiments (DOE) method can effectively achieve this balance. DOE allows you to systematically test variations in angles, dimensions, and shapes of mating parts while measuring their impact on insertion force, snap force, removal force, and stress distribution. Analyzing these outcomes lets you pinpoint the optimal tolerance and clearance that align with your design goals and specifications. This approach helps in fine-tuning the snap-fit design to ensure a reliable, efficient assembly process while meeting performance requirements.
What Are the Advantages of Snap Fit Joint Design?
Some of the advantages associated with snap-fit joints include:
- Allows for rapid assembly without the need for tools or additional fastening hardware, significantly reducing assembly time and cost.
- Eliminates the need for screws, nuts, bolts, or adhesives, lowering material and labor costs.
- Many snap-fit designs can be disassembled and reassembled multiple times without damaging the parts, facilitating easy repairs and maintenance.
- Simplifies designs by reducing the number of components required for assembly, leading to fewer inventory parts and simplified logistics.
- Can be designed to be nearly invisible in the final product, enhancing aesthetic appeal by eliminating visible fasteners.
What Are the Disadvantages of Snap Fit Joint Design?
Snap-fit joints, despite their numerous advantages, come with inherent limitations and challenges such as:
- Are prone to stress concentration, whereby a small part of the joint bears a disproportionately high load, leading to potential failure if the material's strength limit is exceeded. This issue is exacerbated by the flexible and curved geometries typical of snap-fit designs.
- Over time, sustained stress can weaken the material in snap-fit joints, a phenomenon known as creep.
- The repeated assembly and disassembly of snap-fit joints can lead to fatigue, weakening the structure through continual loading cycles and potentially causing failure.
- Their performance can be adversely affected by environmental factors such as: high temperatures, chemical exposure, and humidity, which can accelerate wear and degradation.
- As non-permanent joints, snap fits inherently lack the strength and robustness of traditional fastening methods like screws and bolts.
- The flexibility that makes snap fits appealing also renders them susceptible to breaking under moderate overloading. Their long-term durability can be compromised by even slight excess forces.
What Are Best Practices When Designing Snap Fit Joints?
Designing durable snap-fit joints requires careful consideration of several critical factors to ensure they meet the necessary performance criteria without succumbing to common issues like: stress concentration, material fatigue, or improper engagement. Listed below are the best practices for snap-fit design:
- Add Fillets: Adding fillets to snap-fit designs, especially at the base of the cantilever arm, is crucial for reducing stress concentrations at sharp corners. Fillets help distribute the load over a broader area, making the joint more durable and less prone to breaking.
- Incorporate Taper: Tapering the snap fit, by reducing its cross-sectional area along its length, benefits the design by improving strain distribution and reducing material usage. This not only lowers the chances of failure due to excessive strain but also contributes to cost efficiency in mass production.
- Include Lugs and Stops: Lugs are small protruding elements that assist in aligning two mating parts and support structural integrity by bearing part of the shear force. Lugs and stops are essential for aligning mating parts accurately and preventing over-insertion or hyper-extension, which can lead to stress concentrations. They also provide additional structural support, distributing the load more evenly and enhancing the joint's overall durability.
- Increase Width of Hook: To ensure that snap-fit joints can withstand high loading frequencies, it is advised to increase the width of the hook. This enhances the structural strength of cantilever snap fits, which in turn makes them more capable of resisting applied forces without failure.
- Consider Fatigue Life: Designing snap-fit joints with consideration for fatigue life involves choosing materials with high yield strength and designing geometric features that minimize stress concentrations. This is essential for joints that will be subjected to repeated loading and unloading, to prevent fatigue failure.
- Appropriate Tolerance: Designing snap-fit joints with the correct tolerance is crucial to avoid high stress concentrations from tight fits or insufficient engagement force from loose fits. A balance between interference and sliding fits is recommended to achieve an optimal mechanical fit.
- Design a Wide Clip: The clip, being a major load-bearing component, should be designed wider to enhance its strength. A wider clip is better equipped to handle stresses.
Are Snap-Fit Joints Permanent?
Yes, some snap-fit joints can be permanent, depending on the design and intended application. However, it’s more common for snap-fit joints to be releasable/detachable, which means that they can easily be assembled and disassembled. Snap-fit joints that are designed to function as semi-permanent or permanent connections have different design parameters. For example, a snap-fit design with low insertion force and high removal force can make disassembly difficult without damaging the components, effectively making the joint permanent for all practical purposes.
Are 3D Printed Snap Fit Joints Precise?
It depends. The repeatability of 3D printed snap-fit joints depends significantly on the 3D printing technology used, the printer's calibration, the material properties, and the design of the snap-fit itself. Technologies like stereolithography (SLA) and selective laser sintering (SLS) offer high resolution and accuracy, making them suitable for creating precise snap-fit joints. However, even with high-resolution printing methods, factors such as: the printer's calibration, the chosen material, and the specific design tolerances set for the snap-fit must be carefully managed to ensure repeatability. While 3D printing allows for a high degree of customization and rapid prototyping, the inherent variability in the printing process can introduce some degree of inconsistency. Therefore, achieving precision in 3D-printed snap-fit joints is possible, but it requires careful attention to the details of the printing process, material selection, and design optimization.
Can You Design a Snap Fit Joint With a CNC Process?
Yes, you can design and manufacture a snap-fit joint with a CNC process. State-of-the-art processes like: CNC machining, 3D printing, and injection molding can all be used to create high-quality snap-fit joints.
Summary
This article presented snap fit joints, explained them, and discussed their various types and applications. To learn more about snap fit joints, contact a Xometry representative.
Xometry provides a wide range of manufacturing capabilities, including machining and other value-added services for all of your prototyping and production needs. Visit our website to learn more or to request a free, no-obligation quote.
Disclaimer
The content appearing on this webpage is for informational purposes only. Xometry makes no representation or warranty of any kind, be it expressed or implied, as to the accuracy, completeness, or validity of the information. Any performance parameters, geometric tolerances, specific design features, quality and types of materials, or processes should not be inferred to represent what will be delivered by third-party suppliers or manufacturers through Xometry’s network. Buyers seeking quotes for parts are responsible for defining the specific requirements for those parts. Please refer to our terms and conditions for more information.
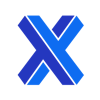