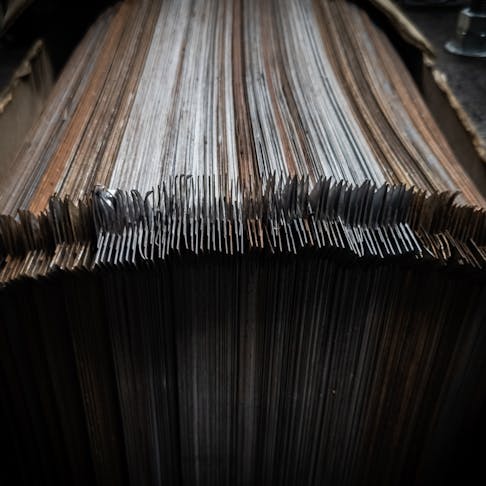
Electrical Steel: Definition, Composition, Properties, and Uses
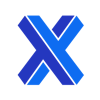
Electrical steel, also known as silicon steel or lamination steel, is a specific kind of steel made to have excellent magnetic properties. It is useful for a variety of electromagnetic applications. Its typical composition comprises iron and a range of silicon contents, with carbon and impurities forced to minimal levels. This type of steel is usually supplied in sheet form, intended for lamination, where multiple sheets are stacked together and insulated from each other.
Electrical steel is appropriate for power transformers, electric motors, generators, and other electrical equipment because of this combination of elements' efficient magnetic performance. Electrical steel is usually made in an electric arc furnace and then processed down to thin sheet form for use in laminated transformers. We will go into greater detail on the composition, characteristics, and uses of electrical steel in the sections that follow, illuminating its essential place in contemporary electrical engineering.
What Is Meant by Electrical Steel?
Electrical steel, often referred to as silicon steel, is an iron-silicon alloy known for its good magnetic characteristics. It is valued for its reduced energy loss and increased magnetic permeability compared to plain carbon steel. The range of silicon composition enables electrical steel to succeed in a variety of electrical equipment, including: electric motors, generators, power transformers, and distribution transformers.
Are Electrical Steel and Silicon Steel the Same?
Yes, electrical steel and silicon steel are interchangeable terms. Silicon steel, with silicon content up to 6.5%, is the common name for electrical steel, denoting its composition of iron and silicon. This family of alloys has high silicon content enhancing its magnetic properties and minimizing energy loss through eddy currents by raising resistivity.
What Is the Origin of Electrical Steel?
In a research conducted between 1882 and 1900, Robert Hadfield discovered that silicon increased the magnetic permeability of iron. This led to the first commercial use of silicon steel for electrical applications, like electric motors, in 1906. The discovery, in 1926 by Honda and Kaya, of the correlation between magnetic permeability and crystallographic orientations in iron single crystals led to subsequent developments that were later applied to silicon steel. By independently inventing the technologies and machinery for high-grade, effective non-oriented silicon steel production in 2008, Baosteel accomplished a rapid, all-encompassing product improvement.
How Does Electrical Steel Work?
Electrical steel, composed of iron and silicon, plays a vital role in the cores of motors and transformers. These cores, responsible for guiding magnetic flux, benefit from electrical steel's properties. Its high silicon content increases electrical resistance, effectively curbing energy-wasting eddy currents. Additionally, the aligned crystal structure allows swift magnetization and demagnetization. Consequently, electrical steel excels in reducing energy losses and maintaining robust magnetic behavior, making it the ideal choice for optimizing the efficiency of electromagnetic devices.
How Is Electrical Steel Made?
Electric arc furnaces are used in the production of most electrical steel.These furnaces melt raw materials such as iron ore and scrap steel. Then, to produce the correct composition, a regulated amount of silicon is added to the molten metal. The steel is hot-rolled into thin sheets after refinement, and then its magnetic characteristics are improved by annealing. In the refinement process of electrical steel production, deoxidization is a specific step where oxygen is removed from the molten metal to enhance the material's purity and electrical properties.
What Are the Different Types of Electrical Steel?
The two main types of electrical steel are:
1. Non-Grain-Oriented Electrical Steel
Non-grain-oriented electrical steel (NGOES) is distinguished by its isotropic magnetic behavior, or the fact that its magnetic properties are constant in all directions. During the manufacturing process, the molten NGOES steel is cast into thin sheets without special processing to deliberately produce a particular alignment of the crystal lattices within the grains. This lack of a preferred crystal orientation results in the steel's uniform magnetic behavior. NGOES is suitable for applications requiring consistent performance in all directions. Non-grain-oriented electrical steel finds its primary use as core parts in electrical motors and generators. Using NGOES in rotating machinery is sensible because it maintains consistent magnetic properties in all directions, optimizing energy efficiency. Unlike Grain-oriented steel, NGOES adapts well to the changing magnetic field directions in motors and generators, reducing energy loss. Its noteworthy properties include high permeability, low core loss, and cost-effectiveness, making it a practical choice for applications where isotropic magnetic behavior is advantageous.
2. Grain-Oriented Electrical Steel
Grain-oriented electrical steel (GOES) is a specialized variant of electrical steel with anisotropic magnetic properties. The manufacturing process for this type involves careful control of crystal orientation. Sheets are rolled in a manner that aligns the crystal grains predominantly in one specific direction relative to the sheet, creating a preferred direction for maximum magnetic permeability. GOES plays a pivotal role in the fabrication of energy-efficient transformers and high-performance generators. Its characteristics include low power loss per cycle, low core loss, and high permeability, all optimized for a distinct magnetization orientation. Because of its crystal orientation, GOES, which enhances magnetic permeability in one direction, is perfect for transformers. The magnetic field direction of rotating machinery, which necessitates materials with isotropic magnetic properties, continually varies. Therefore this anisotropic attribute isn't appropriate.
How Is Electrical Steel Different From Regular Steel?
Unlike conventional steel, electrical steel is created specifically for superior magnetic characteristics. It has silicon in it, which lessens eddy current energy loss by increasing electrical resistivity. Electrical steel is suited for electromagnetic applications like transformers and motors because silicon changes the magnetic behavior of the material. To learn more, see our article on the Chemical Composition of Steel.
Is Electrical Steel Better Than D2 Tool Steel?
No, electrical steel is not inherently better than D2 tool steel. They serve different purposes. Electrical steel excels in electromagnetic applications due to its magnetic properties. On the other hand, D2 tool steel is renowned for its high hardness and wear resistance, making it suitable for cutting tools, dies, and industrial machinery components.
Is Electrical Steel a High-Alloy Steel?
No, electrical steel is not a high-grade alloy steel. It typically falls into the category of low alloy steels, as it contains relatively low levels of alloying elements, usually less than 8%. Whereas high alloy steels consist of more than 8% alloying elements. To learn more, see our guide on What is Alloy Steel.
What Are the Chemical Compositions of Electrical Steels?
Non-grain-oriented electrical steels typically have low carbon content (0.01% or less ) and silicon content (about 3.5%). This helps in reducing core loss and improving magnetic properties. These steels may also contain small amounts of aluminum and manganese. Table 1 below is a simplified table of common chemical compositions found in non-oriented electrical steels:
Element | Percentage Range |
---|---|
Element Carbon (C) | Percentage Range About 0.003% |
Element Silicon (Si) | Percentage Range About 3.5% |
Element Aluminum (Al) | Percentage Range Limited to 0.5% |
Element Manganese (Mn) | Percentage Range Limited to 0.5% |
What Is the Carbon Content of Electrical Steel?
Non-oriented electrical steel usually has a carbon percentage of 0.05% or less. For minimizing magnetic losses and guaranteeing peak performance in electrical applications, this low carbon content is important. Non-oriented electrical steel must have a low carbon content since carbon can affect the material's magnetic characteristics. Extra carbon messes with the magnetic domains' alignment, increasing eddy current losses and lowering transformer and motor efficiency.
What Are the Properties of Electrical Steel?
Electrical steel is essential in electromagnetic applications like transformers and motors. It is clear from a comparison of non-grain-oriented electrical steel (NGOES) and grain-oriented electrical steel (GOES) that each is best suited for particular uses within the electrical sector due to its various qualities. Table 2 outlines the properties of electrical steel:
Property | ATI Allegheny Ludlum Grain-Oriented Electrical Steel |
---|---|
Property Density | ATI Allegheny Ludlum Grain-Oriented Electrical Steel 7.65 g/cm3 |
Property Ultimate Tensile Strength (Angle to Rolling Direction 0°-90°) | ATI Allegheny Ludlum Grain-Oriented Electrical Steel 361-405 MPa |
Property Thermal Conductivity (20-600 °C) | ATI Allegheny Ludlum Grain-Oriented Electrical Steel 70-0.0715 Cal/cm2▪Sec▪°C/cm |
Property Electrical resistivity | ATI Allegheny Ludlum Grain-Oriented Electrical Steel 48 Microhm-cm |
Property Thermal Coefficient of Resistivity (20-145 °C) | ATI Allegheny Ludlum Grain-Oriented Electrical Steel 0.047 Microhm-cm/°C |
Property Heat Capacity | ATI Allegheny Ludlum Grain-Oriented Electrical Steel 0.12 Cal/g/°C |
Property Curie Temperature | ATI Allegheny Ludlum Grain-Oriented Electrical Steel 730 °C |
Property Thermal Expansion (20-100 °C) | ATI Allegheny Ludlum Grain-Oriented Electrical Steel 11.9▪10-6▪cm/cm/°C |
Property Rockwell Hardness (Angle to Rolling Direction 0°-90°) | ATI Allegheny Ludlum Grain-Oriented Electrical Steel 85 |
How Thick Is Electrical Steel?
Electrical steel is available in various thicknesses, commonly ranging from 0.23 to 0.35 millimeters. Thinner sheets help minimize energy wastage by limiting the circulation of induced currents, thus enhancing the efficiency of transformers and motors.
What Are the Characteristics of Electrical Steel?
Electrical steel possesses specific characteristics ideal for electrical applications. It exhibits low electrical conductivity, high magnetic permeability, and reduced core loss compared to conventional steel due to its silicon content. This composition enhances energy efficiency and minimizes heat generation in devices like transformers and motors, making it a vital material in electrical engineering.
Does Electrical Steel Rust?
Yes, electrical steel can rust. It is susceptible to corrosion due to its iron content. It's usual practice to coat each layer with insulating materials, such as varnish or oxide coatings, to reduce this. This guarantees that the stack's laminations are well insulated from one another. To prevent corrosion and preserve the steel's electrical and magnetic qualities over time, it is essential to thoroughly coat all key components, even difficult-to-reach regions like corners and tight spaces.
Can Electrical Steel Be Welded?
Yes, electrical steel can be welded. Fusion welding is a common method used to join electrical steel laminations, especially in high-performance motor applications. This method provides a strong and reliable bond, ensuring structural integrity. In the context of electrical steel, specific welding methods such as resistance spot welding or laser welding are commonly used. Mechanical interlock and glue joints may not offer the same level of durability. The goal is to balance mechanical strength and magnetic properties. Fusion welding is one of the methods but may impact insulation and introduce challenges in maintaining both properties. Research in this field is growing due to the rise of electric vehicles. Mechanical joining and fusion welding are common methods, each with its advantages and costs.
Can Electrical Steel Be Tempered?
Yes, electrical steel can indeed undergo heat treatment for the purpose of preserving and enhancing its magnetic and mechanical characteristics. This involves a carefully orchestrated process, beginning with a light cold roll, often referred to as temper rolling. During this phase, strain energy is stored. Subsequently, in the final annealing stage, specific conditions are applied to promote stress relief and encourage advantageous grain orientation. This method is instrumental in achieving improved grain development and a substantial reduction in core loss, ultimately resulting in enhanced magnetic properties for the steel.
What Are the Uses of Electrical Steel?
Electrical steel is used in various electrical applications due to its magnetic properties. Its main uses include:
- Transformer Cores: Efficiently directs magnetic flux, reducing energy loss. The main parts of electrical transformers are transformer cores. Their main job is to make it easier for magnetic induction to efficiently transmit electrical energy from one circuit to another. The transformer's primary winding generates magnetic flux, which the core focuses and directs onto the secondary winding to transform voltage. This makes it possible to distribute electricity at various voltage levels, which is necessary for power transmission and distribution.
- Motors and Generators: Minimizes eddy current losses, enhancing efficiency. Motors and generators are devices that rely on the principles of electromagnetism. Motors convert electrical energy into mechanical energy, while generators do the reverse—converting mechanical energy into electrical energy. Both devices utilize magnetic fields generated by electrical currents to achieve their respective functions. In motors, this magnetic interaction produces motion, whereas, in generators, it induces electrical voltage.
- Inductors: Provides controlled magnetic fields for electronic components. An electrical component called an inductor, which is sometimes known as a choke when employed for particular tasks, is made to store and regulate electrical energy in the form of a magnetic field. Its main job is to thwart variations in electrical current flow. Inductors can provide energy storage, smooth out current variations, and filter out high-frequency noise in circuits. In particular, chokes are used to block high-frequency alternating current (AC) while allowing direct current (DC) and lower-frequency AC to pass through, thereby "choking" off undesired signals or interference.
How Long Will Electrical Steel Last?
The lifespan of a component made of electrical steel largely depends on factors such as: operating conditions, maintenance, and protective coatings. Properly designed and maintained, electrical steel can have a long operational life, often exceeding several decades in applications like transformers, where durability and efficiency are important.
How Much Does Electrical Steel Cost?
Electrical steel has a range of prices, especially for non-grain oriented electrical steel (NGOES) and grain-oriented electrical steel (GOES). NGOES can cost between $950 and $1000 per ton on average, whereas GOES is typically more expensive, costing between $2000-$2100 per ton. To put things in perspective, 1020 carbon steel, a standard commodity, is normally more affordable for comparison, costing between $300 and $550 per Ton.
What Is the Most Common Form of Electrical Steel?
The most common form of electrical steel is in the shape of thin sheets, typically coated with insulating materials. They are used as laminations stacked to form cores for transformers, motors, and generators. The lamination process reduces eddy current losses and enhances the efficiency of electrical devices.
Can Electrical Steel Be Used in Electric Wires?
No, electrical steel is not used in electrical wires. Electrical steel is better suited for applications like transformers, motors, and generators where its magnetic properties are crucial for energy efficiency and performance.
What Are the Advantages of Electrical Steel?
Electrical steel offers distinct advantages due to its unique properties:
- Is more cost-effective than some advanced magnetic materials, making it a practical choice for various applications, including transformers and electric motors. Materials like neodymium iron boron (NdFeB) magnets offer exceptional magnetic strength but are considerably more expensive than electrical steel.
- Is durable and can withstand mechanical stresses, making it suitable for applications where mechanical strength is crucial.
- Has low core loss, meaning it dissipates minimal energy as heat when subjected to magnetic fields, contributing to energy efficiency.
What Are the Disadvantages of Electrical Steel?
While electrical steel has numerous benefits, it also presents some drawbacks:
- Requires protective coatings to prevent rust.
- Due to its brittleness, particularly at high silicon levels, can be prone to cracking or breaking under mechanical stress.
- Primarily suited for electrical and magnetic purposes, limiting versatility
Is Electrical Steel Better Than Weathering Steel?
No, the functions of electrical steel and weathering steel are distinct. Electrical steel has magnetic characteristics that are enhanced for use in electrical equipment. On the other hand, weathering steel is intended for use in structural applications and is designed to withstand corrosion. It is difficult to compare them because they have advantages in different applications that meet various engineering requirements.
Summary
This article presented electrical steel, explained it, and discussed its composition and uses. To learn more about electrical steel, contact a Xometry representative.
Xometry provides a wide range of manufacturing capabilities and other value-added services for all of your prototyping and production needs. Visit our website to learn more or to request a free, no-obligation quote.
Disclaimer
The content appearing on this webpage is for informational purposes only. Xometry makes no representation or warranty of any kind, be it expressed or implied, as to the accuracy, completeness, or validity of the information. Any performance parameters, geometric tolerances, specific design features, quality and types of materials, or processes should not be inferred to represent what will be delivered by third-party suppliers or manufacturers through Xometry’s network. Buyers seeking quotes for parts are responsible for defining the specific requirements for those parts. Please refer to our terms and conditions for more information.
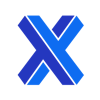