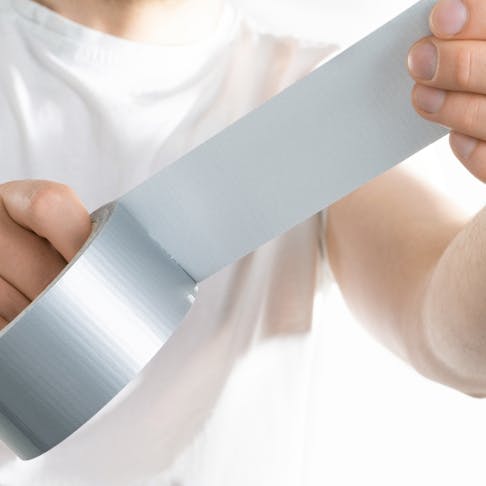
Peel Tester: How Does It Work, How To Test, and Technical Requirements
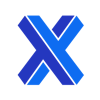
Peel tests are used to measure the adhesive strengths of at least one flexible material bonded to another material that is either flexible or rigid. This is done by pulling or peeling away one material from the other by applying a force.
This article takes a deeper look into peel testing, what it is, how it works, how it is performed, and the technical requirements associated with this testing method.
What Is a Peel Tester?
A peel test is a method used to evaluate the adhesive strength of materials bonded either to a substrate or between layers by measuring the force required to separate them. The materials involved in the test can be entirely flexible, such as tapes, films, rubbers, and laminates, or consist of one flexible and one rigid material, like: metals, composites, or rigid plastics. This method is used in industries, such as: aerospace, automotive, electronics, and packaging. Peel tests are performed by applying a force to peel one material away from another at a specific angle and speed, thereby assessing the adhesive's performance in conditions that mimic real-world conditions. Typical outcomes of a peel test include the initial peak force required to start the peel, the average force exerted across the entire seal, and the peel strength, which is the average force per unit width of the specimen.
There are different types of peel tests, such as: 90-degree peel, 180-degree peel, T-peel, floating roller peel, loop tack strength test, and the Double Cantilever Beam (DCB) test. Each is designed to simulate various peel forces and scenarios encountered in real-world applications. Each test provides insights into the quality of the adhesive bond, considering factors such as: the effect of processing variables, environmental exposure, and the mechanical properties of the materials involved. The choice of peel test for assessing peel strength depends on the geometry of the materials, the specific industry, and their applications. The angle between the components being tested varies according to the test type conducted.
How Does a Peel Tester Work?
Peel tests are conducted using universal testing machines equipped with a test frame, a load cell, testing software, grips, and sometimes additional accessories tailored for specific applications. These tests often necessitate specialized fixtures to uphold the required peel angle. For tests like 180° and T-peel, tensile grips are often used. The specific test being conducted and the material under examination dictate the necessary accessories. A single machine can accommodate a wide range of materials within its force capacity by simply swapping out the fixtures.
Peel testing involves the mechanical separation of one bonded material from another to evaluate the strength of the adhesive bond. During the test, one of the materials is securely held in place, while the other is connected to a grip that moves. This grip extends the flexible material away from its bonded counterpart at a set speed and angle, accurately recording the force needed to separate them. This force data is recorded, allowing for the calculation of key metrics such as: the initial peak force needed to initiate the peel, the average force exerted during the test, and the peel strength, which is the average force per unit width of the bond.
What Manufacturing Processes Use Peel Testing?
Peel testing is widely used in multiple manufacturing sectors to ensure product quality, reliability, and compliance with industry standards. Some of the key industries include:
- Packaging
- Electronics
- Automotive
- Aerospace
- Medical devices and pharmaceuticals
- Construction
- Consumer products
What Type of Materials Need Peel Testing?
Peel tests are used to evaluate the bonding strength of materials such as:
- Tape
- Adhesives
- Films, foils, and thin sheets
- Rubber and elastomers
- Laminates
- Biomaterials
- Labels
How To Do a Peel Test?
To perform a peel test, follow these steps:
- Cut the materials to be tested into strips of a specified width and length, as per the testing standards relevant to your application.
- Use a universal testing machine equipped with the appropriate grips and fixtures for the type of peel test you are conducting (e.g., 180°, 90°, T-peel).
- Attach the test fixture to the universal testing machine, ensuring it is compatible with the peel angle required for your test.
- Secure one end of the material sample to a fixed grip and the other end to a moving grip. The alignment should match the desired peel angle (e.g., 180° or 90°).
- Program the testing machine with the correct speed and distance parameters for the test. The speed should reflect the intended application of the material or industry standards.
- Start the machine to begin peeling the bonded materials apart. The machine will apply a consistent force to peel one material away from the other. Ensure that the peel angle remains constant and that the sample does not slip or tear outside of the intended peel path.
- The machine will record the force required to peel the materials apart throughout the test. Key metrics include the peak initial force and the average force over the length of the peel.
- Evaluate the data to determine the peel strength, represented as the average force per unit width of the bond line. Compare the results against industry standards or product specifications.
How Do You Measure Peel Strength?
Peel tests are conducted at a uniform speed along the tensile direction. The peel strength is determined by first measuring the load required to peel the specimen, then calculating the average of this load, and finally dividing it by the bond line's width. The data for peel-strength calculations are obtained from the steady, or linear, section of the load-versus-position graph.
How Do You Read Peel Test Results?
During a peel test, a load vs. position curve is generated during the test. The first result that is of value is the peak initial force, which reflects the maximum force required to start the peeling process. This value is critical for understanding the initial adhesion strength between the bonded materials. That graph can also be used to calculate the average peel force across the bond line, which is typically presented as force per unit width (e.g., newtons per millimeter or pounds per inch). This average force indicates the consistent strength of the adhesive bond throughout the test. Use a linear section in the load vs. position curve to determine the average force. This is a good indicator of uniform peel strength, which signifies a stable and consistent adhesive performance across the entire bond line. Figures 1 & 2 below give an example of typical data that can be obtained by performing peel tests, including a load vs. position curve:
Typical data that can be obtained from a peel test.
Image Credit: https://www.brookfieldengineering.com/brookfield-university/learning-center/application-notes/texture-applications/food-and-beverage/yoghurt-bottle-peel-test
What Are the Benefits of Peel Testing?
Peel testing has the following benefits:
- Peel testing verifies that adhesive bonds meet required strength standards, ensuring products are consistent, reliable, and fit for their intended use.
- The peel strength of different adhesives and materials can be used to help select the right material for a specific application.
- Through early detection of weaknesses in adhesive bonds, peel testing helps mitigate the risk of product failure in real-world applications.
- Analyzing peel-test results can reveal areas for improvement in materials, adhesives, or manufacturing processes.
What Are the Challenges With the Peel Test?
The challenges associated with peel testing are outlined below:
- Achieving uniformity in sample preparation is crucial. Variations in material thickness, adhesive application, and curing conditions can lead to inconsistent results.
- The peel angle, speed of testing, and fixture alignment must be consistent and aligned with the specific requirements of the test standard being followed. Any deviation can significantly impact the results.
- Different materials can exhibit varied behaviors under peel forces, such as: stretching, tearing, or breaking in a manner that is not uniform. This variability can complicate the interpretation of results and the comparison between different materials or adhesives.
- Correctly identifying the mode of failure (adhesive, cohesive, or substrate failure) is essential for interpreting the results accurately. However, distinguishing between these failure modes can be challenging.
How Different Is a Shear Test From a Peel Test?
Shear tests and peel tests are both methods used to evaluate the strength and performance of materials and adhesives, but they measure different properties and are used for different applications. The primary difference lies in the direction of the applied force and the specific material property being measured—shear strength versus peel strength. Shear tests are aimed at measuring the shear strength of materials or adhesive bonds by applying forces parallel to the surface of the material or bond, making them particularly useful for evaluating the resistance of materials to sliding or slipping under load.
On the other hand, peel tests focus on determining the peel or stripping strength of an adhesive bond by measuring the force required to separate two bonded materials at a controlled angle and speed. This makes peel tests essential for assessing the performance of adhesive tapes, labels, coatings, and laminated materials, in which the quality of the adhesive bond is critical.
To learn more, see our full guide on the Lap Shear Test.
What Are the Technical Requirements of Peel Testing?
The technical requirements of peel testing are as follows:
- The use of appropriate test fixtures and grips that are compatible with the type of peel test being performed (e.g., 90°, 180°, T-peel, floating roller peel) to maintain the specified peel angle throughout the test.
- Setting the testing machine to peel the bonded materials at a constant and specific speed, as dictated by the relevant testing standard, to ensure that the rate of peel does not influence the results.
- Preparing samples according to the dimensions, bonding conditions, and curing times outlined in the testing standards. Uniform sample preparation is crucial for achieving repeatable and comparable results.
- Utilizing a calibrated load cell to accurately measure the force required to peel the materials apart.
- Conducting the test under controlled environmental conditions, such as temperature and humidity, that replicate the intended application environment or follow the specifications of the testing standard.
What Standards Does the Peel Test Follow?
Various standards are applicable to peel tests. Some of the common ones are listed below:
ASTM Standards:
- ASTM D903: Standard test method for peel or stripping strength of adhesive bonds.
- ASTM D1781: Standard test method for climbing drum peel for adhesives.
- ASTM D1876: Standard test method for peel resistance of adhesives (T-peel test).
- ASTM D3167: Standard test method for floating roller peel resistance of adhesives.
- ASTM D3330: Standard test method for peel adhesion of pressure-sensitive tape.
- ASTM D6195: Standard test methods for loop tack.
- ASTM C794-06: The peel test for adhesion measurement for sealants.
To learn more, see our full article on ASTM Guidelines.
ISO Standards:
- ISO 8510-2: Adhesives – Peel test for a flexible-bonded-to-rigid test specimen assembly – Part 2: 180° peel.
- ISO 8510-1: Adhesives – Peel test for a flexible-bonded-to-rigid test specimen assembly – Part 1: 90° peel.
- ISO 4578: Adhesives – Determination of peel resistance of high-strength adhesive bonds – Floating-roller method.
- ISO 14676: Adhesives – Evaluation of the effectiveness of surface-treatment techniques for aluminum – Wet-peel test by floating-roller method.
- ISO 11339: Adhesives – T-peel test for flexible-to-flexible bonded assemblies.
SAE Standards:
- SAE J1553: Cross peel test for automotive-type adhesives for fiber-reinforced plastic (FRP) bonding.
- SAE J1907: Peel adhesion test for glass to elastomeric material for automotive glass encapsulation.
Is There a Difference Between Peel and Tear Strength?
Yes, there is a difference between peel strength and tear strength. Peel strength and tear strength are distinct material properties measuring different aspects of performance. Peel strength refers to the adhesive bond's resistance to peeling forces, indicating how strongly an adhesive clings to a substrate when pulled away at a specific angle. It is measured in units of force per width, such as newtons per millimeter. Tear strength, on the other hand, measures a material's resistance to tearing, capturing how much force is needed to initiate or propagate a tear through the material. This property is crucial for materials subjected to dynamic stresses and is usually quantified in units of force or energy.
Summary
This article presented the peel tester, explained it, and discussed how it works and how to use the test. To learn more about peel testing, contact a Xometry representative.
Xometry provides a wide range of manufacturing capabilities and other value-added services for all of your prototyping and production needs. Visit our website to learn more or to request a free, no-obligation quote.
Disclaimer
The content appearing on this webpage is for informational purposes only. Xometry makes no representation or warranty of any kind, be it expressed or implied, as to the accuracy, completeness, or validity of the information. Any performance parameters, geometric tolerances, specific design features, quality and types of materials, or processes should not be inferred to represent what will be delivered by third-party suppliers or manufacturers through Xometry’s network. Buyers seeking quotes for parts are responsible for defining the specific requirements for those parts. Please refer to our terms and conditions for more information.
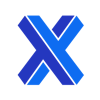