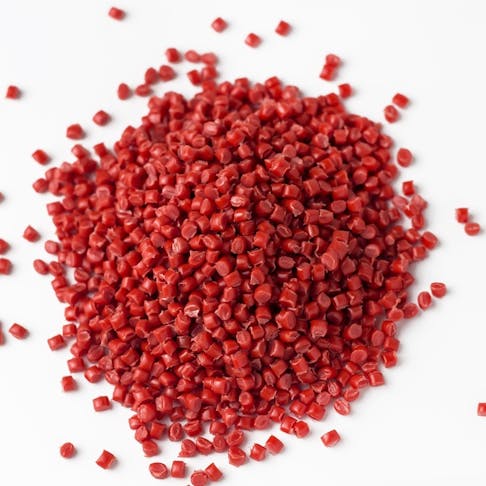
Polypropylene vs. Nylon: Material Differences and Comparisons
Learn more information about both polypropylene and nylon.
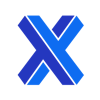
Polypropylene and nylon are both thermoplastics that are used to manufacture products for industrial and household applications. Though nylon and polypropylene share similar traits, they are very different. To start, nylon is a condensation polymer, whereas polypropylene is an additional polymer. Nylon is produced by reacting a diamine with a dicarboxylic acid.
These materials also differ in their uses. The properties that make each one unique mean they fit into separate application categories. For example, nylon can be used in place of aluminum engine parts or to insulate electrical lines. Polypropylene, by contrast, gets built into semiconductor components and auto batteries due to its resistance to water and solvents.
Nylon's malleability makes it a useful material for design prototyping. It is the perfect low-friction material for many items, including rollers, seals, and wheels that must tolerate resistance. On the other hand, polypropylene is ideal for moving components like hinges and gears because it can bend under load without cracking but is still less flexible than nylon.
In this article, we will compare polypropylene vs nylon and highlight their differences in terms of applications, properties, cost, and sustainability.
What is Polypropylene?
Polypropylene, also known as PP or polypropene, is a polyolefin or saturated polymer. It is a low-density thermoplastic with good resistance to heat. Other characteristics of PP include: chemical resistance, elasticity, toughness, fatigue resistance, and electrical insulation capability. The dual functionality of polypropylene as both a plastic and a fiber is another invaluable characteristic of this material. This versatile thermoplastic has a wide range of applications in both domestic and commercial settings. For more information, see our guide on What is Polypropylene.
Figure 1 is an example of polypropylene pellets:
Polypropylene pellets in two colors.
Image Credit: Shutterstock.com/sveticluka
The packaging industry is the largest consumer of polypropylene, accounting for roughly 30% of the market. Electrical and equipment manufacture take up about 13% each. Construction materials take up 5% of PP’s market, followed by household appliances and automobiles which consume 10% each. The remainder is made up of other, more minor applications.
As an addition polymer, polypropylene is produced by connecting monomers together through straightforward additive reactions with no byproducts. Polypropylene is produced from a mixture of propylene monomers and has the chemical formula (C3H6)n. The two main synthesis processes for polypropylene are metallocene-catalyzed polymerization and Ziegler-Natta polymerization.
Polypropylene may form the basis of live hinges using CNC, injection molding, thermoforming, or crimping processes. It can also be easily copolymerized with other polymers, such as polyethylene, to create composite plastics. In comparison to using pure polypropylene, copolymerization dramatically alters the material's characteristics, enabling more durable technical applications.
What Is Nylon?
Nylon is the commercial name for a particular synthetic polyamide thermoplastic. It is created through a reaction between a diamine and a dicarboxylic acid. A molecule with carboxylic groups reacts with a molecule with amine groups at both ends to create polyamide-like nylon. One of nylon’s key purposes early on was to replace silk. It can be shiny, semi-shiny, or dull. It is also capable of experiencing significant elongation. Nylon resists abrasion, numerous chemicals, insects, and fungi. It has good thermal and fatigue resistance and is highly machinable. Additionally, it is also a very effective noise dampener. For more information, see our guide on nylon.
Figure 2 below is an example of nylon:
An example of nylon sliders.
Image Credit: Shutterstock.com/Sander K
The four primary polyamide nylon grades are nylon 66, 11, 12, and 46. These designations are derived from the respective lengths of their polymeric chains. The diamine's carbon atom count is represented by the first number, and the acid's carbon count is represented by the second. The term, "PA" (e.g., PA 6 or PA 6/66), is commonly used to refer to nylon, which is most frequently seen in black, white, and natural-hue (off-white or beige) variants. Nylon 66 is the most common type for engineering applications and the plastic industry. The chemical formula for Nylon 66 is (C12H22N2O2)n.
Toothbrushes, gloves, wheels, guitar strings, strings for tennis rackets, medical devices, electrical connectors, fishing line, and more get made out of nylon.
Polypropylene vs. Nylon: Applications and Uses
Since nylon is a good insulator, it is frequently used to replace aluminum in engine parts and to insulate electrical cables. The water- and solvent-repelling properties of polypropylene, meanwhile, make it a popular material for semiconductor components and automotive batteries. Polypropylene is utilized in laboratory settings and in chemical tanks and plating because of its durability and resilience in the face of stress.
Nylon is a great material for design prototyping because of its malleability, which allows for reheating and re-molding. And with its low friction coefficients, nylon is ideal for numerous parts like rollers, seals, and wheels.
Although less flexible than nylon, polypropylene can bend under stress without cracking, which makes it a perfect material for moving parts like hinges and gears.
Both polypropylene and nylon parts can be manufactured via injection molding. It may be simpler to use polypropylene in injection molds because the raw material pellets have a lower melt viscosity than nylon pellets. Nylon — especially Nylon 12 — is a useful material for both injection molding and additive manufacturing because of its strong heat resistance.
Finally, it's important to note that FDA-compliant grades of nylon and polypropylene are both readily available. Therefore, both materials are common in the food and beverage industry and the medical sector.
Polypropylene vs. Nylon: Physical Properties
Although polypropylene and nylon have certain traits in common, there are some significant differences between their mechanical and physical properties. Table 1, below, compares the two materials in terms of their physical properties:
Property | Polypropylene | Nylon |
---|---|---|
Property Chemical Resistance | Polypropylene Excellent chemical resistance - diluted bases and acids do not react with PP. | Nylon Good chemical resistance - Generally speaking, nylon is resistant to chemicals such as gasoline, mineral spirits, oils, fuels, and some alcohols. |
Property Tensile Strength | Polypropylene 25-40 MPa | Nylon 50-90 MPa |
Property Impact Tolerance | Polypropylene High impact resistance. | Nylon High impact resistance (10 times that of ABS). |
Property Water Absorption | Polypropylene Nearly impermeable to water, PP absorbs only trace amounts: 0.01%, of its weight in water after a 24 hr soak test. | Nylon 0.30 - 7.0% by weight |
Property Surface Hardness | Polypropylene 92 HRR (Rockwell R) | Nylon 100 - 120 (Rockwell R) |
Property Operating Temperature | Polypropylene <180 °F | Nylon -70 to 250 °F |
Property Melting Temperature | Polypropylene 327 °F | Nylon 374 - 460 °F |
Polypropylene vs. Nylon: Recyclability and Sustainability
Polypropylene is a fairly safe and sustainable material. It presents no major human health concerns either during production or as a completed material. In contrast, nylon production is a very energy-hungry process that can have negative impacts on the environment. However, because recycled nylon avoids the destructive production process, recycling is a more environmentally responsible alternative to producing new nylon.
Both polypropylene and nylon are recyclable. During the recycling process, polypropylene does not release any harmful toxins. Polypropylene also takes about 20-30 years to biodegrade, which is far quicker than other plastics. Nylon, on the other hand, is not biodegradable.
Polypropylene vs. Nylon: Cost
Both nylon and polypropylene are considered inexpensive materials. However, polypropylene is significantly cheaper than nylon. The global average price for polypropylene is roughly $1.3 per kilogram, whereas nylon goes for approximately $2.4 per kilogram.
Alternative Materials to Polypropylene and Nylon
Some injection-molding-ready alternatives to polypropylene and nylon include:
- Cyclic Olefin Copolymer (COC): In addition to rigidity, strength, and hardness, copolymers also exhibit exceptional biocompatibility, low water vapor permeability, extremely low water absorption, high refractive index, and great chemical resistance.
- Acrylonitrile Styrene Acrylate (ASA): ASA copolymers are among the best acrylonitrile elastomers in terms of weathering resilience and resistance to UV irradiation, heat, moisture, and cracking. Their mechanical characteristics are comparable to those of ABS (acrylonitrile butadiene styrene) elastomers.
- Polycyclohexylenedimethylene Terephthalate (PCT): PCT is a high-performance, semi-crystalline thermoplastic polyester made by polycondensing terephthalic acid (TPA) and cyclohexane dimethanol (CHDM). Low moisture absorption, outstanding electrical insulation, superior chemical resistance (similar to PET and PBT), and good long-term light and temperature stability are only a few of the material's key attributes.
Summary
This article presented polypropylene and nylon, explained what they are, and discussed the properties and applications of each in manufacturing. To learn more about polypropylene and nylon, contact a Xometry representative.
Xometry provides a wide range of manufacturing capabilities and other value-added services for all of your prototyping and production needs. Visit our website to learn more or to request a free, no-obligation quote.
Disclaimer
The content appearing on this webpage is for informational purposes only. Xometry makes no representation or warranty of any kind, be it expressed or implied, as to the accuracy, completeness, or validity of the information. Any performance parameters, geometric tolerances, specific design features, quality and types of materials, or processes should not be inferred to represent what will be delivered by third-party suppliers or manufacturers through Xometry’s network. Buyers seeking quotes for parts are responsible for defining the specific requirements for those parts. Please refer to our terms and conditions for more information.
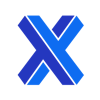