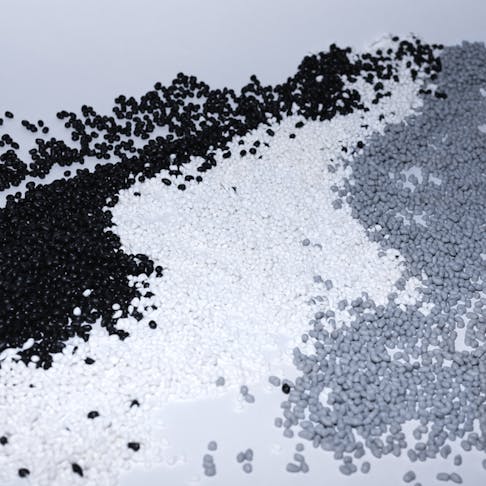
Shore D Hardness Scale: Definition, Use, Types, Benefits, and Limitations
Learn more about how this type of hardness scale is a valuable tool used in various industries to measure and compare the hardness values of materials such as plastics, rubbers, and elastomers.
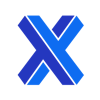
The Shore D hardness scale is a popular test method to determine how hard different materials are. This scale is a crucial tool in sectors like manufacturing, construction, and the automotive industry, where hardness is a key factor in product development, quality assurance, and material selection. The Shore D hardness rating is determined by how far an indenter can go into a material when a specified force is applied. This scale is specifically used to gauge the toughness of semi-rigid plastics, hard rubber, and hard plastics. It is noteworthy that the indenter on the Shore D testing device generates a 10-pound spring force.
The Shore D hardness scale system is valuable because it’s quick, non-destructive, easily repeatable, and suitable for thin or small samples. The Shore D hardness scale's drawbacks, however, include its sensitivity to surface finishing, and surface preparation Today we’ll cover the Shore D hardness scale, its purpose, and the kinds of materials that can be tested using this technique.
What Is the Shore D Hardness Scale?
The purpose behind the Shore D hardness scale, also known as the durometer scale, is to measure and compare the hardness values of materials such as plastics, rubbers, and elastomers. The results indicate how much force it takes to put an indentation into a given material. Higher numbers indicate greater hardness on the scale, which runs from 0 to 100. The Shore D scale is frequently used in sectors like construction and manufacturing to give designers an idea of the product’s quality and potential longevity.
How Is the Shore D Hardness Scale Used in Industry?
In an industrial setting, hard plastics, rubbers, and other materials are measured using the Shore D hardness scale. The Shore D scale utilizes a durometer to gauge how deeply a pointed object can pierce a material under a known, constant force. The material's hardness is then calculated using this depth measurement.
What Type of Materials Can Be Tested Using the Shore D Hardness Scale?
The materials that can be tested include thermoplastic elastomers, other hard rubbers, and rigid plastics. A diamond-tipped indenter's penetration depth is measured using the Shore D hardness scale to determine the material's hardness. This scale is especially helpful for testing materials that need to be highly rigid, such as automotive, athletic, and industrial components.
What Are the Benefits of Using the Shore D Hardness Scale for Material Testing?
The following are some advantages of conducting material testing using the Shore D hardness scale:
- High Precision: A material's hardness can be precisely measured using the Shore D hardness scale, enabling accurate comparisons between various materials.
- Wide Range of Applications: Numerous materials, including plastics, rubber, and composites, can be tested for hardness using the Shore D hardness scale.
- Quick and Easy: A Shore D hardness tester is a quick and simple tool found in many industries to determine a material's hardness.
- Portable: Materials can be tested on-site since Shore D hardness testers are portable.
- Non-destructive: The Shore D hardness test is non-destructive, in contrast to other methods of material testing, so test articles can continue to be used afterward.
What Are the Limitations of the Shore D Hardness Scale?
The Shore D hardness scale has some drawbacks, such as:
- Limited Range: The 0-100 range of the Shore D scale is not adequate for all materials.
- Material Dependency: Comparing hardness values between different materials can be challenging because different materials may respond differently to the same Shore D scale measurement.
- Surface Effects: A material’s surface finish can cause inconsistencies in Shore D measurements.
- Temperature Sensitivity: Temperature can have an impact on some materials' hardness, so it is important to compare hardness values measured under consistent temperatures.
- Operator Error: Shore D hardness measurements must be performed with precision, so the equipment needs careful calibration and operator skill.
How Is the Shore D Hardness Scale Determined?
The depth to which a specific indenter penetrates the material being tested under particular circumstances determines the Shore D value. A steel rod with a pointed, spring-loaded tip gets pressed with a certain amount of force into the material. The hardness value is then determined by measuring the depth of penetration and selecting the corresponding value from a durometer chart. Rubber, hard plastics, and similar materials are the most common targets for this technique.
If you’re using rubber, the durometer chart will offer suggestions on what level of rubber hardness would be appropriate for your particular application. For instance, if you want your material to absorb shocks and provide cushioning, you might want to select a rubber material with a lower durometer rating, which denotes a softer, more malleable rubber. A material with a higher durometer rating, indicating a harder, less pliable rubber, may be preferable if you need it to provide support or resist deformation.
How Does Temperature Affect Shore D Hardness Measurements?
Temperature has an impact on Shore D hardness measurements. Hardness values drop as the temperature rises. This is because the materials themselves soften with higher temperatures and allow for easier penetration by the indenter.
What Is the Range of Hardness Values on the Shore D Hardness Scale?
The Shore D hardness scale outputs values between 0 and 100. Higher values denote harder materials and greater resistance to indentation. A material is said to be very soft if it has a Shore D value of 0.
What Applications is Shore D Scale Used For?
Materials' hardness can be compared based on their Shore D rating. Here are a few examples of items or substances that are typically measured using the Shore D scale:
- Thermoplastic Polyurethanes (TPUs): Numerous products, including footwear, automotive parts, and medical equipment, use TPUs. The relative hardnesses of TPUs are typically compared using the Shore D scale.
- Acrylonitrile Butadiene Styrene (ABS): ABS is a thermoplastic polymer used to make car parts, home appliances, and toys. The Shore D scale is used to evaluate grades of ABS.
- Polycarbonate (PC): PC is a thermoplastic polymer used in a wide range of products, including automotive parts, medical equipment, and eyeglass lenses. PC hardness is typically measured using the Shore D scale.
- Polyethylene Terephthalate (PET): PET is a thermoplastic polymer used to create beverage bottles, food containers, and packaging materials. The hardness of PET is assessed using the Shore D scale.
What Types of Materials are Tested Using ASTM D2240?
Products and materials that are typically tested via the ASTM D2240 standard include:
- Thermoplastic Elastomers: This group of materials exhibits traits common to both elastomers and thermoplastics. They have elastic qualities similar to vulcanized rubber, but they can also be melted and remolded like thermoplastics.
- Vulcanized Rubber: This kind of rubber has undergone the chemical process of vulcanization, which involves heating it and adding sulfur to increase its elasticity, tensile strength, and durability. It is usually applied in goods like tires, hoses, and seals.
- Elastomeric Materials: These are materials with the capacity to stretch and then snap back to their original dimensions once released. To ensure a snug and secure fit, they are frequently used in goods like gaskets, seals, and O-rings. Neoprene, silicone, and polyurethane are some examples.
The ASTM D2240 standard covers Type A, D, and M durometer testing methods. It is not advisable to compare the outcomes of this method with those of other indentation hardness techniques; other methods use different tools and generate results that will appear inconsistent with Type A, D, and M results.
What Are Examples of Shore D Scale Standards?
Materials like plastics, rubbers, and elastomers are rated on the Shore D scale for hardness. Shore hardness scales simplify comparisons between materials that can otherwise be difficult to compare directly. You can use the durometer chart below to get a rough feel for different Shore D hardness values.
- Shore D-40: Hard-back book cover
- Shore D-50: Golf ball
- Shore D-60: Swivel wheel
- Shore D-70: Wooden ruler
- Shore D-80: Computer casing
- Shore D-90: Bone
Can Shore D Hardness Scale Measure Rubber Tires?
Yes, rubber tires can be measured using the Shore D scale. In fact, this scale was created especially to assess the toughness of materials like hard plastics and rubbers. Automotive tires tend to come in at a value of around 70.
Is Shore D Hardness Scale an ASTM Standard?
Yes, ASTM maintains a standard for the Shore D hardness scale. The ASTM D2240-15 Standard Test Method for Rubber Property—Durometer Hardness outlines the procedures for measuring the hardness of materials using the Shore D scale. This standard is widely used in industries that involve rubber and plastics.
Is Shore D Harder Than Shore A Scale?
Yes, Shore D is harder than Shore A. Shore A is designed for softer materials, whereas Shore D measures the hardness of harder materials. Both standards' output values run from 0 to 100, but the scales are not identical.
What Is the Difference of Between Shore D Hardness Scale and Shore A Hardness Scale?
The Shore A and Shore D scales differ in terms of the hardness ranges over which they can apply. The Shore A scale, which ranges from 0 to 100, assesses the hardness of softer elastomers like unvulcanized rubber. The Shore D scale, which uses a different 0-to-100 scale, measures the hardness of harder plastics. Both make measurements by pressing a spring-loaded indenter into the material using a specified amount of force. The depth of the indentation is then measured and compared against the appropriate table of values. Shore A and D differ in the amount of force applied, the shape of the indenter tip, and the scale of output values. You should be aware that the Shore hardness scales do not assess the material's actual physical attributes, such as tensile strength or resistance to compression. They simply reflect how resistant a material is to being indented under a particular set of circumstances.
Summary
This article presented Shore D hardness scale, explained what it is, and discussed various industries that use this scale for testing. To learn more about the Shore D hardness scale, contact a Xometry representative.
Xometry provides a wide range of manufacturing capabilities and other value-added services for all of your prototyping and production needs. Visit our website to learn more or to request a free, no-obligation quote.
Disclaimer
The content appearing on this webpage is for informational purposes only. Xometry makes no representation or warranty of any kind, be it expressed or implied, as to the accuracy, completeness, or validity of the information. Any performance parameters, geometric tolerances, specific design features, quality and types of materials, or processes should not be inferred to represent what will be delivered by third-party suppliers or manufacturers through Xometry’s network. Buyers seeking quotes for parts are responsible for defining the specific requirements for those parts. Please refer to our terms and conditions for more information.
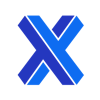