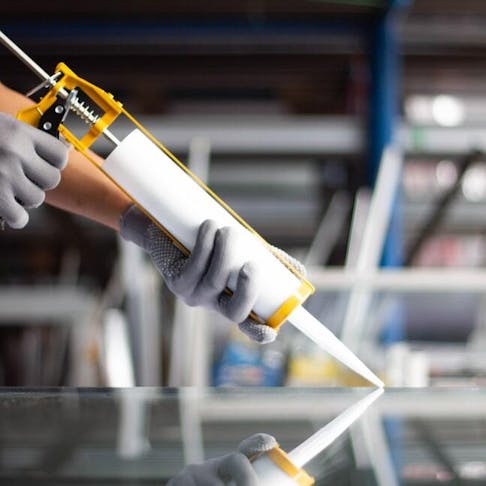
TPE vs. Silicone and Their Differences
Learn all about the differences between these two versatile materials.
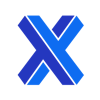
TPE, or thermoplastic elastomer, and silicone are two similar rubber materials that both have a variety of advantages. Both are often used in the process of injection molding. Silicone exhibits unique behavior at elevated temperatures and does not have a melting point, remaining solid until combustion occurs. At high temperatures (200-450C), silicone rubber will slowly lose its mechanical properties over time, becoming brittle. TPE has a melting point of 260-320C.
This article explains what the differences between TPE and silicone are. We will look at what kind of materials TPE and silicone are, as well as how to choose the right material, safety considerations, and how silicone and TPE should be used.
What Is Thermoplastic Elastomer (TPE)?
Thermoplastic elastomer, or TPE, is sometimes referred to as thermoplastic rubber. TPEs are a class of copolymers or a physical mix of polymers that consist of materials with both thermoplastic and elastomeric properties.
While most elastomers are thermosets, thermoplastics are relatively easy to use in manufacturing. Thermoplastic elastomers have the advantages typical of both rubbery materials and plastic materials. One advantage of using thermoplastic elastomers is the ability to stretch to moderate elongations and return to their original shape creating a longer life and better physical range than other materials.
For more information see our full Thermoplastic Elastomers (TPEs) Guide.
What Is Silicone?
Silicone, also known as polysiloxane, is best known for its flexibility and temperature resistance. Silicone is also flame-resistant, gas permeable, hypoallergenic, chemically inert, and nonstick. Silicone rubber is an elastomer, an elastic polymer with an inorganic silicon-oxygen backbone attached to organic molecules.
Silicone is not resistant to steam, hydrocarbon fuel, alkali, acid, trichloroethylene, or aromatic hydrocarbons. The material is generally found in electronics, industrial, aerospace, construction, automotive, medical, consumer product, and HVAC applications.
To learn more, see our guide on What is Silicone Material.
What Is Thermoplastic Elastomer Made Of?
A thermoplastic elastomer material is in a class of copolymers or a physical mix of polymers, which is usually a plastic and a rubber, that are made of materials with both thermoplastic and elastomeric properties. A thermoplastic elastomer is, therefore, a mix of plastic and rubber.
What Material Is Silicone Made Of?
Is silicone rubber or plastic? Scientifically, silicone lies in a gray area but is generally considered a rubber. It’s a human-made elastomer with both plastic and rubber properties. Silicone can be used to form liquids, hard solids, and rubbery products, but since elastomers are generally referred to as rubbers, it’s also usually referred to as rubber. Silicone is also easily confused with silicon, though they are different materials. Silicon is an element, while silicone is a polymer (a large molecule with repeating units).
What Is the Product Performance of TPE and Silicone?
TPE and silicone both make high-quality products. Silicone products have exhibited excellent properties, such as thermal conductivity, fire resistance, good chemical stability, flame retardancy, and excellent resistance to heat and cold, etc. TPE products are extremely versatile, naturally chemical resistant, cost-effective, and have outstanding thermal properties and material stability.
What Is Thermoplastic Elastomer’s (TPE's) Melting Point?
Thermoplastic elastomer has a melting point of 260-320 degrees C. The temperature resistance range of TPE is theoretically 130 to 150 degrees C, and above that range, TPE will age and crack.
What Is Silicone’s Melting Point?
Silicone does not have a melting point. It remains solid until combustion occurs. At high temperatures (200-450 degrees C), silicone rubber will slowly lose its mechanical properties over time, becoming brittle. The temperature resistance range of silicone is considered to be 200 to 300 degrees C.
What Is the Process of TPE and Silicone Injection Molding?
The process of silicone injection molding begins with a molding tool being created using CNC machining. This tool must be a high-temperature tool to withstand the silicone molding process. The tool may then be polished to allow for different finish options.
Next, the finished tool is loaded into a silicone-specific injection molding press that is precision geared to control shot size accurately. Materials used include standard silicones and specific grades to fit different part applications. Once the parts are ready, they are removed from the mold and then put to use as prototypes or production parts.
The process of TPE injection molding begins with TPE pellets being fed into the machine through a hopper and then into a heated barrel. The heat from the barrel turns the material into a liquid resin which is then injected into a closed mold under high pressure. After allowing the molten polymer to cool, the finished part can be removed from the mold.
The advanced properties of TPE compounds deliver short cycle times that allow parts to be produced rapidly.
When Should You Use Thermoplastic Elastomer (TPE) and Silicone?
The main difference between TPE and silicone is how they react to heat. After TPE is heated, it can be reprocessed. If you’re deciding between thermoplastic elastomer and silicone for a product, and it needs to be reprocessed, you should choose TPE. Silicone cannot be reprocessed or altered after heat has been applied.
Suppose you’re deciding between thermoplastic elastomer and silicone for a product that needs to withstand extremely high temperatures. In that case, silicone is the better option, as its temperature resistance range is much higher than that of TPE.
To learn more, see our guide on the Uses of Silicone.
How Do I Choose the Right TPE Materials?
To choose the right TPE materials, you should first consider what it’s replacing, what material is currently being used, where improvements are needed, or if there’s a price target. Next, make sure to note any functional or performance requirements.
Then, you should consider how the part will be manufactured and assembled through injection molding, extrusion, or blow molding. TPE formulations are made based on how the material is processed. For example, suppose the TPE will be over-molded or co-extruded onto another material. In that case, the over-molding or co-extrusion process must be considered, as a TPE that bonds well to one material won’t necessarily adhere to another.
Cost and environmental conditions should also be considered, such as whether or not the TPE product will be used indoors or outdoors and any temperature requirements.
How Do I Choose the Right Silicone Material?
To choose the right silicone, you should consider the required properties for the product’s intended purpose. The reality is there is no one single type of silicone that should be used for everything. Instead, many different types have different flexibility, durability, and resistance.
Consider the desired chemical, mechanical, and physical properties of the material when making a selection.
Is Thermoplastic Elastomer (TPE) Safe To Use?
Yes, it is safe to use thermoplastic elastomers. TPE is less likely to cause allergic reactions than latex. However, some people are concerned about the safety of TPE because it contains chemicals called phthalates. Phthalates are added to TPE to make it more flexible, but they can also harm human health.
Studies have linked phthalates to hormone disruption, reproductive problems, and cancer. However, it is essential to note that the levels of phthalates in TPE products are generally low and pose minimal risk to human health. As a result, TPE is legal to use and generally considered safe.
Is Silicone Safe To Use?
Yes, silicone is safe to use. Silicone is used for medical, electrical, and other applications. Because silicone is chemically stable, experts say it’s safe and likely not toxic. Additionally, according to the FDA, food-grade silicone cookware does not cause harmful chemical contamination of foods.
Summary
This article provided a summary of TPE vs. silicone and highlighted the differences between these two materials and their uses and toxicity.
Xometry provides a wide range of manufacturing capabilities and value-added services for all of your prototyping and production needs. Visit our website to learn more or to request a free, no-obligation quote.
Disclaimer
The content appearing on this webpage is for informational purposes only. Xometry makes no representation or warranty of any kind, be it expressed or implied, as to the accuracy, completeness, or validity of the information. Any performance parameters, geometric tolerances, specific design features, quality and types of materials, or processes should not be inferred to represent what will be delivered by third-party suppliers or manufacturers through Xometry’s network. Buyers seeking quotes for parts are responsible for defining the specific requirements for those parts. Please refer to our terms and conditions for more information.
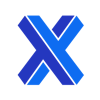