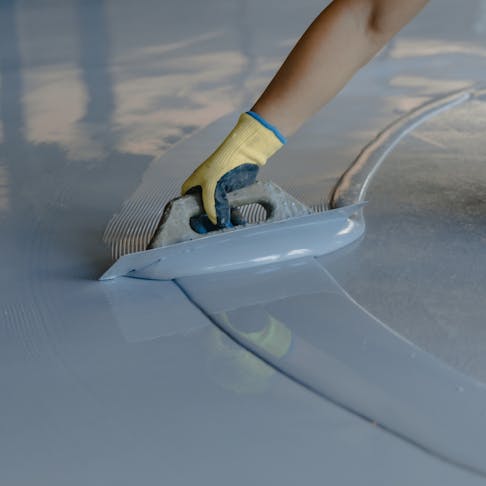
Epoxy: Definition, Properties, Types, and Classes
Learn more about this material and which factors to take into consideration when choosing a type to use for various applications.
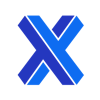
Epoxies are thermoset polymers, belonging to a huge family of materials. Their applications range from 3D printing to composites, dental molding, and protective coatings for steel structures. Epoxies are a key component in numerous advanced technical applications and are among the most relied-upon glues for difficult-to-bond materials. Epoxies are generally supplied as two liquid components to be mixed. They react together to produce highly cross-linked solids with a range of useful properties. This article will discuss What is epoxy?— its properties, types, and classes.
What Is Epoxy?
Epoxies are an extensive and complex family of thermoset polymers that are used for their excellent adhesive properties, high tensile and compressive strength, plus their chemical and thermal stability. Technically, epoxy resins are chemically reactive intermediates containing at least two epoxide or hydroxyl groups. They are stimulated to cross-link, resulting in polymerization into rigid three-dimensional chemical lattices of various types and regularities. Epoxies are widely used in various applications, in the industrial, automotive, aerospace, and construction sectors. They are widely employed as adhesives, coatings, and sealants. They are very effective at bonding unlike materials (metals, woods, stone, plastics, etc.) and acting as gap-filling agents to enable bonding between poorly conforming surfaces.
How Does Epoxy Work?
Epoxies work by turning from liquids (or pastes) to solids by cross-linking that builds between the epoxide groups. Generally, the cross-links are made between epoxide or hydroxyl groups present in the pre-polymerization resin. This results from two basic mechanisms, with variations in detail. The polymerization is a product either of the direct reaction of the resin molecules by the mechanism of catalyzed homopolymerization, or through a reactive additional chemical that acts as a coupling agent.
They are typically made by combining two chemical agents, the resin and a reactive copolymerizing agent OR a catalytic hardener that induces polymerization but does not integrate into the resultant molecule. When these two chemicals are combined in the correct proportions, a polymerization reaction causes the resin and hardener/catalyst combination to harden to a rigid and strong material. In a limited number of cases, the curing process is a UV-light-catalyzed reaction.
How Can Epoxy Help in 3D Printing?
Epoxies can be utilized in a variety of ways in 3D printing and post-processing of printed models. The materials are easy to handle and yet can be employed to create strong, durable, and complex structures. Some of its uses are listed below:
- As a coupling agent between the print bed and the printed object in FDM and FFF printing. They help improve table adhesion and thereby prevent warping or lifting during the print.
- As a penetrating coating on porous models, rendering them more resistant to abrasion and breakage. This can be useful in creating functional parts from FDM and FFF prints when greater durability is required.
- Applied as paints/coatings to 3D printed parts, to smooth and color them.
- Create molds from 3D printed parts, to allow multiple copies of a component to be cast in, for example, polyurethane.
- One of the key applications for epoxies in 3D printing is their use in material jetting technologies such as Objet. These are UV-light-cured epoxy resins that are directly printed by bubble jet methods.
What Is the History of Epoxy?
The history of epoxies started during the 1930s when polymers had become an area of intensive research for many scientists. Epoxies were created independently in the 1930s by Pierre Castan in Switzerland. He produced materials based on reacting bisphenol A with epichlorohydrin, and thermoset by reaction with phthalic anhydride. His work started in 1936 and his first patent was granted in 1940. Additionally, Paul Schlack, a German chemist, became a leading player in the epoxy sector where his earliest patent was granted in 1934. In 1942, Sylvan Greenlee researched for materials to use in dentistry. He independently discovered the reaction of bisphenol A (BPA) and epichlorohydrin (ECH) to make BADGE and was granted his first patent in 1948. By the 1950s, epoxies gained widespread use across many industries, with an explosion of new chemistries and polymerization/cure methods. Epoxy resins saw rapidly increasing use across many sectors, including aerospace, automotive, and marine industries. By the 1970s, the use of epoxies expanded into the consumer market, as manufacturing processes improved and material prices fell. This accelerated the development of epoxy adhesives and composites for use in the consumer, home, and hobby markets. Since then, epoxies have continued to evolve and improve, with new formulations and applications being developed all the time.
What Are the Properties of Epoxy?
Epoxies are a broad group, and they offer a wide range of properties as listed below:
- Have high tensile strength, compressive strength, and impact strength, which make them ideal for use in structural applications.
- Are resistant to many chemicals, including: acids, bases, solvents, and oils. This property makes them ideal for use in chemical processing and storage applications such as tank and reaction chamber coatings.
- Have excellent heat resistance, which makes them suitable for use in high-temperature applications, such as aerospace and electronics.
- Suffer limited shrinkage during curing, which ensures good dimensional stability and reduces the risk of cracking or distortion. Epoxies are excellent electrical insulators, which makes them ideal for use in electrical and electronic applications.
- Can be polymerized by UV-stimulated catalysts, thermal-triggered catalysts, and even moisture-cured processes.
- Have excellent adhesion to a wide range of substrates, including metals, plastics, ceramics, stone, wood, and composites. They are ideal for use in bonding and coating applications.
- Have excellent durability and can withstand harsh environmental conditions, including exposure to UV radiation, moisture, and saltwater.
What Are the Different Types of Epoxy?
Epoxies are one of the earliest synthetic polymer families to develop mass-market applications. The nature of the precursor chemicals gives rise to many different resin families and often many types within families. Listed below are some of the different types of epoxy:
1. Standard Epoxy
Standard epoxies remain derivatives of the earliest experimental materials from the 1930s to the 1950s. Various alterations in constituents have facilitated extra strength, higher resilience, and in some cases fast cure. The basic BADGE materials remain in service today as adhesives, moderate-temperature potting compounds, and casting resins. These materials offer toughness, high strength, low cost, and easy use for adhesion, repairs, furniture making, and many more applications.
2. Water-Based Epoxy
Water-based epoxies are two-component coatings that are applied in a water-dispersed form as sealing and waterproofing agents, particularly for “tank” sealing and dust control in concrete structures. They exploit an amine-based cure system and can be cleaned up with water, in the uncured state. Once cured (by a reaction that commences as the water content evaporates), they form an epoxy coating that offers similar physical properties to more traditional epoxies such as solvent-based epoxy coatings. The toxicity and irritant levels of these materials are much lower than the solvent-dispersed epoxies they compete with, making them much safer to use and easier to apply.
3. UV-Cured Epoxy
UV-cured epoxies can be premixed (resin and UV cure agent) or two-part materials. In either case, the UV-triggered catalysts/hardeners generally release acids that perform the curing process. This has the advantage of curing in partial shadow as the byproducts travel, allowing the continuance of cure after the light source is extinguished. They mainly consist of cycloaliphatic epoxy resin, generally precombined with a cationic photoinitiator. Widely employed in dental work, and in casting and artwork, these chemicals require careful handling and have moderate toxicity/irritant levels.
4. Structural Epoxy
Structural epoxies have some unique properties that make them an ideal adhesive for difficult bonding applications. They are viscous and do not slump, which makes them excellent gap-filling agents. Structural epoxies are highly electrically insulative, allowing them to be a barrier to galvanic/bimetallic corrosion. They offer very high water, impact, and abrasion resistance and can be machined effectively, even having threads tapped that offer high pull-out strength. Most are epoxy-polyamide formulations, with two (equal) parts epoxy and hardener.
5. High-Temperature Epoxy
These epoxies offer similar properties to general epoxy resins, except they can commonly withstand temperatures of 250 °C and up to 300 °C. They are extensively used in automotive and industrial equipment applications, particularly in coupling and repairs of piping and exhaust systems. They also tend to have very high chemical resilience and resistance to acids, opening other applications. They are commonly based on bisphenol F diglycidyl ether copolymers and use fatty acid dimers/tetraethylenepentamine polyamides and triethylenetetramine as cure agents.
6. Flexible Epoxy
Rubber/elastomer modified epoxies generally use fine elastomer beads as toughening agents, generally premixed into one of the two parts of the resin. In a limited number of recent developments, the elastomeric component has been made such that it becomes a reacted element of the resulting copolymer. This lends greater integrity and shock capacity to the final material. The use of amphiphilic diblock copolymers, which include epoxy miscible segments, has been shown to result in hydrogen bonding and the formation of nanostructures within the cured epoxy. These materials deliver improved shock tolerance and limited flexibility and are used in shock-vulnerable applications in bonding components in dynamic systems.
Recent developments include the commercialization of intrinsically flexible epoxies, for example containing 2,4,6 tris (dimethylaminomethyl) phenol, polyoxypropylenediamine bis [(dimethylamino)methyl] phenol, using (3-glycidyloxypropyl) trimethoxysilane as the reacting agent that triggers co-polymerization. Notable in this, apart from a lot of chemical naming that can confuse, is the silane component. Silanes and siloxanes are the key components in silicone rubbers, and their integration into the basic chemistry of epoxies is a revolutionary step. This results in tough, cured, and cross-linked materials that are epoxied in all regards but have Shore-D hardnesses as low as 20.
7. Conductive Epoxy
Conductive epoxies have varied uses in the electronics sector, in functions such as conductive traces on printed circuit boards (PCBs) and in repair pastes for etched copper tracks. They also serve extensively in anti-static applications as a conductive jointing mechanism between flexible conductive components such as wristbands and floor contacts and the rigid grounding that they must connect to. No epoxy has intrinsic conductivity for electrical current. The addition of moderate resistance materials such as finely divided carbon (or carbon fiber, fullerene, or graphene) allows the epoxy to carry low currents to the ground, or for signal purposes. The addition of finely divided silver particles can enhance conductivity to a great degree, allowing the transmission of higher-energy signals and even low-power sources.
What Are Different Classes of Epoxy Resin?
The different classes of epoxy resin are listed below:
1. Glycidyl Epoxy
Glycidyl epoxy refers to a class of epoxy resins that contain a glycidyl functional group (-O-CH2-CH(CH2OH)-) in their chemical structure. These resins are widely used in the manufacturing of coatings, adhesives, electronics, and composite materials. Glycidyl epoxy resins are formed through the reaction of epichlorohydrin and a compound containing reactive hydrogen, such as bisphenol A (BPA). This reaction produces a linear or branched epoxy polymer that has high chemical and thermal resistance, excellent adhesion, and good mechanical properties. However, glycidyl epoxy resins have been associated with health concerns, as they often release potentially harmful substances such as bisphenol A and glycidol. Regulatory bodies have established guidelines for the use of these materials in consumer products.
2. Novolac Epoxy
Novolac epoxy is a family of epoxy resins based on the reaction of phenolic novolac and epichlorohydrin. Phenolic novolac is a resin that is formed from phenol and formaldehyde, which results in a highly cross-linked structure. Novolac epoxy resins are highly cross-linked and offer improved thermal stability, chemical resistance, and electrical properties compared to conventional bisphenol A types. They are widely used in high-performance applications such as coatings, adhesives, and composites. Novolac epoxy resins are typically cured with amines. This involves the reaction of the epoxy groups in the resin with the curing agent, which results in a highly cross-linked network. Novolac epoxy resins may contain hazardous substances, such as formaldehyde and phenol, and appropriate safety measures should be taken when handling them.
3. Cycloaliphatic Epoxy
Cycloaliphatic epoxy contains a cycloaliphatic ring in its chemical backbone. These resins are known for their high-performance properties such as excellent chemical resistance, mechanical strength, and electrical insulation. Cycloaliphatic epoxy resins are synthesized from cycloaliphatic compounds and epichlorohydrin. The reaction between these two results in a more rigid and compact structure compared to conventional epoxy resins.
Due to their excellent properties, these resins are used in high-performance applications such as aerospace, automotive, and the electronics sector. They are also used in the manufacturing of composites, coatings, and adhesives. Like other epoxy resins, cycloaliphatic epoxy resins may contain hazardous substances and appropriate safety measures should be taken when handling these materials.
4. Aromatic Epoxy
Aromatic epoxies contain an aromatic ring structure in their chemical backbone. They are typically synthesized from bisphenol A and epichlorohydrin. Aromatic epoxies have excellent thermal and chemical resistance properties, as well as high strength and stiffness. They are commonly used in the manufacturing of coatings, adhesives, and composite materials that require high performance under harsh environmental conditions. However, it is important to note that some aromatic epoxies may contain hazardous substances, such as bisphenol A, which has been associated with potential health concerns.
5. Aliphatic Epoxy
Aliphatic epoxies contain aliphatic structures in their chemistry. Aliphatic structures are straight or branched chains of carbon atoms—unlike the ring structures in other resins. They are typically synthesized from compounds such as aliphatic alcohols or polyols, and epichlorohydrin. The reaction between these two compounds results in a more flexible and less rigid structure compared to other types of epoxy resins.
Aliphatic epoxies have excellent UV resistance and color stability, making them suitable for outdoor applications, such as coatings and adhesives for cars and boats. They are also commonly used in the food industry due to their low toxicity and low to zero odor. Some aliphatic epoxy resins may still contain hazardous substances, and appropriate safety measures should be taken when handling these materials.
6. Hybrid Epoxy
Hybrid epoxies are created by combining two or more resin types, or non-epoxy polymers. The resulting hybrid resin aims to combine some desirable properties of each component, allowing tuning of properties. A hybrid epoxy resin results from combining a cycloaliphatic epoxy with a novolac epoxy. They will acquire chemical and thermal resilience from the cycloaliphatic component and improved mechanical performance from the novolac part. Hybrid epoxy resins are used in high-performance applications where specific property combinations are required. They are often used in the manufacturing of coatings, adhesives, and composite materials for industries such as aerospace, automotive, and construction.
How To Use an Epoxy?
Listed below are some tips for using an epoxy:
- The surfaces to which the epoxy will be applied must be clean, dry, and free of any contaminants. Depending on the surface, sanding, degreasing, sandblasting, and potentially acid washing may be appropriate.
- Most epoxies require two components, the resin and hardener/catalyst, together in the proper ratio. The mixing ratio should be followed closely, as it affects the curing and final properties of the epoxy.
- The mixed epoxy should be applied immediately, using a brush, roller, or spatula. The epoxy should be applied evenly, without leaving any air pockets or areas of thin coverage.
- The epoxy must be allowed to cure fully, according to the manufacturer's instructions. This may involve a certain curing time and temperature range and these must be adhered to, as stressing or overheating part-cured epoxy will result in lower strength.
- Where UV cure is appropriate, it is wise to somewhat exceed the suggested time and intensity. This will assist in curing any shadowed or thicker areas that might otherwise be under-exposed.
How To Choose an Epoxy?
Selecting the most appropriate epoxy depends heavily on the specifics of the application and the performance requirements of the product. Listed below are some tips for choosing epoxy:
- Check the epoxy’s application, whether it's for adhesive, coating, or composite material. These applications often require particular properties, such as strength, flexibility, or chemical resistance.
- Check the material to which the epoxy will be applied. Various epoxies adhere better to particular substrates. An epoxy for metal will likely have different properties than one for wood.
- Check the conditions the epoxy will be exposed to. Elevated temperature, humidity, and aggressive chemicals will likely direct the selection of epoxy.
- Determine the cure time. Faster- and slower-cure epoxies are available, assuming other properties are sufficient.
- Check the potential health hazards associated with the epoxy, such as toxicity or flammability. Choose an epoxy that is appropriate for the application and can be handled safely, ensuring correct safety precautions are adhered to.
It is recommended to always follow the manufacturer's instructions carefully when using any type of epoxy, and take the necessary safety precautions.
What Type of Epoxy Is Best for Metal?
As a general guideline, two-part epoxies give the best results in metal bonding. The choice of which types of epoxy resin depend on the details of the application. Choose an epoxy that has the appropriate properties for the application and is developed for bonding metal surfaces. Some tips are listed below:
- Clear epoxy is ideal for bonding metals that require a cosmetic result, as it dries to a transparent finish.
- Toughened epoxies are developed to be more durable and impact-resistant than typical epoxy adhesives. They are a good choice for bonding metal parts that will be subject to stress or flexing.
- High-temperature epoxies are the right choice to bond metal parts that will be exposed to elevated temperatures, such as exhaust systems or engine parts. Take care that the temperature limit of the epoxy will not be approached too closely.
- Conductive epoxies are developed for use with electronics and can create a conductive bond between metal surfaces. Selection depends heavily on the desired or tolerated contact resistance and expected current flow at the joint.
For more information, see our guide on Metal.
What Type of Epoxy Is Best for Plastic?
There are many types of epoxy resins available that ostensibly bond well with plastics. However, it is important to take into account the nature of plastic. Listed below are some guidelines to follow:
- Plastic bonding agents are developed to bond with plastics. “Plastic bonding agents” generally means a selection of aggressive solvents and other chemicals that disrupt the bonded surface. This causes a degree of plastic welding while “gap filling” with the epoxy component. These epoxies must be handled with greater care because of the risk of respiratory and eye damage and high flammability.
- Fast-setting epoxies can be a good choice. They are developed to bond to a variety of surfaces, including plastics.
- Flexible epoxies are a good choice to bond plastics that will be exposed to stress or movement. These types of epoxies remain flexible even after curing, which helps to prevent cracking and breaking.
- Structural epoxies are the right choice to bond load-bearing parts. These types of epoxies are developed for strength and durability under heavy loads.
It's beneficial to choose an epoxy that is specifically designed for bonding plastics, as this will probably achieve a stronger overall bond.
What Type of Epoxy Is Best for Cement?
For bonding cement, various epoxies can give good results and are listed below:
- Concrete epoxies are developed for bonding cement and other porous, rigid, and brittle surfaces. They are intended to penetrate the material to a degree, increasing the bond strength by increasing material connection.
- Structural epoxies are developed for bonding load-bearing parts and unlike materials with poor surface conformance. These types of epoxies provide exceptional strength and durability, even under heavy loads.
- High-temperature epoxies are suited for bonding cement surfaces that will be exposed to elevated temperatures. This type of epoxy can be used to bond cement surfaces that will be exposed to temperatures up to 260 °C and potentially higher.
- Moisture-tolerant or water-based epoxies are developed to “wet” water-contaminated surfaces and cure in the presence of moisture and can be used to bond cement surfaces that are wet.
What Type of Epoxy Is Best for Polymer?
The type of epoxy best for polymers are plastic bonding agents, fast-setting epoxies, flexible epoxies, and structural epoxies. For more information, see our guide on Polymer.
What Are the Advantages of Epoxy?
The advantages of epoxy are listed below:
- Surface conformity and gap filling at bond.
- High attachment strength to the widest range of materials.
- High strength.
- Shock resilience.
- Temperature tolerance.
- Good hardness.
- Low cost.
- Easy use, method error tolerant.
What Are the Disadvantages of Epoxy?
The disadvantages of epoxies are listed below:
- Long cure times for high strength.
- Fast-cure epoxies are generally weaker.
- Toxicities and irritant chemicals are common, as are strong smells.
- Many epoxies are brittle.
- Poor coupling to low-energy surfaces.
How Long Does it Take for Epoxy To Cure?
Epoxies offer a wide spectrum of cure times—from minutes up to several days (for full strength). Often the cure time is closely related to the bond quality and overall material strength/toughness, so the trade-off in cure convenience can come at a cost.
How Do You Know When Epoxy Is Fully Cured?
For rigid epoxies, the material will generally be fully cured when it loses all indentability when pressed with a point or edge. In most cases, part-cured epoxies will dent with a fingernail. When they harden, they are generally at full strength. For flexible epoxies, this may not apply and manufacturers' curing schedules should be considered. Some epoxies require a very prolonged cure time to achieve full strength, so refer to the maker's recommendations to evaluate cure completion. Cure time can be accelerated with a slightly elevated temperature, but it is important not to exceed the maximum service temperature.
What Is the Life Span of Epoxy?
Epoxies have an unlimited functional life span provided that they are not exposed to attack from conditions that are outside their recommended limits. This includes: excess heat, radiation, UV, aggressive solvents, or excess stress.
Does Epoxy Break Easily?
Yes, epoxy breaks easily. Most basic epoxies are strong materials but they are brittle and cannot handle deflection well. This leads to easy breakage when general epoxies are used to bond more flexible components. Toughened and flexible epoxies go a long way toward reducing this vulnerability.
What Are the Alternatives for Epoxy?
Some alternatives to epoxy are listed below:
- Polyurethanes: Versatile polymers that are widely used as adhesives, coatings, and sealants. They offer an alternative to epoxy due to superior flexibility and resistance to impact and abrasion.
- Acrylic Adhesives: Are low toxicity and known for their fast cure times, which can be useful in applications in which speed is important. They also offer good resistance to weathering and UV radiation.
- Cyanoacrylates: Offer fast bonding and good strength, but are not as durable as epoxies. For perfectly fitting surfaces they offer good bond strength and durability when not flexed, but they have no gap-filling ability. Toughened cyanoacrylates improve flexural weakness.
- Silicone Adhesives: Offer excellent flexibility and resistance to high temperatures and weathering. They are often used in applications that require a strong, flexible bond, such as sealing joints in plumbing or electrical applications.
Summary
This article presented epoxy, explained what it is, and discussed its various types and properties. To learn more about epoxy, contact a Xometry representative.
Xometry provides a wide range of manufacturing capabilities and other value-added services for all of your prototyping and production needs. Visit our website to learn more or to request a free, no-obligation quote.
Disclaimer
The content appearing on this webpage is for informational purposes only. Xometry makes no representation or warranty of any kind, be it expressed or implied, as to the accuracy, completeness, or validity of the information. Any performance parameters, geometric tolerances, specific design features, quality and types of materials, or processes should not be inferred to represent what will be delivered by third-party suppliers or manufacturers through Xometry’s network. Buyers seeking quotes for parts are responsible for defining the specific requirements for those parts. Please refer to our terms and conditions for more information.
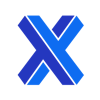