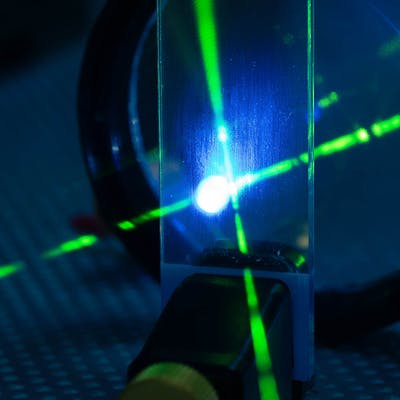
Laser Lens: Use, Importance, How to Take Care of Them
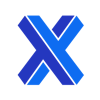
Laser lenses are optical components that are used in various laser applications. They are responsible for shaping and directing laser beams for tasks like: cutting, engraving, and marking.
This article will explore laser lenses, discussing their types, functions, and uses, and how to take proper care of them.
What Is a Laser Lens?
A laser lens is an optical component specifically designed for laser use to manipulate laser beams. These lenses can focus, collimate (make parallel), or diverge laser light, depending on their design and the requirements of the application. Laser lenses cover a wide wavelength range from ultraviolet (UV) to visible, near-infrared (NIR), and long-wave infrared (LWIR), which cater to different laser types such as: CO2 lasers, fiber lasers, solid-state lasers, and laser diodes.
What Is the Use of Laser Lens?
Laser lenses are used to modify the properties of a laser beam to suit specific applications. This includes: focusing the beam to a small spot for precision cutting or engraving, collimating the beam to keep it parallel and focused over long distances, and shaping the beam into specific patterns for applications like scanning or medical imaging. Laser lenses are used for a wide range of applications, including: material processing (cutting and welding), precision tasks (scanning and dimensioning), and creating specific patterns or lines. They also play key roles in laser collimation, illumination, and tracking.
The Importance of Laser Lenses in Laser Cutting Equipment
Laser lenses are crucial for laser cutting equipment because they allow for the precise focusing of the laser beam, which enables high-precision cuts with clean edges. The ability to select lenses with different focal lengths also makes it possible to optimize the cutting process for a variety of materials and thicknesses.
To learn more, see our full guide on Laser Power.
What Are Laser Applications That Rely on Laser Lenses?
Laser applications that rely heavily on laser lenses include: material processing (like cutting, welding, marking, and engraving), medical procedures (such as surgeries and imaging), scientific research (for precise measurements and spectroscopy), and manufacturing (specifically in additive manufacturing or 3D printing). Other applications include optical communication, in which lenses collimate beams for long-distance data transmission, and consumer devices like barcode scanners and laser pointers, in which lenses shape the beam for specific uses.
What Are the Different Types of Laser Lenses?
Laser lenses come in various types, each with its functions within laser applications. Here are some of the common types:
- Spherical: These lenses have surfaces that are portions of a sphere and are used to focus or diverge light. These lenses are classified into various types based on their shape: plano-convex and plano-concave lenses have one flat and one spherical surface; meniscus lenses feature both concave and convex surfaces; bi-convex and bi-concave lenses possess two spherical surfaces. Plano-convex lenses (flat on one side and bulging outward on the other, used for focusing laser beams) and plano-concave lenses (flat on one side and indented inward on the other, used for beam expansion or collimation correction) are the most common spherical lens configurations. Plano-convex lenses are mainly used to focus parallel beams/rays to a single point, whereas plano-concave lenses, with a negative focal length, are used for beam expansion, light projection, or to expand the focal length of any optical system.
- Aspherical: Unlike spherical lenses, aspherical lenses have a more complex surface profile that can reduce spherical aberration, allowing for more precise control over the laser beam's focus with no blur. They are particularly useful in applications requiring tight focus or high beam quality.
- Cylindrical: These lenses are curved in only one direction and flat in the perpendicular direction, used to focus or shape laser light in one direction or to correct astigmatism in laser beams. They are available in two main configurations: plano-concave, which is used to diverge light, and plano-convex, used to converge or focus light. They are essential in applications like laser line generation.
- Powell: Powell lenses are a type of laser line generator lens designed to create uniform, straight laser lines with a more even energy distribution across the line, compared to traditional cylindrical lenses that often produce lines with Gaussian intensity profiles (bright in the center and fading towards the ends). The unique design of Powell lenses involves an aspherical surface that refracts the laser beam in a way that spreads the intensity more evenly along the length of the line, resulting in uniform line illumination. They are ideal for applications requiring even line illumination, such as in barcode scanning or alignment.
- Axicon: Also known as conical lenses, are conical prisms that are used to transform a laser beam into a ring or to create Bessel beams for applications in optical trapping, microscopy, and laser machining.
Can a Blurry Laser Lens Affect the Laser Cutting Process?
Yes, a blurry laser lens can negatively impact the laser cutting process. A lens that is not clear can scatter or distort the laser beam, leading to decreased precision and quality of the cut. This can result in wider kerf widths, rough edges, and inaccurate cuts. Additionally, it may require more laser power to achieve the desired cutting depth or speed, leading to inefficiencies and increased operational costs. To avoid this, it is important to perform regular maintenance and ensure that the lens is clean and clear for optimal cutting performance.
Do Laser Lenses Differ in Laser Engraving Applications?
Yes, different types of laser lenses can be used in both laser cutting and laser engraving applications. These lenses include: axicon, Powell, cylindrical, aspherical, and spherical focusing lenses. Each of these lens types has their own, intended applications.
To learn more, see our full guide on How Laser Engraving Works.
What Types of Materials Are Laser Lenses Made Of?
Laser lenses are manufactured from a diverse array of materials tailored to specific optical properties and laser wavelength compatibilities. Some common construction materials include:
- N-BK7 glass
- Sapphire
- Calcium fluoride (CaF2)
- Zinc sulfide (ZnS)
- Zinc selenide (ZnSe)
- Magnesium fluoride (MgF2)
- Gallium arsenide (GaAs)
- Germanium (Ge)
- Silicon (Si)
- UV-grade fused silica
How Do You Maintain and Care for Laser Lenses?
Laser lenses are very delicate components and should be handled with great care. Lenses are very susceptible to damage like scratches; it is, therefore, important to always handle them with clean, dry hands and avoid touching the lens. Use lint-free gloves if necessary. It’s also important to try and work in a clean and dust-free environment to prevent contaminants from settling on the lenses. The lenses should be inspected regularly for any signs of dirt, dust, or damage.
To clean the lenses the following steps can be taken:
- Use a clean, dry, and oil-free air source (such as a compressed air can or an air bulb) to blow away loose particles and dust from the lens surfaces. Blow air gently and at an angle to avoid scratching.
- Invest in a high-quality lens-cleaning kit that includes lens-cleaning solution and lens tissue or optical wipes. Avoid using regular tissues or cloth, as they can scratch the lens.
- Apply a small amount of lens-cleaning solution to the lens tissue or optical wipe.
- Gently wipe the lens surface in a circular motion, starting from the center and moving outward. Use minimal pressure.
How Do You Protect the Lenses of a Laser Cutting Machine Not in Use?
To protect the lenses of a laser cutting machine during periods when it is not in use, use lens caps or covers specifically designed for the machine's lenses to shield them from dust and potential damage. Before storage, clean the lenses properly to eliminate any contaminants. If no lens caps are available, store the lenses in dedicated protective cases or containers in a clean, dry, and controlled environment, adhering to recommended temperature and humidity levels. Avoid direct sunlight exposure, label lenses for easy identification, and handle them with care using lint-free gloves.
How Does Lens Design Impact Laser Performance?
Lens design significantly impacts laser performance by influencing factors such as: beam quality, focusability, and efficiency. The design determines the lens's ability to focus the laser beam to a precise spot, control beam divergence, and minimize aberrations. An optimal lens design enhances cutting, engraving, or marking quality and efficiency while minimizing heat-affected zones. Different lens types, shapes, and coatings are chosen based on specific laser applications and wavelengths to achieve desired performance outcomes. Proper lens design is critical for maximizing laser system performance and ensuring consistent and high-quality results.
How Long Do Laser Lenses Last?
The life span of laser lenses can vary depending on factors such as: their quality, usage conditions, and maintenance. Typically, well-maintained laser lenses can last for several years in industrial laser systems. However, in high-power laser applications in which lenses are subjected to extreme conditions, their life span may be shorter, often requiring more frequent replacement or maintenance. Regular cleaning and proper handling can help extend the lifespan of laser lenses. However, if you’d like to replace your laser lens preventatively, we recommend doing so yearly.
What Are the Environmental Impacts of Laser Lens Production?
The environmental impacts of laser lens production are primarily associated with the manufacturing process, material sourcing, and waste management. Production involves using raw materials such as glass or crystals (e.g., fused silica, calcium fluoride) which need to be mined and processed, contributing to environmental degradation and resource depletion. The manufacturing process consumes significant amounts of energy, especially for high-precision lenses, and may involve hazardous chemicals for cleaning and polishing lenses, leading to potential air and water pollution if not properly managed. Additionally, the production of specialized coatings for these lenses involves chemical processes that can produce toxic by-products. Waste management is another concern, as the production process can generate waste materials that need to be disposed of in an environmentally responsible manner to avoid contaminating landfills.
Do Laser Lenses Adjust Depending on the Type of Laser Wavelength Required?
No, laser lenses themselves cannot adjust their properties depending on the laser wavelength required. Laser lenses are specifically designed and manufactured for specific wavelengths. Different materials and coatings are used to optimize their performance at particular wavelengths. A lens designed for the specific wavelength of the laser source is used to accommodate different wavelengths.
Are Laser Lenses Removable?
Yes, laser lenses are typically removable and replaceable. They can be unscrewed or detached from their respective lens mounts or holders, allowing for easy replacement or maintenance when needed. This simplifies tasks such as: cleaning, inspection, and adjustments within laser systems.
What can Xometry Offer for Laser Cutting Projects?
Xometry offers a comprehensive range of services for laser cutting projects. They provide access to a vast network of manufacturing partners with expertise in laser cutting. Customers can upload their design files, receive instant quotes, and choose from various materials and finishes. Xometry caters to both prototyping and production needs, offering competitive pricing and quick turnaround times. With our advanced technology and dedicated support, Xometry is a one-stop solution for laser cutting projects.
Summary
This article presented laser lens, explained them, and discussed how to take care of them. To learn more about laser lens, contact a Xometry representative.
Xometry provides a wide range of manufacturing capabilities, including laser cutting and other value-added services for all of your prototyping and production needs. Visit our website to learn more or to request a free, no-obligation quote.
Disclaimer
The content appearing on this webpage is for informational purposes only. Xometry makes no representation or warranty of any kind, be it expressed or implied, as to the accuracy, completeness, or validity of the information. Any performance parameters, geometric tolerances, specific design features, quality and types of materials, or processes should not be inferred to represent what will be delivered by third-party suppliers or manufacturers through Xometry’s network. Buyers seeking quotes for parts are responsible for defining the specific requirements for those parts. Please refer to our terms and conditions for more information.
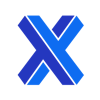