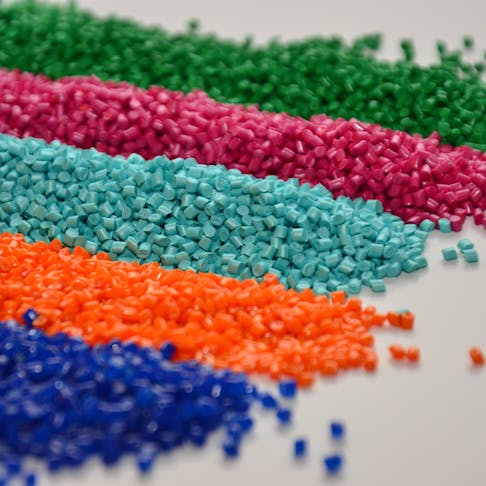
4 Top Tips on Processing High-Temperature Materials for Injection Molding
Even experienced molders can face challenges when using high-temperature materials for injection molding. However, with the proper equipment and a little extra know-how, processing such plastics can be just as easy as low-melt resins. This article will discuss tips and guidelines on how to process high-temperature materials for injection molding.
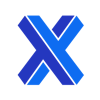
Even experienced molders can face challenges when using high-temperature materials for injection molding. These challenges can arise from inadequate equipment, improper material preprocessing, and poor mold design, among other things. Not all injection mold machinery is intended for high temperatures, so the process requires special considerations.
In the realm of molded plastics, high-temperature materials are those with continuous use temperatures (CUT) above 150℃. These plastics also typically require significantly higher processing temperatures — in the range of 300-450℃ (662°F-752°F). For molders accustomed to working with commodity resins or engineering plastics, transitioning to high-temperature, specialized resins can seem daunting. However, with the proper equipment and a little extra know-how, processing such plastics can be just as easy as low-melt resins. This article will discuss tips and guidelines on how to process high-temperature materials for injection molding.
Best Practices for Processing High-Temperature Material
High-temperature materials such as polyether ether ketone (PEEK), polyetherimide (PEI), and polyphthalamide (PPA), as well as some specialized polyoxymethylene (POM, also known as acetal) and nylon resins, are becoming more commonplace. For example, designers in the automobile industry have been steadily replacing metal parts with plastic-injected parts to improve their cars’ fuel efficiency. However, the field of high-temperature resins has far fewer experts than the CNC machining or plastic injection/extrusion industries.
Here are four top tips that can help molders process high-temperature materials for injection molding.
1. Use Appropriate Equipment
When processing materials such as PEEK or PEI, it’s important to ensure all equipment (i.e. press barrel, heater bands, temperature regulators, mold material, etc.) is designed to withstand high temperatures. While most standard injection machines can achieve these temperatures, some may require higher-specification heater bands and thermocouples. Generally, ceramic heater bands are the best choice for processing high-temperature resins because they have built-in insulation that ensures consistent operation and less heat loss. A general-purpose screw is normally sufficient, no matter the material. Learn more about injection molding here.
Some molds require hot runners to ensure quick injection cycles and less heat loss. Excessive cooling can lead to degradation in the material. When using hot runners, it’s important to ensure each input channel in the mold has its own heater and thermocouple to keep temperatures consistent.
2. Preprocess High-Temperature Materials
Dehumidifying or drying plastic resins is one of the most important steps toward achieving a high-quality injected part. Drying the resin is even more critical for high-temperature materials — especially hygroscopic materials that attract water from the surrounding environment. By dehumidifying high-temperature resins, most excess moisture within the resin is removed. Drying helps prevent surface defects such as splay or silver streaking caused by excess moisture. To determine the appropriate drying time, refer to the resin’s material specification sheet.
Additionally, drying the resin works to maintain the covalent bonds that hold the material’s polymer chains together. Moisture can break these polymer chains, negatively impacting the material’s mechanical properties. With high-temperature materials, even slight variations in moisture content can have profound effects on part quality. Therefore, it’s important to maintain rigid control over moisture levels before processing the material in a press.
3. Use The Proper Press Size
Another key to properly processing high-temperature materials for injection molding is to use the correct size of press for the material and the mold. Due to the nature of these materials, lengthy residence times in the barrel can lead to resin degradation. Degraded resin makes itself known in the form of flashing, burn marks or reduced-strength plastic. Long residence times can also result in excessive drool out the nozzle. Therefore, it’s important to determine the optimal press size which will minimize time spent in the lines while also achieving optimal injection velocities and pressures.
Generally, high-temperature resins should not have a residence time exceeding that prescribed by the manufacturer. Unfortunately, resins can easily wind up inside a barrel for much longer if the machine must sit idle when a molder is prototyping a new product or troubleshooting injection parameters. It is vital to periodically purge the resin while working or to completely remove it from the barrel if you expect the material to sit for over ten minutes.
4. Regulate The Melt Temperature
Maintaining a consistent temperature is important when processing high-temperature materials. Manufacturers must place strict control over the heater bands, hot runners, and thermocouples used to ensure temperature stability both in the barrel and the mold.
Most molds utilize heated water that circulates through the mold to maintain a specific temperature while the melted resin fills it. With high-temperature materials, however, the mold typically has to be much hotter - often around 125℃. Since this is above the standard boiling point of water, oil can be used in its place. Alternatively, pressurized water can achieve temperatures higher than 100℃. Molds should be designed such that each cavity receives equal heat transfer from its attendant water or oil lines.
No matter your experience level, processing high-temperature materials for injection molding can be challenging. Your first step should be to ensure all your equipment can withstand the specified temperatures. Second, make sure the plastic resin is dried per the manufacturer’s specifications. Next, choose properly-sized machine components that will minimize residence times in the barrel while still achieving optimal injection quality. Finally, make sure to keep the resin temperature as consistent as possible. Small temperature variations are enough to cause extensive quality defects.
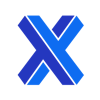