Centerless Grinding Services
High-quality Centerless Grinding Services in Days Not Weeks | Free Standard Shipping on All US Orders | Subject to availability. Xometry doesn't guarantee that we can provide this service at any given time.
Centerless grinding is a high-precision, cost-effective, and productive method of grinding standard cylindrical and custom profile components. Very little setup is required. The workpieces can simply be fed into the machine by hand and they will be ground to the predefined profile. Through-feed machines will drive the workpiece past the grinding wheel and it will exit the other side with precisely ground dimensions. Xometry can help you decide how centerless grinding can benefit your unique application.
Xometry offers centerless grinding as a value-added, turnkey service to our primary manufacturing processes, including CNC, 3D printing, injection molding, casting, sheet cutting, etc. A product can be fully customized using the Xometry Instant Quoting Engine®. Xometry does not provide secondary processing or finishing to parts supplied by a third party, with few exceptions.
Centerless Grinding Process
A centreless grinding machine typically consists of two wheels that rotate in the same direction. A workpiece is fed between these two wheels, and the difference in rotation speed between the two wheels determines the material removal rate. One wheel is fixed and cannot move perpendicularly to the axis of the workpiece. This is called the grinding wheel and is made of an abrasive material bound with an adhesive. The other wheel called the regulating wheel, can move such that it creates perpendicular pressure on the workpiece. The regulating wheel turns the workpiece. The workpiece is held in place on what's called a work rest blade which is positioned between the two wheels. These three components create a three-point contact on the workpiece which causes the workpiece to self-center, resulting in parts with high circularity and cylindricity.
There are four different types of centreless grinding machines as described below:
- In-Feed or Plunge Grinding: This process is used to manufacture parts with complex cross-sections as well as standard cylindrical parts. The grinding wheel is dressed to match the “mirror” of the desired part cross-section.
- End-Feed: This process is typically used to grind parts with a tapered profile. The workpiece is fed into the grinding wheel until it reaches a physical stopper, at which point it is removed.
- Through-Feed: This process is used to grind parts with a consistent cylindrical profile. The part is automatically drawn past the grinding wheel as the regulating wheel is set at an angle that pulls the workpiece axially into the grinding wheel and out the other side.
- Internal Grinding: This process is used to grind the internal surface of a cylinder and does this by sliding the workpiece over the grinding wheel. The regulating wheel then pushes the cylinder against the internal grinding wheel.
Centerless Grinding Materials
Centreless grinding can be used to process a wide range of materials, producing parts with superior surface finishes and extremely tight tolerances. While metals are the most common materials used in centreless grinding, plastics and ceramics are also popular choices.
- Metals
- Plastics
- Ceramics
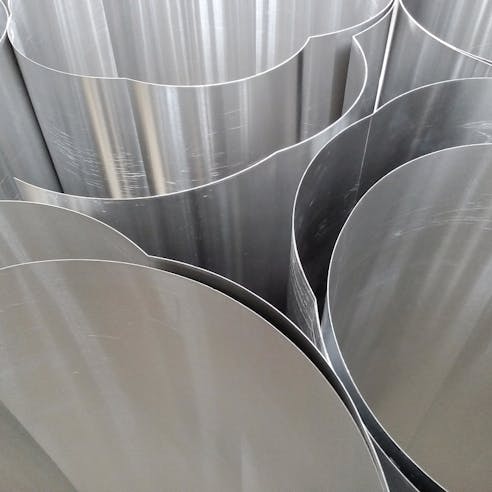
Metals
Metals are the most commonly used materials in centreless grinding. Extremely hard superalloys like Inconel® or soft metals like aluminum can be processed via centreless grinding, provided the correct grinding wheels, speeds, and feeds are utilized. Excellent surface finishes and extremely tight tolerances can be achieved.
Plastics
Plastics can be grounded to achieve tight tolerances. Coupled with their relative softness when compared to metals and ceramics, plastics are easy to grind but care must be taken to manage heat build-up as some plastics can melt or smear if speeds or feeds are incorrect.
Ceramics
Ceramics are extremely hard and brittle. Centreless grinding is ideal for processing these materials. However, specialized grinding wheels are required as ceramics are inherently abrasion-resistant and grinding is an abrasive process. Typically, diamond or CBN (Cubic Boron Nitride) wheels are used to grind ceramics.
Advantages of Centerless Grinding
Cylindrical grinding has a number of advantages. Key among these are: its high production rate, precision, minimal setup, and cost-effectiveness. These are described in more detail below.
High Production Rate
Centerless grinding is faster than similar processes such as CNC turning. This is because parts can be fed into the machine by hand and be naturally ground to the required dimensions and shape without the need to accurately set the workpiece, as is the case with turning.
Consistency
Centreless grinding has many features that aid in the creation of consistent, accurate parts. For example, the grinding wheel, regulating wheel, and rest blade create a three-point contact that improves circularity while the regulating wheel fully supports the workpiece and prevents any deflection. Centerless grinding is able to achieve tolerances of as little as 10 microns.
Minimal Setup
One of the key advantages of a centerless grinder is how quickly it can process a workpiece. Very little setup is required, and once the machine is running, it can continuously produce parts as they simply need to be fed into the grinding wheels. Through-feed machines automatically eject completed parts allowing for workpieces to be continuously fed into the machine.
Cost Effective
Due to its high productivity and minimal setup requirements, centreless grinding is very cost effective for producing cylindrical parts with relatively simple cross-sections.
In need of custom centerless grinding services?
Disadvantages of Centerless Grinding
Centreless grinding is a relatively niche manufacturing method that is limited to cylindrically shaped components. Listed below are some typical disadvantages of centerless grinding:
Limited to Cylindrical Shapes
The nature of centreless grinding means that typically only cylindrical parts or parts with a consistent radial profile can be processed. However, in some cases, indexing systems can be used to produce more complex features.
Limited Complex Shapes
It is possible to produce non-cylindrical parts. However, the level of complexity is limited to relatively basic cross-sections. This is because the grinding wheel must be dressed into the desired shape; as such, undercuts and deep, narrow features are not possible.
Concentricity with Existing Features
In some cases, pre-machined features like drill holes can end up not being concentric after the part has been ground. This is because the part will typically find its own center based on the workpiece irregularities. In such cases, a lathe might be better suited.
Centerless Grinding Applications and Industries Served
Centerless grinding is used in a wide range of industries due to its high productivity, low cost, and high precision. Listed below are some common industries in which this manufacturing technology is used:
- Manufacturing
- Aerospace
- Automotive
- Medical
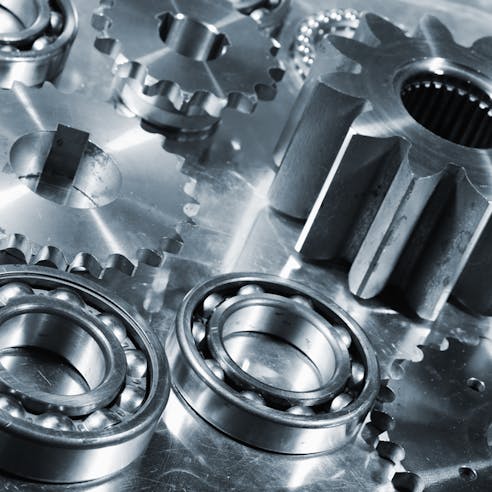
Manufacturing
Centreless grinding is useful when building machines or systems used in the manufacturing industry. For example, piston rods in hydraulic or pneumatic cylinders are used for actuation in automated systems and must be precisely ground while also being as smooth as possible to prevent air or hydraulic oil from leaking past the seals.
Aerospace
Centreless grinding is especially useful for processing high-hardness superalloys common in the aerospace industry. Components can include: shafts, fuel system parts, and bearings.
Automotive
The automotive industry makes extensive use of centreless grinding, especially for combustion engine components, which can include: crankshafts, piston pins, and axles. Centreless grinding is able to produce parts with repeatable tolerances, which is especially important for complex mechanical systems.
Medical
Centreless grinding is ideal for producing cylindrical components used in medical devices and equipment. For example, guide wires for stenting procedures are often produced on centerless grinding machines. This highlights the versatility of this process as both large industrial shafts as well as wire-thin medical devices are possible.
Alternatives to Centerless Grinding
Centreless grinding is a versatile manufacturing technique but is not always the best option for every grinding application, listed below are some common alternatives:
Cylindrical Grinding
In cylindrical grinding, the workpiece is held in a chuck, and the grinding wheel is introduced perpendicularly to the shaft axis. Much larger workpieces can be processed like this, but some setup time is required. In some cases, a center hole must first be drilled to align the workpiece in the machine.
Surface Grinding
Surface grinding is ideal for flat parts that must be made parallel or parts with an angular profile. It is typically used to make gauge blocks and fixtures for machines. Large, flat parts can be produced using this technique. However, it is not suited for producing cylindrical parts.
Honing
Honing is a process in which very little material is removed. It is primarily used for parts that require extremely high levels of precision. Honing is also used to polish parts as it uses a very fine abrasive grit and typically operates at slower speeds when compared to other grinding processes like cylindrical or centerless grinding.
Why Choose Xometry for Centerless Grinding Services?
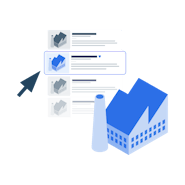
Endless Options
Choose from millions of possible combinations of materials, finishes, tolerances, markings, and certifications for your order.
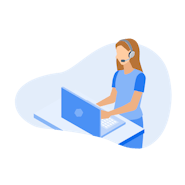
Easy to Use
Get started with our easy-to-use platform and let our experts take care of managing the project from locating the right manufacturing partner to delivery logistics.
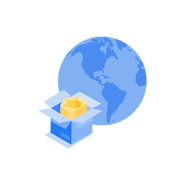
Vetted Network
We are ISO 9001:2015, ISO 13485, and AS9100D certified. Only the top shops that apply to become Suppliers make it through our qualification process.