Powder Coating Service by Xometry
High-quality Powder Coating Services in Days Not Weeks | Free Standard Shipping on All US Orders | Subject to availability. Xometry doesn't guarantee that we can provide this service at any given time.
Xometry offers powder coating as a value-added, turnkey service to our primary manufacturing processes, including CNC, 3D printing, injection molding, casting, sheet cutting, etc. A product can be fully customized using the Xometry Instant Quoting Engine®. Xometry does not provide secondary processing or finishing to parts supplied by a third party, with few exceptions.
Xometry provides powder coating services in a variety of colors, finishes, and materials. Our powder coating services provide a continuous, protective color finish on parts using evenly applied, heat-cured paint in several color options like red, orange, blue, black, and several other colors and in matte, gloss, and textured finishes. A powder coat provides a durable and vibrant finish to materials like aluminum, steel, and other metals that protect it from weathering, water, impacts, and other stresses. A variety of applications use powder coating, such as kitchen appliances, automotive painting, lawn and garden products, architectural and construction products, drum hardware, bicycle parts, and much more.
What is Powder Coating?
Powder coating is the process of applying protective coatings to surfaces by applying dry, electrostastically charged powders of typically thermoset or thermoplastic polymer onto a grounded surface using a specialized spray gun, forming a thin and even coat. Once applied, the coated surface is heated and/or cured to fuse the powder into a durable finish. Powder coating protects metals surfaces from corrosion, scratches, and other types of damage, and also provides a vibrant color finish.
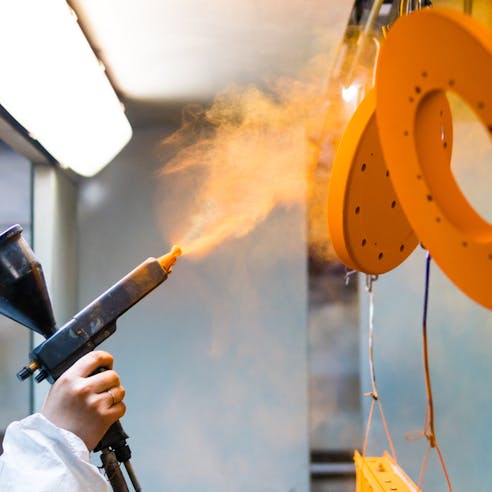
Powder Coating Process - How Does Powder Coating Work?
Powder coat application, as opposed to traditional liquid coating, is achieved through a multi-step process. The steps of the powder coating process typically include:
- Powder Preparation
- Surface Preparation
- Powder Application
- Curing
- Quality Control
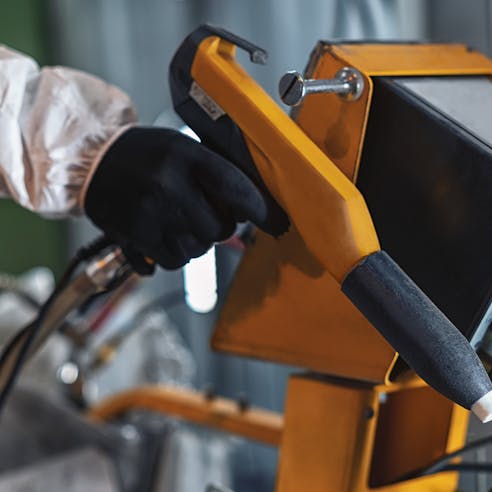
Powder Preparation
The polymer, hardneners, colorants, and other additives are blended together in a mixer. This mixture is then extruded, hardened, and then converted into small pieces, which are then milled into a uniform, flour-like fine powder.
Surface Preparation
The surface receiving the powder coat is cleaned and prepped by removing dirt, oils, and other contaminants. This may involve sandblasting, chemical degreasing, or other mechanical and chemical methods on a metal surface to ensure the surface is prepared for coating. It is essential to remove any contaminants to ensure a clean, smooth application.
Powder Application
The dry powder is applied to the surface, typically using a specialized spray gun that electrostatically charges the powder particles. The charged particles are attracted to the grounded surface and form a thin, even coat. A variety of nozzles help cater the powder coating process to unique part shapes, and in some instances the spray gun is replaced with a fluidized powder bed for commercial powder coating volumes.
Curing
Once the powder has been applied, the surface is then cured by heating it to a high temperature, typically between 350 and 400 degrees Fahrenheit. This fuses the powder into a smooth, durable finish. Newer powder coating blends allow for UV curing, which hardens the powder coat in just a few minutes at lower temperatures using ultraviolet light. This method is suitable for a variety of heat-sensitive materials and is also more energy and time efficient.
Quality Control
After the curing process, the coated surface is inspected to ensure that the coating is smooth and even, and that there are no defects or imperfections. Any necessary repairs or touch-ups are made at this stage.
It's important to note that these steps may vary slightly depending on the specific application and the type of powder being used. The specifications for each step will also depend on the specific requirements of the project, such as the type of surface being coated, the desired thickness of the coating, and the intended use of the finished product.
Powder Coating Finishes
The finish on powder coated parts come in the same range as conventional paint, and is capable of dead-matte to full-gloss appearances depending on the specific polymer blend and powder coating process used. Xometry’s powder coating services offers standard matte finishes for our powder coated parts, unless otherwise specified in notes attached to your quote. If you require a custom finish coating be sure to reach out during the quoting process and our fabricators will achieve the exact finish you need.
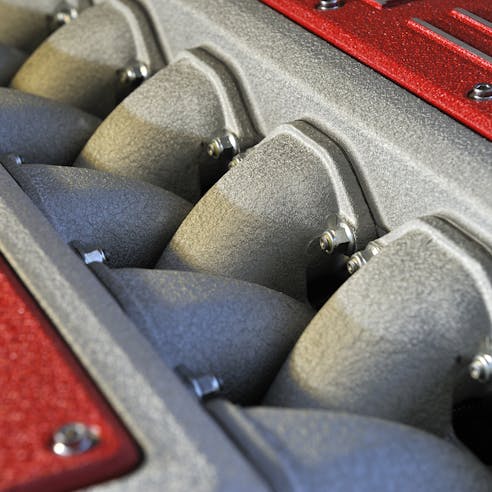
Powder Coating Materials
Here are some suitable materials that are commonly powder coated. Note that Xometry will work closely with you to achieve the right combination of material and finish if the below list does not contain your intended material.
- 5052 H32 Aluminum
- 6061 T6 Aluminum
- 7075 T6 Aluminum
- MIC6 Aluminum
- AR400 & AR500 Steel
- 4140 + 4130 Chrome-moly Steel
- 304 Stainless Steel
- 316 Stainless Steel
- A36 Steel
- Hot Rolled Steel
- Tool Steel
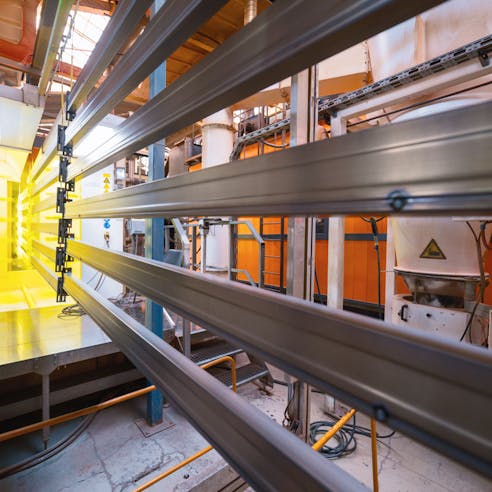
5052 H32 Aluminum
5052 aluminum in the H32 temper is a high strength, corrosion resistant aluminum alloy commonly used for general purpose applications like sheet metal and for applications like marine and transportation products, fuel tanks, architectural products, gutters, window frames, and many other uses.
6061 T6 Aluminum
6061 aluminum in the T6 temper is a high strength, lightweight, and easily machined aluminum alloy commonly used in the production of structural components for a variety of applications including aerospace components, automotive parts, recreational equipment, and construction uses.
7075 T6 Aluminum
7075 aluminum in the T6 temper is an exceptionally high strength and fatigue resistant aluminum alloy commonly used in the production of high stress structural components such as aerospace gears, shafts, aircraft fittings, and other components in extreme environments.
MIC6 Aluminum
MIC6 aluminumis a trademarked cast aluminum alloy plate by manufacturer Alcoa that is commonly used for tooling and base plates for automotive and aerospace components, as well as for jigs and fixtures.
AR400 & AR500 Steel
Abrasion-resistant (AR) 400 and 500 steel are high hardness steels specifically designed to withstand high levels of wear and tear, where they are commonly used in the production of body armor, ballistic plates, and shooting targets as well as in construciton and mining applications.
4140 + 4130 Chrome-moly Steel
4140 and 4130 chrome-moly (or chromoly) steel are types of low-alloy steel, where the “40” and “30” designate a 0.40% and 0.30% carbon by weight composition respectively. Both have a high strength-to-weight ratio, excellent tensile and fatigue strength, and good machinability, making them ideal for producing structural components and mechanical parts for automobile and bicycle parts, and tubular products for the oil and gas industry.
304 Stainless Steel
304 stainless steel is a type of corrosion-resistant stainless steel thanks to its high chromium and nickel content, making it suitable for a wide range of applications including food processing equipment, kitchen utensils, medical instruments, as well as construction and automotive parts, architectural features, window frames, and more.
316 Stainless Steel
316 stainless steel is a type of corrosion-resistant stainless stel with a high level of molybdenum and a lower carbon content than 304 stainless stel, making it exceptionally corrosion resistant and ideal for marine environments, medical implants, chemical processing equipment, as well as high wear construction and architectural applications.
A36 Steel
A36 steel is a low-carbon steel with good formability and weldability, making it suitable for use in a wide range of applications, including structural components, tanks, and welded bridges, as well as in the construction of buildings, automotive parts, and other fabricated products like pipes, rods, and beams.
Hot Rolled Steel
Hot rolled steel is a type of steel formed by rolling at high temperatures (> 1700 °F), resulting in a stronger and more malleable material useful for structural steel bars, sheet metal, and other stock for piping, beams, and automobile parts.
Tool Steel
Tool steel is a high-carbon, high-alloy steel that is specifically designed for tool manufacturing. Its ability to be heat-treated and withstand high levels of wear and abrasion make it ideal for punches, dies, cutting edges, hand tools, power tool bits, and automotive parts.
In need of powder coating services?
Benefits of Powder Coating
Some benefits of powder coating include:
- Improved Durability & Lifespan
- Enhanced Aesthetics
- Environmental Friendliness
- Cost-Effectiveness
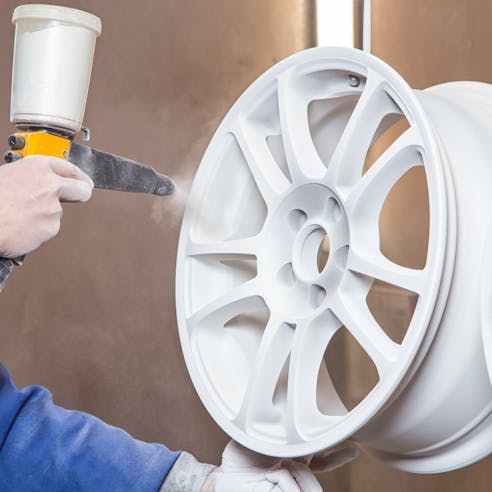
Improved Durability & Lifespan
Powder coating provides a protective layer on the surface of the material that is more durable and resistant to wear, abrasion, and corrosion than liquid coatings. Powder coating can also extend the lifespan of the material, as it is less prone to chipping, peeling, or fading than liquid coatings.
Enhanced Aesthetics
Powder coating can provide a smooth, even finish that enhances the appearance of the coated material and can be applied in a variety of colors and finishes.
Environmental Friendliness
Powder coating is a dry process that does not produce volatile organic compounds (VOCs) or other harmful emissions, making it a more environmentally friendly option than liquid coatings.
Cost-Effectiveness
Powder coating can be a more cost-effective option than liquid coatings, as it requires less material and produces less overspray, leading to lower material and disposal costs.
What Products Can Be Powder Coated?
Powder coating can be applied to a wide variety of products, and is only held back by how evenly the dry particles adhere to a given surface. Some examples of products that are regularly powder coated include:
- Automotive parts like car and truck wheels, bumpers, internals, and other components
- Appliances such as refrigerators, washing machines, and dryers
- Metal furniture such as tables, chairs, and outdoor patio furniture
- Industrial equipment such as conveyor belts, machinery parts, and storage tanks
- Home and garden products like grills, outdoor lighting, and fencing
- Sporting goods such as bike frames, golf clubs, and exercise equipment
- Signs and displays, frames, display stands, and other signage
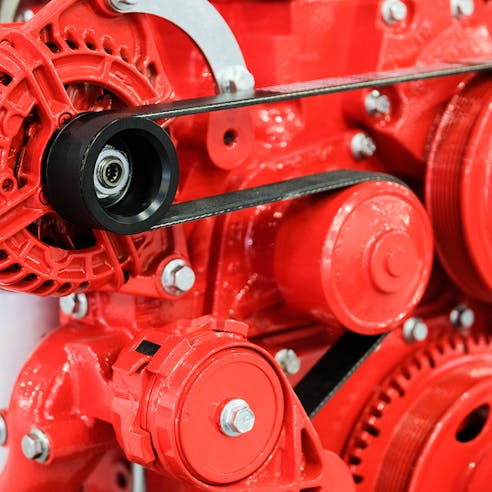
What Products Can't Be Powder Coated?
It is important to note that the suitability of powder coating for a particular material may depend on its specific characteristics and the coating process being used. In some cases, it may be possible to apply a powder coating to a material that is not typically suitable, but this may require the use of special coatings or pretreatment processes. That being said, there are generally some product categories that cannot be powder coated, such as
- Plastics, as the powder does not bond well to the surface and may cause the plastic to become brittle.
- Wood, as the powder does not adhere well to the surface and may cause the wood to become damaged.
- Glass, as the coating process may cause the glass to become brittle or shatter.
- Non-metallic materials like rubber, fabric, or paper, as powder does not bond well to these surfaces.
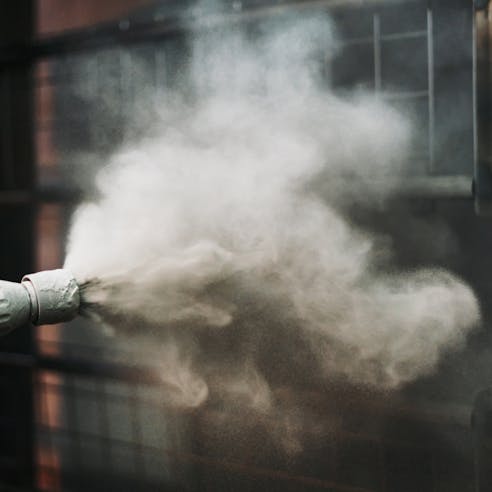
Design Considerations for Powder Coating
When surface finishing a product with powder coating, there are some key design considerations that must be taken into account, such as:
- Tolerances & coating thickness
- Material surface
- Color
- Cost
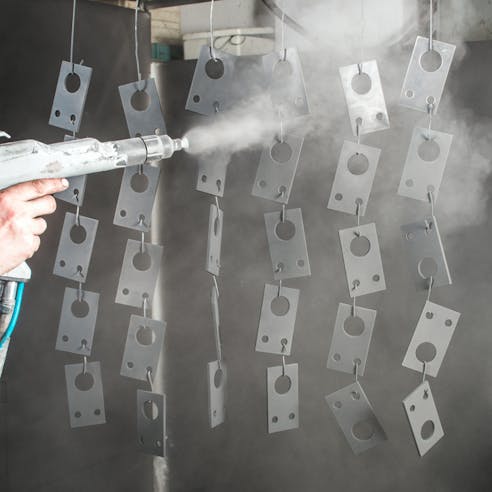
- Tolerances & coating thickness: The thickness of a typical powder coat adds .006”-.012” of surface thickness, which can throw off some low-tolerance builds or through-hole diameters. The thickness of the powder coat should also be appropriate for the intended use of the part – too thin of a coat may not protect the part, while too thick of a coat may result in warped tolerances and uneven surfaces.
- Material surface: parts with porous surfaces may require special primers or other treatments to ensure proper adhesion of the powder coat. Also, ensure that all surfaces are properly degreased, cleaned of contaminants, and are dry and smooth to achieve the best results.
- Color: color can impact the overall appearance of the finished part, so it is important to carefully consider the desired color and ensure every part is powder coated in the same method and with the same coating powder. Different powder blends will result in different end colors, which may cause unintended color mis-matching and an inconsistent look.
- Cost: though economical, powder coating and its cost can vary based on the size and complexity of the part, as well as the desired finish and color. Some complex parts will require more attention, and therefore labor and time to powder coat, where it may take less resources to simply plate the part.
Why Choose Xometry for Powder Coating Services?
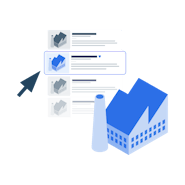
Endless Options
Choose from millions of possible combinations of materials, finishes, tolerances, markings, and certifications for your order.
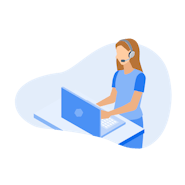
Easy to Use
Get started with our easy-to-use platform and let our experts take care of managing the project from locating the right manufacturing partner to delivery logistics.
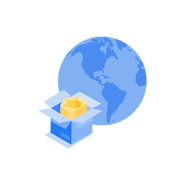
Vetted Network
We are ISO 9001:2015, ISO 13485, and AS9100D certified. Only the top shops that apply to become Suppliers make it through our qualification process.