Custom Plastic Injection Molding Service
Get custom plastic molded prototypes and production parts in as few as five business days. We provide expert engineering reviews and $500 off your first mold. Dozens of materials and finishes are available.
What Is Injection Molding?
Injection molding is the most cost-effective way to make a plastic part at scale. The injection molding process involves injecting molten plastic into a mold tool, then ejecting the solidified part. This process quickly repeats hundreds or thousands of times, amortizing the cost of the mold tool and driving down the cost of each unit to a few dollars or less. Since the injection molding process uses the same mold tool for each part, it offers consistent quality across every part. Injection molding also has the highest variety of materials, colors, cosmetics, polishes, and surface textures when compared to CNC machining or even 3D printing.
Xometry's custom injection mold service is a service providing on-demand prototype and production molding. We take a customer-first approach which means we find the right injection molding supplier within our manufacturing supplier network to mold the parts the way you need them—without design compromises—at the right price point. We offer expert consultation on each injection mold quote and project managers on every order to move your parts from design to production. Our team has experience in every industry, especially medical injection molding and liquid silicone rubber molding. First-time buyers receive $500 off their first mold with Xometry. We offer both domestic and China injection molding options, as well as ITAR injection molding.
Injection Molding Services Capabilities
Service | Details |
---|---|
Service Lead Time | Details Starts at 5 business days, including fast quote responses with design-for-manufacturing (DFM) feedback |
Service Production Options | Details Domestic and international |
Service Materials | Details Most plastics, including custom sourcing and matching; see materials list below |
Service Machines Available | Details Single, multi-cavity, and family molds; 50 to 3,700+ press tonnage; automated side actions or hand-loaded cores. |
Service Inspection and Certification Options | Details Includes FAI and PPAP. ISO 9001, AS9100, ISO 13485, UL, ITAR, and ISO 7 and 8 Medical Clean Room molding. |
Service Tool Ownership | Details Customer-owned with mold maintenance |
Service Mold Cavity Tolerances | Details +/- 0.005" when machining the mold and an additional +/- 0.002" per inch when calculating for shrink rate |
Service Part to Part Repeatability | Details +/- 0.004" or less |
Service Critical Feature Tolerances | Details Tighter tolerances can be requested and may increase the cost of tooling because of additional sampling and grooming. Xometry will mill to a steel-safe condition on critical features. |
Service Available Mold Types | Details Steel and aluminum; Production grades range from Class 105, a prototype mold, to Class 101, an extremely high production mold. Xometry typically produces Class 104, 103, and 102 tools. |
This table depicts the general tolerances for Xometry’s plastic injection molding service and accounts for adequate draft, radii, and coring for manufacturability. Learn more about our injection molding manufacturing standards.
Looking for Quick-Turn Molding and Parts?
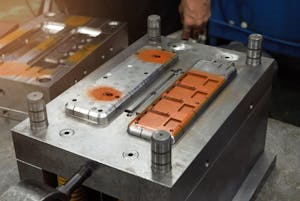
Quick Turn Injection Molding
Xometry Injection Molding Mold Classes
What is a SPI Mold Classifcation?
Standard injection mold tooling is defined by classes from Class 105 (prototype) to Class 101 (high volume production). These mold classes help manage expectations for both customers and suppliers on the overall tool requirements and scope.
What is a Class 105 Mold?
Under 500 cycles. Prototype only. This mold will be constructed in the least expensive manner possible to produce a minimal quantity of prototype parts. Class 105 molds are also known as Class V tools.
Example: a one-and-done market test of 100 molded units.
What is a Class 104 Mold?
Under 100,000 cycles. Low production mold. Use only for limited production, preferably with non-abrasive materials. Low to moderate price range. Class 104 molds are also known as Class IV tools.
Example: Aluminum or MUD tooling, SPI B-3 finish, hand-loaded cores, and limited re-runs.
What is a Class 103 Mold?
Under 500,000 cycles. Medium production mold. This is a very popular mold for low to medium-production needs. Most common price range. Also known as a Class III tool.
Example: Aluminum or steel tooling, automated lifts or slides, multiple re-runs with batches between 1,000-5,000 units.
What is a Class 102 Mold?
Medium to high production tooling, suitable for abrasive materials or parts requiring close tolerance. This is a high-quality, reasonably high-priced mold. Class 102 Molds are also known as Class II tools.
Example: Steel tooling with an SPI A-2 finish, automated slides, scheduled production cycles.
What is a Class 101 Mold?
Over 1,000,000 cycles. They are engineered for extremely high production. This is the highest-priced mold and is made with only the highest-quality materials. Class 101 molds are also known as Class I tools.
Example: Multiple-cavity steel tooling with full automation and overnight production work centers for dedicated part manufacturing.
Additional Molding Options Available at Xometry
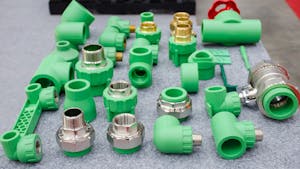
Insert Molding Service
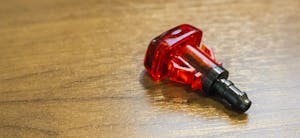
Overmolding Service
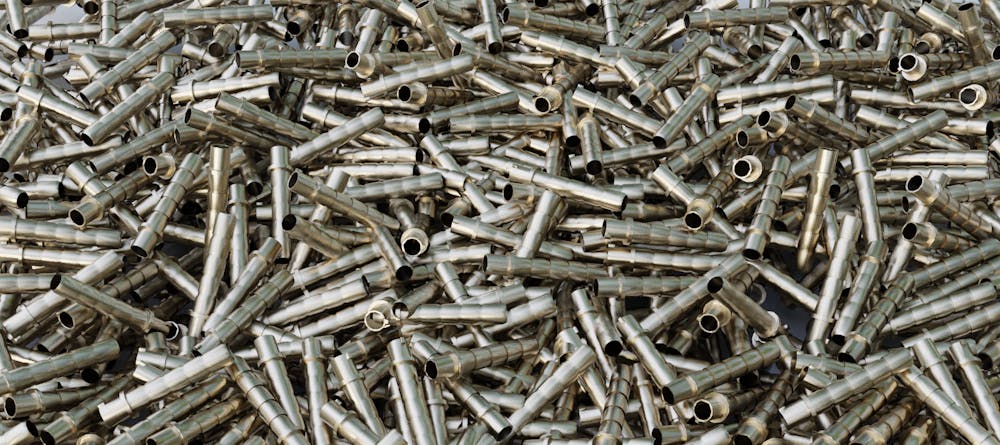
Metal Injection Molding Service
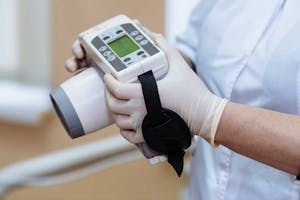
Medical Injection Molding Service
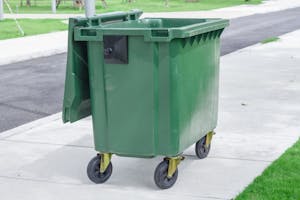
Gas Assist Injection Molding
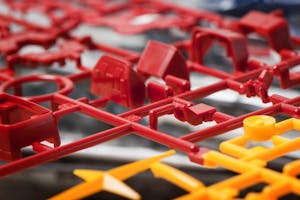
China Injection Molding Service
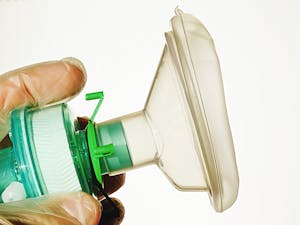
Liquid Silicone Rubber Molding
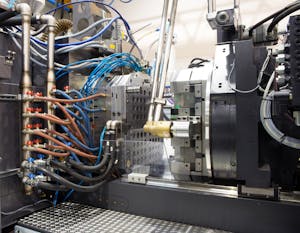
Large Part Injection Molding Service
How Custom Plastic Injection Molding Works
The plastic injection molding process requires an injection molding machine, raw plastic material, and a machined mold. The raw plastic material is first melted in the injection unit and is then injected into the mold—most often machined from steel or aluminum—where it cools and solidifies into the final plastic part.
At Xometry, we first review your plastic injection molding online quote, then consult with you to ensure your specifications, lead time, and price fit your project needs. We then use your 3D part data to CNC machine a high-quality injection mold. Once the molded parts are created, Xometry sends ten part samples (T1) for approval. Once the mold is refined and approved, Xometry begins production. Xometry molds a variety of products and parts from the smallest medical insert up to large automotive, aerospace, and defense parts.
Custom Plastic Injection Molding Materials
Rigid Plastic Materials:
- ABS (acrylonitrile butadiene styrene)
High-strength general-purpose engineering plastic, used for many commercial products. - ASA (acrylonitrile styrene acrylate)
A material very similar to ABS with higher resistance to fading and better suited for outdoor use. - CA (cellulose acetate)
Typically used in eyeglasses and film, CA is a flexible clear material that can be used in food contact. - HDPE (high-density polyethylene)
Excellent strength-to-weight ratio and chemical resistance. It is often used for fuel tanks, connector insulators, and food containers. HDPE is also used in outdoor equipment like playgrounds. - LCP (liquid crystal polymer)
LCP has mechanics even at elevated temperatures as well as low dielectric constants. This material provides exceptional features for micromolding and thin walled components. LCP is popular for electrical connectors and interconnects as well as medical devices. - LDPE (low-density polyethylene)
A flexible and tough material with lower density versus HDPE. LDPE does not react to acids, bases, or alcohols. Useful for trays, snap lids, and general-purpose containers. - PA 6 (polyamide 6, nylon 6)
Offers increased mechanical strength, rigidity, good stability under heat, and/or chemical resistance. - PA 6/6 (polyamide 6/6, nylon 6/6)
Offers increased mechanical strength, rigidity, good stability under heat, and/or chemical resistance. - PARA (polyarylamide)
Often combined with infills such as glass or mineral fibers, PARA creates rigid parts with low creep and a slower rate of water absorption than nylon (PA). PARA is excellent for structural components in handheld and medical electronics. - PBT (polybutylene terephthalate, Valox)
A common electronic insulator with a polyester base. Highly used in automotive as a longer-wear alternative to nylon. - PBT-PET (polybutylene terephthalate-polyethylene terephthalate)
A compounded blend of PBT and PET. - PC (polycarbonate)
A clear or colored, lightweight, glass-like plastic that is heavily used across multiple industries. PC is impact resistant, holds great feature detail, and can be used for safety equipment, lenses, electronic devices, and much more. - PC-ABS (polycarbonate-acrylonitrile butadiene styrene)
The best of both PC and ABS. Higher-strength engineering thermoplastic with slightly more flexibility than standard polycarbonate. - PC-PBT (polycarbonate-polybutylene terephthalate, Xenoy)
A tough and rigid material resistant to lubricants, solvents, and cleaning agents. Very common in electronic enclosures. - PC-PET (polycarbonate-polyethylene terephthalate)
A blend of PC and PET provides tough and chemically resistant results and can be used as an alternate to PC-ABS. It endures harsh solvents and cleaners, making it excellent for sports equipment and healthcare applications. - PCT (polycyclohexylenedimethylene terephthalate)
A thermoplastic polyester that typically outperforms PET due to lower moisture absorption and better environmental stability. PCT is often used for connectors and switches. - PE (polyethylene)
One of the most common plastics used in the world, PE has high ductility, abrasion resistance, and chemical resistance. PE is often described by its molecular weight, such as UHMW PE (ultra-high molecular weight), LDPE (low density), or HDPE (high density). PE is used in packaging, tubing, films, bottles, and more. - PEEK (polyether ether ketone)
Offering excellent tensile strength that surpasses most plastics, PEEK is often used as a lightweight substitute for metal parts in high-temperature, high-stress applications. PEEK resists chemicals, wear, and moisture. - PEI (polyetherimide, Ultem)
Known best for its extremely high heat and flame resistance, PEI is used for many medical applications and is more affordable than PEEK. - PE-PP (polyethylene-polypropylene)
A resin blend of the polyolefin’s polypropylene and polyethylene. - PE-PS (polyethylene-polystyrene)
A resin blend of the polyethylene and polystyrene. - PES (polyethersulfone)
A rigid, transparent plastic that is chemically inert, biocompatible, and sterilizable. PES is suitable for food-contact devices such as coffee machine components as well as aerospace and automotive where chemical exposure is high. - PET (polyethylene terephthalate, Rynite)
Also abbreviated PETE, this is a clear, strong, and lightweight PE resin heavily used in food packaging, soda bottles, jars, and more. The material is food-safe. PET is recyclable with a resin code of 1. - PLA (polylactic acid)
A biodegradable and renewable plastic. PLA has a relatively low glass transition temperature and is common in short-use applications. - PMMA (polymethyl methacrylate, acrylic)
A clear glass-like plastic. Good wear and tear properties. Great for outdoor use. - POM (acetal polyoxymethylene, Delrin)
Good moisture resistance, high wear-resistance, and low friction. - PP (polypropylene)
Polypropylene has excellent electrical properties and little or no moisture absorption. It carries light loads for a long period in varying temperatures. It can be molded into parts requiring chemical or corrosion resistance. - PPA (polyphthalamide)
A subset of nylons (polyamide) that typically exhibit a higher melting point and lower moisture absorption. PPA is typically used in automotive and industrial applications because it can withstand harsh chemicals. PPA is good for fuel and fluid manifolds and headlight housings. - PPS (polyphenylene sulfide, Ryton)
A high-performance thermoplastic with extreme resistance to solvents. - PS (polystyrene): A clear, hard, and brittle material widely used for food packaging, clamshell containers, and even disposable cutlery.
- PS-PPE (polystyrene-polyphenyl ethers, Noryl)
Exhibiting high heat and flame resistance, PPE-PS has high stiffness and tensile strength even at elevated temperatures. - PSU (polysulfone, Udel)
A rigid, stiff, and transparent plastic which is a higher-performance alternative to polycarbonate. - PVC (polyvinyl chloride (Shore D))
A rigid, general-use plastic that is common in plumbing, non-food packaging, and trimming. - PVDF (polyvinylidene fluoride, Kynar)
A chemically inert, high-temperature material. Due to its low friction, PVDF is used in plumbing parts, bearings, chemical handling, electrical wire insulation, and tubing. - SAN (styrene acrylonitrile)
A polystyrene that is heat resistant and transparent. Due to its relationship with polystyrene, SAN is low cost and has enhanced clarity and shine. SAN is common in household goods, door handles, and kitchenware. - TPO (thermoplastic polyolefin)
A flexible plastic with good chemical resistance but lower temperature resistance compared to PP. - TPU (thermoplastic polyurethane (Shore D))
A tough, highly abrasion-resistant resin that bridges the gap between rubbers and plastics. TPUs can be formulated to be rigid or elastomeric. TPU exhibits a high flex before break and is ideal for wheels and door panels.
Elastomer and Rubber Molded Materials:
Manufacturing elastomeric parts can be accomplished through injection molding, transfer molding, or compression molding. When getting a quote through Xometry, our team can help you decide the best method depending on the part geometry, estimated annual volume, and the type of material required.
- EPDM (ethylene propylene diene monomer rubber (Viton))
One of the highest performing rubber elastomers with high heat resistance, chemical resistance, and moisture sealing properties. EPDM is commonly found in automotive seals, gaskets, O-rings, and electrical insulators. - PEBA (polyether block amide)
A soft, flexible, plastic or elastomer used for medical devices such as catheters. PEBA foams are used for padding, shoe insoles, and sports equipment. PEBA is resistant to moisture and UV exposure. - PVC (polyvinyl chloride (Shore A))
A soft rubber-like, general use elastomer, that is common in outdoor products, protective films, and mats. Shore A rubber-like PVC requires plasticizers to improve its flexibility from its typical rigid state. PVC is flame retardant due to self-extinguishing properties. - TPE (thermoplastic elastomer)
A broad class of elastomers that behave like a thermoset with high flex and elasticity but process like a thermoplastic through molding. TPE is an umbrella term for many unique elastomer classes. - TPU (thermoplastic polyurethane (Shore A))
A tough, highly abrasion-resistant elastomer that bridges the gap between rubbers and plastics. TPUs can be formulated to be rigid or elastomeric. TPU exhibits a high flex before break and is ideal for flexible tires, skateboard wheels, and weatherproof gaskets. - TPV (thermoplastics elastomer, vulcanized rubber (Santoprene))
An excellent elastomer with high versatility due to temperature resistance, compression, and elasticity. - LSR (liquid silicone rubber)
Silicones are versatile rubber materials offering food and biocompatibility, extreme heat resistance, and excellent flexibility. LSR is used for medical devices, automotive, aerospace, and consumer products. Liquid silicone rubber molding is a specialized process different from traditional injection molding.
Several plastic injection molding, liquid silicone molding, and compression molding options are available for an online quote. If you do not see the material stock you are looking for, please choose “Other" under the material drop-down on your quote page and submit for an expert engineering review once you have specified features, tolerances, inspection needs, and quantities required.
Custom Injection Mold Finishes
Standard Finish
Moldmaker's choice of finish. Typically SPI B-2, depending on geometry and drafts. Interior, non-cosmetic faces, are typically as-machined.
SPI Finishes
Range of Society of Plastics Industry (SPI) finishes from Grade 3 diamond / high polish to 320 stone low polish. Finishes include: SPI A-1, SPI A-2, SPI A-3, SPI B-1, SPI B-2, SPI B-3, SPI C-1, SPI C-2, SPI C-3, SPI D-1, SPI D-2, and SPI D-3
MoldTech Finishes (Mold Texturing)
Range of finishes including matte, swirls, lines, and patterns. Our most common texture finishes include: MoldTech MT11010, MoldTech MT11020, and MoldTech MT11030. Other textured finishes can be added by request.
Other Textures - VDI
VDI 3400 Surface Finish (commonly known as VDI surface finish) refers to the mold texture standard set by Verein Deutscher Ingenieure (VDI), the Society of German Engineers. This is mainly processed by EDM machining, producing fine to coarse matte finishes.
As Molded
No secondary polishing or grinding. Part will show tooling marks.
Threaded Inserts
We can install most commonly used standard inserts in UNF and metric sizes.
Pad Printing
Transfer a 2D image onto a 3D part. All images are subject to review.
Laser Engraving
Engrave part numbers, logos, and more onto your parts.
Assembly
Xometry has the ability to assemble and label injection molded parts. Discuss your needs with your salesperson.
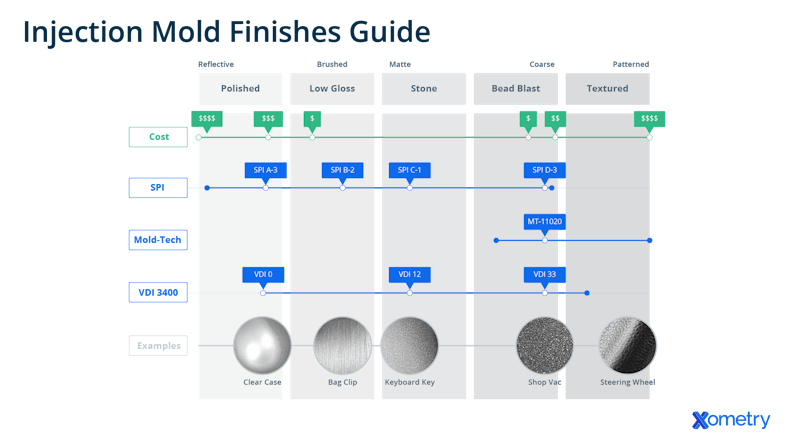
A guide to injection molding finishes
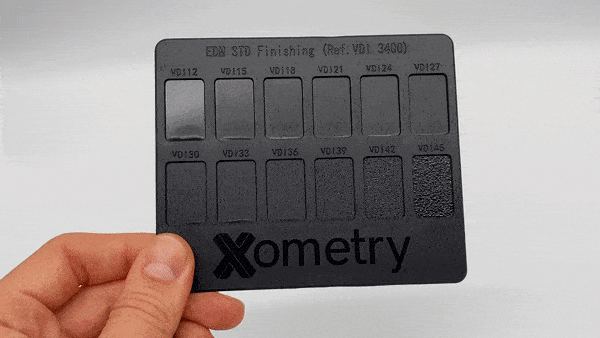
An Overview of Injection Molded Surface Finishes
Video: 7 Ways to Save on Injection Molding
Custom Injection Moldings Design Guidelines
Feature | Tip |
---|---|
Feature Undercuts | Tip Reduce undercuts, which will increase the complexity and cost of the tool ejection mechanisms, by adding in pass-thru coring. |
Feature Wall Thickness | Tip Prevent wall sink and voids by maintaining an even wall thickness. Thinner walls reduce cycle time and reduce costs. |
Feature Drafts | Tip Ensure parts are designed with a minimum draft angle of 0.5°, or up to 5°, for faces with medium textures. |
Feature Ribs/Gussets | Tip Ribs should be 40-60% the thickness of outer walls and should still maintain draft. |
Feature Bosses | Tip Bosses should be designed at a depth of 30% the wall thickness and with a 30% edge groove. Attach them to side walls or ribs for structural integrity. |
To see these design-for-manufacturing recommendations in detail, view our Injection Molding Design Guide.
Ready to Get a Custom Injection Molding Quote?
Applications and Advantages of a Plastic Injection Molding Service
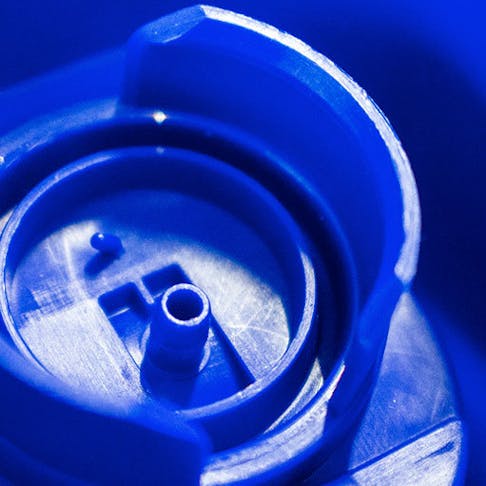
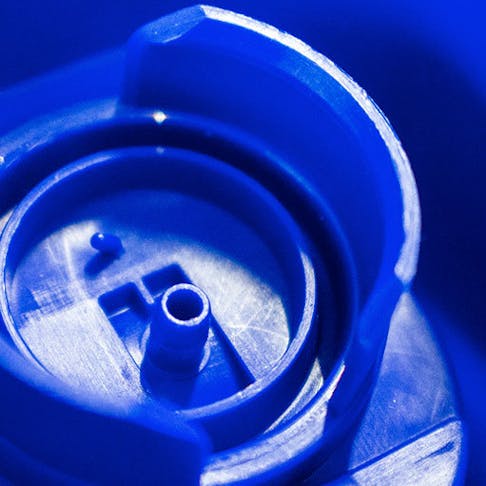
Low-cost tooling allows for rapid injection molding to be produced in as fast as 10 business days at affordable prices.
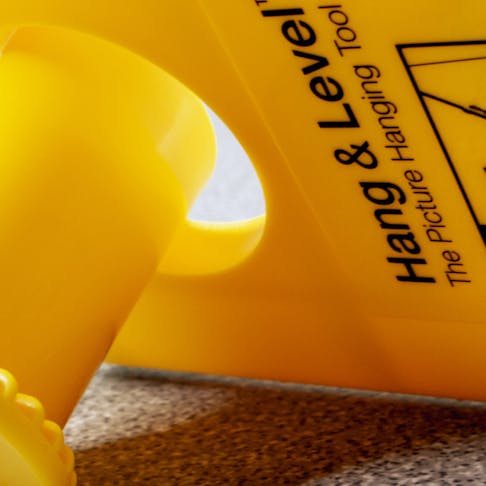
Custom injection molding can be the ideal process for low-volume production molding of 250 units to mass production molding of over 1,000,000 units. Plastic injection parts will generally perform better than the same part CNC machined or 3D printed using the same material. Careful selection of the resins allow for a wide range of properties and solvent compatibility. Molds are CNC machined to high precision, high tolerances and are able to produce thousands of identical parts with very small and intricate details.
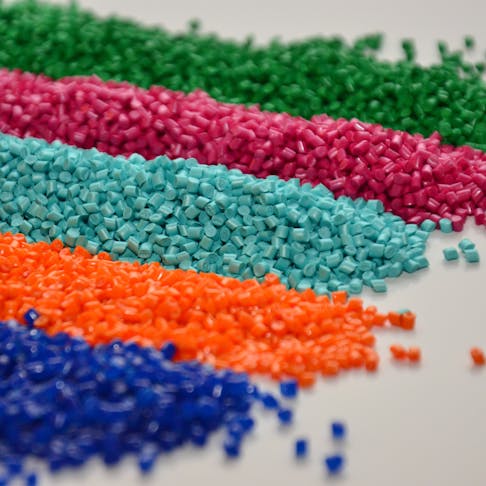
We offer ISO 9001, AS9100, ISO 13485, UL, ITAR, and ISO 7 and 8 Medical Clean Room molding.
Injection Molding FAQs
What industries use injection molding?
Injection molding is used across a wide range of industries including aerospace, medical devices, consumer goods, energy, electronics, automotive, robotics, toys, and more.
What is the difference between molding and printing?
With the molding process, plastic or metal parts are created inside a mold. They are then removed from the mold as fully-formed parts. 3D printing, on the other hand, is an additive manufacturing process, meaning that the part is built layer-by-layer using processes like deposition or sintering.
What is the process after ordering?
After receiving the order, the statement of work is reviewed by one of our manufacturing engineers. A case manager is assigned, and an appropriate manufacturing supplier is identified. A comprehensive DFM/PEG report is created and provided for approval. Upon approval, tooling and mold production is commenced. T1 samples are produced and shipped for approval. Upon approval, the remaining parts are made.
Who owns the tool?
At Xometry, our customers own their injection mold tools! After a run is complete, the tool will remain at our facilities. Tools can be shipped to you upon request; however, you will be responsible for any associated shipping and packaging costs. Our engineers will work with you regarding tool compatibility with your equipment if you're unsure.
Can you run different colors of the same material?
Yes, multiple colors can be run even on the same order! When running multiple colors on the same order, a purge charge will be added.
Why Use Xometry Injection Mold Services?
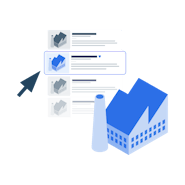
Endless Options
Choose from millions of possible combinations of materials, finishes, tolerances, markings, and certifications for your order.
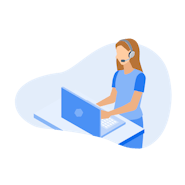
Easy to Use
Get your parts delivered right to your door without the hassle of sourcing, project management, logistics, or shipping.
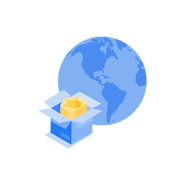
Vetted Network
We are ISO 9001:2015, ISO 13485, and AS9100D certified. Only the top shops that apply to become Suppliers make it through our qualification process.
Built-In Tool Management
Xometry's platform has built-in features that make managing tooled projects a breeze, giving customers greater transparency into production. Find all your tooling quotes and orders in one space with your Tool Library. From there, you can explore their Tool Details page, which covers the current status, milestones, tool specifics, and activity related to that tool. You can also easily find and contact the Xometry team member assigned to your project, no matter the project's current phase.
Our Tool Library and Tool Details pages provide multiple benefits, such as:
- Better Management of Tooled Quotes & Orders
- Tool Organization & Categorization
- Detailed Status Updates & Tooling Information
- Easily Connect with Experts
- Project Transparency
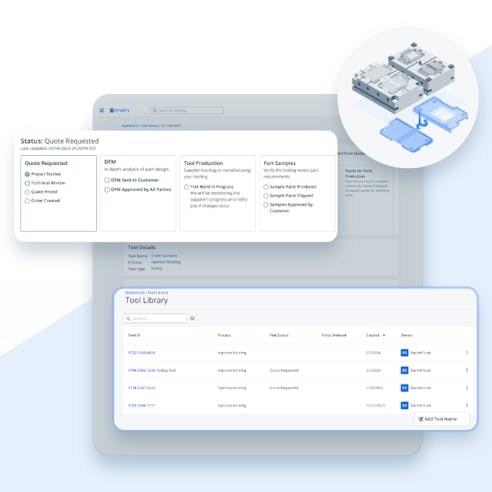
Xometry Plastic Injection Molding Case Studies
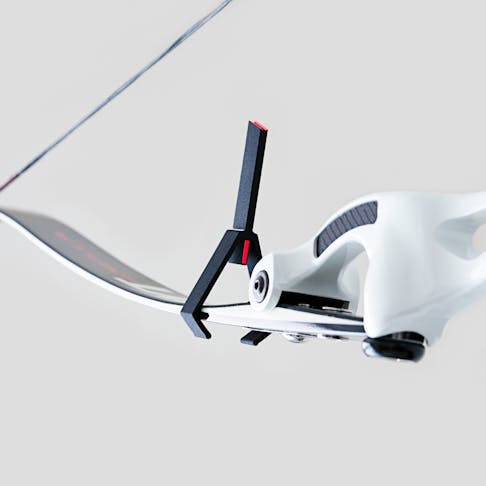
Case Study: An Archer Aims, Shoots, and Lands His Shot with Xometry Injection Molding
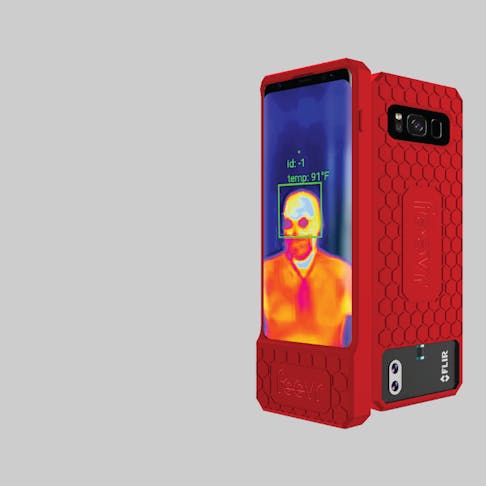
Case Study: Combating COVID-19 with a Contactless, AI-Based Thermal Imaging Device