Tube Bending Services
Xometry offers precision tube bending services for round metal tube stock to meet your needs.
Overview of Tube Bending
Tube bending consists of a series of manufacturing processes that alter the shape of a pipe or tube to create the desired geometry or features that meet specific requirements. In the process, tube stock is loaded into a bending machine which uses mechanical forces to push the tube against dies and rollers that cause the tube to conform to a shape. Tubes can be bent two-dimensionally where the openings remain on the same plane or in three dimensions where they sit on different planes. Multiple bends are allowed in CNC tube bending, reducing the need to weld or fabricate a complex shape with elbow and straight tube sections.
Xometry offers a full suite of custom tube bending services for your application with instant online quoting, DFM, and competitive lead times. Whether you are looking for standard rotary draw tube bending or highly precise mandrel tube bending, Xometry offers different processes to meet your requirements for tube fabrication services in both low and high volumes. Xometry also offers laser tube cutting services for parts that include cut features such as holes, slots, and more. Material choices for our tube bending services include stainless steel, aluminum, and alloy steel.
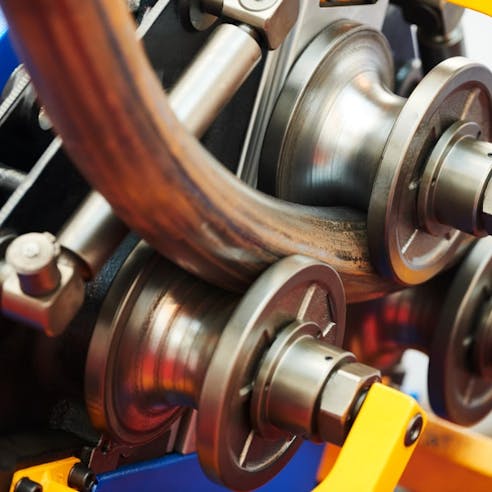
Tube Bending Sizes and Tolerances
Our tube bending service is built around typical industry standards to ensure a smooth manufacturing experience. Xometry can achieve tighter tolerances after a manual review by one of our project engineers. In the list below, you'll find the standards and tolerances specific to our drawn or mandrel bending techniques for round profiles:
- Minimum bendable tube diameter: .250"
- Maximum bendable tube diameter: 2.000"
- Minimum bendable tube wall thickness: .035"
- Maximum bendable tube wall thickness: .188"
- Overall tube sheath envelope tolerance is +/- 0.125” typical
- Linear dimensions (excluding locations to bends) are +/- 0.010"
- Simple, single planar bends are +/- 0.010”
- Multiple surface or multi-planar bends are +/- 0.030”
- Angularity: +/- 2 degrees
- Tube center line radius tolerance is +/- 0.125” typical
- Tube end diameter tolerancing is +/- 0.020”
- Cut edges will be normal-to-surface as a default. Normal-to-edge cuts will require agreement at the time of order.
View more standards on our manufacturing standards page.
Tube Bending Material Options
Xometry's tube bending services are for creating custom round tubes in a variety of shapes and materials:
- Stainless Steel 304 and 316 (Welded or Seamless) are resistant to rust and corrosion, making them ideal for outdoor, wet, or salty environments. 316 has slightly better corrosion resistance than 304.
- Aluminum 6061 (Extruded or Drawn) is a stiff, lightweight tube that won't rust. It it heavily used in lightweight frames and aircraft parts.
- Alloy Steel 4130 (Seamless) is an extremely strong and tough tube used in race cars and aerospace structures. Seamless reduces failure points in this material making ideal for critical applications.
- Steel A513 (Type 1 HREW, Type 2 CREW, or Type 5 DOM) is a go-to for general use. DOM is smooth and strong for car parts; HREW is less expensive and good for simple structures; CREW is cold-formed for better strength and finish.
The table below depicts the range of tube sizes available for these services. Learn more on our standard tube sizes resource page.
Material | Minimum O.D. | Maximum O.D. | Minimum wall thickness | Maximum wall thickness |
---|---|---|---|---|
Material Stainless Steel 304 | Minimum O.D. .250" | Maximum O.D. 2.000" | Minimum wall thickness .035" | Maximum wall thickness .188" |
Material Stainless Steel 316 | Minimum O.D. .250" | Maximum O.D. 2.000" | Minimum wall thickness .035" | Maximum wall thickness .120" |
Material Aluminum 6061 | Minimum O.D. .250" | Maximum O.D. 2.000" | Minimum wall thickness .035" | Maximum wall thickness .188" |
Material Steel 4130 (Chromoly) | Minimum O.D. .375" | Maximum O.D. 2.000" | Minimum wall thickness .035" | Maximum wall thickness .188" |
Material Steel A513 Type 5, DOM | Minimum O.D. .250" | Maximum O.D. 2.000" | Minimum wall thickness .035" | Maximum wall thickness .188" |
Material Steel A513 Type 1, HREW | Minimum O.D. 1.000" | Maximum O.D. 2.000" | Minimum wall thickness .065" | Maximum wall thickness .120" |
Material Steel A513 Type 2, CREW | Minimum O.D. .500" | Maximum O.D. 2.000" | Minimum wall thickness .035" | Maximum wall thickness .065" |
See additional details on our standard tube sizes page.
Tube Glossary
- Welded: Welded tube is made by rolling a flat piece of metal into a tube shape and then welding the edges together.
- Seamless: Seamless tube is made without any welding. It's formed by heating and stretching a solid piece of metal until it becomes a tube.
- Extruded: Extruded tube is made by pushing heated metal through a shaped opening. This process can create complex shapes and is commonly used for aluminum.
- Drawn: Drawn tube is made by pulling a tube through a smaller die, making it more precise and stronger. Extruded and welded tube stock can be drawn.
- DOM: Drawn Over Mandrel is like drawn where welded tube is drawn over a mandrel after welding to improve strength and finish.
- HREW: Hot Rolled Electric-Welded tube is made from hot-rolled steel. This is a less expensive tube used for general purposes.
- CREW: Cold Rolled Electric-Welded is similar to HREW but made from cold-rolled steel giving it a slightly better surface compared to HREW.
Ready to start your tube bending quote?
Design Tips for Tube Bending
When it comes to tube bending, there are a few things you can do when designing your parts to ensure a smoother quoting and manufacturing experience. We've compiled a few tube bending design for manufacturing (DFM) tips below. For additional tips, check out our top tube bending design tips article.
- For multi-bend parts, maintain a consistent center line radius (CLR)
- We recommend a bend radius to tube diameter ratio of 2:1 to 5:1, no greater than 6", using the center line radius (CLR)
- Bend distances should be at least 2X the outer diameter for tubes less than 1", 3X for 1"-2", and 4X for tubing with outer diameters greater than 2"
- Assume normal-to-surface cutting for cut features and end conditions.
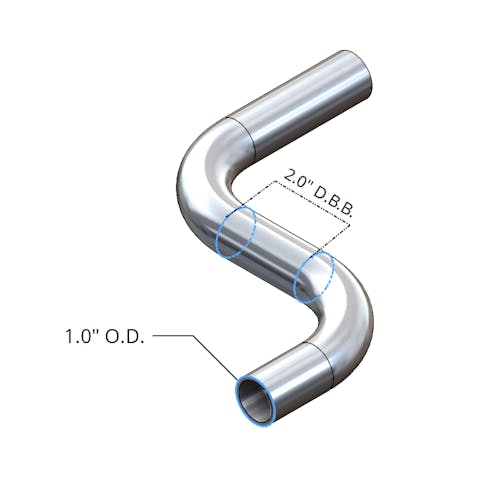
Recommended Center Line Radius to Outer Diameter
Beyond the bend distance guidelines, Xometry has found the following tube diameter (OD) to center line radius (CLR) combinations more readily available across a broad network.
Note: CLRs under 2X the OD are at a higher risk of manufacturing issues, especially when paired with thinner wall thicknesses. We recommend holding CLRs above 2X the tube OD for projects.
The list below shows a tube OD in decimals or fractions as the related CLR to help you design your project. It is recommended that single tubes contain only one CLR for ease of manufacturability.
OD to CLR Recommended Combinations:
- .188" (3/16") OD: CLR of .25", .5", .75", 1", 3.5", or 4"
- .25" (1/4") OD: CLR of .25", .5", .75", 1", or 1.25"
- .375" (3/8") OD: CLR of .75", 1", 1.25", 1.5", 2", or 3"
- .5" (1/2") OD: CLR of .75", 1", 1.25", 1.5", 1.75", 2", 2.5", 3", or 3.5"
- .625" (5/8") OD: CLR of 1", 1.25", 1.5", 1.75", 2", 2.5", 3.5", or 4"
- .75" (3/4") OD: CLR of .75", 1", 1.25", 1.5", 1.75", 2", 3", 3.5", or 4"
- .875" (7/8") OD: CLR of 1.5", 2", or 2.5"
- 1" OD: CLR of 1", 1.5", 2", 2.5", 3", 3.5", or 4"
- 1.25" (1 1/4") OD: CLR of 1.25", 1.5", 2", 2.5", 3", 3.5", or 4"
- 1.5" (1 1/2") OD: CLR of 1.5", 1.75", 2", 2.5", or 3"
- 1.75" (1 3/4") OD: CLR of 2.5", 3", 3.5", or 4"
- 2" OD: CLR of 2", 2.5", 3", or 4"
(Above: Center Line Radius, CLR)
Capabilities
Xometry offers a full range of tube bending capabilities and pipe bending services. These services include:
- Mandrel Tube Bending
- Rotary Draw Tube Bending
- Roll Tube Bending
- Compression Bending
Mandrel Tube Bending – This method (also known as mandrel bending) is similar to rotary draw bending; however, it fully retains the internal tube profile throughout the bend. This process is accomplished using internal support known as a mandrel that preserves the structure of the tube during bending, ensuring that little to no unwanted deformation occurs. The mandrel tube bender has a long bed with a mandrel rod, which holds the mandrel right at the tangent point of the bend. The tube slides over the mandrel, the machine clamps down on it, and the tube is bent while the mandrel remains stationary. Mandrel tube bending is especially useful for thin wall thicknesses, large diameters, and tight radii, where collapsing during bending is common.
Rotary Draw Tube Bending – by far the most popular method, rotary draw benders use a clamping die, radius (or bend) die, and pressure die to hold the tube to form during the entire bending process. The tube is clamped to the bend die and is “drawn” around the other dies via hydraulic or electrical power, resulting in a highly accurate and repeatable bend. Rotary draw tube bending processes can be manual, semi-manual, or CNC-operated. Computer-guided rotary draw bending allows unmatched precision (especially for high-volume applications). However, setup time can be longer, and each unique bend requires tooling to be created.
Roll Tube Bending – In roll tube bending (also known as roll bending), three dies (or rollers) are used to lock down the tube, where a piston presses down on the tube, and the operator “rolls” the pipe through the machine, causing a gradual bend (also known as an arc). The tube is reset into the dies, the piston is lowered further, and the process is repeated until the desired profile is achieved. This method is often a manually-powered process; however, it can also be motorized for additional power input. Roll tube bending offers variable bends and angles without additional tooling and is ideal for large, gradual bends, but its accuracy and repeatability are limited.
Compression Bending – With compression bending, the tube or pipe is clamped in place, and force is directly applied, which creates the bend. This process is primarily utilized for single bend applications. No internal support is used with compression bending, which typically produces an oval cross-section and may result in crushing of the bend. Bends generally are limited to angles of 120 degrees or less.
Industries Served
Tube bending can be utilized across a diverse set of industries. From architectural and lighting fixtures in buildings to vehicle exhaust systems. Below is a list of just some of the notable sectors our tube fabrication and bending services are an ideal fit for:
- Aerospace & Defense
- Automotive
- Architectural & Lighting
- Consumer Goods
- Oil & Gas
- Marine & Shipbuilding
- Construction
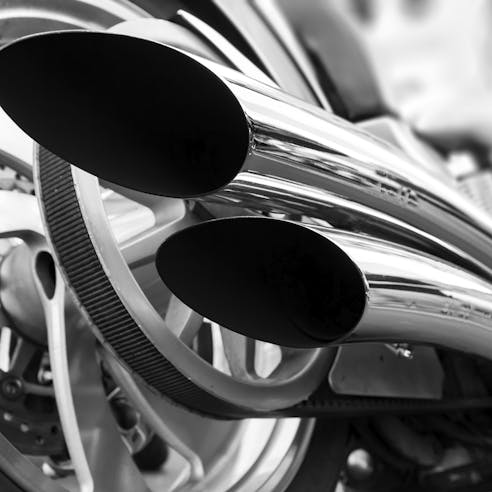
Why Choose Xometry for Tube Bending?
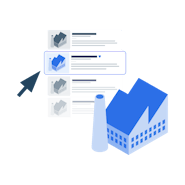
Easy to Use
Access hundreds of service suppliers through our easy-to-use platform.
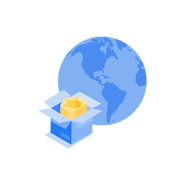
Vetted Network
We are ISO 9001:2015, ISO 13485, and AS9100D certified. Only the top shops that apply to become network suppliers make it through our qualification process.
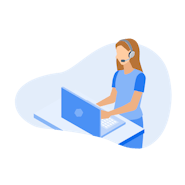
Expert help
Our team of Application Engineers and Process Specialists are available to support you and provide answers to all of your fabrication and manufacturability questions.
Related Services
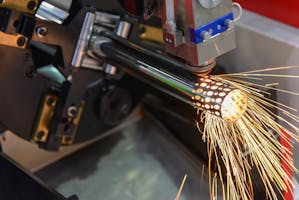
Laser Tube Cutting Services
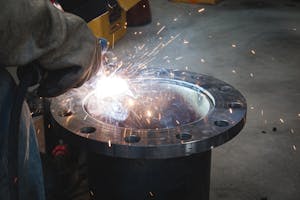
Custom Online Weldment Services by Xometry
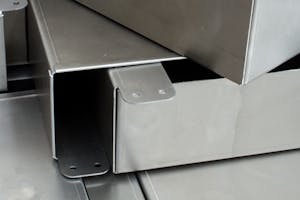
Sheet Metal Fabrication Services
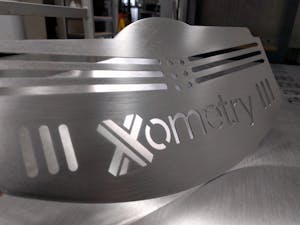