Carbon Digital Light Synthesis™ (DLS™) 3D Printing Service
High-Performing Prototypes and Serialized Production Parts
Free Shipping on All US Orders
Overview: What is Carbon DLS™ Technology?
Carbon DLS™ Technology Basics
Carbon uses digital light projection, oxygen-permeable optics, and programmable liquid resins to produce products with end-use durability, resolution, and surface finish. This 3D printing technology is called Digital Light Synthesis™, or DLS for short. Another legacy term for the process is Continuous Liquid Interface Production (CLIP). Along with Carbon’s custom liquid resins, DLS unlocks new business opportunities and product designs previously impossible, including mass customization and on-demand inventory of end-use products.
Carbon bridges, and sometimes substitutes, for processes like Urethane Casting and Injection Molding service production, because the materials are urethane-based or epoxy-based, giving excellent mechanical properties. There are even elastomer and silicone resins that outperform most additive manufactured rubber-like materials.
DLS™ Materials
Material Name | Description | Shore Hardness | Elongation at Break (%) | Impact Strength (J/m) | Data Sheets |
---|---|---|---|---|---|
Material Name RPU 70 | Description Rigid polyurethane | Shore Hardness 80D | Elongation at Break (%) 100% | Impact Strength (J/m) 22 J/m | Data Sheets |
Material Name UMA 90 | Description Urethane methacrylate | Shore Hardness 86D | Elongation at Break (%) 17% | Impact Strength (J/m) 33 J/m | Data Sheets |
Material Name EPX 82 | Description Impact-resistant epoxy | Shore Hardness 89D | Elongation at Break (%) 5.9% | Impact Strength (J/m) 44 J/m | Data Sheets |
Material Name FPU 50 | Description Flexible polyurethane | Shore Hardness 71D | Elongation at Break (%) 280% | Impact Strength (J/m) 40 J/m | Data Sheets |
Material Name EPU 40 | Description Elastomeric polyurethane | Shore Hardness 68A | Elongation at Break (%) 310% | Impact Strength (J/m) N/A | Data Sheets |
Material Name SIL 30 | Description Elastomeric silicone-urethane | Shore Hardness 35A | Elongation at Break (%) 330% | Impact Strength (J/m) N/A | Data Sheets |
More carbon 3D materials are available upon request by selecting Material: Other and writing in the specific resin on your online quote.
Available Finishes for Carbon DLS™ Parts
Standard
Parts built with Carbon DLS technology will typically have a matte to semi-gloss surface finish depending on feature direction. Extended protrusions will show vertical lines in the part that are parallel to the direction of growth. Supports are removed and mitigated as required.
Custom Color (UMA 90)
UMA 90 materials come in different colors available for custom mixing. Although the standard is black or white, other solid colors can be available for part productions.
Custom
Don’t see the finish you need? Submit an RFQ and we’ll look into a finishing process for you.
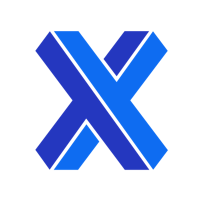
Ready to get started on your 3D printing quote?
Free shipping available for domestic 3D printing orders ; learn more!
Applications for Carbon DLS™ Technology
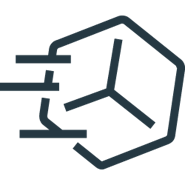
Rapid Prototyping
Carbon DLS™ technology can be used to create strong, flexible, and colorful prototypes
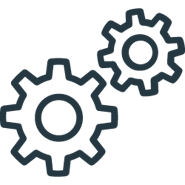
End-Use Functional Parts
Carbon DLS™ materials are fully dense and engineered for end-use
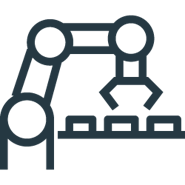
Direct Digital Manufacturing
Carbon DLS™ printing is ideal for serialize production of small to medium-sized parts
Benefits of Carbon DLS™ 3D Printed Parts
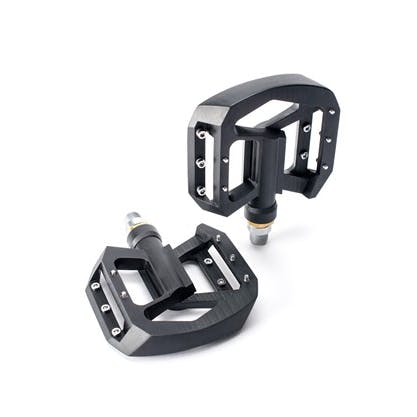
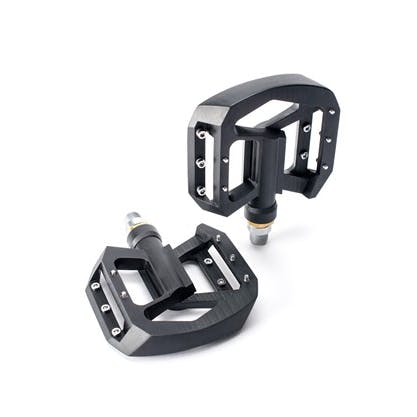
3D print directly in urethanes, epoxies, elastomers, and other specialty thermosets.
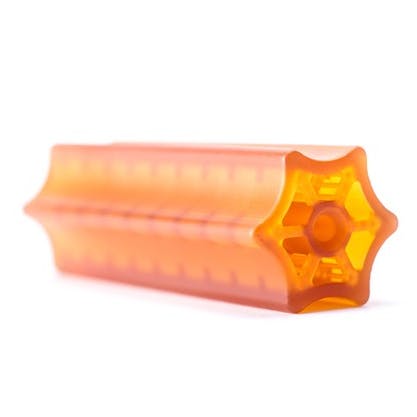
Best-in-class at 3D printing of lattice structures and organic shapes.
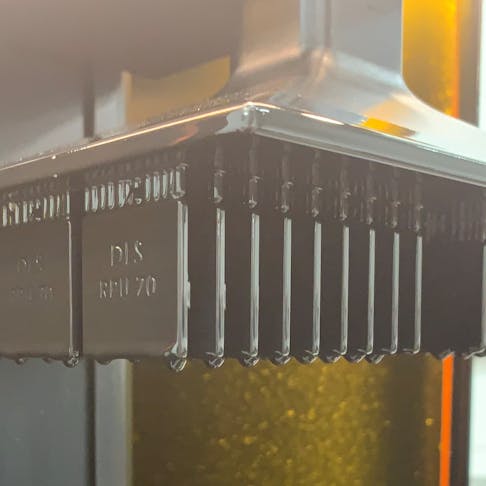
Produce small parts in serialized production at pricing competitive with injection molding.
Carbon DLS™ General Tolerances
Description | Tolerance Notes |
---|---|
Description General Tolerances | Tolerance Notes +/- 0.003” for the first inch is typical, plus +/- 0.010” for every inch thereafter**. |
Description Build Size | Tolerance Notes The typical build area is 7.4” x 4.6” x 12.8”. Parts with dimensions exceeding 4” x 4” x 6” will require manual review. |
Description Ideal Part Size | Tolerance Notes Part's below 2" x 1" x 3" or smaller tend to have the best production economy of scale. |
Description Minimum Wall Thickness | Tolerance Notes 0.030" or larger is suggested for any walls, text, or lattice features. |
Description DLP Pixel Resolution | Tolerance Notes Approx. 0.005" square |
This table depicts the general tolerances for Digital Light Synthesis™. Stresses during the build, support strategy, and other geometry considerations may cause deviation in tolerances and flatness. Improved tolerances may be possible with a manual quote review, after successful completion of a prototype build, and must be approved on a case-by-case basis. General tolerances apply before secondary finishing or post-processing unless otherwise specified. Please check out Xometry's Manufacturing Standards for more information on tolerances per process.
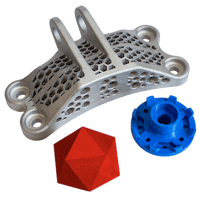
Need to Compare Printing Processes?
Our quick reference guides let you quickly compare different 3D printing processes!
What Differentiates Carbon
What differentiates Xometry's Carbon DLS 3D printing service from similar processes like Stereolithography (SLA) or PolyJet 3D prints is that the resin has a secondary thermal step which activates dormant epoxies or urethanes, making parts much stronger than UV-curing alone. Additionally, the digital light synthesis process is continuous, without stopping layer-by-layer as with most additive manufacturing. This gives the parts isotropic properties, meaning that strength is even regardless of orientation. This is a significant advantage over processes like Fused Deposition Modeling (FDM), where Z-direction features can be much weaker than similar features built in the XY-direction.
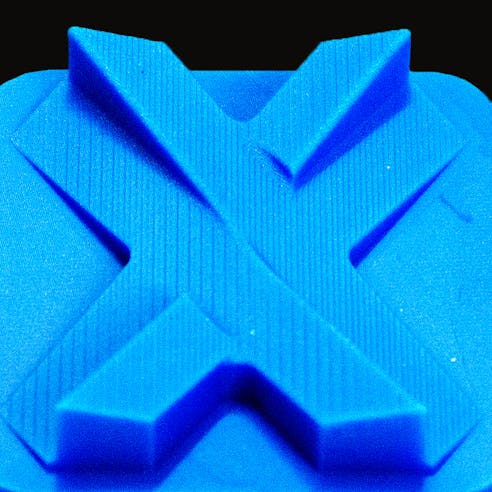
Why Choose Xometry for 3D Printing?
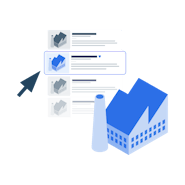
Endless Options
Choose from millions of possible combinations of materials, finishes, tolerances, markings, and certifications for your order.
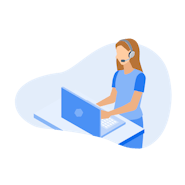
Easy to Use
Get your parts delivered right to your door without the hassle of sourcing, project management, logistics, or shipping.
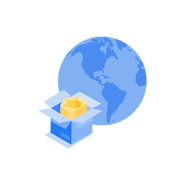
Vetted Network
We are ISO 9001:2015, ISO 13485, and AS9100D certified. Only the top shops that apply to become Suppliers make it through our qualification process.