Custom Online Weldment Services by Xometry
High quality custom weldment services available with a variety of materials, manufacturing processes, finishes, and more. Subject to availability. Xometry doesn't guarantee that we can provide this service at any given time.
Xometry offers high-quality custom weldment services, enabling you to complete complex assemblies with confidence. Our network of certified welding partners provides expert solutions with flexible options for materials, processes, and finishes. Here’s how to get started:
Here Is The Best Way To Request Weldment Services Using Xometry
Please follow these steps to the best of your ability to make assembling your project as fast and accurate as possible. A representative will reach out to ensure we have all the details and requirements for making your project successful.
Need help? Contact us at support@xometry.com.
- Upload Your 3D CAD Files: Include all parts, assemblies, and relevant technical documents in our Quoting Engine. Ensure both a final assembly file and necessary technical drawings are attached, as well as any inspection templates (if applicable). In the notes field of your assembly file, please put “Assembly,” and in parts files please label “Welding” on the parts to be joined.
- Specify Requirements: Add notes on weld types, locations, materials, finishes, tolerances, and any application-specific needs.
- Select Certifications: Choose applicable standards like ITAR, ISO, or AWS for your project. (Note: AWS certifications will require a procedure qualification record PQR to be filled out and stored on file, so it may require extra processing time).
- Request a Manual Quote if Needed: For complex assemblies, a manual quote may better capture project-specific requirements.
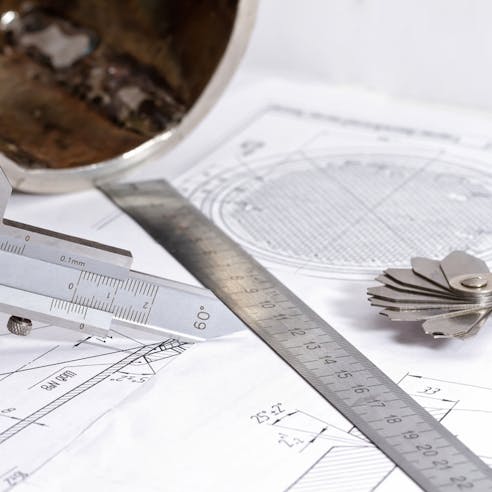
By following these steps, you help our team deliver a smooth, precise, and efficient quoting process.
- TIG Welding (Tungsten Inert Gas or Gas Tungsten Arc Welding): Provides clean, aesthetic welds; commonly used in high-precision projects like custom fabrication or customer facing parts which require a great cosmetic finish.
- MIG Welding (Gas Metal Arc Welding): Known for speed and efficiency; ideal for automotive and general fabrication applications.
- FCAW (Flux Cored Arc Welding): Delivers deep weld penetration and high deposition rates, suited for heavy equipment and structural applications.
- Stick Welding (SMAW): Versatile and commonly used for structural projects, pressure vessels, and repairs.
- Submerged Arc Welding (SAW): Ideal for long seams, creating strong and clean welds with minimal distortion.
- Spot Welding (Resistance Spot Welding): Provides quick, reliable joints, perfect for sheet metal applications in automotive and appliance industries.
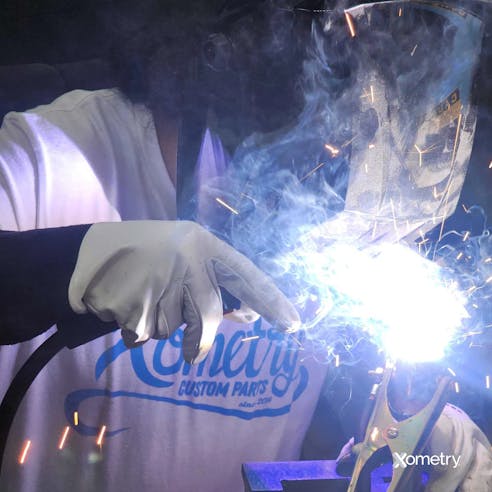
If you don’t see the welding type you need listed here, reach out to our team. We leverage a vast network of skilled welders to match your exact project needs.
Require Weldment Services?
Weldment Design Tips
Ensuring weld quality begins at the design stage. Here are key tips to help optimize your design for strength, efficiency, and cost-effectiveness:
Choose Appropriate Weld Seams:
- Butt Weld (a): Ideal for load-bearing joints.
- Fillet Weld (b): Great for T-joints and lap joints, offering strong connections.
- Lap Weld (c): Used for overlapping sheets, ideal for thin materials.
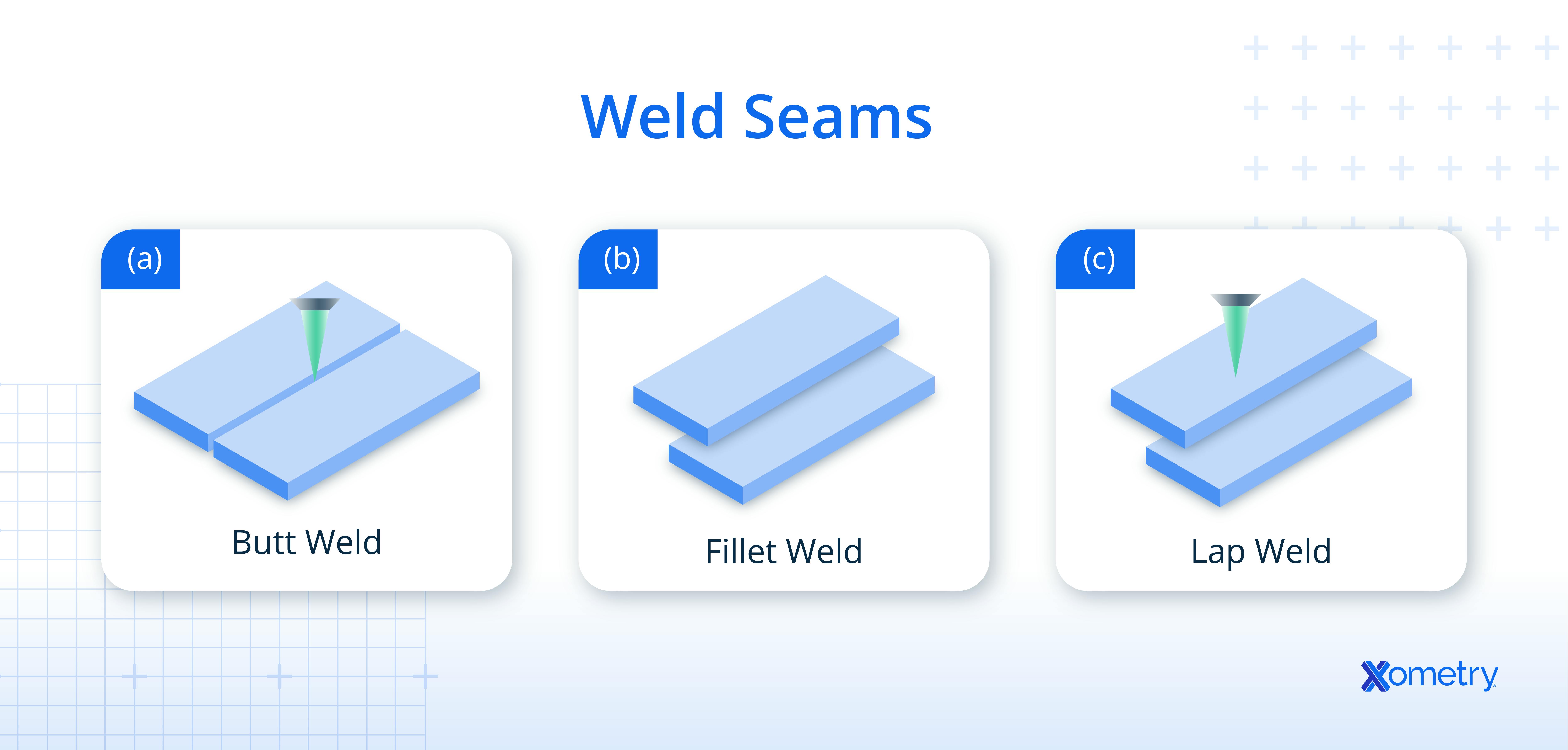
Use Standard Weld Symbols: Proper use of weld callouts and symbols in your CAD files ensures clear communication between design and fabrication teams, minimizing misinterpretations.
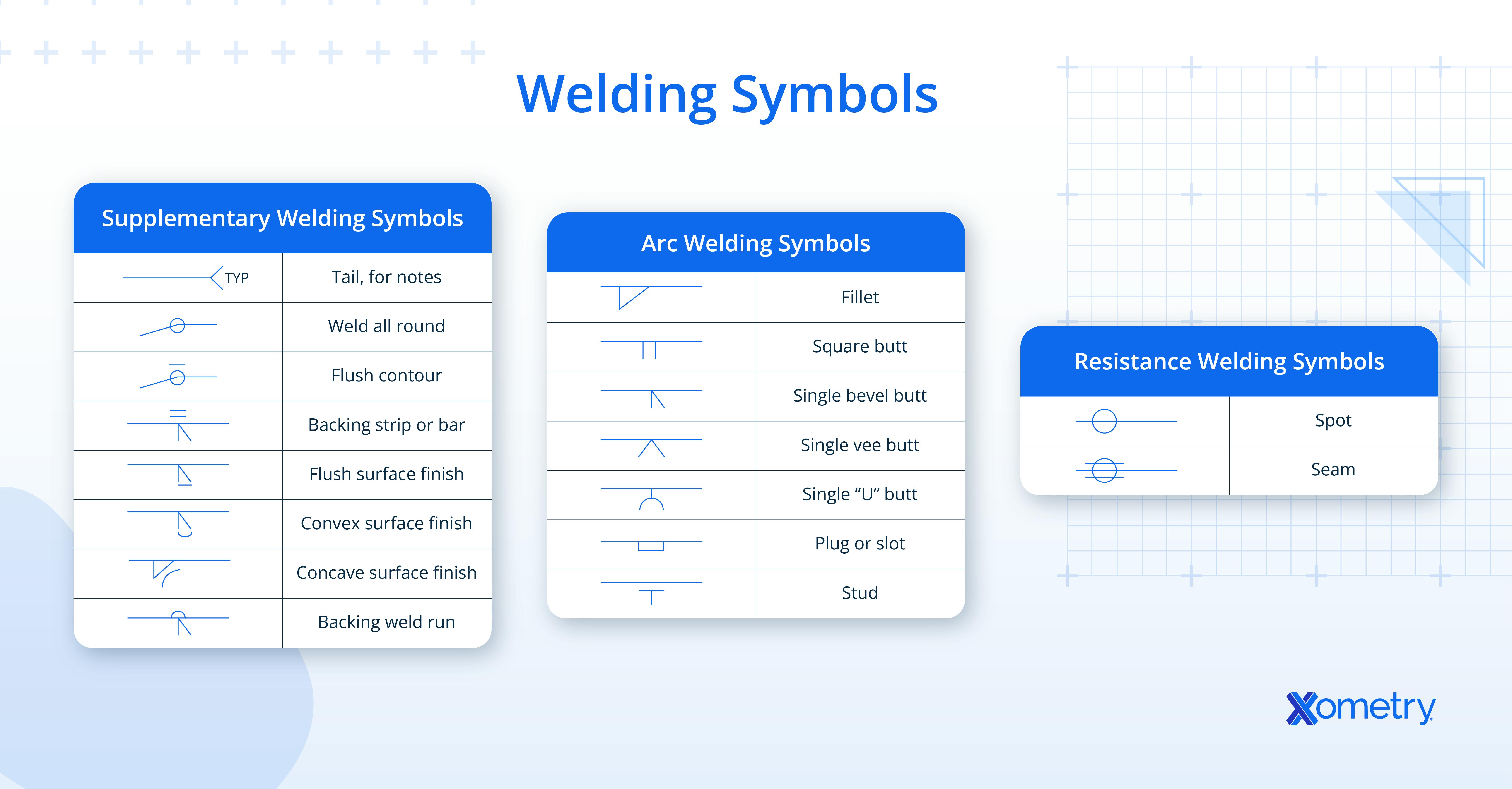
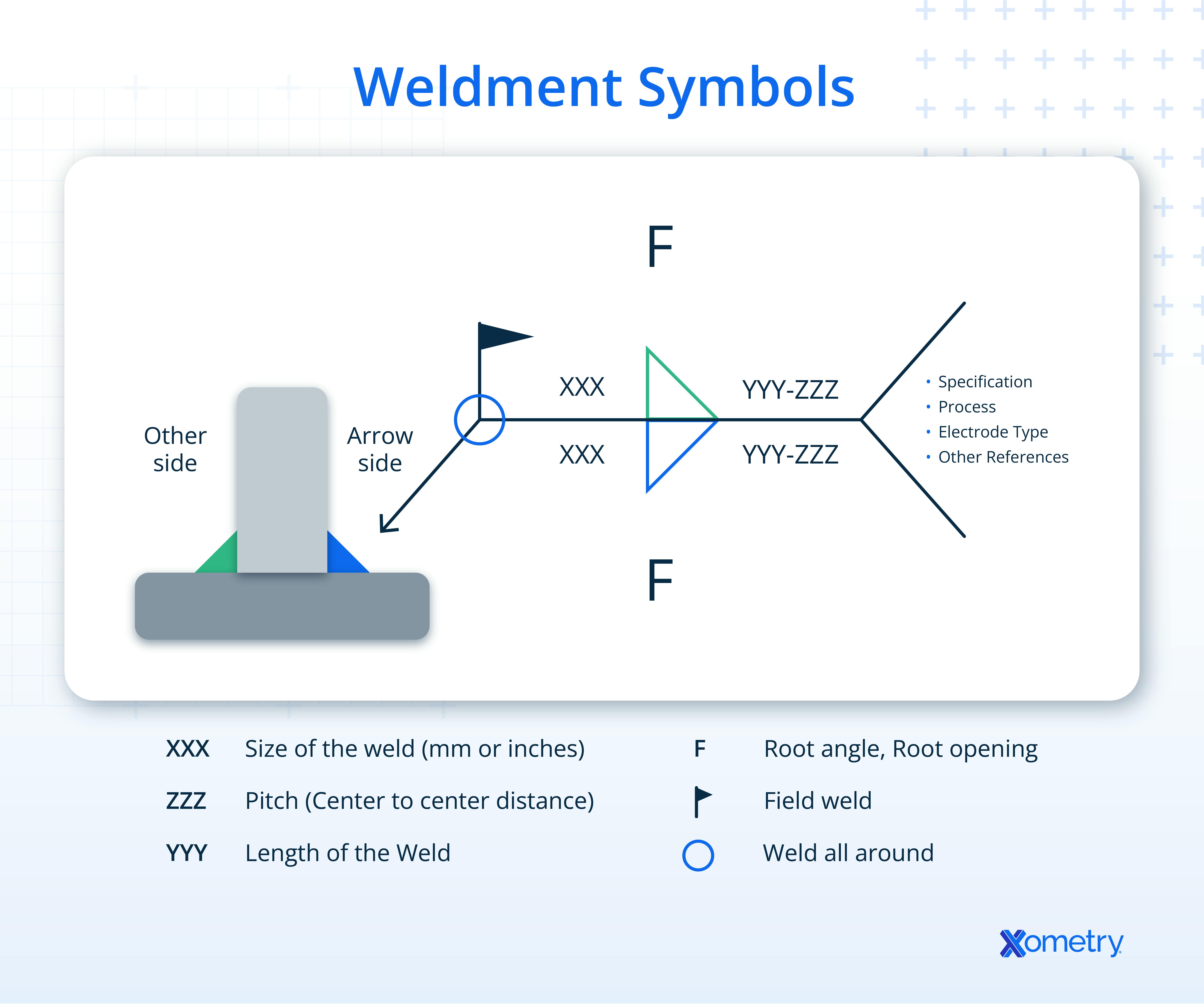
Mitigate Distortion in Long Seam Welds: Techniques like intermittent (stitch) welding help control heat and minimize distortion, especially on long or thin-walled components. Proper joint preparation, alignment, and fit-up also help achieve stronger welds.
Avoid Welding Dissimilar Metals: Joining different metals can weaken the joint and cause issues in the weld process. Stick to compatible materials like aluminum to aluminum or steel to steel for the best results.
Account for Heat-Affected Zones: Warping can occur around the weld area, especially in large or complex projects. Plan for sufficient spacing and consider adding fixtures to maintain stability during welding.
Optimal Gap Sizing: Ensure the weld gap is appropriate for the material thickness and type of weld. Too small a gap can lead to lack of fusion, while too large a gap increases the risk of burn-through and distortion. For groove welds, follow the AWS guidelines, as they provide recommendations for root openings based on joint configurations.
Advantages and Benefits of Xometry's Weldment Service
Choosing Xometry for your welding needs provides a seamless, reliable, and cost-effective solution. Key advantages include:
- Turnkey Welding Solutions: From material sourcing to final inspection, Xometry handles every step, reducing your need for multiple suppliers.
- Scalable Production Capacity: Leverage our network of certified partners to meet project demands of any size or complexity.
- Expert Engineering Support: Our team collaborates with you to ensure that every detail aligns with your specifications.
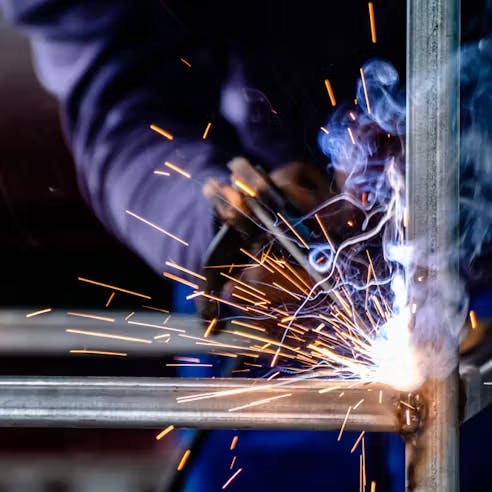
Additional benefits:
- Wide Range of Welding Capabilities: Access TIG, MIG, FCAW, Stick, and Spot welding, along with specialty processes as needed.
- Certified Quality Standards: All welds adhere to industry standards, including AWS, ASME, and ISO, ensuring high quality results and consistency.
Weldment Inspection and QA
Xometry’s welding services include rigorous quality assurance, meeting a range of inspection levels to suit your project’s requirements:
- Standard Inspection: Visual checks to identify surface defects.
- Dimensional Verification: Ensures that welded parts meet specified tolerances.
- Advanced Testing Options: Includes dye penetrant (shown below), ultrasonic testing, and radiography, ideal for high-integrity applications.
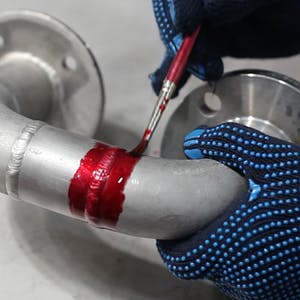
Our team ensures 100% quality control, supported by detailed inspection records and certifications to meet your project’s needs.
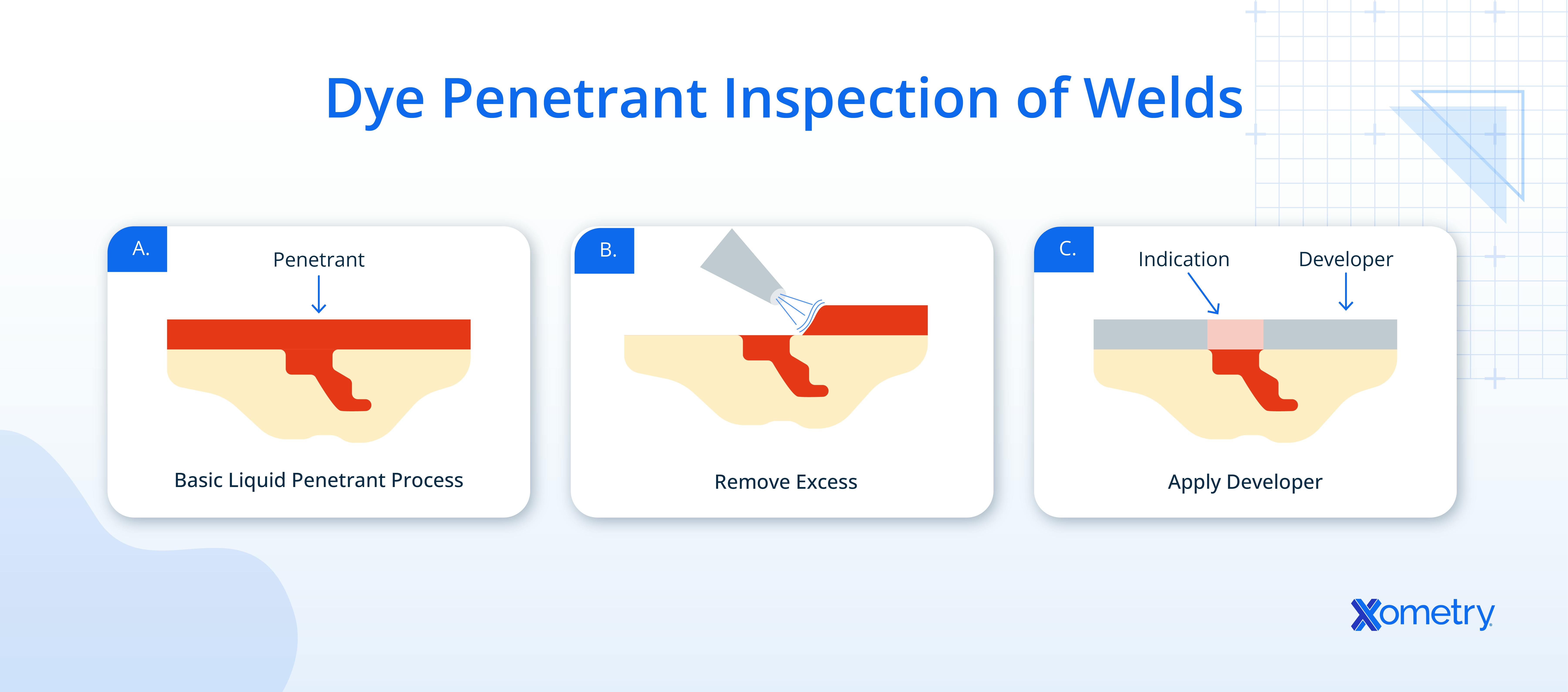
Certifications Offered:
- AWS (American Welding Society): Essential for ensuring adherence to welding standards, such as AWS D1.1 for structural welding.
- AS9100: Critical for quality management in aerospace welding applications.
- NADCAP: Necessary for compliance with special process requirements in aerospace and defense, including welding.
- ISO 9001: Fundamental for maintaining a consistent quality management system applicable to welding.
- ITAR Registered: Important if your welding work involves defense-related manufacturing and export controls.
Each certification reflects our commitment to quality and precision, giving you confidence in every weld.
Weldment Applications
Xometry’s welding services cater to a diverse range of industries, including:
- Automotive & Aerospace: Structural frames and high-strength assemblies.
- Energy & Power: Components for utilities, renewable energy infrastructure, and oil & gas.
- Shipbuilding & Construction: Large structural weldments and critical welds for building projects.
- Medical Devices: Welding for medical-grade assemblies, including cleanroom-certified projects.
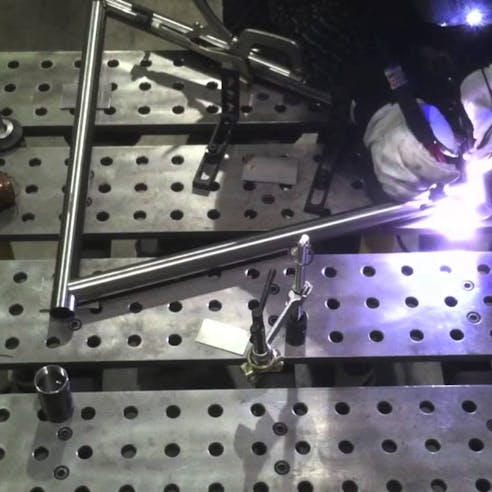
These examples show the versatility of Xometry’s welding services, from custom applications to high-production environments. Whether it’s a single prototype or large-scale production, we have the capabilities to deliver.
Why Choose Xometry for Weldment Services?
Xometry provides a full range of end-to-end services to ensure your welding project is completed accurately, on time, and to the highest quality standards.
Access to Certified Welding Professionals: Our network includes skilled welders trained to handle any welding process or material.
Xometry combines technology with a deep commitment to quality, ensuring every weld is crafted to meet the demands of your project.
Endless Options
Choose from millions of possible combinations of materials, finishes, tolerances, markings, and certifications for your order.
Easy to Use
Get started with our easy-to-use platform and let our experts take care of managing the project from locating the right manufacturing partner to delivery logistics.
Vetted Network
We are ISO 9001:2015, ISO 13485, IATF 16949:2016 and AS9100D certified. Only the top shops that apply to become suppliers make it through our qualification process.