Gas Assist Injection Molding
Get custom gas assist plastic molded prototypes and production parts in as few as 10 business days. We provide expert engineering reviews and $500 off your first mold. Dozens of materials and finishes are available. Subject to availability. Xometry doesn't guarantee that we can provide this service at any given time.
Gas assist injection molding is a low-pressure injection molding technique. It fills an injection mold under pressure, first with plastic and then a gas (typically nitrogen). Gas injection molding enhances the adaptability of traditional plastic processing while benefiting from its proven repeatability in high-quality component production by offering design and manufacturing choices for a wide range of applications. Some of the main benefits of this process are the improved quality and reduced weight of the product, as well as shorter cycle times and lower overall production costs.
It's important to note that gas assist injection molding and blow molding services are not the same thing. Gas assist molded parts have thick walls and relatively small hollow cores, which reduce the weight of the part around 10%. Blow molded parts, on the other hand, feature thin walls and large hollow cores that reduce weight by 80%. Overall, a gas assist molded part will be sturdier than a blow molded part, but more lightweight than a traditional injection molded part.
Here we'll cover all the basics around gas assist molding, including the process' steps, properties, and advantages. You can also check out our page on general injection molding services for more specific information around the types of materials and production options available for this and other injection molding services.
The Gas Assist Injection Molding Process
There exist multiple distinct types of injection molding, one of which is gas-assisted injection molding. The introduction of pressurized nitrogen gas aids the injection of molten plastic into the mold. The gas creates a bubble, which forces the plastic towards the mold's edges, making hollow parts as the bubble expands.
The steps of this process are relatively similar to conventional injection molding, though it features a few additional gas injection stages:
- Mold Clamping – this is the initial step in the process and it is very important since it prevents the injected material from spilling out. The injection machine places the two halves of the mold into the clamping unit which is responsible for putting and keeping the mold together against the pressure of the resin.
- Resin Injection - the plastic, usually in the form of pellets, is then poured into a container where it is melted down to a liquid state. This liquid is then pumped into the mold, keeping the temperature constant.
- Primary Gas Penetration - a bubble is formed when gas is injected into the molten core. This bubble forces the molten plastic into the empty cavity, thoroughly filling the mold.
- Secondary gas penetration - when the polymer reaches the end of the mold at the completion of the filling step, secondary gas penetration occurs. As the component cools and the material shrinks, the gas bubble expands and takes up the excess cavity volume. This pressure in the bubble also aids the packing stage of the process.
- Gas Release - the pressure is discharged after the gassing phase, either by releasing the gas into the atmosphere or by gas recycling.
- Part Ejection - when ambient pressure is attained and the plastic has cooled sufficiently, the mold is opened and the component ejected.
Gas Injection Location
The location along the melt stream where the gas is supplied varies amongst gas assist systems. Let's take a look at the different places where gas might be injected:
- Machine Nozzle - "through-nozzle" gas assist molding is when gas is injected through a specific shut-off nozzle mounted to the press's barrel. Because the gas comes from a single place, all gas lines must be linked to the sprue or gate. The sprue is the vertical channel through which the material enters the mold; it is used to regulate the flow of molten plastic into the mold.
- Resin Delivery System - "in-runner" gas assist molding occurs when gas is supplied into the runner system or the sprue bushing through gas pins. The gas channels must all come from the sprue if the component is direct-sprue gated.
- Mold Cavity Gas Injection System - "in-article" gas aid molding occurs when gas is supplied directly into the mold cavity using gas pins. Independent gas channels may be designed into parts molded utilizing this technology, where each channel can have its own control over gas pressure and timing.
Properties of Gas Assist Injection Molding
Gas assist molding can be further split into two separate sub-types: external and internal gas assist molding. The main difference is the location where the pressurized nitrogen gas is injected.
In internal gas assist plastic molding, the gas is injected directly into the component's cavity. The nitrogen gas is directed through strategically designed gas channels to displace the material in the thick parts of the component, resulting in hollow sections. Due to the nitrogen gas pressure, the molten resin is pushed against the cavity walls until it hardens. The continuous, properly distributed gas pressure prevents the component from shrinking while eliminating surface blemishes, sink marks, and internal stress. Internal molding is perfect for maintaining precise measurements and intricate curvatures across long distances.
In external gas assist plastic molding, the gas is injected in a micro thin layer between the mold core and the back surface of the component. The pressurized gas ensures that the front side of the component exactly matches the mold surface when the resin cools. This process is ideal for items with a high profile and large surface area that require exceptional surface aesthetics.
Advantages of Gas Assist Injection Molding vs. Traditional Plastic Injection Molding
Gas assist technology allows for various parts with complex designs and differing wall thicknesses to be easily molded as a single part. With traditional injection molding, packing pressure is applied by forcing more molten plastic through the feed gates of the material. Because of this, the internal pressure is significantly increased and the packing pressure can only be applied as long as the material gates don't freeze off. Gate freeze-off happens when the gate cools down and prevents the molten plastic from flowing through it into the mold cavity. The time it takes to reach this stage is known as 'freeze time'. As pressure continues to be applied, cooling down is also occurring in the part itself. The areas of the component farthest from the gates will freeze (solidify) first, and pressure will no longer be able to be applied to them. However, as packing pressure is applied, more resin is driven into the region closest to the gates. Because of the pressure difference, the resin densities in the portion are unequal. As the part cools, it shrinks at varying speeds, generating tension and warping. This main problem of traditional injection molding can be solved by introducing gas pressure, which drastically reduces the internal cavity pressure. Some other significant advantages of the gas assist injection molding include:
- Enhanced Surface Definition - gas assist injection molding produces significantly smoother surfaces, making it easier to obtain the required design. With very few alterations or subsequent operations, the plastic product can be ready for market distribution as soon as it has been ejected from the machine.
- Improved Quality – the gas-assisted technique aids the minimization of traditional injection molding defects, such as flow lines, discoloration, distortion, and warping. Thus, this method results in better dimensional control and improved quality of the produced part.
- Cost Reduction - not needing to pack the material, and the resulting hollow core in thicker components can save up to 30% on the material utilized. This directly translates to a reduction in production costs.
- Weight Reduction – the components that have been produced with gas assist injection molding are much lighter in weight when compared to those made with conventional injection molding. The primary reason for this is that the procedure uses less space and material, resulting in a more robust and sturdier product that isn't too heavy. However, parts are still able to have thick walls for increased sturdiness.
- Cycle Time Reduction – since there is no molten core to solidify, the material in the mold cavity hardens faster, so the component may be ejected sooner.
- Certain Structural Advantages - gas assist molded parts feature less hoop stress than standard injection molded parts (they are better able to bend without damage).
Types of Gas Assist Injection Molded Plastic Parts
Gas assist parts include a range of items from armrests and frames to panels and chassis. However, based on the molded items' properties, they can be split into two distinct groups – contained-channel and open-channel. There are also parts that are a mixture of these two types.
Contained Channel Parts
Tubes, armrests, handles, and frames are examples of contained-channel components. These items are made out of a single thick section or channel that the gas must pass through. The components are often easier to process since the gas has a well-defined channel through which it propagates and there are no thin-walled sections that must stay gas-free.
Open Channel Parts
Access covers, panels, shelves, and chassis are a few examples of open-channel items. The main characteristic of all items produced with this technique is that the components have a nominally thin wall with gas channels running through them. Because the gas can migrate into the thin-walled portions of the component (known as fingering), these parts are more challenging to design and produce.
Cost-Saving Design Tips
For gas assist molding specifically, bear in mind the following to ensure you're not paying more than you have to:
- Recycle your resin scrap. A small amount of unused plastic will be expelled from the molds as air is pushed in. Recycling enables you to save on scrap costs and buy less material.
- If you're involved in injection mold prototyping or other small production run cases, your mold will cost less if you have less cavitation. This means using two holes to form parts instead of four.
More tips on savings for injection molding can be found on our general injection molding page.
Why Choose Xometry for Gas Assist Injection Molding?
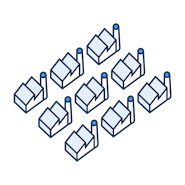
Endless Options
Choose from millions of possible combinations of materials, finishes, tolerances, markings, and certifications for your order.
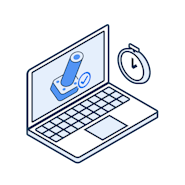
Easy to Use
Get your parts delivered right to your door without the hassle of sourcing, project management, logistics, or shipping.
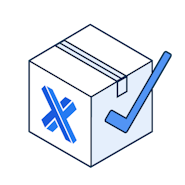
Vetted Network
We are ISO 9001:2015, ISO 13485, and AS9100D certified. Only the top shops that apply to become Suppliers make it through our qualification process.
Disclaimer
The content appearing on this webpage is for informational purposes only. Xometry makes no representation or warranty of any kind, be it expressed or implied, as to the accuracy, completeness, or validity of the information. Any performance parameters, geometric tolerances, specific design features, quality and types of materials, or processes should not be inferred to represent what will be delivered by third-party suppliers or manufacturers through Xometry's network. Buyers seeking quotes for parts are responsible for defining the specific requirements for those parts. Please refer to our terms and conditions for more information.