Production 3D Printing Services
Get instant online quotes on production 3D parts in over 70 metal and plastic materials. Free shipping on all US orders. ISO 9001:2015, ISO 13485 and AS9100D certified.
Production 3D printing, also known as additive manufacturing, is a cutting-edge technology that enables businesses to create complex parts and products in a highly efficient and cost-effective manner. It involves the layer-by-layer fabrication of three-dimensional objects based on digital designs. This approach not only reduces material waste but also allows for the creation of intricate geometries that were once challenging or even impossible to achieve using traditional methods. Production 3D printing also enables on-demand manufacturing, eliminating the need for large-scale, fixed production lines. With this technology, companies can produce parts and products as needed. On-demand manufacturing also opens up new opportunities for customized and personalized products, as each item can be tailored to meet individual customer requirements.
Production 3D Printing Process
Xometry’s production 3D printing process is a comprehensive set of workflow steps that involves several key stages. The process begins with part design, during which digital 3D models of a desired product are created using computer-aided design (CAD) software. Next, the properties of candidate materials that could be used to 3D print the product are carefully evaluated to ensure that they match up with the intended application and its requirements.
Likewise, the chosen material and the design of the part will feed into the decision about which 3D printing technology makes the most sense for the application. The selected method might be fused deposition modeling (FDM), stereolithography (SLA), or selective laser sintering (SLS), to name a few of the more common techniques.
Once the design, the material, and the printing method are chosen, the 3D model is prepared for printing using software that "slices" the 3D model into layers that can be printed, converting the information into instructions that can be understood by the printer. The printer then follows the provided instructions and deposits the chosen material layer by layer, gradually constructing the final part.
Post-processing is often required to refine the printed parts and achieve the desired surface finish and mechanical properties. Throughout the production 3D printing process, quality assurance is paramount. Various inspection methods, such as visual inspection, dimensional measurement, and non-destructive testing, are employed to ensure that the printed parts meet the required specifications and standards.
Materials and Technologies Used for Production 3D Printing
At Xometry, we take pride in offering a wide range of cutting-edge production 3D printing services. We have expertise in such advanced additive manufacturing methods as multi jet fusion, selective laser sintering, and fused deposition modeling. We can handle the 3D printing needs of customers across a broad spectrum of industries, applications, and materials.
Our production 3D printing services boast an extensive selection of materials, catering to various industry needs. For metal parts, we utilize a variety of metal powders, including stainless steel, aluminum, titanium, and cobalt-chrome alloys. For polymers, we provide a comprehensive range of materials, from standard thermoplastics like ABS and PLA to high-performance engineering polymers like nylon and polycarbonate. Additionally, our production 3D printing services offer advanced composites that combine the strength of traditional materials with the lightweight characteristics of reinforced fibers. Carbon fiber-reinforced nylon and fiberglass-reinforced materials are examples of composites available.
Industries Using Production 3D Printing
Our production 3D printing services cater to a wide range of industries, including:
- Automotive
- Aerospace
- Healthcare
- Consumer Goods
- Engineering
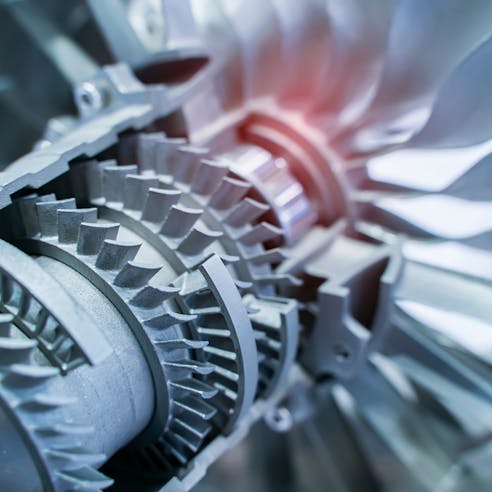
Automotive
In the automotive industry, our production 3D printing services play a critical role in rapid prototyping, mock-ups, functional testing, and manufacturing of complex parts. From lightweight components to customized parts, we enable automotive manufacturers to streamline their product development processes and achieve enhanced performance and efficiency.
Aerospace
Aerospace companies benefit significantly from our production 3D printing services, as they require dimensionally accurate, lightweight parts with superior strength. We assist in producing intricate aerospace components, such as turbine blades, brackets, and interior components, using advanced additive manufacturing technologies to meet the industry's stringent standards.
Healthcare
The healthcare industry benefits from the capabilities of production 3D printing in various applications, including medical device manufacturing, surgical planning models, and patient-specific implants. With our diverse materials and technologies, we contribute to improving patient outcomes and revolutionizing the medical field with custom and functional 3D-printed solutions.
Consumer Goods
Our 3D printing services enable the consumer goods industry to bring innovative and customized products to market quickly and efficiently. From personalized accessories to unique home decor items, we help consumer goods companies embrace on-demand manufacturing and cater to individual customer preferences.
Engineering
Engineering firms rely on our production 3D printing services for rapid prototyping and product development. Our expertise in multi jet fusion, selective laser sintering, and fused deposition modeling allows engineers to iterate designs rapidly, validate concepts, and optimize product performance before committing to traditional manufacturing processes.
Advantages of Production 3D Printing
Production 3D printing offers numerous advantages that set it apart from traditional manufacturing processes, including:
- Reduced Waste
- Design Iterations
- Cost Effective
- Time-Efficient
- On-Demand Production
- Reduced Lead Times
- Customization
- Lightweight Materials
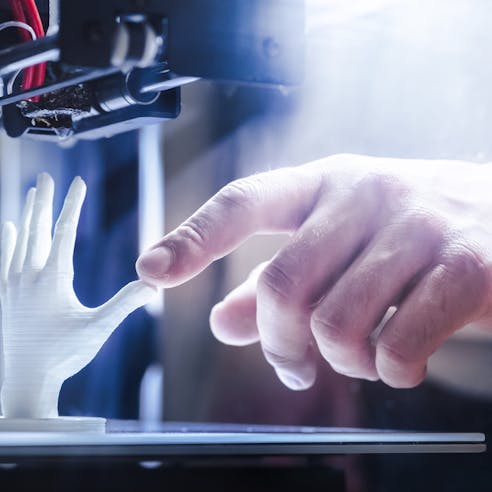
Reduced Waste
Additive manufacturing builds parts layer by layer, using only the necessary amount of material. This not only reduces material costs but also contributes to more sustainable and environmentally friendly production practices.
Design Iterations
Production 3D printing allows for unparalleled design freedom, enabling the creation of intricate geometries and complex structures that would be challenging or impossible to achieve through traditional methods. This design flexibility empowers engineers and designers to iterate quickly on their designs, testing and refining concepts with ease.
Cost Effective
For complex parts with intricate designs, production 3D printing can offer cost savings compared to traditional manufacturing processes. 3D printing eliminates the need for tooling, making it cost-effective for producing small batches or one-off parts without sacrificing quality. This advantage is also associated with the "complexity paradox," a concept wherein the complexity of a part doesn't necessarily increase its cost when using 3D printing. Additionally, 3D printing's "Just in Time" production approach can mitigate storage costs and reduce risks for companies, making it a viable alternative for low-volume manufacturing scenarios.
Time-Efficient
The lead time for producing a 3D-printed part, from concept to finished product, is shorter than for other fabrication processes. This is because design files can be quickly sent to the printer, and parts can be fabricated without the need for lengthy setup times or complex assembly processes. This rapid turnaround time makes 3D printing ideal for time-sensitive projects and on-demand production requirements.
On-Demand Production
Production 3D printing enables on-demand manufacturing, meaning that parts can be printed as needed rather than being produced in large quantities and stored in inventory. This on-demand approach reduces storage costs and the risk of overstocking.
Reduced Lead Times
With streamlined workflows and minimized setup requirements, Xometry’s production 3D printing services can significantly reduce lead times from design concept to final product. Complex parts that once took weeks or months to produce using traditional methods can now be manufactured within days.
Customization
Production 3D printing facilitates product customization on a scale that was previously impractical with traditional manufacturing processes. Businesses can easily tailor products to meet individual customer preferences, even at low volumes.
Lightweight Materials
For industries where lightweight materials are essential, such as aerospace and automotive, production 3D printing offers a distinct advantage. Additive manufacturing allows for the use of advanced lightweight materials and optimized designs. Materials like titanium aluminide (TiAl), known for its high-temperature strength, and carbon fiber reinforced polymers (CFRP), combining strength and low weight, are prime examples. 3D printing enables intricate designs and precise placement of materials, enhancing properties like strength-to-weight ratios. Even commonplace materials like aluminum can be optimized for lightweight structures through additive manufacturing, showcasing the technology's versatile application. Additionally, 3D printing excels in crafting intricate cellular structures that offer exceptional strength with minimal weight, a feat difficult to achieve through conventional manufacturing methods.
Disadvantages of Production 3D Printing
Production 3D printing also has some limitations and drawbacks that businesses should consider, including:
- Material Limitations
- Print Size Constraints
- Post-Processing Requirements
- Material Costs
- Equipment and Training Costs
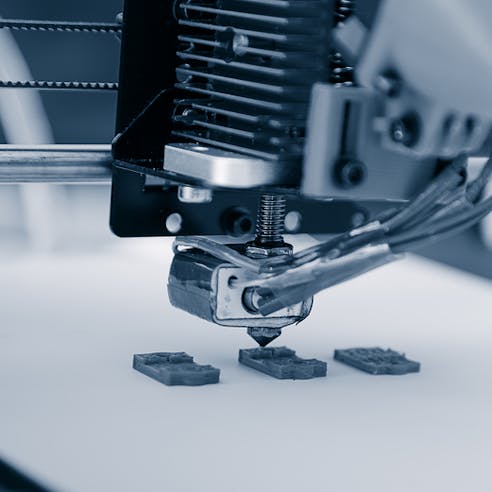
Material Limitations
While there is a growing selection of materials suitable for additive manufacturing, it may not always match the diversity of materials used in traditional manufacturing processes. For instance, specialized materials required for extreme temperatures, high-stress environments, or specific chemical resistance may have limited availability in the 3D printing market.
Print Size Constraints
The size of the 3D printer's build chamber can impose limitations on the maximum dimensions of parts that can be produced. For larger industrial-scale components, the print size constraints of some 3D printing technologies may restrict the feasibility of using production 3D printing for certain applications.
Post-Processing Requirements
Most 3D printed parts require post-processing to achieve the desired surface finish, mechanical properties, and dimensional accuracy. Depending on the technology and material used, post-processing steps such as support structure removal, sanding, sintering, polishing, or additional treatments may be necessary.
Material Costs
The costs of some 3D printing materials can still be higher than those used in traditional manufacturing processes. This could impact the overall cost-effectiveness of additive manufacturing, especially for parts with high material requirements.
Equipment and Training Costs
Adopting production 3D printing may involve upfront investments in advanced 3D printing equipment and the training of personnel to operate and maintain the technology effectively. For some businesses, this initial investment can be a barrier to entry.
Alternatives to Production 3D Printing
While production 3D printing offers numerous advantages, it's essential to consider other manufacturing methods to determine the most suitable approach for specific applications. Here are some alternative methods for comparison:
- CNC Machining
- Injection Molding
- Sheet Metal Fabrication
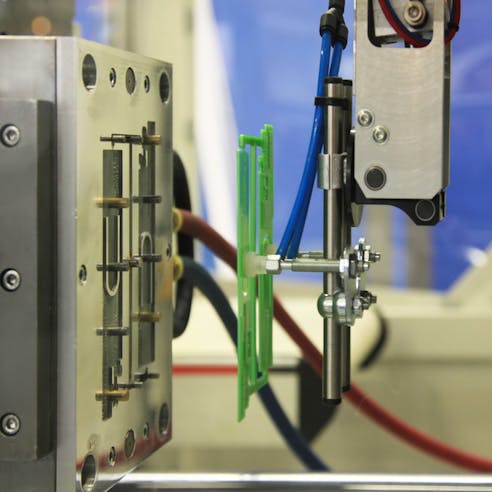
- CNC Machining: CNC machining is a subtractive manufacturing process that utilizes computer-controlled machines to remove material from a solid block, creating the desired shape. It excels in high-precision and high-accuracy applications, making it suitable for producing parts with tight dimensional requirements. CNC machining is an excellent choice for high-volume production runs, ensuring consistent and repeatable results. Nonetheless, its limitations lie in the difficulty of achieving complex geometries and the generation of material waste during the machining process.
- Injection Molding: Injection molding is widely used for mass-producing plastic parts by injecting molten plastic into a mold cavity. Its key advantage lies in high production rates, making it cost-effective for large-scale manufacturing. It offers consistency and uniformity, making it ideal for industries with high-volume demands. However, injection molding requires substantial upfront tooling costs, making it less suitable for low-volume production or prototypes. Additionally, there are also some limitations on the different shapes and complexity that are possible with injection molding.
- Sheet Metal Fabrication: Sheet metal fabrication involves cutting, bending, and forming sheet metal into various shapes and components. It is commonly used for producing structural parts and enclosures in industries like aerospace and automotive manufacturing. Sheet metal fabrication offers strength and durability, along with a wide range of metal materials. However, complex geometries may be challenging to achieve, and specific designs may require costly tooling.
Why Choose Xometry for Production 3D Printing?
Endless Options
Choose from millions of possible combinations of materials, finishes, tolerances, markings, and certifications for your order.
Easy to Use
Get your parts delivered right to your door without the hassle of sourcing, project management, logistics, or shipping.
Quality Assurance
We are ISO 9001:2015, ISO 13485 and AS9100D certified.