Nitronic 60 CNC Machining
Get instant quotes on custom nitronic 60 CNC machined parts. Make quick turn prototypes and production parts in days with free standard shipping on all US orders. ISO 9001:2015, ISO 13485, IATF 16949:2016, and AS9100D certified. ITAR registered.
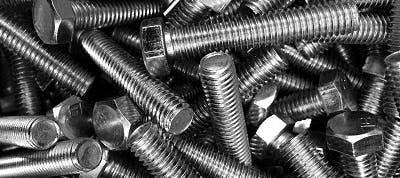
About Nitronic 60 Machining
Nitronic is a trade name for a group of nitrogen-strengthened austenitic stainless steels. Instead of only strengthening the surface of the steel via the nitriding process, nitronic alloys incorporate nitrogen homogeneously through the entire crystal structure. This property strengthens the steel throughout rather than just on the surface. The resultant metal has the same corrosion resistance as other austenitic steels like 316 stainless steel while exhibiting up to twice the yield strength. Nitronic alloys offer a low-cost alternative for wear and galling resistance when compared to nickel and cobalt alloys.
Nitronic 60 stainless steel exhibits excellent yield strength due to the inclusion of nitrogen in the alloy. It also maintains the superior corrosion resistance of other austenitic stainless steels. These properties make it uniquely suited to marine and chemical industries.
Nitronic 60
Parts made via CNC machining in Nitronic 60 differ from those in other nitronic alloys due to the material’s superior galling resistance (i.e. wear caused by localized bonding and subsequent tearing of bits of material when parts slide against each other). In addition to its galling resistance, Nitronic 60 has almost double the yield strength of more common stainless steels like 316 or 18-8. Nitronic 60 also resists corrosion far better than most similar metals. These properties make it ideal for mechanical components like shafts, fasteners, or gears that experience sliding contact and need high strength while being subjected to corrosive operating environments.
Tensile Strength, Yield (MPa) | Shear Modulus (GPa) | Elongation at Break (%) | Hardness (Brinell) | Density (g/cm^3) |
---|---|---|---|---|
Tensile Strength, Yield (MPa) 414 | Shear Modulus (GPa) 69 | Elongation at Break (%) 64 | Hardness (Brinell) 210 | Density (g/cm^3) 7.62 |
Finishes
Xometry offers the following surface finishes applicable to Nitronic 60 steel.
As-Machined (Standard): Xometry can achieve 125 Ra or better when CNC machining in Nitronic 60. Finishing passes can further refine the surface roughness. This is an ideal surface finish for Nitronic 60 due to its inherent corrosion-resistant properties and its use in sliding-contact applications.
Powder Coating: Powder coating creates an excellent and robust surface finish. Stainless steel resists corrosion by a wide array of chemicals, but some, like chlorides, still pose a challenge. Nitronic 60 provides improved resistance to chlorides compared to SS316.
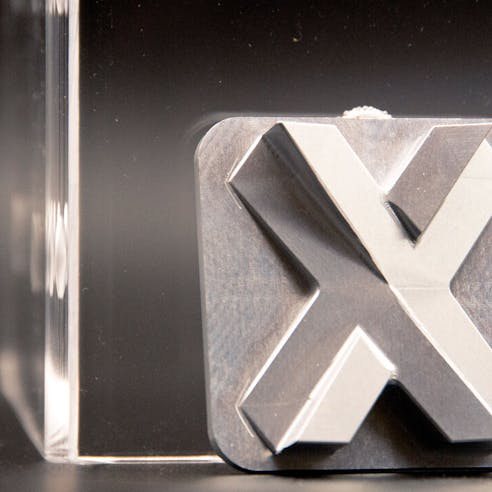
Cost-saving Design Tips
Though CNC machining in Nitronic 60 can produce superior parts compared to other stainless steels, it is more expensive. Below are our cost-saving tips:
Consider end-use application: Nitronic 60 can be a lower-cost alternative to more expensive nickel and cobalt-based alloys. However, the process of CNC machining in Nitronic 60 is more expensive than it is for other more common austenitic steels. As such, you should carefully consider when and where the metal is actually needed. For example, Nitronic 60’s galling resistance makes it ideal for fasteners that must be removed regularly. However, if the fastener is permanent and only needs to resist corrosion, cheaper stainless steel like 18-8 or 316 should be considered.
Design to existing stock sizes - Nitronic 60 machinability is generally more difficult when compared to SS316 (316’s machinability rating is 36 compared to Nitronic’s 22). With that in mind, it is important to design parts to fit as close as possible to existing stock sizes since Nitronic 60 is both an expensive material and generally more expensive to machine.