Cylindrical Grinding Services
High-quality Cylindrical Grinding Services in Days Not Weeks | Free Standard Shipping on All US Orders | Subject to availability. Xometry doesn't guarantee that we can provide this service at any given time.
Cylindrical grinding is a common process that can be applied to any component that is radially symmetrical. The most common type of cylindrical grinding is external (outer diameter or OD) grinding, where the external cylindrical surface of the part is ground. Another variation is internal cylindrical grinding, where the inside diameter (ID) is the focus.
Xometry offers cylindrical grinding as a value-added, turnkey service to our primary manufacturing processes, including CNC, 3D printing, injection molding, casting, sheet cutting, etc. A product can be fully customized using the Xometry Instant Quoting Engine®. Xometry does not provide secondary processing or finishing to parts supplied by a third party, with few exceptions. Our manufacturing experience across a variety of industries, coupled with our extensive manufacturing network, ensures that your part will be fabricated to the highest standards, within lead times that will get your finished products to your customers on time.
Cylindrical Grinding Processes
Cylindrical grinding imparts accurate dimensions onto a cylindrical part by means of a rotating grinding wheel. There are some variations in how it’s accomplished — the grinding can be external or internal. Further, the movement of the grinding wheel relative to the workpiece can differ, such as in the case of plunge grinding or traverse grinding. More detail is given below:
- External Cylindrical Grinding
- Internal Cylindrical Grinding
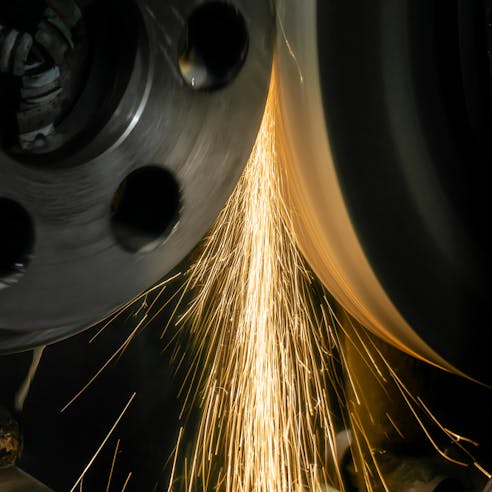
External Cylindrical Grinding
External cylindrical grinding perfects the outer dimensions and surface finish of a round part. This grinding is accomplished with a relatively large rotating grinding wheel. The workpiece is rotated while the grinding wheel rotates in the opposite direction. In this way, it looks similar to a lathe, except that the machine has a grinding wheel in place of a cutting tool.
The grinding wheel can move relative to the workpiece in a number of different ways. For plunge grinding, the centers of the workpiece and grinding wheel move gradually inwards towards each other, the grinding wheel “plunging” into the workpiece. In traverse grinding, the movement of the grinding wheel is axial, moving along the length of the workpiece.
Various grinding wheels are available for different materials and different surface finishes. The diameters and thicknesses depend on the workpiece’s geometry. The abrasive material in the grinding wheel must also be carefully selected, with common choices being diamond or cubic boron nitride. Grinding wheels vary in terms of how open, or rough, their surface is. Dressing a grinding wheel reveals a fresh abrasive surface on the wheel, and the details of how this is done will affect the final surface finish of the workpiece.
Internal Cylindrical Grinding
Internal cylindrical grinding is similar in concept to external cylindrical grinding but is used to finish the interior of a radially symmetrical workpiece. The grinding wheel, therefore, needs to be significantly smaller than the internal diameter of the hole. This version of cylindrical grinding puts more of the workpiece in contact with the grinding wheel, so heat removal and chip evacuation can be challenging.
Cylindrical Grinding Materials
Listed below are the classes of materials that can accept cylindrical grinding:
- Metals
- Ceramics
- Plastics
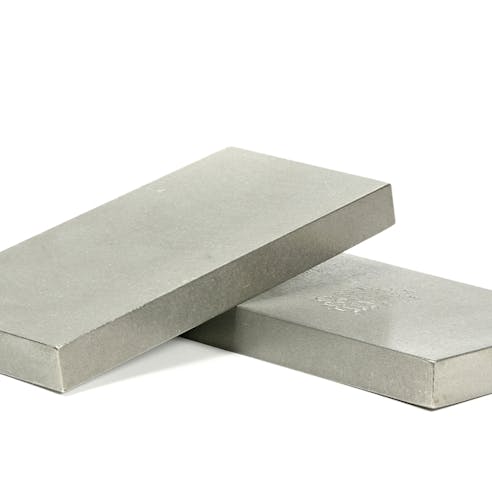
Metals
Metals are a common target for cylindrical grinding. The technique is commonly employed on hard metals such as tungsten, titanium, and various steels. Steels are available in different grades and can also be hardened. Cylindrical grinding can be applied to these various metals to smooth any ridges or imperfections and provide an impeccable surface finish.
Ceramics
Ceramics can be shaped via cylindrical grinding if it’s performed carefully. There are a number of different engineering ceramics, such as alumina, zirconia, and silicon nitride. They are incredibly hard materials, but they’re also brittle, which can make them challenging to work with. The grinding wheel needs to be selected carefully, especially since grinding wheels themselves are often made with ceramics such as cubic boron nitride.
Plastics
Cylindrical grinding can be applied even to plastic components when they need precise tolerances and smooth surface finishes. Cylindrical grinding works on both thermoplastic and thermoset plastics. Some care does need to be taken with the selection of lubricants and grinding wheels, as some plastics can embed themselves between the cutting grains and quickly “load” the grinding wheel.
Advantages of Cylindrical Grinding
Listed below are the advantages of cylindrical grinding:
- High Precision
- High-Quality Finishes
- Versatility
- Cost Effective
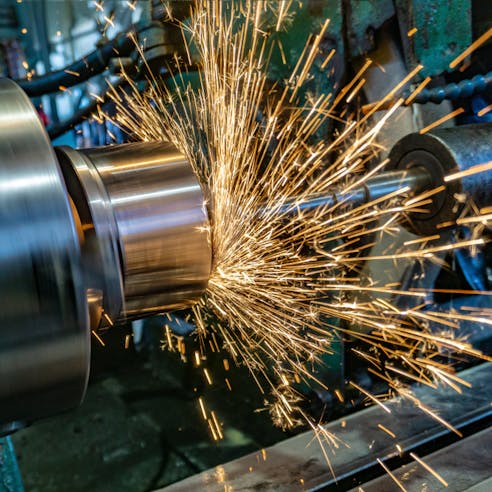
High Precision
Cylindrical grinding allows parts to be finished with very high precision. It ensures dimensional accuracy in the radial direction. Cylindrical grinding smooths out any high points or ridges and corrects out-of-roundness errors. Accurate dimensions are possible with tolerances as low as 0.00005 inches (1.3 μm).
High-Quality Finishes
Cylindrical grinding can correct surface imperfections caused by machining and also improve the surface finish. Completed surfaces can reach smoothness ratings better than 30 microinches Ra. Surface finish quality depends heavily on the proper selection and dressing of the grinding wheel.
Versatility
Cylindrical grinding is versatile and can be applied to a wide range of materials and geometries. Many different grinding wheel sizes, materials, and dressings enable this versatility. Cylindrical grinding can perfect the dimensional accuracy of items made of various steels and alloys, as well as ceramics and plastics. Variations such as plunge grinding are used for components with multiple steps and diameters. Cylindrical grinding can be applied as long as the workpiece has rotational symmetry.
Cost Effective
Cylindrical grinding is a relatively cost-effective way to manufacture or finish precise and high-quality parts, particularly when you’re making reasonable volumes of identical components. This is particularly true when care is taken to select the correct grinding wheel for the material, and when the wheel is re-dressed at appropriate intervals.
In need of custom cylindrical grinding services?
Disadvantages of Cylindrical Grinding
Listed below are the disadvantages of cylindrical grinding:
- Time Consuming
- Skilled Operator Required
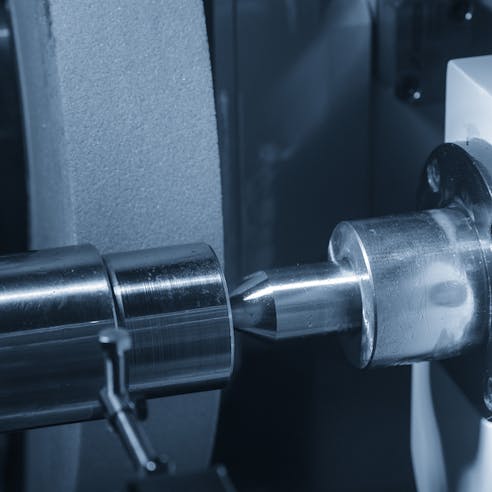
Time Consuming
Grinding by its nature removes material slowly. This means that it can be time-consuming to achieve your component’s final dimensions. A variation of cylindrical grinding, creep feed grinding, forces the removal of more material at a time in order to speed up the machining. Depending on the complexity of the workpiece and its finishing needs, the grinding machine can also take a long time to set up.
Skilled Operator Required
Some grinding processes can be difficult to manage. Internal cylindrical grinding, for instance, places a large portion of the wheel in contact with the workpiece. It takes an experienced operator who knows their way around the machine’s grinding parameters to accomplish a good quality finish.
Cylindrical Grinding Industries Served and Applications
Cylindrical grinding is applicable to a variety of industries. Some examples are listed below:
- Manufacturing
- Engineering
- Tool and Die
- Automotive Industry
- Aerospace
- Medical
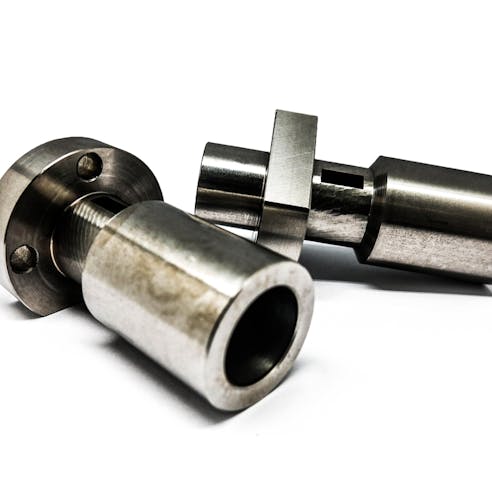
Manufacturing
Cylindrical grinders are employed to manufacture key cylindrical components and shafts used in other manufacturing industries. Some examples include spindles for textile spinning, rollers for printing, and other rollers found in continuous manufacturing processes for textiles and plastics. These rollers’ radii must be extremely precise and consistent in order to turn out quality products.
Engineering
Cylindrical grinding is an ideal way to create cylindrical components such as bolts and shafts. Every high-speed rotating shaft must be able to withstand thousands of rotations per second without taking unnecessary wear. Such shafts cannot have ridges or imperfect dimensions. Each component must be produced to precise specifications, and cylindrical grinding is often the best solution.
Tool and Die
Cylindrical grinding is a key process in the production of dies and cylindrical tools such as punches. These are fabricated from hard metal alloys but need to have accurate dimensions. Internal cylindrical grinding can also be valuable for mold making.
Automotive Industry
Cylindrical grinding is widely applied in the automotive industry for various types of shafts and axles. Complex shafts with multiple diameters and shoulders are machined via external (OD) cylindrical grinding. There are also automotive components that require accurate internal bores, where internal (ID) cylindrical grinding is applied.
Aerospace
Due to aircrafts’ extreme operating conditions, some exotic and hard-to-machine materials are necessary. Components thus have extremely stringent requirements for precision. Cylindrical grinding is one of the key steps that make possible parts like landing gear axles and turbine shafts.
Medical
In the medical industry, cylindrical grinding is important for the manufacture of implants and prosthetics. These items can only be made from a limited set of biocompatible materials including metals such as titanium and plastics such as PEEK (polyether ether ketone). Cylindrical grinding allows these materials to be accurately manufactured to precise dimensions that will meet each patient’s requirements.
Alternatives to Cylindrical Grinding
Xometry offers various alternatives to cylindrical grinding that may serve you better, depending on the part’s geometry and finish. For flat workpieces, surface grinding is the necessary approach; but even for cylindrical components, there are alternatives for grinding external and internal surfaces. These alternatives are discussed below:
- Surface Grinding
- Centerless Grinding
- Honing
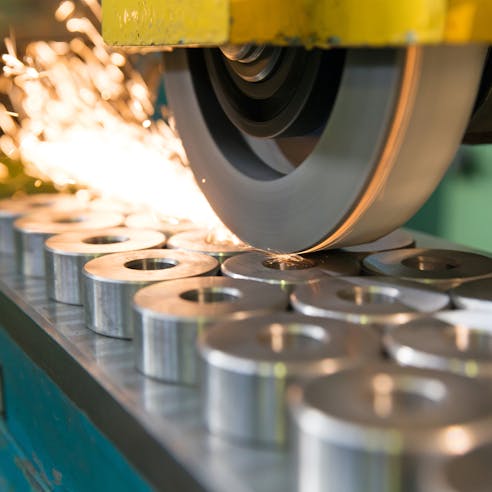
Surface Grinding
Surface grinding is the most common grinding process for flat surfaces. A rotating circular grinding wheel is still used but it operates on a flat surface. The workpiece is affixed to a table that moves to put the fixed grinding wheel in contact with the proper surfaces. This grinding approach is limited to only flat surfaces and does not work for cylindrical parts.
Centerless Grinding
Centerless grinding is an alternative grinding approach for items with rotational symmetry. The workpiece does not have to be held on its axis. In centerless grinding, the rotation of the workpiece is accomplished by a regulating wheel and a blade while the grinding wheel rotates against it. Centerless grinding can be operated as a semi-continuous operation, with identical components in a production run being successively fed through the centreless grinder.
Honing
Honing is a finishing process for holes and bores. It uses an abrasive honing tool in reciprocating or rotating motion to improve dimensional accuracy and surface finish. It differs from internal cylindrical grinding in that the honing tool does not perform significant amounts of material and the workpiece remains stationary.
Why Choose Xometry for Cylindrical Grinding Services?
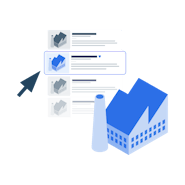
Endless Options
Choose from millions of possible combinations of materials, finishes, tolerances, markings, and certifications for your order.
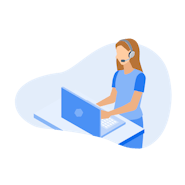
Easy to Use
Get started with our easy-to-use platform and let our experts take care of managing the project from locating the right manufacturing partner to delivery logistics.
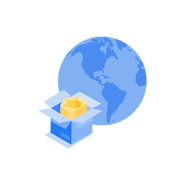
Vetted Network
We are ISO 9001:2015, ISO 13485, and AS9100D certified. Only the top shops that apply to become Suppliers make it through our qualification process.