Sheet Metal Prototyping Services
Upload your CAD files to get an instant online fabrication quote on custom formed sheet metal prototypes. Lead times as fast as days.
Sheet metal prototyping is the subtractive manufacturing process of fabricating new-concept products to verify form and function. It is a versatile and efficient rapid prototyping method used in on-demand manufacturing and metal fabrication across various industries. Each fabrication method can be used for a variety of metals.
Xometry offers high-quality sheet metal prototyping for a variety of applications, from automotive parts like fenders and floor plans to medical parts like prosthetic components and wheelchair frames. Choosing Xometry for your sheet metal prototyping needs ensures a fast turnaround of high-quality, precise components coupled with exceptional customer service.
Sheet Metal Prototyping Process
The sheet metal prototyping process consists of four steps: design review, digital modeling, production, and final quality inspection. Before sheet metal prototypes are made, the product’s design must first be reviewed and verified for compatibility with the various sheet metal fabrication methods. In this initial stage, the material type, geometry, and appearance requirements are considered to determine the manufacturing method best suited to produce the prototype parts. Once the product design is verified and deemed suitable for sheet metal fabrication processes, the process flow, process parameters, tool paths, and machine settings are created. The production of the sheet metal prototypes will then begin once the process flow and parameters are established. After the sheet metal prototypes are produced, a final quality inspection is completed to ensure dimensional tolerances and aesthetic requirements are met. The parts are then shipped to the company who initially requested the parts to be made.
Materials and Techniques Used for Sheet Metal Prototypes
Many different materials and techniques can be used for the fabrication of sheet metal prototypes. Similarly, many different fabrication methods can be used to convert raw sheet metal material into finished parts. Common materials used for sheet metal prototypes include: steel, stainless steel, aluminum, copper, bronze, titanium, and nickel alloys. Xometry also uses various fabrication methods for sheet metal manufacturing which include: laser cutting, waterjet cutting, plasma cutting, CNC bending, CNC forming, and welding.
Sheet Metal Prototyping Industries
A broad range of industries use sheet metal prototyping to test and verify new products and designs. The different industries and how they use sheet metal prototyping are described below:
- Electronics
- Automotive
- Aerospace
- Consumer Goods
- Medical
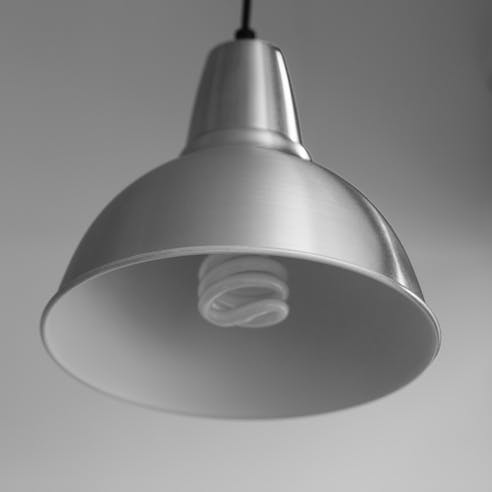
Electronics
Sheet metal products are common in the electronics industry. Protective housings for cell phones, computers, and other electronic devices are commonly fabricated from aluminum, stainless steel, and steel sheet metal. Additionally, sheet metal is commonly used in light fixtures, household appliances, and industrial machinery.
Automotive
Steel, stainless steel, aluminum, and titanium sheet metal are all used in the automotive industry for different applications. Parts like fenders, panels, brackets, and housings for automotive electronic equipment are commonly made from sheet metal.
Aerospace
Aluminum, titanium, and nickel alloys are three sheet metal materials commonly used in the aerospace industry. From brackets and frame components to jet engine turbines to avionic housings, sheet metal fabrication is widely employed in the aerospace industry.
Consumer Goods
Consumer goods can range from everyday kitchen appliances and toys to tools and furniture. Sheet metal is often used for panels in washing machines, dryers, and coffee makers, as well as brackets for furniture and components for toys.
Medical
The medical industry commonly features sheet metal components. Titanium sheet metal is often used in the creation of prostheses, while stainless steel sheet metal is often used for protective housings for medical diagnostic equipment and electronics.
Advantages of Sheet Metal Prototyping
Sheet metal prototypes have key advantages over prototypes produced by other rapid prototyping methods like CNC machining, plastic injection molding, and 3D printing. Sheet metal prototyping advantages include:
- Cost Effective
- Fast Turnaround
- Design Flexibility
- Material Variety
- Complex Geometries
- Reduced Lead Times
- Material Optimization
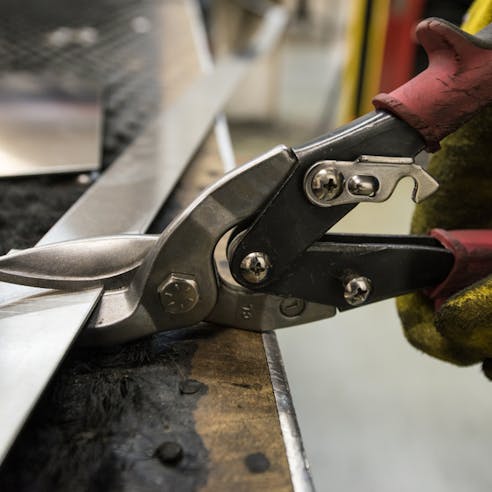
Cost Effective
Sheet metal prototyping is a cost-effective method of producing prototypes. This is due to many reasons, including: simple and affordable tooling and machinery, reduced lead times, quick cycle times, and optimized material usage.
Fast Turnaround
Another key advantage of sheet metal prototyping is the fast turnaround for complete parts. Sheet metal fabrication methods like laser cutting, waterjet cutting, plasma cutting, bending, forming, and welding can all be automated and CNC-controlled. The high degree of automation reduces the need for human intervention and ensures that parts are made in a fast and repeatable manner.
Design Flexibility
Sheet metal prototyping offers designers a high degree of design flexibility since many different manufacturing methods can be used to fabricate sheet metal parts. This enables manufacturers to determine the technique most suitable for their product based on their design requirements and production goals.
Material Variety
Sheet metal prototyping is suitable for a variety of different metals—from steel and aluminum to bronze and brass. This makes sheet metal prototyping a versatile process that can be used to fabricate different sheet metal products easily.
Complex Geometries
Complex geometries can easily be made by sheet metal prototyping methods. Processes like laser cutting, waterjet cutting, and plasma cutting can be used to create complex 2D features while bending and forming can be used to create 3D features. Because these processes are largely automated, complex geometries can be made swiftly and in a repeatable manner.
Reduced Lead Times
Reduced lead times for sheet metal prototyping is the norm. This is because sheet metal fabrication tooling is simple to set up. Additionally, because cut paths and forming processes are simple to program, manufacturers can quickly translate a design from a CAD model to a finished product.
Material Optimization
Sheet metal fabrication techniques are great for optimizing material usage. This is because multiple parts can be made from a single piece of sheet metal regardless of whether cutting or forming methods are used. Not only does material optimization lead to more efficient manufacturing processes, but it also helps manufacturers reduce their carbon footprint.
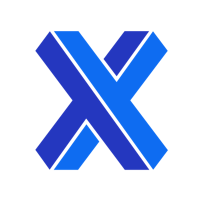
Ready to Get a Sheet Metal Prototype Quote?
Free shipping available for domestic sheet metal orders ; learn more!
Disadvantages of Sheet Metal Prototyping
Sheet metal prototyping is not without its disadvantages. Below are some drawbacks of sheet metal prototyping.
- Tooling Costs
- Limited Material Choices
- Batch Production Constraints
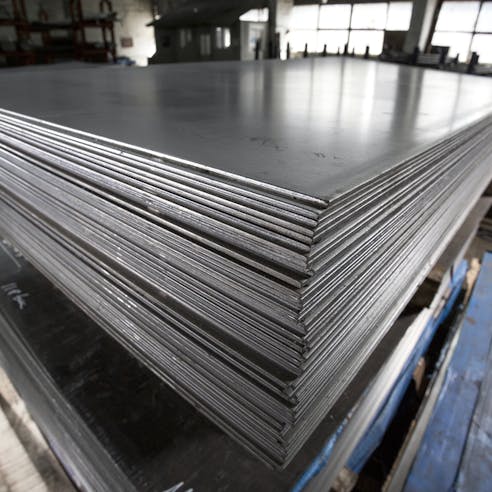
Tooling Costs
Tooling costs for sheet metal prototyping are wide-ranging but can be expensive when it comes to laser cutting, waterjet cutting, and plasma cutting machines. Fiber laser or CO2 laser cutting machines capable of cutting sheet metal can easily cost anywhere between $30,000–$1,000,000. The high upfront costs for these machines are precisely why many companies opt to use Xometry for their sheet metal prototyping needs.
Limited Material Choices
While sheet metal prototyping is suitable for a variety of metals, it cannot be used for the fabrication of prototype parts made from plastics. Alternative manufacturing methods like injection molding, plastic extrusion, and CNC machining are needed to produce plastic prototype parts.
Batch Production Constraints
Though sheet metal fabrication is great for optimized material usage, sheet metal fabrication processes are constrained when it comes to producing large batches. This is because the process is slow compared to other manufacturing methods like metal stamping or pressing. Additionally, post-processes like painting, finishing, and surface treatments constrain the speed at which products can be made.
Alternatives to Sheet Metal Prototyping
While sheet metal fabrication methods are capable of producing high-quality prototypes, some part features, like undercuts, or thicker parts (<~0.2") may not be achievable. Consequently, there are many alternative rapid prototyping methods to sheet metal prototyping. The different alternatives are described below.
- CNC Machining
- 3D Printing
- Injection Molding
- Vacuum Forming
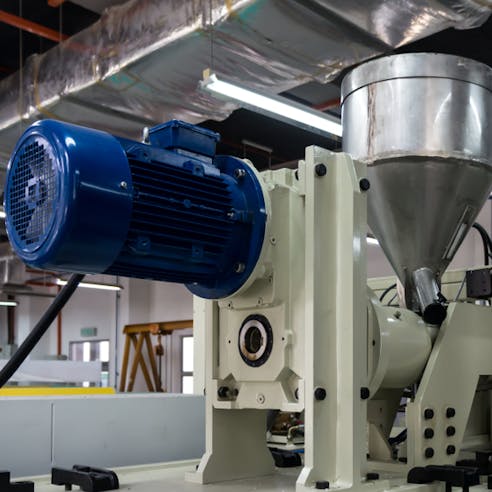
- CNC Machining: CNC machining is a reliable rapid prototyping method for fabricating with sheet metal. While CNC machining can be used to cut features into thin sheet metal workpieces, the process can also be used to create 3D parts thicker than the thickest sheet metal gauge (around 0.18" depending on the type of material). Like sheet metal fabrication methods, CNC machining is largely automated and requires little human intervention.
- 3D Printing: 3D printing is another great alternative for producing prototype parts. 3D printing is capable of creating the same thin, flat parts commonly fabricated from sheet metal, but is also capable of producing intricate and complex 3D parts. While 3D printing is a slow process compared to sheet metal fabrication techniques, the potential features that can be created with 3D printing are unmatched.
- Injection Molding: Injection molding is a manufacturing method used to create 3D parts out of thermoplastics and thermosets. Compared to sheet metal prototyping, injection molding prototyping is more expensive due to the costs associated with producing molds and die sets. Because parts are largely complete after injection require little post-processing and cycle times are short, injection molding is great for producing large volumes of parts.
- Vacuum Forming: Vacuum forming is a thermoforming process used to create parts from thermosets. The process uses a heated plastic sheet and forces it over a mold to produce parts. Because of its low cost, high efficiency, and ability to make large parts, vacuum forming is a great alternative to sheet metal prototyping. Vacuum forming can be used to make many of the same parts produced by sheet metal fabrication techniques but out of plastics. Parts like enclosures, housings, and panels can all be created by vacuum forming.
Why Use Xometry's Sheet Metal Prototyping Services?
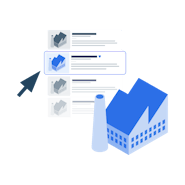
Endless Options
Choose from thousands of possible combinations of sheet metal materials, finishes, tolerances, markings, and certifications for your order.
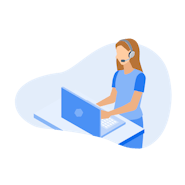
Easy to Use
Get your parts delivered right to your door without the hassle of sourcing, project management, logistics, or shipping.
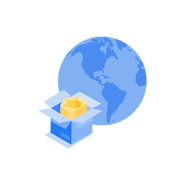
Vetted Network
We are ISO 9001:2015, ISO 13485, and AS9100D certified. Only the top shops that apply to become Suppliers make it through our qualification process.