Aluminum CNC Machining
Get instant quotes on custom aluminum machined parts with our Online CNC Machining Service. Make quick turn prototypes and production parts in days with free standard shipping on all US orders. ISO 9001:2015, ISO 13485, and AS9100D certified. ITAR registered.
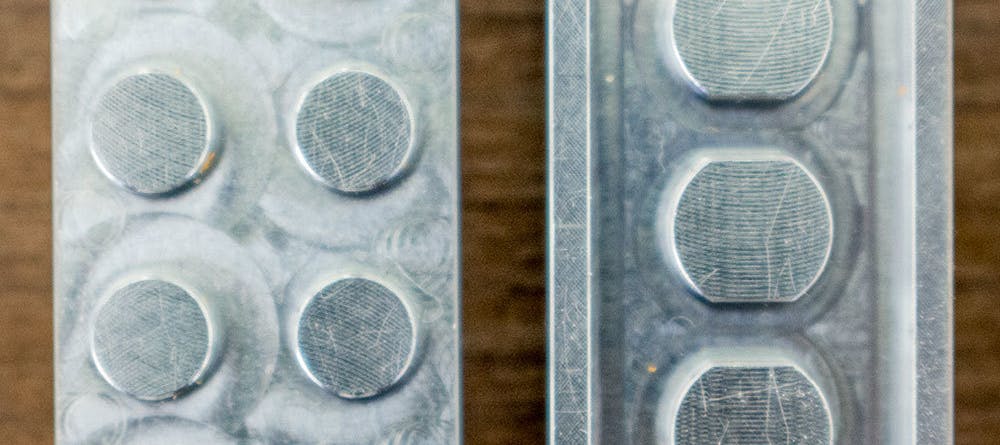
Aluminum CNC Machining
Aluminum is a lightweight metal with an excellent strength-to-weight ratio, making it ideal for applications in which metallic-level strength is required, but mass is still a concern. There are various alloys for aluminum, each denoted by the first number in their classification. The number indicates the main alloying element(s).
Aluminum is one of the most common materials used in the aerospace, medical, and automotive industries. This is due to its excellent strength-to-weight ratio, formability, and general versatility. Choose aluminum CNC machining in the Xometry Instant Quoting Engine℠.
Aluminum 2024-T3
This aluminum alloy resists fatigue well and is quite machinable, but exhibits poor weldability characteristics. It is not very resistant to corrosion, so it requires surface treatments if used in harsh environments. Aluminum 2024-T3 is typically used for bolts, aircraft fittings, and pistons.
Tensile Strength, Yield (MPa) | Fatigue Strength (MPa) | Elongation at Break (%) | Hardness (Brinell) | Density (g/cm^3) |
---|---|---|---|---|
Tensile Strength, Yield (MPa) 345 | Fatigue Strength (MPa) 138 | Elongation at Break (%) 18 | Hardness (Brinell) 120 | Density (g/cm^3) 2.78 |
* Generalized values. For reference only.
Aluminum 5052-H32
This aluminum alloy uses magnesium as its primary alloying element. It is very corrosion-resistant due to the lack of copper in its composition but it cannot be heat-treated. Aluminum 5052 is typically used in fuel tanks, sheet metal parts, and fuel/oil lines.
Tensile Strength, Yield (MPa) | Fatigue Strength (MPa) | Elongation at Break (%) | Hardness (Brinell) | Density (g/cm^3) |
---|---|---|---|---|
Tensile Strength, Yield (MPa) 193 | Fatigue Strength (MPa) 117 | Elongation at Break (%) 12 | Hardness (Brinell) 60 | Density (g/cm^3) 2.68 |
* Generalized values based upon Aluminum 5052-H32. For reference only.
Aluminum 6061
This grade of aluminum is considered a general-purpose alloy. It has excellent machinability characteristics and can be easily welded. The primary alloying elements are magnesium and silicon. This aluminum alloy is regularly used to make electrical fittings, brake pistons, and bike frames.
Tensile Strength, Yield (MPa) | Fatigue Strength (MPa) | Elongation at Break (%) | Hardness (Brinell) | Density (g/cm^3) |
---|---|---|---|---|
Tensile Strength, Yield (MPa) 276 | Fatigue Strength (MPa) 96.5 | Elongation at Break (%) 17 | Hardness (Brinell) 95 | Density (g/cm^3) 2.7 |
* Generalized values based upon 1/2" Aluminum 6061-T6. For reference only.
Aluminum 6063
There is only a slight difference between the alloying elements in aluminum 6063 as compared to 6061. This aluminum alloy is not as strong but offers better formability. As a result, it’s well-suited for pipes, railings, and extrusions.
Tensile Strength, Yield (MPa) | Fatigue Strength (MPa) | Elongation at Break (%) | Hardness (Brinell) | Density (g/cm^3) |
---|---|---|---|---|
Tensile Strength, Yield (MPa) 214 | Fatigue Strength (MPa) 68.9 | Elongation at Break (%) 12 | Hardness (Brinell) 73 | Density (g/cm^3) 2.7 |
* Generalized values based upon 1/16" Aluminum 6063-T6. For reference only.
Aluminum 7050
This aluminum alloy is one of the strongest available. Its main alloying element is zinc. Aluminum 7050 achieves its strength by sacrificing corrosion resistance; the inclusion of copper is the reason behind both effects. This alloy is also highly machinable. Its strength makes it ideally suited for aircraft structures.
Tensile Strength, Yield (MPa) | Fatigue Strength (MPa) | Elongation at Break (%) | Hardness (Brinell) | Density (g/cm^3) |
---|---|---|---|---|
Tensile Strength, Yield (MPa) 490 | Fatigue Strength (MPa) 160 | Elongation at Break (%) 11 | Hardness (Brinell) 147 | Density (g/cm^3) 2.83 |
* Generalized values based upon1/2" Aluminum 7050-T7651. For reference only.
Aluminum 7075
This alloy is slightly stronger than 7050 aluminum and has very good fatigue resistance, making it ideal for applications that undergo cyclic loading. Its main alloying element is zinc and its typical applications include meter shafts and gears, aircraft fittings, and shaft keys.
Tensile Strength, Yield (MPa) | Fatigue Strength (MPa) | Elongation at Break (%) | Hardness (Brinell) | Density (g/cm^3) |
---|---|---|---|---|
Tensile Strength, Yield (MPa) 503 | Fatigue Strength (MPa) 159 | Elongation at Break (%) 11 | Hardness (Brinell) 150 | Density (g/cm^3) 2.81 |
* Generalized values based upon 1/2" Aluminum 7075-T6. For reference only.
Aluminum MIC-6
This aluminum alloy is cast specifically for applications that require highly accurate components like assembly jigs, test structures, and fixture plates. It is well-suited to these applications because its crystal structure has no internal stresses. It also allows for high-speed machining without the significant distortion common in other aluminum alloys.
Tensile Strength, Yield (MPa) | Fatigue Strength (MPa) | Elongation at Break (%) | Hardness (Brinell) | Density (g/cm^3) |
---|---|---|---|---|
Tensile Strength, Yield (MPa) 105 | Fatigue Strength (MPa) N/A | Elongation at Break (%) 3 | Hardness (Brinell) 65 | Density (g/cm^3) 2.7 |
* Generalized values. For reference only.
Finishes and Post-Processing Options
Xometry offers a wide range of surface finishes suitable for aluminum alloys. The most popular surface finishing process is anodization. Both normal- and hard-coating anodizing are offered to improve the wear resistance and the corrosion resistance of the various available alloys. Chemical conversion coating and metal plating are also available for aluminum alloys. Learn more about the surface finishes we offer.
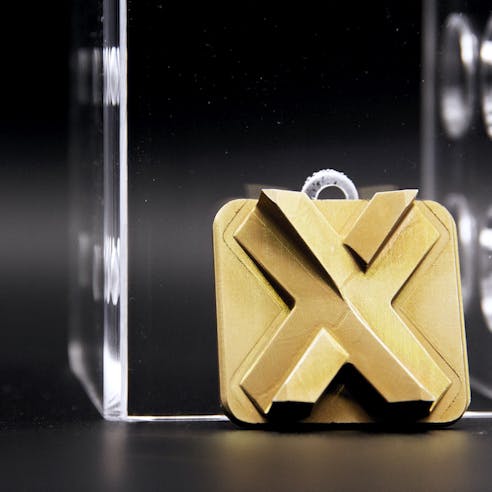
Cost-saving Design Tips
Design for manufacturing: The first way to save cost when machining an aluminum alloy part is by following design for manufacturing principles to limit the use of difficult-to-machine features. Learn more here.
Choose the right alloy: Not all aluminum alloys are equal in price. If the part is only a prototype, using the most advanced and expensive alloy may not be necessary. To learn more, contact a Xometry expert.
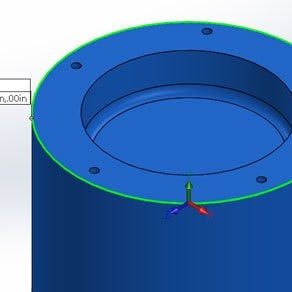