Brass CNC Machining Service
Get instant quotes on custom CNC brass parts with our Online CNC Machining Service. Make quick-turn prototypes and production parts in days with free standard shipping on all US orders. ISO 9001:2015, ISO 13485, and AS9100D certified. ITAR registered.
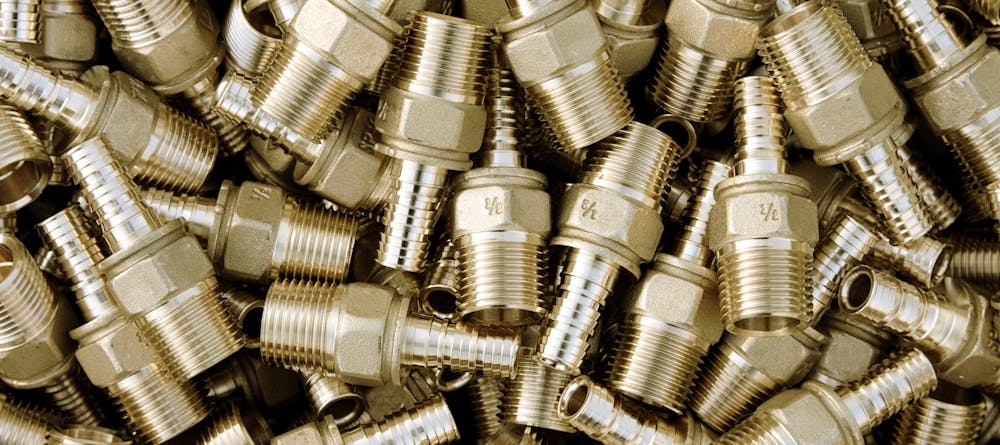
CNC Machining Brass
Brass is the name used for a wide range of copper-zinc alloys. These alloys vary by the amount of zinc as well as the inclusion of other alloying elements such as lead, aluminum, and iron. Brass is thermally and electrically conductive thanks to its copper content. It also has good wear resistance. The inclusion of lead improves machinability, making brass the most machinable of all the copper alloys. Choose Brass CNC machining in the Xometry Instant Quoting Engine℠
Brass is a versatile copper alloy that retains some of the benefits of copper but also improves on some of its attributes. Brass is a mechanically stronger and lower-friction metal, and offers better corrosion and wear resistance than basic copper. These properties make CNC machining brass ideal for mechanical applications that also require corrosion resistance such as those encountered in the marine industry.
Cartridge Brass (Copper C260)
Copper C260 is a zinc-alloyed formulation with approximately 30% zinc with less than 1% lead and iron. This grade is sometimes referred to as cartridge brass thanks to its history of use in ammunition cartridges. Other common applications include rivets, hinges, and radiator cores.
Tensile Strength, Yield (MPa) | Fatigue Strength (MPa) | Elongation at Break (%) | Hardness (Brinell) | Density (g/cm^3) |
---|---|---|---|---|
Tensile Strength, Yield (MPa) 95 | Fatigue Strength (MPa) 90 | Elongation at Break (%) 65 | Hardness (Brinell) 54 | Density (g/cm^3) 8.53 |
* Generalized values. For reference only.
Free-Cutting Brass (Copper C360)
Copper C360, also referred to as free-cutting brass, is highly machinable due to the relatively high amount of lead in the alloy. Typical applications include gears, screw machine parts, and valve components.
Tensile Strength, Yield (MPa) | Fatigue Strength (MPa) | Elongation at Break (%) | Hardness (Brinell) | Density (g/cm^3) |
---|---|---|---|---|
Tensile Strength, Yield (MPa) 124 to 310 | Fatigue Strength (MPa) 138 | Elongation at Break (%) 53 | Hardness (Brinell) 63 to 130 | Density (g/cm^3) 8.49 |
* Generalized values. For reference only. Values vary greatly depending on temper.
Finishes and Post-Processing Options
Like stainless steel or copper, brass is often left uncoated due to its inherent conductivity, corrosion resistance, and low friction coefficient. However, clear coating is considered if the application is cosmetic and the part is exposed to the elements. Listed below are some useful surface finishes for CNC machined brass.
Hand polishing, buffing, or honing: Brass is often used for ornamental applications. This is in part because different brass alloys naturally show up in different colors. Polishing brass can produce a very smooth and shiny surface, making it ideal for aesthetic components.
As Machined: Brass readily accepts machining, so its freshly machined surfaces often come out with attractive finishes even without any extra attention. As such, it’s often viable to just leave the part as machined. The surface finish is further improved with additional finishing passes.
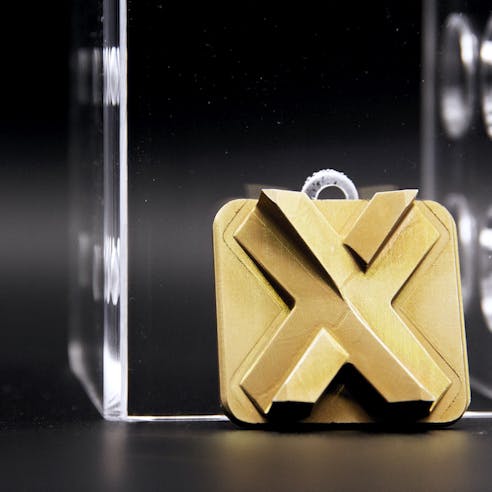
Cost-saving Design Tips
Brass is a costly material, so optimization of its use is recommended.
Design for manufacturing (DFM): Even though brass is easy to machine, take care to design parts that follow the applicable DFM principles. In addition to this, designing the part to minimize the number of machine setups will further reduce the cost of machining.
Choose the right grade: If the application is a purely cosmetic one, it is not necessary to use high-strength or low-friction brass. If, however, your part needs a lot of machining, (like a gear, for example) then a more machinable brass is used in order to minimize machining time.
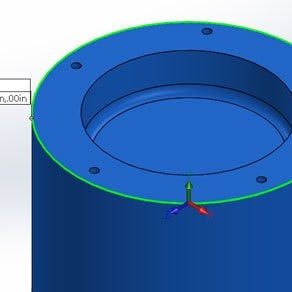