Stereolithography (SLA) 3D Printing Services
High Detail, Smooth Surfaced Parts in Days
Free shipping on all US 3D printing orders
High-Resolution, Accurate Parts without Tooling
Stereolithography (SLA) is a powerful 3D printing technology that produces extremely accurate and high-resolution parts that can be used directly in end-use, low-volume production, or rapid prototyping. Xometry offers over 20 uniquely engineered SLA materials from Accura, Somos, and Formlabs, which can enable products to be brought to the market.
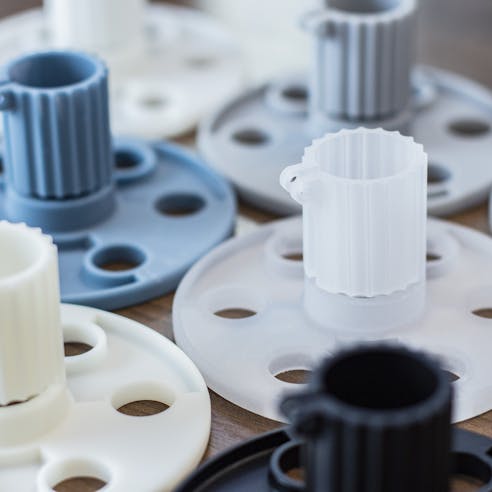
Introducing Formlabs Materials
We’re happy to announce the launch of Formlabs SLA resins on Xometry’s Instant Quoting Engine®! Formlabs is a key innovator in stereolithography (SLA) 3D printing, offering a versatile portfolio of low-cost engineered materials with professional results that meet various engineering and design needs. From general prototyping to demanding functional applications, their materials empower users to create high-resolution parts with specific mechanical, thermal, and visual properties. Read more about our new Formlabs materials.
General Purpose Materials
Material Name | Short Description | Flexural Strength (MPa) | Elongation at Break (%) | Notched Izod Impact (J/m) | HDT @ 0.45 MPa (°C) | Technical Datasheet |
---|---|---|---|---|---|---|
Material Name Accura 25 | Short Description White, general purpose | Flexural Strength (MPa) 55 MPa | Elongation at Break (%) 13.0% | Notched Izod Impact (J/m) 19 J/m | HDT @ 0.45 MPa (°C) 58°C | Technical Datasheet |
Material Name Accura ABS Black (SL 7820) | Short Description Black, general purpose | Flexural Strength (MPa) 75 MPa | Elongation at Break (%) 6.0% | Notched Izod Impact (J/m) 39 J/m | HDT @ 0.45 MPa (°C) 51°C | Technical Datasheet |
Material Name Formlabs Grey V5 | Short Description Grey, general purpose | Flexural Strength (MPa) 103 MPa | Elongation at Break (%) 13.0% | Notched Izod Impact (J/m) 32 J/m | HDT @ 0.45 MPa (°C) 71°C | Technical Datasheet |
Material Name Formlabs White V5 | Short Description Bright white, general purpose | Flexural Strength (MPa) 103 MPa | Elongation at Break (%) 13.0% | Notched Izod Impact (J/m) 32 J/m | HDT @ 0.45 MPa (°C) 71°C | Technical Datasheet |
*Material Properties are with Post-Thermal Cure
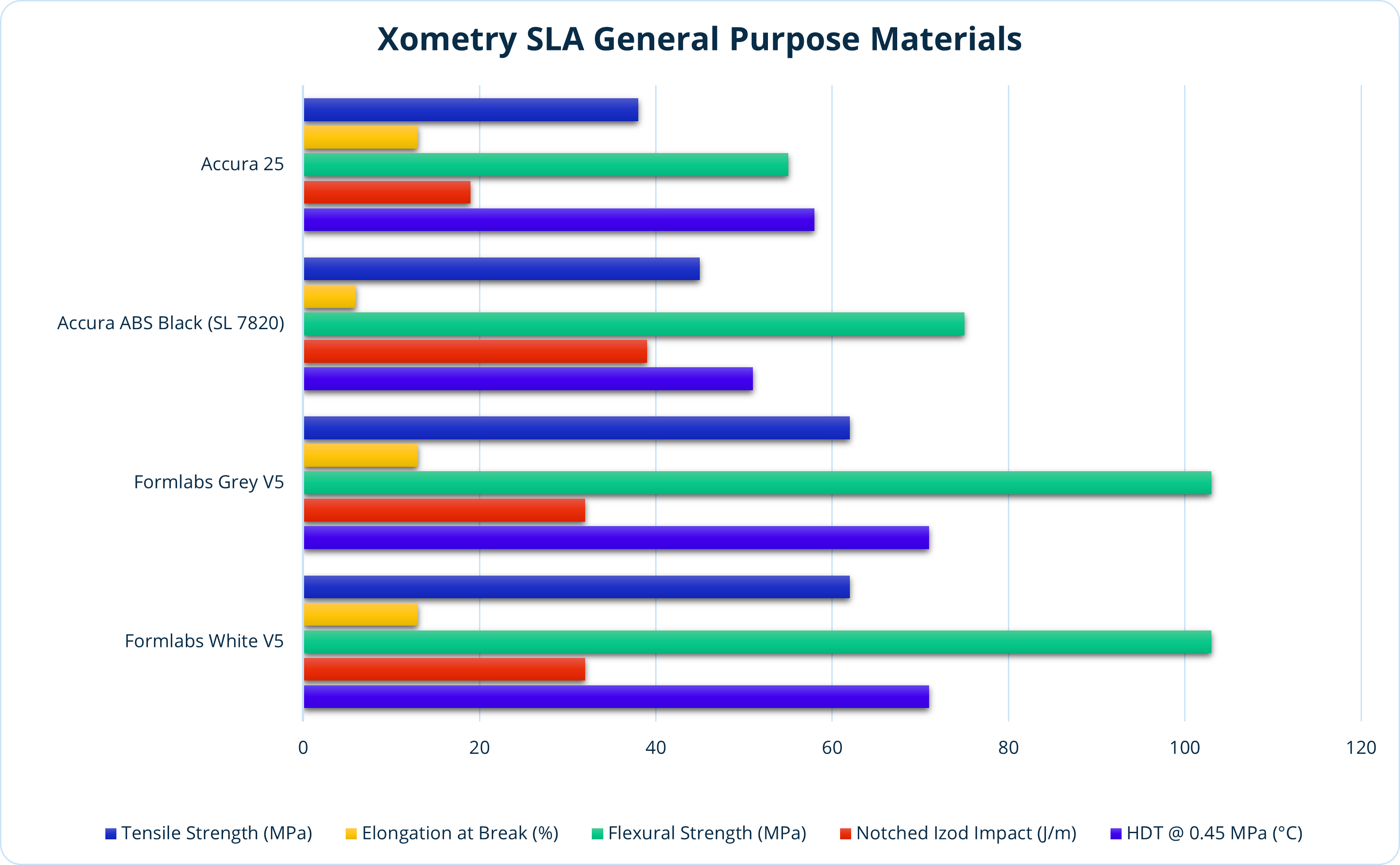
Durable Stereolithography Materials
Material Name | Short Description | Flexural Strength (MPa) | Elongation at Break (%) | Notched Izod Impact (J/m) | HDT @ 0.45 MPa (°C) | Technical Datasheet |
---|---|---|---|---|---|---|
Material Name Accura Xtreme Grey | Short Description Grey, durable | Flexural Strength (MPa) 52 MPa | Elongation at Break (%) 14.0% | Notched Izod Impact (J/m) 35 J/m | HDT @ 0.45 MPa (°C) 62°C | Technical Datasheet |
Material Name Accura Xtreme White 200 | Short Description White, durable | Flexural Strength (MPa) 75 MPa | Elongation at Break (%) 7.0% | Notched Izod Impact (J/m) 55 J/m | HDT @ 0.45 MPa (°C) 47°C | Technical Datasheet |
Material Name Formlabs Tough 1500 V2 | Short Description Grey, durable, compliant | Flexural Strength (MPa) 41 MPa | Elongation at Break (%) 155.0% | Notched Izod Impact (J/m) 45 J/m | HDT @ 0.45 MPa (°C) 66°C | Technical Datasheet |
Material Name Formlabs Tough 2000 | Short Description Grey, durable | Flexural Strength (MPa) 71 MPa | Elongation at Break (%) 51.0% | Notched Izod Impact (J/m) 41 J/m | HDT @ 0.45 MPa (°C) 54°C | Technical Datasheet |
Material Name Somos EvoLVe 128 | Short Description Off-white, durable | Flexural Strength (MPa) 67 MPa | Elongation at Break (%) 11.0% | Notched Izod Impact (J/m) 38.9 J/m | HDT @ 0.45 MPa (°C) 52.3°C | Technical Datasheet |
Material Name Somos Taurus | Short Description Charcoal gray, durable, robust | Flexural Strength (MPa) 62.7 MPa | Elongation at Break (%) 17.0% | Notched Izod Impact (J/m) 35.8 J/m | HDT @ 0.45 MPa (°C) 91°C | Technical Datasheet |
*Material Properties are with Post-Thermal Cure
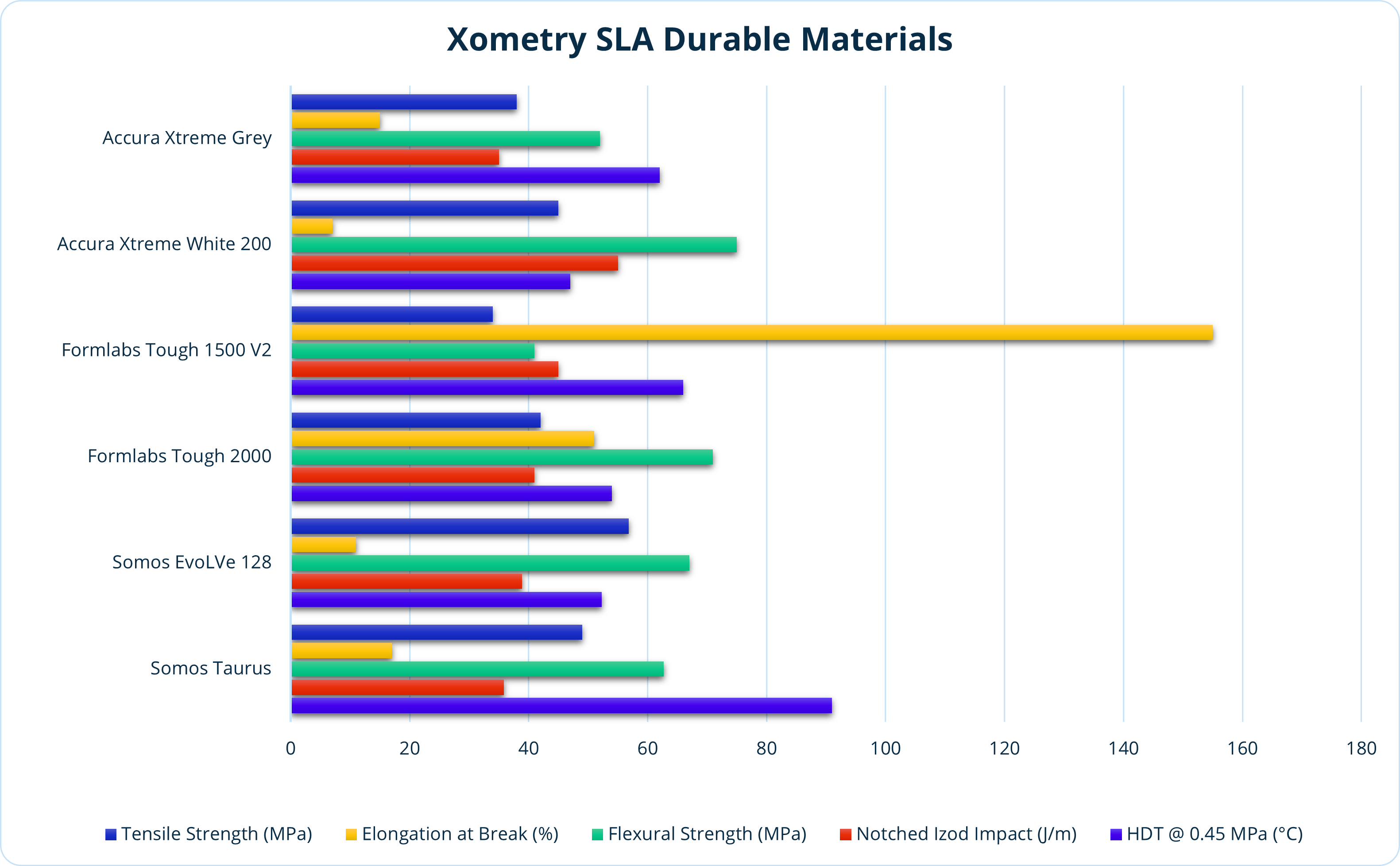
Clear Stereolithography Materials
Material Name | Short Description | Flexural Strength (MPa) | Elongation at Break (%) | Notched Izod Impact (J/m) | HDT @ 0.45 MPa (°C) | Technical Datasheet |
---|---|---|---|---|---|---|
Material Name Accura 60 | Short Description Clear, rigid, and strong | Flexural Strength (MPa) 87 MPa | Elongation at Break (%) 5.0% | Notched Izod Impact (J/m) 15 J/m | HDT @ 0.45 MPa (°C) 53°C | Technical Datasheet |
Material Name Accura ClearVue | Short Description Clear, excellent clarity | Flexural Strength (MPa) 72 MPa | Elongation at Break (%) 3.0% | Notched Izod Impact (J/m) 40 J/m | HDT @ 0.45 MPa (°C) 51°C | Technical Datasheet |
Material Name Formlabs Clear v5 | Short Description Colorless clear | Flexural Strength (MPa) 103 MPa | Elongation at Break (%) 8.0% | Notched Izod Impact (J/m) 29 J/m | HDT @ 0.45 MPa (°C) 69°C | Technical Datasheet |
Material Name Somos WaterClear Ultra 10122 | Short Description Colorless, clear, polishes well | Flexural Strength (MPa) 84 MPa | Elongation at Break (%) 7.5% | Notched Izod Impact (J/m) 25 J/m | HDT @ 0.45 MPa (°C) 47°C | Technical Datasheet |
Material Name Somos WaterShed XC 11122 | Short Description Near-colorless clear | Flexural Strength (MPa) 68.7 MPa | Elongation at Break (%) 15.5% | Notched Izod Impact (J/m) 25 J/m | HDT @ 0.45 MPa (°C) 50°C | Technical Datasheet |
*Material Properties are with Post-Thermal Cure
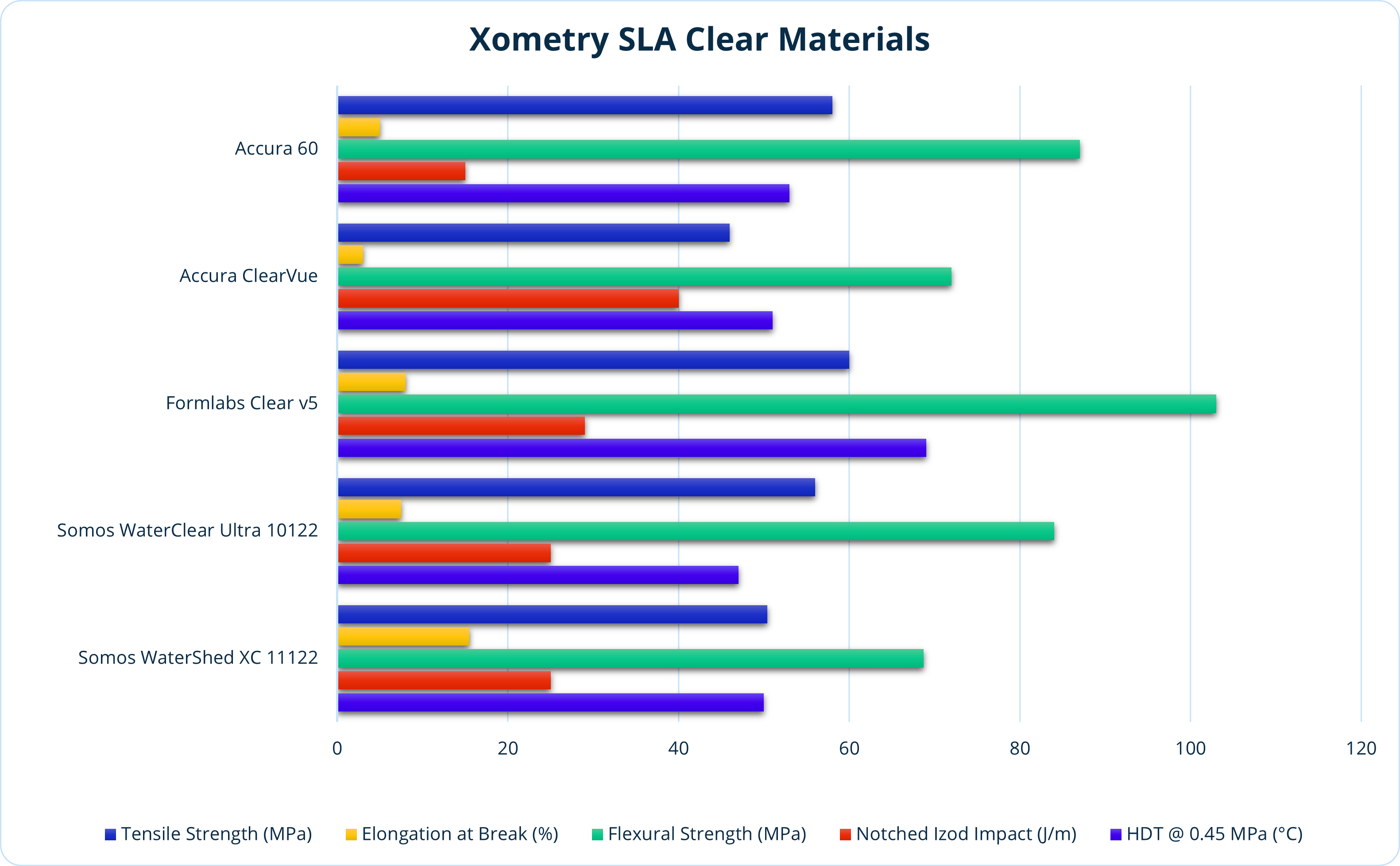
Highly Stiff Stereolithography Materials
Material Name | Short Description | Flexural Strength (MPa) | Elongation at Break (%) | Notched Izod Impact (J/m) | HDT @ 0.45 MPa (°C) | Technical Datasheet |
---|---|---|---|---|---|---|
Material Name Accura Bluestone* | Short Description Blue, highly stiff composite | Flexural Strength (MPa) 124 MPa | Elongation at Break (%) 1.4% | Notched Izod Impact (J/m) 13 J/m | HDT @ 0.45 MPa (°C) 65°C | Technical Datasheet |
Material Name Formlabs Rigid 10K* | Short Description Off-white, highly stiff composite | Flexural Strength (MPa) 103 MPa | Elongation at Break (%) 1.0% | Notched Izod Impact (J/m) 18 J/m | HDT @ 0.45 MPa (°C) 218°C | Technical Datasheet |
Material Name Somos PerFORM* | Short Description Off-white, highly stiff composite | Flexural Strength (MPa) 146 MPa | Elongation at Break (%) 1.2% | Notched Izod Impact (J/m) 20 J/m | HDT @ 0.45 MPa (°C) 268°C | Technical Datasheet |
*Material Properties are with Post-Thermal Cure
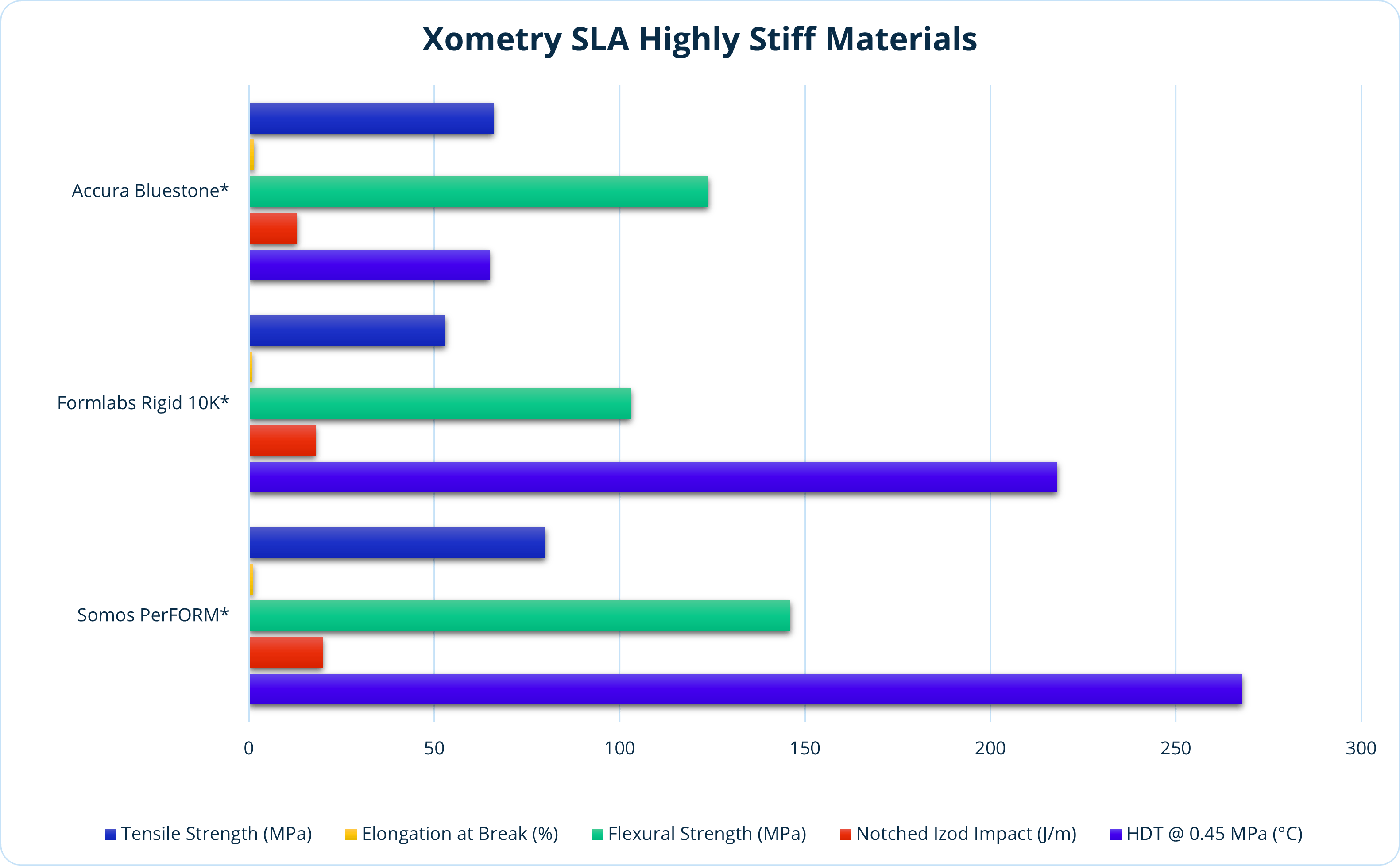
Specialty Stereolithography Materials
Material Name | Short Description | Flexural Strength (MPa) | Elongation at Break (%) | Notched Izod Impact (J/m) | HDT @ 0.45 MPa (°C) | Technical Datasheet |
---|---|---|---|---|---|---|
Material Name Formlabs ESD | Short Description Black, ESD-safe | Flexural Strength (MPa) 61 MPa | Elongation at Break (%) 12.0% | Notched Izod Impact (J/m) 26 J/m | HDT @ 0.45 MPa (°C) 62.2°C | Technical Datasheet |
Material Name Formlabs High Temp* | Short Description Translucent, high HDT (238°C) | Flexural Strength (MPa) 97 MPa | Elongation at Break (%) 2.3% | Notched Izod Impact (J/m) 17 J/m | HDT @ 0.45 MPa (°C) 238°C | Technical Datasheet |
*Material Properties are with Post-Thermal Cure
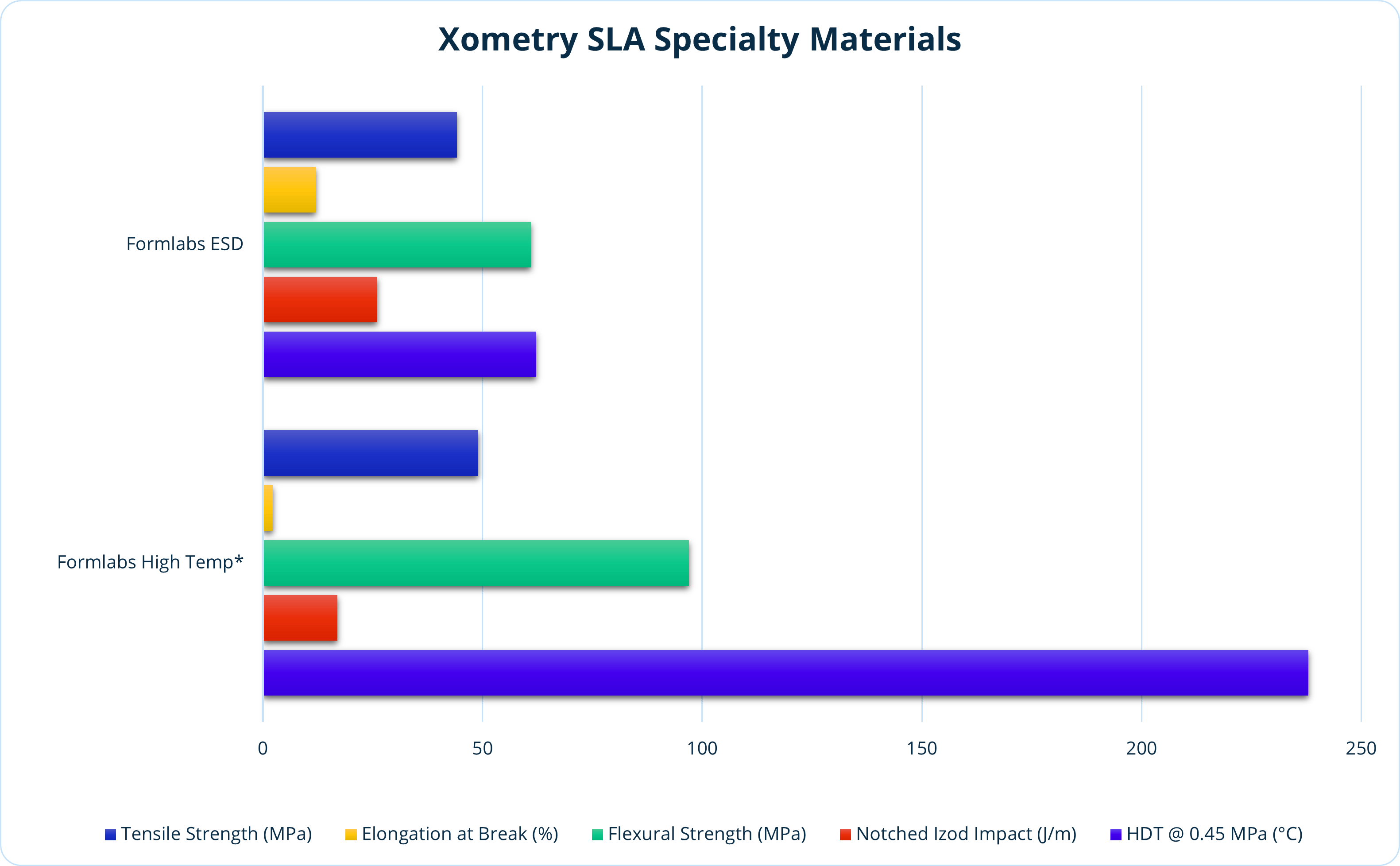
Available Finishes for SLA Printed Parts
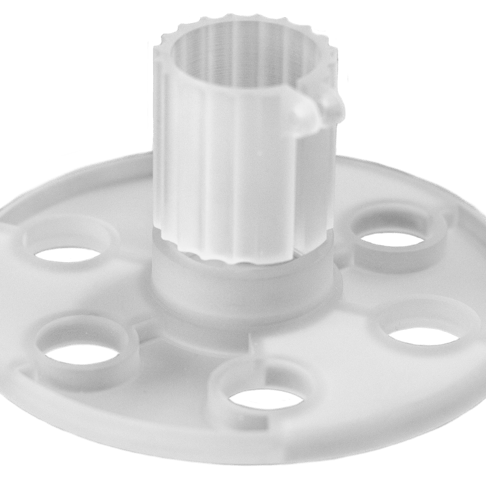
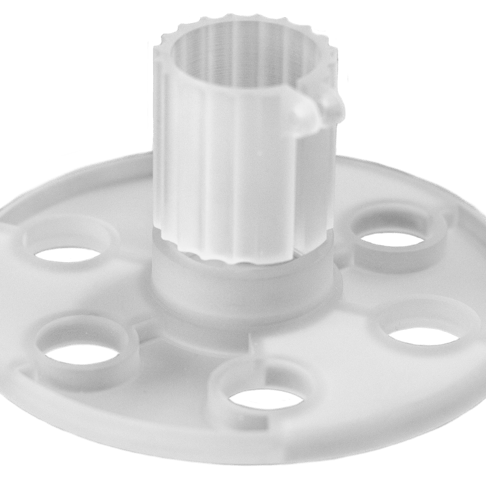
Supported surfaces will be lightly sanded with 220 or 320 grit sandpaper, then media blasted for a uniform matte finish.
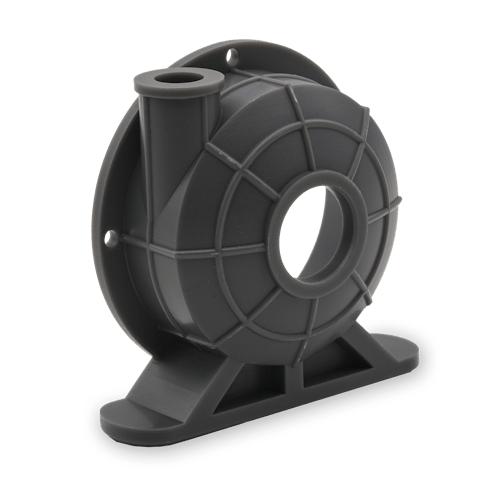
Supported surfaces will be lightly sanded with 220 or 320 grit sandpaper for improved surface quality. Sanding scratches will be visible on supported surfaces.
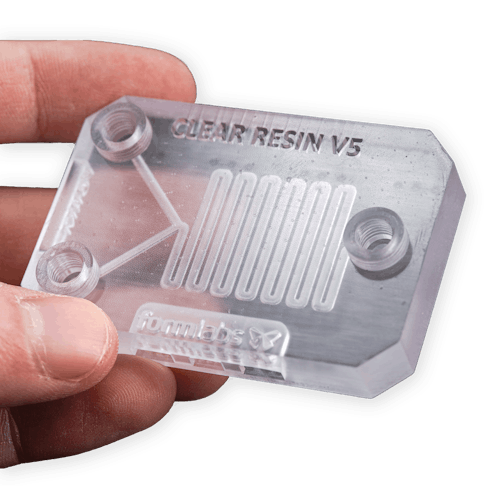
Supported areas may show small grid-like dots or surface blemishes as a result of support removal.
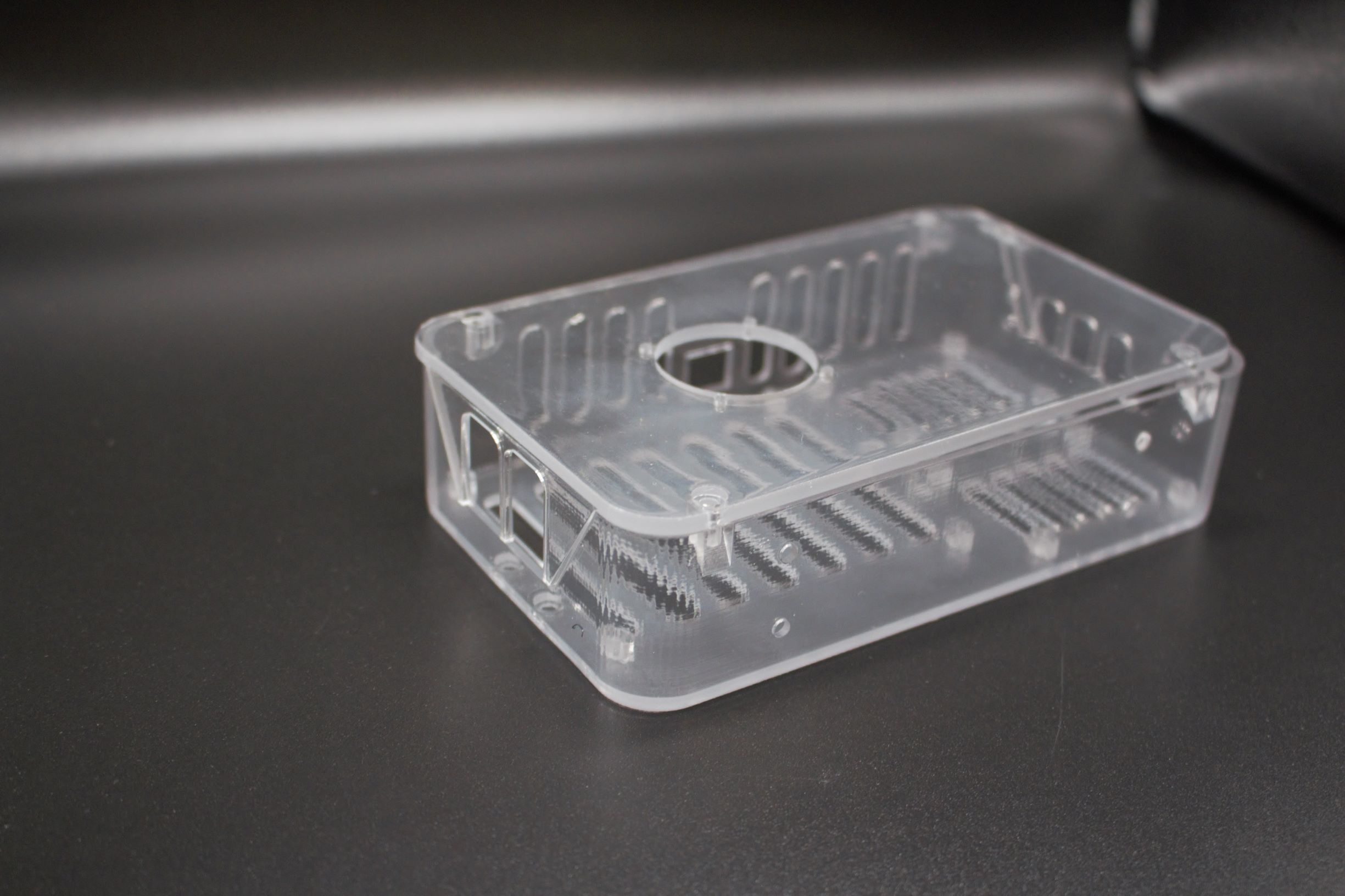
Available for several clear SLA materials. Only supported surfaces are sanded. Parts will still have visible layering. High gloss clear coat is applied to enhance natural clarity.
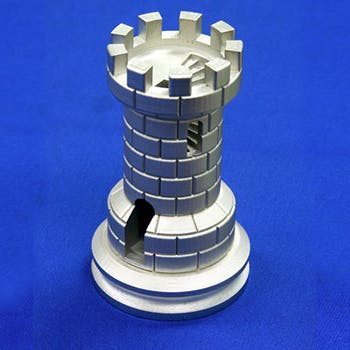
Xometry provides additional SLA finishing options, including but not limited to sanding, polishing, painting, post thermal processing, and plating to meet your needs.
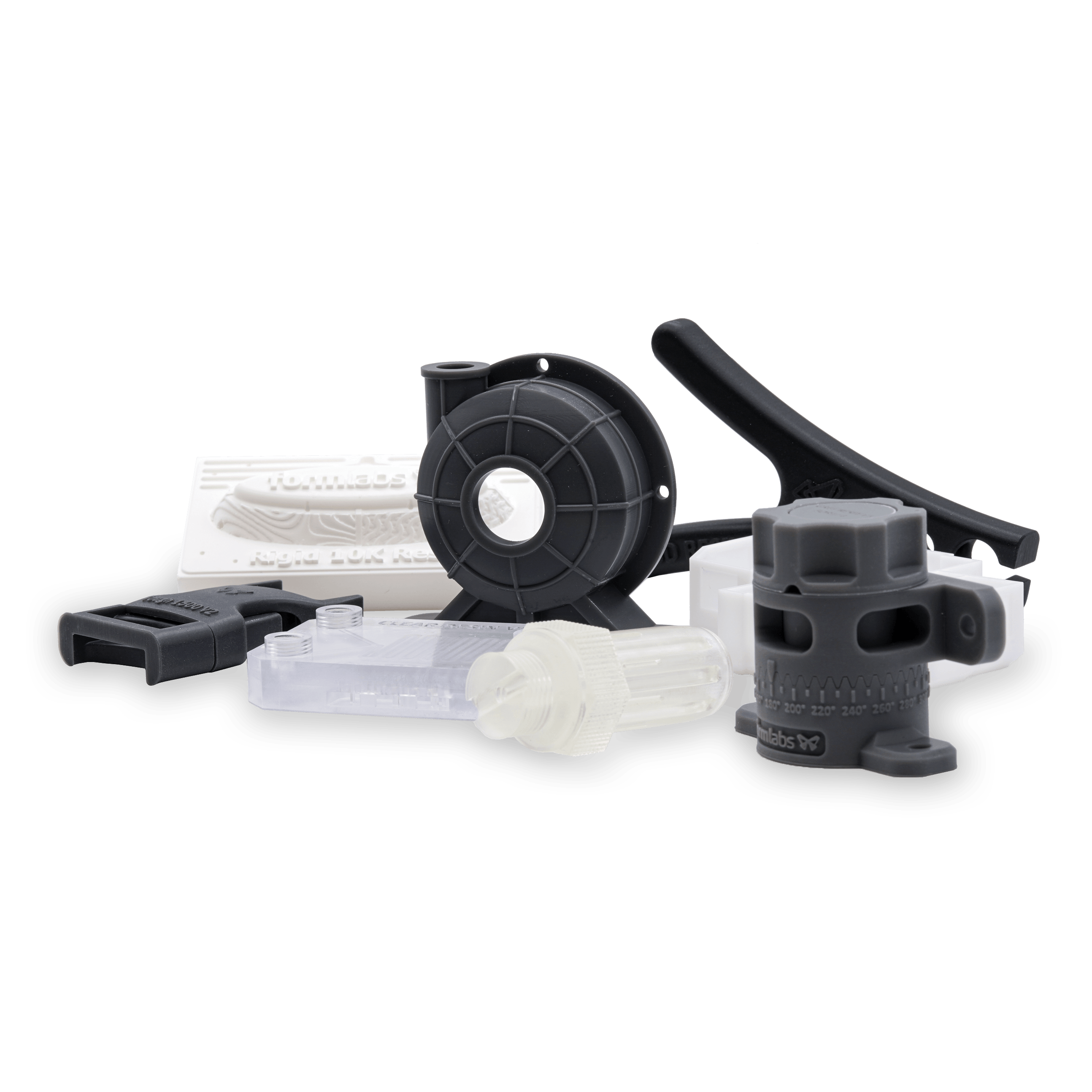
Navigating Stereolithography (SLA) Resins by Applications
Ready to get started on your 3D printing quote?
Free shipping available for domestic 3D printing orders ; learn more!
Applications of Stereolithography (SLA) 3D Printing
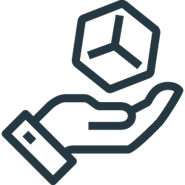
Concept Models
The speed, accuracy, and great surface finish of SLA parts let product developers create physical snapshots of their designs through the iterative process.
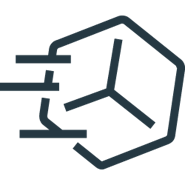
Rapid Prototyping
SLA prototyping is a fully functional prototype, with materials that can simulate polypropylene, polycarbonate, ABS, and rigid composites.
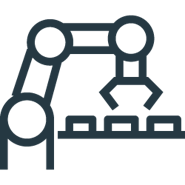
Direct Digital Manufacturing
SLA's high accuracy and consistency make it ideal for building large quantities of discrete or customized parts.
Benefits of SLA 3D Printing
SLA is a go-to choice for 3D-printed models that require accurate features and a smooth surface finish. Xometry's stereolithography 3D printing service offers both standard and high-resolution options for fine-detail parts and can also print larger-sized parts and products, offering a 29-inch build area or larger for select materials. With the ability to produce complex features with good mechanical properties, an SLA 3D print is often used for final fit checks before moving to injection molding services.
In addition, Xometry's manufacturing partner network allows us to offer a larger variety of materials than other 3D printing companies - we offer a wide range of both Accura and Somos brand materials.
- Outstanding surface finish and post processing options
- Tight tolerances and high detail precision
- Complex shapes with a high degree of precision
- High selection of engineered materials
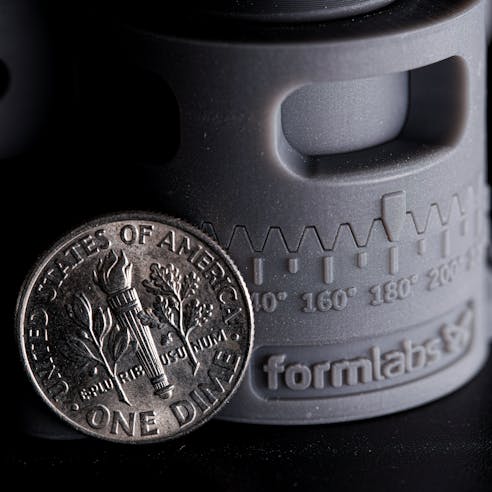
SLA General Tolerances
Description | Standard Resolution | High Resolution |
---|---|---|
Description Build envelope | Standard Resolution Up to 29” x 25” x 21” (13.5" x 7.5" x 7.5" for Formlabs) | High Resolution 10” x 10” x 10” |
Description Layer height | Standard Resolution 0.004" | High Resolution 0.002" |
Description Tolerance, XY Plane | Standard Resolution +/- 0.005” for the first inch is typical, plus +/- 0.002” for every inch thereafter. | High Resolution +/- 0.005” for the first inch is typical, plus +/- 0.002” for every inch thereafter. |
Description Tolerance, Z Plane | Standard Resolution +/- 0.010” for the first inch is typical, plus +/- 0.002” for every inch thereafter. | High Resolution +/- 0.010” for the first inch is typical, plus +/- 0.002” for every inch thereafter. |
Description Minimum linear feature size | Standard Resolution Under 0.030” are at risk and under 0.020” will not build. | High Resolution Under 0.020” are at risk and under 0.010” will not build. |
Description Minimum radial feature size | Standard Resolution 0.035" | High Resolution 0.030" |
The table depicts the general tolerances for industrial-grade stereolithography (SLA) services. Stresses during the build, support strategy, and other geometry considerations may cause deviation in tolerances and flatness. After completing a prototype build, improved tolerances may be possible with a manual quote review and must be approved on a case-by-case basis. General tolerances apply before secondary finishing or post-processing unless otherwise specified. Please check out Xometry's Manufacturing Standards for more information on tolerances per process.
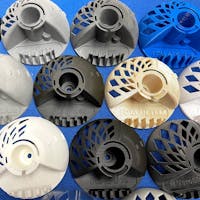
Need to Compare Printing Processes?
Our quick reference guides let you quickly compare different 3D printing processes!
Overview: What is Stereolithography (SLA) 3D printing?
How Stereolithography Works
The stereolithography process is an additive manufacturing process that uses ultraviolet (UV) light on a vat of liquid photopolymer resin to selectively solidify part features, building the part layer by layer. The UV light continues this process through the entire vat of resin, selectively curing and solidifying the resin to match the design of the CAD file. Support structures are created during the pre-build setup process and manually removed after the print is completed. The parts are then washed in a solvent solution to remove uncured resin, and then receive a final post-cure in a UV light oven. Standard SLA uses a laser for resin printing, and other processes use a projector (DLP) or a masked LCD panel (mSLA, such as Formlabs), which are all included under this product line.
Xometry's SLA printing service offers higher resolution printing than many other 3D printing technologies, allowing customers to print parts with fine details and surface finishes. SLA 3D printing is a highly versatile platform for making custom parts in prototype and production settings, often acting as a stand-in for injection-molded parts.
Applications of Stereolithography
With a broad range of suitable materials and a rapid turnaround for even complex net-shapes, SLA technology is an ideal tool for a broad range of manufacturing sectors. It is primarily used in automotive, consumer product, and medical device engineering, enabling the cost-effective generation of intricate parts with various surface finishes and fine detailing. Depending on the manufacturing requirements, parts can be embossed or engraved, with matte, natural, and myriad other textures available. While its primary success has been in rapid, functional prototyping and design assistance for the automotive sector, stereolithography is rapidly being adopted at scale in various mechanical modeling sectors.
Why Choose Xometry for 3D Printing?
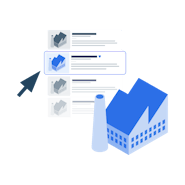
Endless Options
Choose from millions of possible combinations of materials, finishes, tolerances, markings, and certifications for your order.
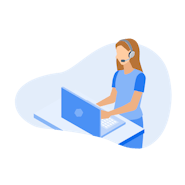
Easy to Use
Get your parts delivered right to your door without the hassle of sourcing, project management, logistics, or shipping.
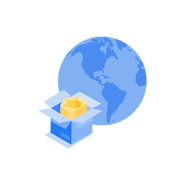
Vetted Network
We are ISO 9001, ISO 13485, IATF 16949, and AS9100D certified. Only the top shops that apply to become Xometry Suppliers pass our qualification process.