Additive manufacturing refers to the process of creating a part by incrementally building it up via the addition of material. This material can be metal, ceramic, plastic, photopolymer, or even food! ISO/ASTM has categorized all the different types of additive manufacturing technologies into seven categories.
This article will describe how each of these types of additive manufacturing processes works, their uses, their advantages, and the differences among them.
1. Binder Jetting
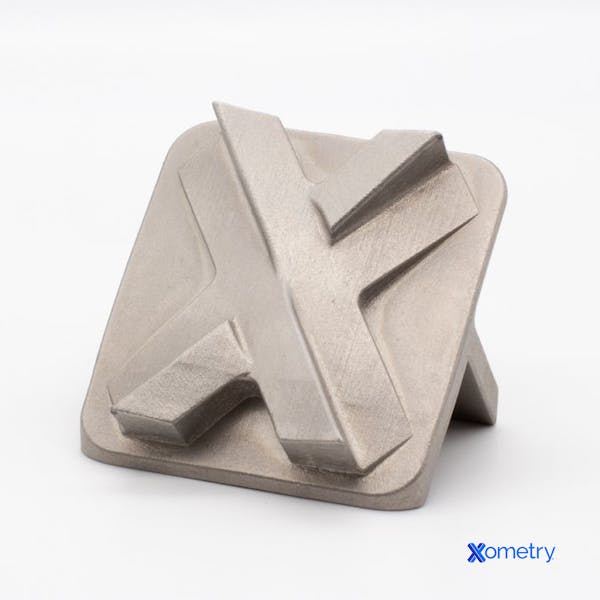
Binder jetting is a powder bed-based additive manufacturing technology. The printer first lays down a thin layer of plastic or metal powder on the build platform. A recoating blade is used to ensure that a precise layer of powder is distributed on the build platform. This is typically done by the recoater blade transferring material from a powder storage bin next to the print area. The material in the storage bin is lifted and the recoater blade sweeps the powder from the storage bin across the build platform at the required layer height. Next, an inkjet head moves over the powder and dispenses a binding agent over the powder in the shape of the part cross-section for the current layer. For full-color plastic parts, the binding agent also contains a colorant to create multiple-color parts.
The print bed then moves down by one layer height. The recoating blade distributes another layer of powder on top of the previous one, and the process continues. When binder jetting metals, the part must be sintered after printing to eliminate porosity and improve the mechanical strength. Alternatively, a low melting temperature metal powder like bronze can be mixed with the main material. When the printed part is heated, the bronze will melt and fill the spaces between the primary metal alloy powder particles.
Table 1 below shows the typical materials, applications, and advantages of binder jetting:
Materials | Applications | Advantages |
---|---|---|
Materials
| Applications
| Advantages
|
2. Powder Bed Fusion
Powder bed fusion (PBF) refers to a range of additive manufacturing technologies that fuse powders using a high-powered focused energy source. The energy source can be a laser (SLM or DMLS) or electron beam (EBM). Both metal and plastic powders can be used with PBF. The process works by first placing a thin layer of powder (often pre-heated) onto the build platform. This is achieved with a recoater blade to ensure layer height consistency. A focused energy beam then melts the powder particles to form the current cross-sectional layer of the part. The build platform then moves down by one layer. Another layer of powder is added and the process repeats.
Higher power energy beams are needed for metals, and an inert atmosphere is required for DMLS and SLM printing. For EBM, the build volume must be kept under a vacuum. PBF machines can print quickly, especially if multiple-beam printers are used. EMB uses only one beam but the beam can be redirected extremely quickly, thereby simulating multi-beam functionality.
Table 2 below shows the typical materials, applications, and advantages of powder bed fusion:
Materials | Applications | Advantages |
---|---|---|
Materials
| Applications Functional metal parts like turbine blades, rocket engine combustion chambers, heat exchangers | Advantages
|
3. Directed Energy Deposition
Directed energy deposition (DED) is an additive material process used exclusively with metals. It is often used to repair existing metal parts. This repair capability is possible because DED can print in five axes of motion, unlike other printing processes, which are limited to three. A DED printer can maneuver around existing parts with complex geometries.
This type of additive manufacturing is not limited to repairs, but can also print brand-new parts. DED works by directing either a powder or a metal wire to the print nozzle. A laser or electron beam then melts the material and fuses it with the base material. Any weldable metal can be made or repaired with DED. As with welding processes, a shielding gas (laser beam) or a vacuum (electron beam) is required for DED printing. The gas will only cover the area that is actively being melted by the beam. Alternatively, the entire build volume can be saturated with an inert gas which requires a sealed airtight build volume.
Table 3 below shows the typical materials, applications, and advantages of DED:
Materials | Applications | Advantages |
---|---|---|
Materials Metals (cobalt-chrome, titanium, Inconel, tantalum, niobium, stainless steels) | Applications
| Advantages
|
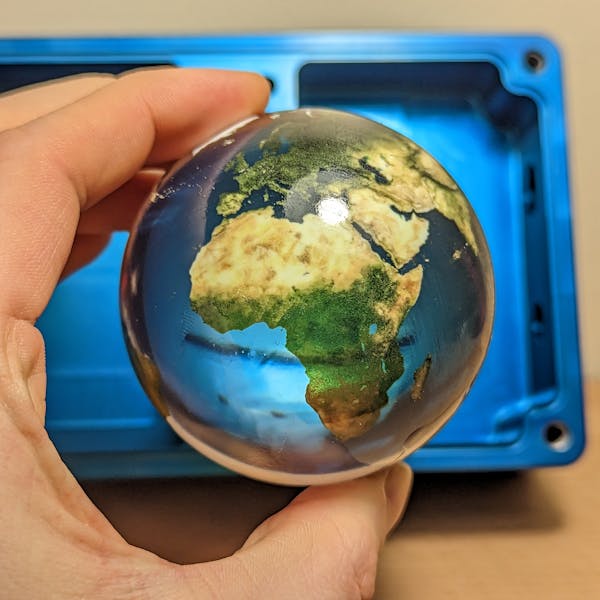
Material jetting makes use of a series of inkjet nozzles to deposit material onto a build platform to create a part. This process requires the use of photopolymers as raw materials. Material jetting works by first depositing a layer of photopolymer onto the build platform. Next, a UV light source moves over the photopolymer to cure it. The build platform then moves down, and the process is repeated.
Since UV-light curing of the printed material is an integral part of this additive manufacturing process, only plastics, many of which are photopolymers, can be printed by material jetting. Support structures are required to print parts by material jetting successfully.
Table 4 below shows the typical materials, applications, and advantages of material jetting:
Materials | Applications | Advantages |
---|---|---|
Materials
| Applications
| Advantages
|
5. Sheet Lamination
Sheet lamination is a unique additive manufacturing technology that builds up parts by laying down a stack of sheets that become the final part, rather than working with bulk powders or liquids. It can be used to make both plastic and metal parts. Sheet lamination produces low-resolution parts, but at a much higher production rate and lower cost than all other additive manufacturing technologies. The process works by piling thin sheet layers on top of each other. These sheets are then fused to the previous layer using a variety of bonding techniques. In some cases, a laser then outlines the part and cuts away unwanted sheet material.
Metal sheets are fused using ultrasonic vibration, whereas plastics are usually bonded with high temperature and pressure. Composites, like aramid panels or fiberglass and paper, are joined using adhesives and pressure. In some cases, near-net shapes are produced. They are then finished using subtractive technologies like CNC machining.
Table 5 below shows the typical materials, applications, and advantages of sheet lamination:
Materials | Applications | Advantages |
---|---|---|
Materials
| Applications
| Advantages
|
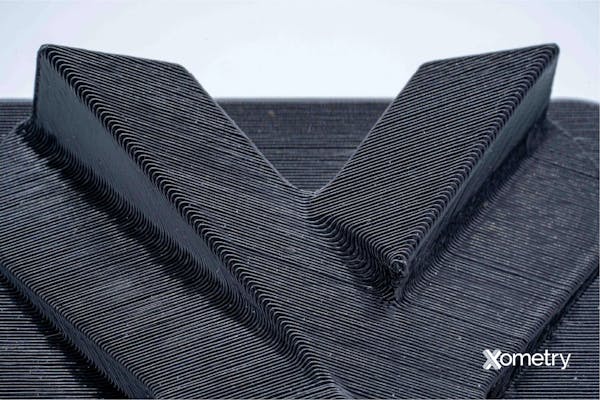
Material extrusion is one of the most well-known types of additive manufacturing, mainly due to its adoption by the consumer market. Material extrusion is often referred to as FDM (Fused Deposition Modeling), or alternatively, FFF (Fused Filament Fabrication). The process works by directing a plastic filament from a supply spool, passing it through a heated chamber, and then out of a print nozzle. As the material exits the nozzle, it is deposited in the form of the current part cross-section on the build platform. Once a layer is complete, the print heads move up by one layer thickness. The process is repeated until the part is complete.
Thermoplastics and filled thermoplastics are the most typical raw materials used with this technology. However, metallic powder/polymer matrix materials can be used to create metal parts. They must be post-processed in a furnace to develop their final mechanical properties.
Table 6 below shows the typical materials, applications, and advantages of material extrusion:
Materials | Applications | Advantages |
---|---|---|
Materials
| Applications
| Advantages
|
7. VAT Photopolymerization
VAT photopolymerization is an additive manufacturing technology used to create parts using photopolymers. The two main branches of this technology are SLA (Stereolithography) and DLP (Digital Light Processing). Both technologies use a light source to cure one layer of dispensed photopolymer at a time in the shape of the current cross-sectional layer of the part. The build platform then lowers until it is just under the surface of the liquid photopolymer. The part cross-section is then either projected onto the build platform or the cross-section is traced out with a laser which simultaneously solidifies the polymer. As the build platform moves up and the next layer is polymerized onto the previous one until the part is complete, it appears as if the build platform is pulling the part out of the vat of liquid.
Table 7 below shows the typical materials, applications, and advantages of VAT photopolymerization:
Materials | Applications | Advantages |
---|---|---|
Materials
| Applications
| Advantages
|
What Is Additive Manufacturing?
Additive manufacturing refers to the additive process of creating a part by building it up one layer at a time. This is in contrast to subtractive manufacturing, which starts with a solid block of material and removes any excess to create a part. CNC machining is an example of subtractive manufacturing.
Common FAQs About Types of Additive Manufacturing
What is the Most Frequently Used Type of Additive Manufacturing?
The most frequently used types of additive manufacturing are: material extrusion (FDM/ FFF), sheet lamination, VAT polymerization, and powder bed fusion (PBF). It must be noted that the degree of adoption of each additive manufacturing technology differs depending on the industry it is used in. For example, the aerospace industry makes heavy use of DED and powder bed fusion.
What Organization Categorizes Additive Manufacturing Processes?
ASTM International and ISO are jointly responsible for the categorization of additive manufacturing processes. The seven categories described in this article were created by ASTM and ISO.
How Are Additive Manufacturing Processes Classified?
The specific standard used to classify additive manufacturing processes is ISO/ASTM 59200 - Additive Manufacturing - General Principles - Terminology. This standard provides definitions of additive manufacturing processes.
Is 3D Printing an Example of Additive Manufacturing?
Yes, 3D printing is an example of additive manufacturing. It is the most commonly recognized example of additive manufacturing.
Summary
This article reviewed 7 different types of additive manufacturing processes and described how they work, their advantages, and their disadvantages. To learn more about the different additive manufacturing types and how each may be best suited to your specific application, contact a Xometry expert today.
Xometry provides a wide range of manufacturing capabilities, including 3D printing and value-added services for all of your prototyping and production needs. Visit our website to learn more or to request a free, no-obligation quote.
Disclaimer
The content appearing on this webpage is for informational purposes only. Xometry makes no representation or warranty of any kind, be it expressed or implied, as to the accuracy, completeness, or validity of the information. Any performance parameters, geometric tolerances, specific design features, quality and types of materials, or processes should not be inferred to represent what will be delivered by third-party suppliers or manufacturers through Xometry’s network. Buyers seeking quotes for parts are responsible for defining the specific requirements for those parts. Please refer to our terms and conditions for more information.
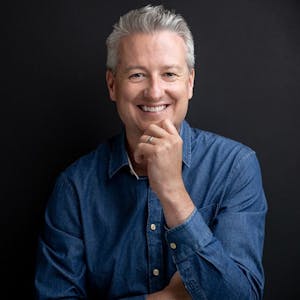