Polypropylene (PP) and HDPE (High-Density Polyethylene) are both commodity thermoplastics. Polyethylene, the basic building block of HDPE, is the highest production volume of plastic in the world, and polypropylene has the second-highest production volume. Polypropylene has excellent fatigue resistance, but it is also used for many single-use plastic applications, such as food packaging. Polypropylene can be manufactured using blow molding, injection molding, and extrusion.
HDPE has an excellent strength-to-weight ratio as well as good chemical resistance. HDPE is widely used for water tanks, food packaging, and piping. HDPE can be manufactured using extrusion, injection molding, and rotomolding. Both HDPE and PP are considered food-safe. This article will further compare polypropylene vs HDPE in terms of its applications, uses, physical properties, sustainability, and costs.
What is Polypropylene?
Polypropylene (PP) is a thermoplastic with a semi-crystalline structure. It is produced from petroleum products like natural gas through a polymerization process. Propylene can be polymerized into polypropylene by making use of chain growth polymerization. Once polymerized, the polypropylene is extruded into long filaments which are then processed via a pelletizer, which cuts the filaments into pellets to be processed using standard thermal processing techniques like injection molding. Polypropylene is typically produced in two different forms: a homopolymer and a copolymer. Homopolymeric polypropylene is the most common grade, whereas copolymeric polypropylene is less common.
Polypropylene is processed using injection molding, blow molding, extrusion, and CNC machining, which are all processes we can do here at Xometry. You can find it being used for food containers, beverage bottles, fabrics, and chemical process tanks. Polypropylene has excellent chemical resistance, is inexpensive, and has excellent fatigue strength. For more information, see our guide on All About Polypropylene.
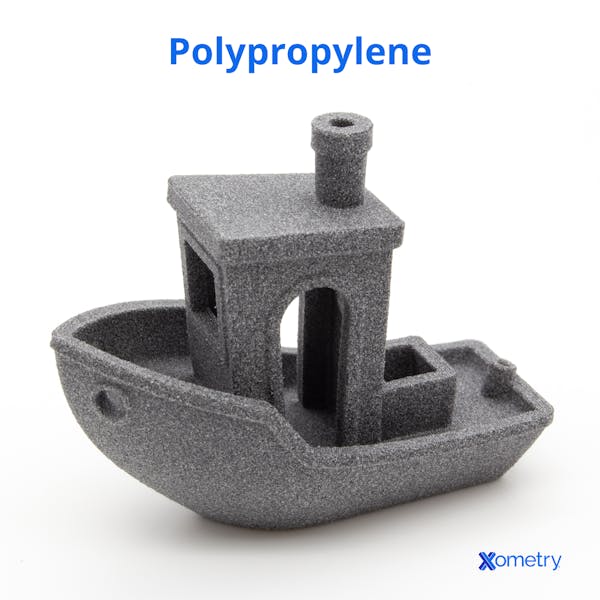
What is HDPE?
HDPE (High-Density Polyethylene), less commonly known as PE-HD (Polyethylene High-Density), is a thermoplastic homopolymer with limited to no branching from the main molecular chain. HDPE is produced from petroleum products like natural gas through a polymerization process. Ethylene can be polymerized into polyethylene only in the presence of a suitable catalyst like metallocene or Ziegler-Natta-type catalysts. Once polymerized, the HDPE is extruded into long filaments. These filaments are then processed through a pelletizer, which cuts the filaments into pellets to be processed using standard thermal processing techniques like rotomolding or extrusion.
HDPE forms part of the PE (polyethylene) group of plastics, which is made up of LDPE (Low-Density Polyethylene), LLDPE (Linear Low-Density Polyethylene), and UHMWPE (Ultra-High Molecular Weight Polyethylene). HDPE has an excellent strength-to-weight ratio. It is often joined via plastic welding techniques, but can also be extruded, injection molded, rotomolded, and CNC machined. HDPE is often used for water tanks, piping, shopping bags, and food packaging. For more information, see our guide on What is HDPE Plastic.
HDPE can be identified by the triangular recycling symbol with the number 2 enclosed as indicated in middle bottle below:
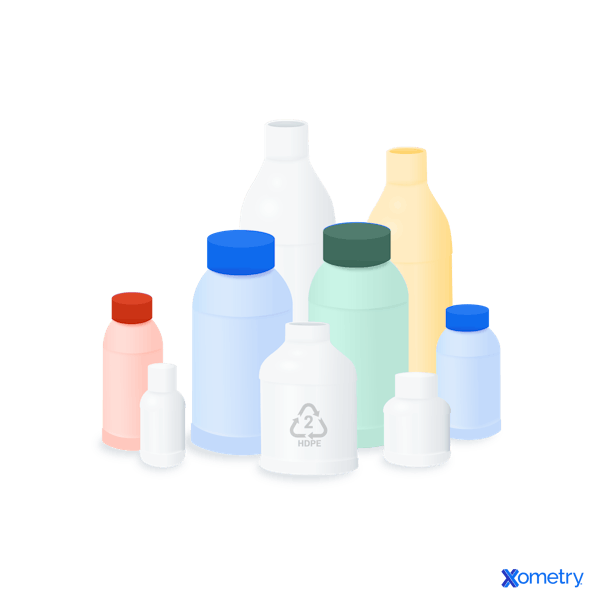
Polypropylene vs. HDPE: Applications and Uses
Polypropylene and HDPE are popular materials. The popularity of these two plastics is due to their low cost, ease of use, and food safety.
HDPE is highly flexible and has an excellent strength-to-weight ratio. Some typical applications are listed below:
- Milk cartons, squeeze bottles, bottle caps, and beverage bottles
- Pipes and fittings, chemical storage tanks, and water tanks
- Shopping bags, toys, and playground equipment
- Fibers and textiles
Polypropylene has excellent chemical resistance and can be exposed to boiling water without degrading. Some typical applications are listed below:
- Beverage bottles, food containers, and bottle caps with living hinges
- Syringes, medicine bottles, and vials
- Washing machine and dishwasher components
- Chemical storage tanks, water piping, and packaging for industrial equipment
- Dashboards and fenders
- Furniture, toys, and carpets
Polypropylene and HDPE have overlapping uses. However, HDPE is generally more flexible, while polypropylene has better resistance to elevated temperatures.
Polypropylene vs. HDPE: Physical Properties
Some key mechanical, thermal, and chemical properties of HDPE and polypropylene are listed in Table 1 below:
Properties | Polypropylene | HDPE |
---|---|---|
Properties Density (g/cm3) | Polypropylene 0.9 | HDPE 0.96 |
Properties Ultimate Tensile Strength (MPa) | Polypropylene 23.4 | HDPE 31.7 |
Properties Izod Impact (Notched) (J/cm) | Polypropylene 4.27 | HDPE 0.694 |
Properties Hardness (Shore D) | Polypropylene 72 | HDPE 70 |
Properties Max Service Temperature (Air) (°C) | Polypropylene 82.2 | HDPE 71.1 |
Properties Melting Temperature (°C) | Polypropylene 160 - 168 | HDPE 180 - 205 |
Properties UV Resistance | Polypropylene Poor | HDPE Poor |
Properties Chemical/ Corrosion Resistance | Polypropylene Resistant to diluted and concentrated acids like nitric acid, as well as alcohols and bases | HDPE Resistant to diluted and concentrated acids like hydrochloric acid, as well as some reducing agents and oxidants. |
Properties Water Absorption (ASTM D570) (% by weight) | Polypropylene 0.02 | HDPE 0.1 |
Table Credit: matweb.com
Both HDPE and polypropylene have poor UV (ultraviolet) light resistance. However, UV-stabilized versions of both are available to provide improved UV resistance.
Polypropylene vs. HDPE: Recyclability and Sustainability
HDPE and polypropylene are both theoretically recyclable due to their thermoplastic nature. Polypropylene can be identified with the number 5 stamped on objects made from it, and HDPE with the number 2. Polypropylene can be recycled up to four times, whereas HDPE can be recycled up to ten times. Despite this recyclability, the vast majority of plastics are not recycled, and simply end up in landfills or in the ocean.
HDPE and PP are both produced from non-renewable crude oil and are therefore not regarded as sustainable products. In addition to this, both of these materials are widely used in single-use applications.
Polypropylene vs. HDPE: Cost
HDPE can be bought at $0.98-1.56 per kilogram. Polypropylene, on the other hand, can be bought at $1.00-3.00 per kilogram.
Alternative Materials to Polypropylene and HDPE
Alternatives for polypropylene and HDPE include PET (polyethylene terephthalate) and PVC (polyvinyl chloride). PET is widely used for food containers and can also be used for living hinge designs. PVC has good thermal and chemical resistance properties. It can be used for both rigid applications, like piping, as well as applications requiring flexibility, such as tubes.
Summary
This article presented polypropylene and HDPE, explained each of them, and discussed their various differences and applications. To learn more about polypropylene and HDPE, contact a Xometry representative.
Xometry provides a wide range of manufacturing capabilities and other value-added services for all of your prototyping and production needs. Visit our website to learn more or to request a free, no-obligation quote.
Disclaimer
The content appearing on this webpage is for informational purposes only. Xometry makes no representation or warranty of any kind, be it expressed or implied, as to the accuracy, completeness, or validity of the information. Any performance parameters, geometric tolerances, specific design features, quality and types of materials, or processes should not be inferred to represent what will be delivered by third-party suppliers or manufacturers through Xometry’s network. Buyers seeking quotes for parts are responsible for defining the specific requirements for those parts. Please refer to our terms and conditions for more information.
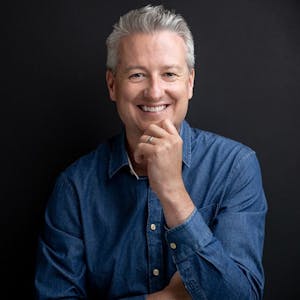