The development of 3D printing, also known as additive manufacturing, has been shaped by decades of scientific research, technological innovation, patent activity, and commercialization. These efforts have culminated in the widespread adoption of a technology that enables the production of low-cost, high-precision parts with strong mechanical properties and rapid turnaround times. While the core objective across 3D printing platforms remains consistent—efficient production of high-quality components—the range of available processes and materials continues to expand rapidly. Innovations in hardware, software, and materials science are driving the development of more complex and specialized solutions tailored to diverse industries.
This article will discuss what 3D printing is, its fundamental principles, and how ongoing innovation is transforming it into an increasingly versatile and sophisticated manufacturing solution.
What Is the Historical Origin of 3D Printing?
The origins of 3D printing trace back to the early 1980s, during a period of rapid experimentation in materials and digital manufacturing. In 1983, Chuck Hull, co-founder of 3D Systems, developed and patented stereolithography (SLA)—the first commercially viable additive manufacturing technology. SLA works by using ultraviolet (UV) light to selectively cure photopolymer resin, layer by layer, to build three-dimensional objects with high precision.
This foundational innovation marked the beginning of the modern 3D printing era and laid the groundwork for other key technologies, including selective laser sintering (SLS) and fused deposition modeling (FDM®). These complementary methods expanded the range of printable materials and applications, ultimately enabling 3D printing to gain traction in industries such as aerospace, automotive, healthcare, and consumer goods.
When Did 3D Printing Start?
3D printing began in the early 1980s when Chuck Hull developed the first stereolithography (SLA) machine, known as the SLA-1 (also referred to as STL-1). This pioneering system used photopolymerization, a process in which ultraviolet (UV) light selectively cures layers of liquid photopolymer resin to form solid, three-dimensional structures.
Hull filed a patent for this innovation in 1984, and it was officially granted in 1986. That same year, he co-founded 3D Systems, which began commercializing SLA technology, marking the official entry of additive manufacturing into the industrial market. This breakthrough not only introduced a new method of rapid prototyping but also laid the foundation for further developments in 3D printing technologies across multiple sectors.
How Did 3D Printing Start?
The commercialization of 3D printing began in 1988 when 3D Systems released the first stereolithography (SLA) machine to the market. This innovation had a transformative impact on product development, enabling designers and engineers to create physical prototypes with unprecedented speed and geometric complexity. It introduced a new era of rapid prototyping, making it easier to test, iterate, and refine designs.
Shortly after, Stratasys introduced Fused Deposition Modeling (FDM®), which offered a more cost-effective alternative. Although FDM produced lower-resolution parts compared to SLA, it utilized thermoplastics with properties closer to those of end-use materials, making it attractive for functional prototyping and preliminary product validation.
These developments catalyzed the rise of early service bureaus and in-house prototyping labs, which revolutionized design workflows by shortening development cycles and enabling faster design verification. As a result, 3D printing quickly became an essential tool in engineering, product design, and manufacturing strategy.
When Was the First 3D Printer Introduced?
The adoption of 3D printing was an organic process that initially occurred over several years, as conservative thinking gave way to a more rapid, testable process that facilitated exploration. Combined with the concurrent advent of 3D CAD-CAM systems, product design became a more flexible and less artistic field.
The first SLA machines, introduced in 1989, heralded a revolution, but that change was slow-moving, and it is still in motion.
Who Invented the First 3D Printer?
The first 3D printer was invented by Chuck Hull and was awarded a patent in 1986. Around the same time, Scott Crump developed Fused Deposition Modeling (FDM®) in 1988, which began commercializing FDM technology shortly after SLA. Together, these two innovations, SLA and FDM, laid the foundation for the modern 3D printing ecosystem.
What Are the Significant Events That Happened During the 1980s in 3D Printing History?
During the 1980s, the following seminal events shaped the origin and early history of 3D printing:
- In 1983, Chuck Hull first developed the concept that would become SLA, the earliest 3D printing technology, which was commercialized by 3D Systems in 1988.
- Carl Deckard and Joseph Beaman developed selective laser sintering (SLS) at the University of Texas in 1986, bringing another foundational technology in additive manufacturing to early-stage development.
- Scott Crump patented fused deposition modeling (FDM®) in 1989, laying the groundwork for the commercialization of FDM®-based 3D printers by Stratasys.
These milestones mark the birth of 3D printing and set the stage for its ongoing and rapid evolution in subsequent decades.
What Are the Significant Events That Happened During the 1990s in 3D Printing History?
During the 1990s, the following pivotal events contributed to the accelerating evolution of 3D printing:
- Commercialization of SLA and SLS technologies by companies like 3D Systems and DTM Corporation led to increased adoption across many higher-value and higher-tooling-cost design sectors.
- The introduction of desktop 3D printers, starting with FDM technology by Stratasys, made 3D printing more accessible to businesses, as well as to hobbyists and enthusiasts.
- Expansion of applications into all industries, driven by advancements in materials, printing techniques, increased agency competition, falling costs to users, and improved post-processing methods.
- The development of rapid prototyping and rapid tooling applications streamlines product-development cycles and manufacturing processes.
These milestones cemented 3D printing as the transformative technology it was rapidly becoming, with widespread and near-universal sector application.
What Are the Significant Events That Happened During the 2000s in 3D Printing History?
During the 2000s, the following significant developments and technological events propelled the advancement of 3D printing:
- The development of new 3D printing technologies, including direct metal laser sintering (DMLS) and electron beam melting (EBM), enabled the production of full-density, finished-size metal parts with complex geometries.
- The introduction of low-cost desktop 3D printers by companies like MakerBot, Ultimaker, and Prusa Research disseminated access to 3D printing technology down to the comfortable reach of individuals and small businesses.
- Expansion of applications into healthcare, with the use of 3D printing for medical implants, prostheses, early bioprinting, and patient-specific surgical guides.
- The continued refinement and expansion of materials, as well as increased diversification of printing processes and software, enhanced the capabilities and precision of 3D printing technology.
The most significant effect of the developments of this period was the demystification of additive manufacturing and the increasing acceptance of at least the idea that higher-level processes have the potential for manufacturing finished products on a small to medium scale.
What Are the Significant Events That Happened During the 2010s in 3D Printing History?
During the 2010s, the pace of development increased yet further, shaping a variety of trajectories in the increasingly diverse capabilities that together represent 3D printing. Some of these are:
- Advances in bioprinting technology enabled the printing of collagen frameworks to be populated with growth by living tissues during this period. Increased experimentation with live-cell printing for medical research and potential transplantation began at this time as techniques developed.
- Growth of 3D printing in aerospace and automotive industries for manufacturing end-use parts, such as aircraft/rocket combustion chamber parts and automotive prototypes, restoration parts, and even exploration towards “mass” production.
- Penetration of 3D printing into construction, with the development of large-scale additive manufacturing techniques for building structures by liquid extrusion of cement-type pastes.
- Introduction of metal 3D printing systems capable of producing high-resolution, full-density metal parts for aerospace, automotive, and medical applications. Two basic approaches were developed — polymer-bonded parts that are post-printing sintered, and directly applied local melting for final off-machine finished components.
- Adoption of 3D printing in education, maker spaces, and DIY communities fosters innovation and creativity.
What Are the Significant Events That Happened During the 2020s in 3D Printing History?
Significant events in 3D printing during the 2020s include:
- 3D printing played a well-publicized role in producing personal protective equipment (PPE), ventilator experiments, and nasopharyngeal swabs. Much of this was publicity-driven and not suitable for real use, but the profile effects on the sector were profound.
- Increasing focus on eco-friendly materials and processes, as well as recycling and circular economy initiatives. This includes increasing the use of recycled and biologically sourced filaments for FFF/FDM, the increased use of water-soluble and biologically inert support materials, and efforts to reduce waste and toxicity in various processes.
- NASA, the US military, and private companies began to utilize additive manufacturing for prototyping and manufacturing components for spacecraft and habitats.
- Progress in printing complex tissues and organs for medical applications and regenerative medicine continued, though this remains generally experimental.
- Research into atomic-scale additive manufacturing processes is in its very early stages, small-scale, but rapidly developing.
- Increasing use of 3D printing for mass customization, spare parts production, and tooling across various industries.
The pace of release of new commercial executions of existing technologies, entirely new processes, and diversification of materials towards “real” rather than prototype properties and end-use part characteristics is still accelerating.
When Did 3D Printing in the Food Industry Start?
3D printing in the food industry started gaining momentum in experimentation in the early 2010s. While the concept of 3D printing food has been explored for several years, notable developments began around 2011–2012 when researchers and chefs started experimenting with 3D printers modified to extrude food materials. The basic concept differs only in automation from the complex, 3D hand-decorating of cakes and confectionery, which already has a long history.
One of the early pioneers in the additive manufacture of food was Barcelona-based Natural Machines, which introduced the Foodini 3D food printer in 2014. Subsequently, various companies, research institutions, and culinary professionals have been exploring the potential of 3D printing technology to create customized, visually appealing food items, ranging from confectionery and chocolate to pasta, meat substitutes, and even entire meals.
To learn more, see our full guide on 3D Printing in Food.
When Did 3D Printing of Prosthetics Start?
3D printing of prosthetics began to gain traction beyond the conceptual and visualization levels in the early to mid-2010s. The concept had been explored in research settings before that, with few long-term functioning outcomes.
One of the significant early developments occurred in 2011 when a South African carpenter, Richard Van As, collaborated with an American prop maker, Ivan Owen, to create a 3D-printed prosthetic hand for a young boy named Liam. Their design, known as the "Robohand," was open-source and widely shared online, sparking interest in using 3D printing technology to create affordable and customizable prosthetic devices. Since then, 3D printing has been increasingly utilized in the prosthetics field for its ability to produce personalized, lightweight, and cost-effective prosthetic limbs and components. Improving materials, the wider dispersal of capabilities, and a deeper understanding of the approach's implications are driving constant innovation in this space.
To learn more, see our full guide on 3D Printing in Prosthetics.
When Did 3D Bioprinting Start?
3D bioprinting, the process of creating three-dimensional biological structures using living cells, emerged as a research field in the early 2000s. One of the earliest demonstrations of 3D bioprinting occurred in 2003 when Thomas Boland, a researcher at Clemson University, developed a technique to print living cells onto biocompatible scaffolds using an inkjet-based bioprinter. This marked a significant milestone in the development of 3D bioprinting technology.
Subsequent advancements in materials science, bioengineering, and additive manufacturing techniques have led to the development of more sophisticated 3D bioprinting systems capable of printing complex tissues and organ-like structures. Today, 3D bioprinting holds immense promise for applications in tissue engineering, regenerative medicine, drug discovery, and personalized medicine.
What Is the Current Status of 3D Printing?
3D printing has evolved from a prototyping tool into a mature, industrial-grade manufacturing technology spanning a broad spectrum of methods and materials. Additive manufacturing now supports applications across a range of scales—from microscale components in biomedical engineering to large-scale architectural and aerospace structures. Its reach extends to industries such as automotive, aerospace, defense, consumer goods, healthcare, energy, and even food and bioprinting.
Today, 3D printing encompasses a diverse ecosystem of specialized technologies, including polymer extrusion, resin photopolymerization, powder bed fusion, binder jetting, and material jetting. These methods are tailored to optimize for speed, material properties, resolution, and cost-efficiency, depending on the application. The field continues to diversify and expand, with additive processes becoming integrated into production lines for both high-volume parts and highly customized components. Innovations in materials science, software, process automation, and hybrid manufacturing are accelerating this shift, driving 3D printing toward a central role in digital manufacturing strategies worldwide.
As core technologies advance, additive manufacturing is evolving beyond its roots in prototyping to become a strategic asset in enhancing supply chain resilience, facilitating lightweight, on-demand production, and promoting sustainable manufacturing.
What Are the Significant Developments in 3D Printing Today?
Several significant near-term and forward-looking developments are shaping the 3D printing landscape over the next period. Examples include:
- Researchers are making significant strides in 3D bioprinting, with advancements in printing complex tissues and organ-like structures for regenerative medicine, drug testing, and personalized healthcare. These hold out the potential for built replacement organs to become commonplace.
- There is increasing investment in large-format 3D printing for the construction, aerospace, and automotive sectors. Novel techniques and materials—including polymer-bound regolith for extraterrestrial construction—are enabling the printing of building components, airframe sections, and structural vehicle parts. This supports in-situ resource utilization (ISRU) concepts for applications such as moon-based construction using lunar soil.
- The 3D printing industry is focusing on sustainability, with efforts to develop more eco-friendly materials, reduce waste, and implement recycling programs. Companies are exploring (or already marketing) bio-origin, biodegradable, and recycled materials that minimize environmental impact.
- 3D printing is becoming a core component of digital manufacturing ecosystems, enabling mass customization, on-demand production, and distributed manufacturing. Advances in automation, real-time process monitoring, digital design software, and AI-driven optimization are increasing throughput, reducing cost, and embedding additive manufacturing into Industry 4.0 environments.
- Additive manufacturing is transforming personalized medicine, from patient-specific implants and prosthetics to biocompatible surgical guides and anatomical models. Progress in medical-grade materials and biofabrication techniques is driving improvements in surgical outcomes, patient recovery, and healthcare efficiency.
These developments reflect the ongoing evolution and diversification of 3D printing technologies across a wide spectrum of technologies and approaches, with significant implications in all market sectors. As the core technologies continue to advance and diversify, 3D printing is poised to unlock new possibilities and reshape the future of manufacturing and beyond.
Did the Development of 3D Printing Technology Take Place in the Latter Half of the 20th Century?
The dream of additive manufacturing is older than the technology, but the reality of converting a digital file into a real, physical, printed part only became tentatively realized in the last years of the 20th century.
What Are the Other Things I Should Know About 3D Printing?
The vast and expanding range of technologies under 3D printing is astonishing so far. AI and machine learning algorithms are being integrated into 3D printing processes to optimize design, improve printing speed, and enhance material properties.
Researchers are approaching the ability to bio-print complex human tissues and organs using living cells derived from the patient. This has the potential to revolutionize regenerative medicine and organ replacement. 3D printing enables the customization of medical devices such as implants, prosthetics, and surgical tools to match individual patient anatomy. This reduces surgery times, improves treatment outcomes, and reduces recovery times.
Combining 3D printing with nanotechnology enables the creation of intricate structures at the nanoscale, leading to advancements in materials science, electronics, and drug delivery systems. This is approaching atomic scale construction, at the leading edge of research.
Furthermore, 3D printing technologies are being adapted for use in space. This enables the manufacture of tools, spare parts, and even habitats on demand during long-duration space missions. Advancements in multi-material 3D printing enable the simultaneous deposition of a range of materials. This enables the creation of complex structures with customizable properties built from multi-functional parts.
To learn more, see our full guide on How 3D Printers Work.
Summary
This article introduces the history of 3D printing, explains how it works, and highlights key developments over time. 3D printing has evolved into a vital technology utilized in numerous industries, providing innovative approaches to design and manufacture products.
Xometry provides a wide range of manufacturing capabilities, including 3D printing and other value-added services for all of your prototyping and production needs. Visit our website to learn more or to request a free, no-obligation 3D printing quote.
Copyright and Trademark Notice
- FDM® is a registered trademark of Stratasys Inc.
Disclaimer
The content appearing on this webpage is for informational purposes only. Xometry makes no representation or warranty of any kind, be it expressed or implied, as to the accuracy, completeness, or validity of the information. Any performance parameters, geometric tolerances, specific design features, quality and types of materials, or processes should not be inferred to represent what will be delivered by third-party suppliers or manufacturers through Xometry’s network. Buyers seeking quotes for parts are responsible for defining the specific requirements for those parts. Please refer to our terms and conditions for more information.
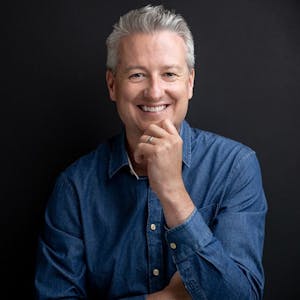