All About Carbon Fiber
All the ins and outs of this low-weight high-strength manufacturing material.
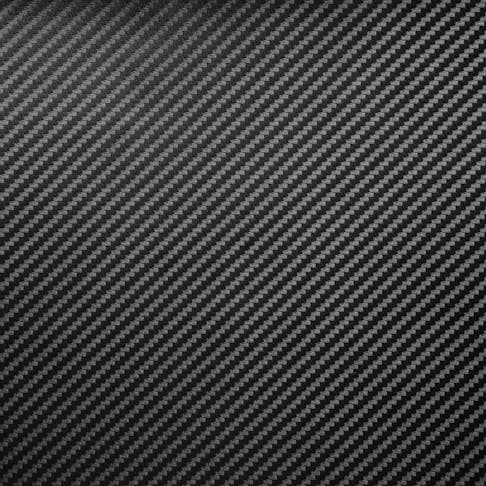
Carbon fiber, a.k.a. graphite fiber or carbon graphite, has become a firm favorite in several sectors, and for good reason. But we won’t give it all away in the intro: read on to find out what this material is, its different types, and what it’s used for.
What is Carbon Fiber?
Carbon fiber is a fabric mat made of woven fibers and is classed as both a composite and fiber-reinforced plastic. It’s 90% polyacrylonitrile (the carbon precursor) and 10% other precursors, like pitch or cellulose. This material is made by carbonization, oxidation, or graphitization. It’s first cut into the required shape, impregnated with resin, then processed in one of the aforementioned methods. When cured, the result is a lightweight and incredibly strong material with an impressive strength-to-weight ratio.
This type of fiber’s high heat tolerance was what inspired Sir Joseph Wilson Swan to use it for an incandescent lightbulb in 1860. Back then, carbon fiber filaments weren’t as strong as they are now, so when tungsten came onto the scene, it pretty much took over in the lightbulb-making department. More than 50 years went by without carbon fiber being really used for anything, but a stronger version was brought out in the 1960s, and Rolls-Royce snapped it up for its jet engines—despite the brittleness thing.
The carbon fiber that’s used in manufacturing today has a tensile strength of around 4,000 MPa and a high modulus of 400 GPa, making it useful for a whole host of things (not just bulbs). It’s resistant to creep, fatigue, chemicals, and corrosion, as well as nonflammable and nontoxic. With the right treatment, it can be electrically conductive.
This material is infamously expensive. It’s both lighter and stronger than steel, but its high cost puts manufacturers off from using it unless absolutely necessary (kind of like that pricey fragrance you’re saving for special occasions). But now the price of carbon fiber has gone down, and its usage up! Carbon fiber’s days of waiting for high-profile tasks are over; it’s now made into tools and fixings, springs and wires, and can even be used to reinforce tires. You can see a part made from this material in the image below.

Wing mirror made of carbon fiber.
Image Credit: Shutterstock.com/Composite_Carbonman
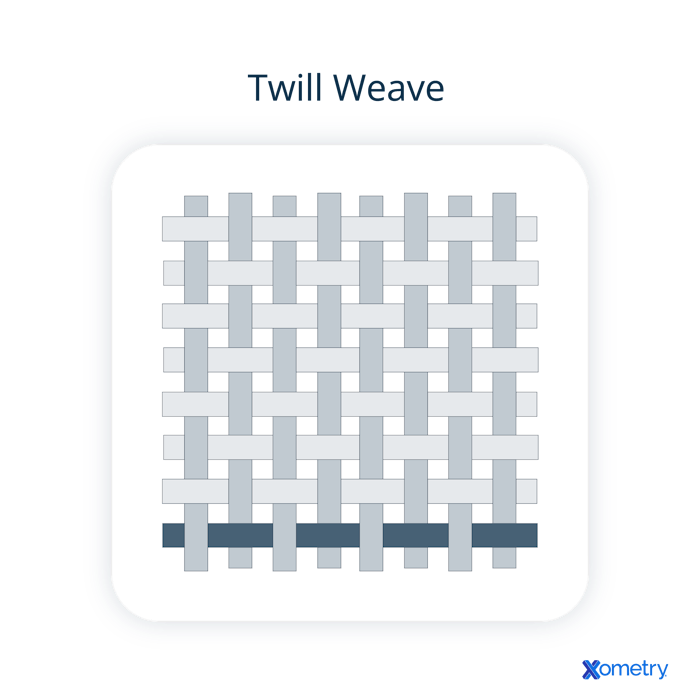
Twill weave
Satin: Smooth and glossy, ideal for draping

Satin weave
Basket: A flat, two-over/two-under pattern with more thickness and stiffness, but less flexibility.
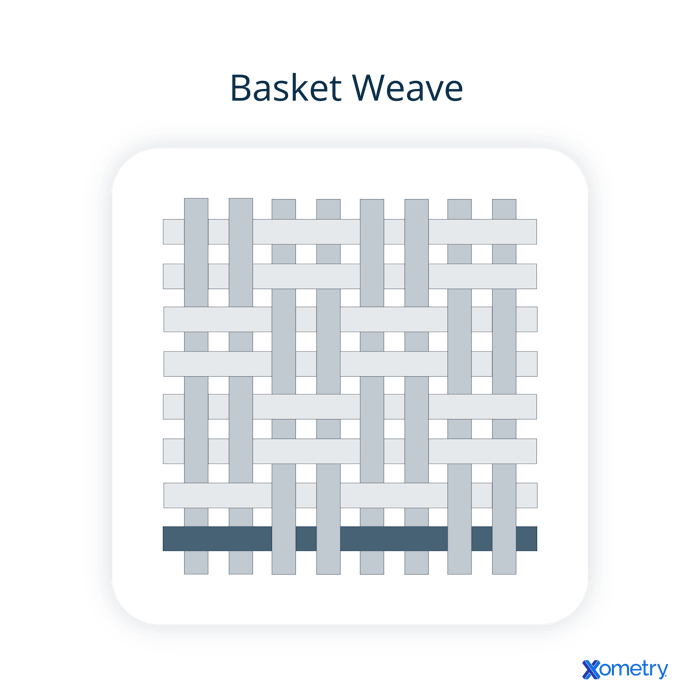
Basket weave
Leno: A criss-cross pattern that keeps fibers securely in place to prevent unraveling.
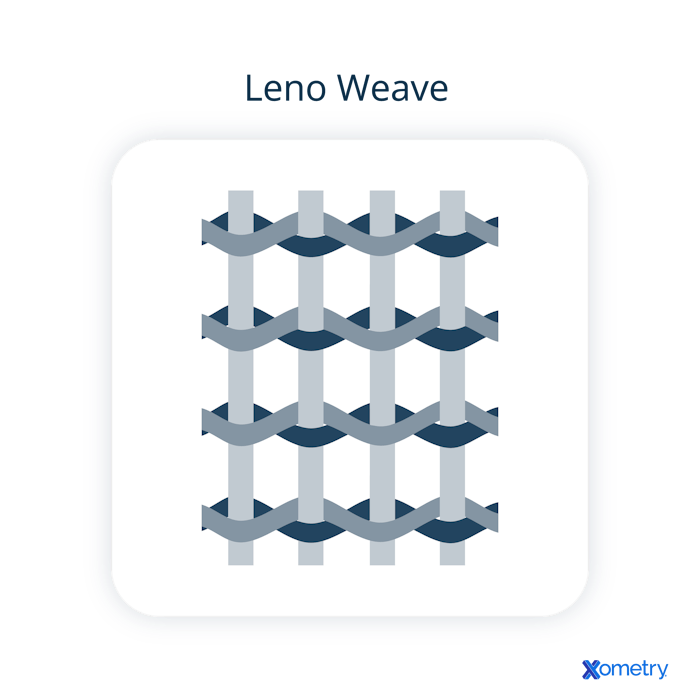
Leno weave
Mock leno: Looks like leno but is a little more flexible and less stable.
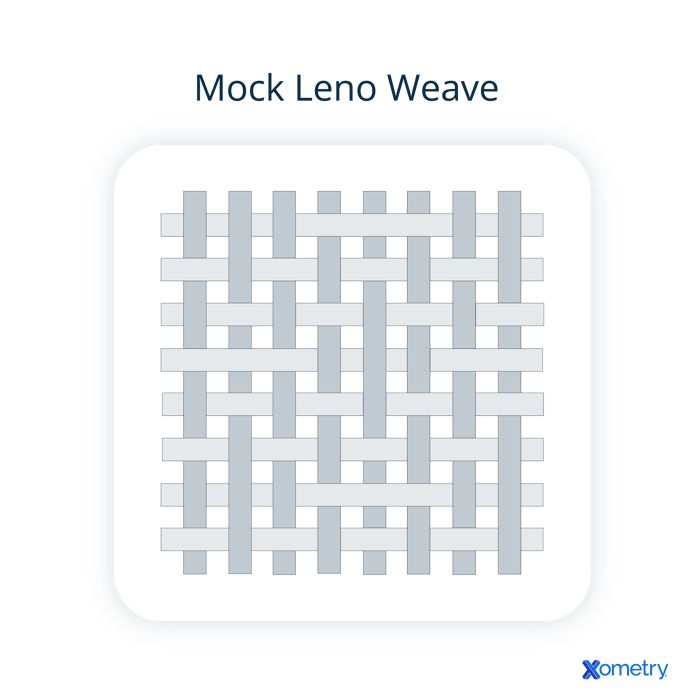
Mock leno weave
The number of times a fiber goes over and under other fibers is known as the crimp, and the higher the crimp, generally, the higher its stability. But high-crimp carbon fiber means the material won’t be very flexible (known as its drapability) to form intricate shapes or geometry.
Advanced Applications
Because of its high price tag, carbon fiber is currently only used in high-performance applications, a few of which we list below.
Aerospace: Its low weight makes carbon fiber suitable for aircraft fuselage, empennage, nose cones, and rotor blades. When these parts are made from this material, aircraft weight can be reduced by up to 20%—something that saves millions of dollars in fuel.
Sporting goods: It’s used to make lighter, stronger, and faster-moving tennis rackets, skis, snowboards, bikes, and golf clubs. Just be prepared to pay a lot more for carbon fiber sports equipment.
Medical: X-ray devices and implants are made from carbon fiber mainly because it is radiolucent (X-rays can pass through it easily). It’s also wear-resistant and has a similar stiffness to human bone. Unlike the metal used in some implants, carbon fiber is brittle and could shatter.
Energy: Plans for carbon fiber battery storage systems are in the works, which could greatly reduce the weight of electric cars.
Civil engineering: Carbon fiber is becoming increasingly popular in bridges and concrete structures where strength is more important than weight. Because it can be up to ten times stronger than steel, it’s preferred, but as we’ve established, it’s much more expensive to use.
Marine: As carbon fiber’s price is on the decline, it’s starting to replace the use of fiberglass in yachts and small boats.
Military/defense: Drones, helicopters, jets, and transport aircraft can all be made using this material. The design of helmets has become much more complex over the years—something that also makes them heavier. Carbon fiber is here to save the day (but there’s still the issue of difficulty detecting damage).
One downside, though, is something called Barely Visible Impact Damage. Basically, it’s hard to spot damage on this material with the naked eye, so checking for faults needs extensive training and testing. This factor affects most of the above industries, but especially aerospace, energy, marine, and military.
Carbon Fiber and 3D Printing
Carbon fiber is compatible with 3D printing. It can either be used as a continuous fiber layer or printed as short strands in the filament of an FDM (Fused Deposition Modeling) printer. The printer will need two printheads if you are to print with a continuous fiber: one for the plastic filament and one for the carbon fiber. If you choose to embed chopped strands within the filament, you can improve the strength and stiffness of printed parts without going bankrupt. Using this material in 3D printing means you can make parts that can be used for structural purposes because they’re way stronger than the typical PLA and ABS used in 3D printing. With carbon fiber, parts can be compared in strength to materials like aluminum.
The aerospace industry is using 3D-printed carbon fiber parts to some extent. Because of safety regulations, any new technology or materials need to undergo extensive testing and qualification before being used in aerospace, but for now, it’s not uncommon to find parts for brackets and specialized tooling made from 3D-printed carbon fiber. Companies don’t have to deal with huge lead times, either.
How Xometry Can Help
For more info on carbon fiber, feel free to reach out to one of our reps, or request a free no-obligation quote for any one of our manufacturing services, like CNC machining, 3D printing, and carbon fiber laser cutting, to name just a few.
Disclaimer
The content appearing on this webpage is for informational purposes only. Xometry makes no representation or warranty of any kind, be it expressed or implied, as to the accuracy, completeness, or validity of the information. Any performance parameters, geometric tolerances, specific design features, quality and types of materials, or processes should not be inferred to represent what will be delivered by third-party suppliers or manufacturers through Xometry’s network. Buyers seeking quotes for parts are responsible for defining the specific requirements for those parts. Please refer to our terms and conditions for more information.
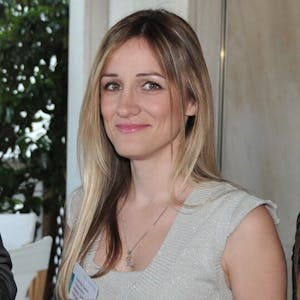