Metal injection molding and die casting are both prominent ways of creating high-quality metal parts. Despite their similar purpose, they each have their own pros and cons and work better in different situations. How do they work, when would you use them, and are there any alternatives? Let’s see.
Metal Injection Molding Definition and Comparison to Die Casting
Metal injection molding (MIM) works on a principle similar to plastic injection molding and was invented by Raymond Welch in the 1970s. One of the biggest differences between the two is that MIM uses metal powder that’s mixed with a plastic binder which is later burned out and removed, whereas in plastic injection molding, you can add certain additives like glass or ceramic fibers into the mix, but they stay in to improve the part’s qualities.
In MIM, the metal and binder mix is fed into a barrel, inside which a screw pushes it through a narrowing space and, in turn, compresses it as it moves toward the mold. This compression actually generates heat, and so does the barrel itself, which ultimately melts the plastic binder that helps carry the metal powder into the mold. When the melting is done, the screw will move back and then push the material into a two-part mold that is clamped tightly. When the molded piece has cooled down (it’s known as the green part), it’s ejected.
The next step is to remove the binder, and this will leave some gaps that can be filled by sintering. Then, the green part is exposed to certain solvents or a catalyst along with high heat which will remove the binder. The part that’s left is now referred to as the brown part. This brown part is then placed into a furnace where the metal particles will fuse together—the sintering process. This will make the part strong and dense. During this time, though, the part can shrink by around 15–30%, depending on the material. After the sintering, the part has reached its final mechanical properties. This is an example of parts created using MIM:
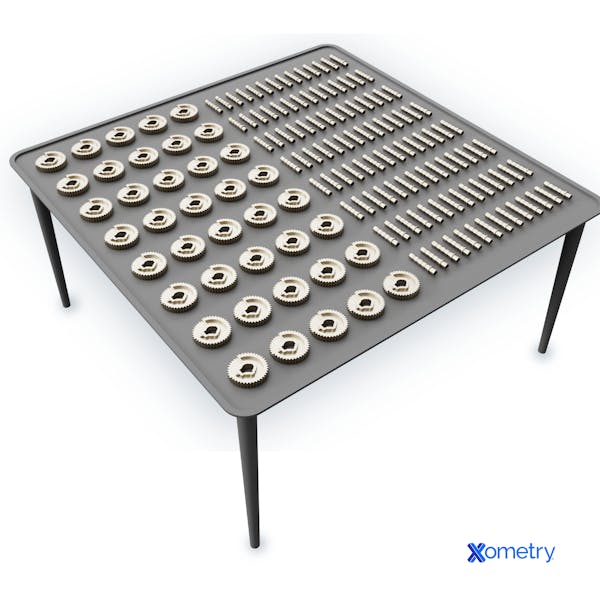
MIM is a great way of making parts that are small and rather complex in terms of features. It also doesn’t require a molten metal feedstock like other methods do. That’s because it only really uses high temperatures during the sintering process. That’s also good because you can use materials with really high melting points without having to worry about processing and handling them in their molten form. A few potential drawbacks with MIM include the fact that these machines and their tools tend to be expensive. The molds don’t last too long because of the abrasive nature of the metal powder, and the parts need quite a bit of post-processing, which also bumps up the cost. Also, as mentioned, the parts shrink quite a lot. So you’ll need to take this into account beforehand to make sure parts meet your size requirements.
What are the Advantages of Metal Injection Molding Compared to Die Casting?
Listed below are some advantages of metal injection molding compared to die casting:
- MIM can manufacture a wide variety of small, complex parts with fine features using the same techniques in standard plastic injection molding. Die casting, on the other hand, struggles to produce fine feature parts.
- The MIM process only makes use of high temperatures during the sintering process. A molten metal feedstock is not required like with die casting. This also means that materials with very high melting temperatures can be used without the challenges of processing and handling these metals in molten form.
What are the Disadvantages of Metal Injection Molding Compared to Die Casting?
Listed below are some disadvantages of metal injection molding compared to die casting:
- Due to the complex high wear resistant tooling required for metal injection molded parts, metal injection molding (MIM) equipment can be expensive. MIM molds do not last as long as diecast molds because of the abrasive nature of the metal powder feedstock.
- MIM requires multiple post-molding steps to produce the final part. This adds cost to the final parts compared to those produced by die casting.
- Metal injection molded parts shrink significantly during the densification process. Mold design requires an advanced understanding of the properties of the binder, the metal, and the interaction between the two during post-processing to produce final parts that can meet dimensional requirements.
Die Casting Definition and Comparison to Metal Injection Molding
It sounds quite similar to MIM, in that die casting is a way of manufacturing metal parts by injecting molten metal into a mold. It dates all the way back to 1838 when it was first invented and later patented in 1849. This method was first used for lead and tin, and in 1914, aluminum and zinc were introduced. Today, it’s also fine with magnesium, copper, and silicon, but it’s limited to non-ferrous metals. Having said that, if you really want to, you can try die-casting ferrous metals, but it’s not very common.
With this technique, the molten metal can either be injected under pressure or simply flow in by gravity feed. When the part has finally cooled down—which can take up to a minute, subject to part size and wall thickness—it can be ejected from the mold. You can remove any excess material from the gates, runners, and parting line flash manually or using a press die.
Die casting molds last a long time; in some instances, just one can make up to a million parts (compared to MIM molds which make a couple hundred thousand if you’re lucky). Die-cast parts also don’t shrink. This type of casting does have some potential downsides, though. For example, it’s best used with non-ferrous metals. Ferrous metals tend to have a really high melting point, which can ultimately make the molds deteriorate much faster. Also, if you’re injecting molten metal at high pressures and temperatures, it’s very easy to trap gasses within the material. This can make the part porous and reduce its mechanical strength, whereas MIM parts have the chance to get rid of any entrapped gases during sintering.
Kevin Choate, a Senior Solutions Engineer here at Xometry, says "Metal Injection Molding (MIM) is a process developed to mold high melting temp materials, like steel. There are other factors for MIM which are important when looking at part specific or project specific. High melt temperature metals are not suited for die-casting -- with die casting you melt the metal and use pressure to inject or force the molten material into the cavity, or tool, similar to injection molding. You would use MIM over die-casting if you need stainless steel, or other steels/materials that have a very high melt temp. Die-casting is pretty much just for aluminum, and zinc."
What are the Advantages of Die Casting Compared to Metal Injection Molding?
Listed below are some advantages of die casting compared to metal injection molding:
- Die casting molds last longer than MIM molds. In some cases, a single die-casting mold can be used to make a million parts, whereas a MIM mold can only produce a couple hundred thousand.
- Diecast parts do not shrink the way MIM parts do. This means that molds can be more easily manufactured to the required size.
What are the Disadvantages of Die Casting Compared to Metal Injection Molding?
Listed below are some disadvantages of die casting compared to metal injection molding:
- Die casting is typically used with non-ferrous metals. While ferrous metals like steel can be die-casted too, these materials have very high melting points. This can significantly reduce the life of the molds. This makes die casting of limited use for high-performance and high-temperature applications.
- Molten metal injected at high pressures and temperatures will often entrap gasses within the material. This results in porosity which ultimately reduces the part’s mechanical strength. MIM parts have significantly less porosity as the pre-sintered part has a lot of room for air to escape during sintering.
Comparison Table Between Metal Injection Molding and Injection Molding
Table 1 below compares some common properties of metal injection molding and die casting:
Attribute | Metal Injection Molding | Die Casting |
---|---|---|
Attribute Wall thickness | Metal Injection Molding 0.04” to 0.12” | Die Casting 0.04” to 0.2” |
Attribute Multi-step process | Metal Injection Molding Yes | Die Casting No |
Attribute Materials | Metal Injection Molding Anything that can turn into a powder, including tungsten, stainless steel, tool steel, cemented carbides, nickel superalloys, and precious metals | Die Casting Aluminum, zinc, copper, magnesium, lead, pewter, tin |
Attribute Volume | Metal Injection Molding Good for high-volume production of intricate parts | Die Casting Suitable for producing a high volume of larger, simple parts |
Metal Injection Molding vs. Die Casting Attributes
MIM is better suited to engineering applications that require high-performance materials and small, complex parts. Die casting is better suited to lower-performance metals and larger part sizes.
Metal Injection Molding vs. Die Casting: Lead Cost Comparison
Due to the cost of mold manufacture for MIM and die casting, both technologies require relatively large production volumes to justify the mold costs. However, at medium to large volumes, both technologies produce very low-cost parts. Die casting is up to 30% less expensive than MIM due to there being no need for multiple post-processing steps as is the case with MIM.
Metal Injection Molding vs. Die Casting: Speed Comparison
Comparing only the speed of the actual molding process, metal injection molding (MIM) is faster than die casting. However, MIM requires post-molding processes that make its overall cycle time to produce a finished part longer than for a finished diecast part.
Metal Injection Molding vs. Die Casting: Volume Comparison
Metal injection molding and die casting are both high production-volume technologies. Typical production runs on a mold for both can easily reach hundreds of thousands or even millions of parts. MIM is ideally suited to high-volume production of intricate parts, whereas die casting is better suited to high-volume runs of larger, simpler parts.
Metal Injection Molding vs. Die Casting: Materials Comparison
Die casting typically only makes use of non-ferrous metals like: aluminum, copper, zinc, magnesium, and lead. MIM can make use of ferrous metals as well as more advanced materials like titanium and nickel alloys. One of the most commonly used MIM materials is stainless steel. MIM can essentially be used with any metal that can be converted into powder form.
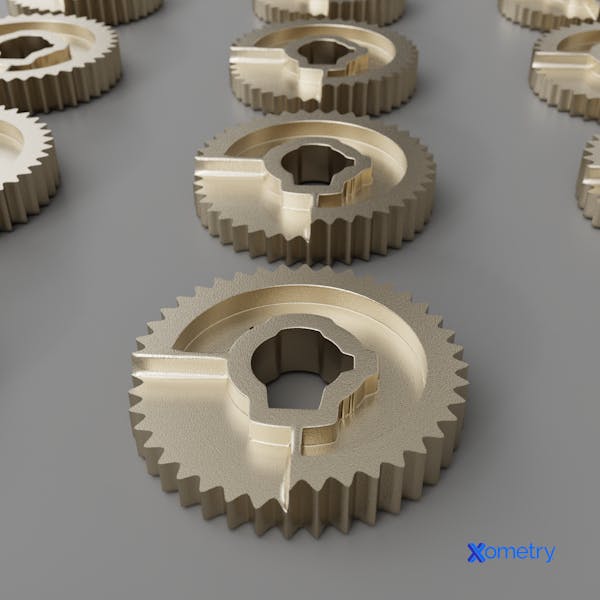
Frequently Asked Questions on MIM and Die Casting
Which of these is faster?
When it comes to the actual casting process, MIM wins. But, it also requires post-molding processing which can ultimately make it slower than die casting overall.
What are the Mutual Alternatives to the Metal Injection Molding and Die Casting?
The manufacturing technique that can be considered an alternative to both of these is SLM, which stands for selective laser melting. It’s a form of additive manufacturing (3D printing) that can create complex parts made of metal. It works by using a laser to melt a metal powder in select areas. When each layer is complete, it gets started on the next one until the part is finished.
What are the Similarities Between Metal Injection Molding and Die Casting?
Listed below are some similarities between metal injection molding and die casting:
- MIM and die casting can both produce metal parts. However, die casting is restricted to a more limited group of suitable materials..
- MIM and die casting both have material injected into molds at high pressures. This allows for parts with fine features and thin walls.
What are the Other Comparisons for Metal Injection Molding Besides Die Casting?
Binder jetting is a type of 3D printing, and it works by binding metal powder together without the need for a mold. It does everything right there on the print bed. When the parts are done, they can be post-processed and sintered, much like MIM parts. Unlike MIM, though, binder jetting is only really good for low-volume production runs.
What are the Other Comparisons for Die Casting Besides Metal Injection Molding?
Sand casting is one of the oldest ways of processing metal parts and is still prominent today. It works using a special kind of sand, which is packed around a core that’s shaped like the final part. Holes are made in the mold for filling and letting air escape. The metal is then cast into the mold, and once it’s cooled down, the mold is broken open to get the part out. Any sprues, feeders, and flash need to be ground off after.
How Xometry Can Help
If you have any questions about molding or anything else manufacturing-related, a Xometry representative would be happy to help you. We also offer an abundance of other related services including CNC machining, 3D printing, and laser cutting. You can get your project off the ground today by requesting a free, no-obligation quote right from our website.
Disclaimer
The content appearing on this webpage is for informational purposes only. Xometry makes no representation or warranty of any kind, be it expressed or implied, as to the accuracy, completeness, or validity of the information. Any performance parameters, geometric tolerances, specific design features, quality and types of materials, or processes should not be inferred to represent what will be delivered by third-party suppliers or manufacturers through Xometry’s network. Buyers seeking quotes for parts are responsible for defining the specific requirements for those parts. Please refer to our terms and conditions for more information.
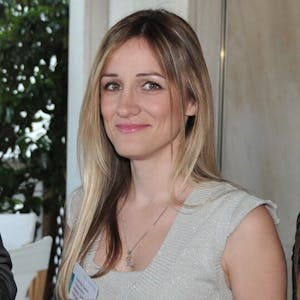