Transfer molding is a well-liked manufacturing process that our customers use to make durable parts. Let’s go into what it is exactly and its most common applications.
What is Transfer Molding?
Transfer molding is a process in manufacturing that involves transferring a preheated and softened material that has already been measured, into a closed mold cavity under pressure. That way, it can cure or solidify into whichever shape you need. This method is not quite the same as compression molding because it uses an enclosed mold. It has a lot going for it, though. For example, it’s easy to integrate inserts, it can make complex shapes with sharp edges, it makes parts with minimal to no flash, and isn’t excessively expensive because its design is fairly simple.
One of the most popular uses of transfer molding is to wrap electronic components in rubber or plastic. It’s also a great way of making plastic parts with metal inserts like prongs or semiconductor chips. You can also make things like connectors, studs, pins, and molded terminals. Another advantage of using this molding method is that it can make parts with sharp corners and edges. That’s especially useful in sectors like hydraulics which require proper fluid sealing. Lip seals are one example of this. It’s also a hit in the natural gas industry for face seals and the medical industry for medical device handles and surgical instrument components. Here’s a video we made all about transfer molding:
Materials
Transfer molding is compatible with a few different materials. These are some of the typical ones:
Epoxy
A thermosetting polymer that’s surprisingly versatile, epoxy has really good electrical insulation properties and is very resistant to chemicals. It’s also quite low in viscosity, meaning it flows easily during the process. One potential downside is that it will likely need post-curing because it can be quite brittle.
Silicone
Another versatile polymer, silicone is known for how flexible it is. It’s durable, temperature resistant, and biocompatible. But, it’s not the cheapest material out there, and it has a relatively long curing time.
Polymers
This is a broader category, but when it comes to certain polymers like polyurethane and polyester, they work very well with transfer molding. Polyurethane is very strong, flexible, and chemical resistant, and polyester is heat resistant and has good mechanical strength.
Rubber
Rubber is basically elastomers that have high elasticity and resilience. Whether natural or synthetic, rubber is easy to make with transfer molding. Depending on the type, you may need post-curing or vulcanization to improve its properties. We have a guide on TPR material, which you can read to learn more.
Plastics
We’ll use two plastics as examples: polypropylene and polycarbonate. Both of these work very well with transfer molding. Polypropylene flows well and can fill every crevice of the mold cavity. It’s also chemical resistant and has good dimensional stability. Polycarbonate has high impact strength, transparency, and heat resistance. Some plastics, like polyethylene, will be limited in terms of temperature resistance, strength, and dimensional stability.
How it Works
The technical explanation of this method is that it combines compression and transfer of the polymer charge. What does this mean? This means that a pre-weighed polymer charge is fed into a transfer pot by gravity feed and introduced into the mold cavity under pressure from a plunger. When the resin cures and is ready to be taken out, it’s ejected using an ejector pin. It’s not uncommon to have to do some post-processing after this, like trimming off the sprue and gate. The following image breaks down the basic process:
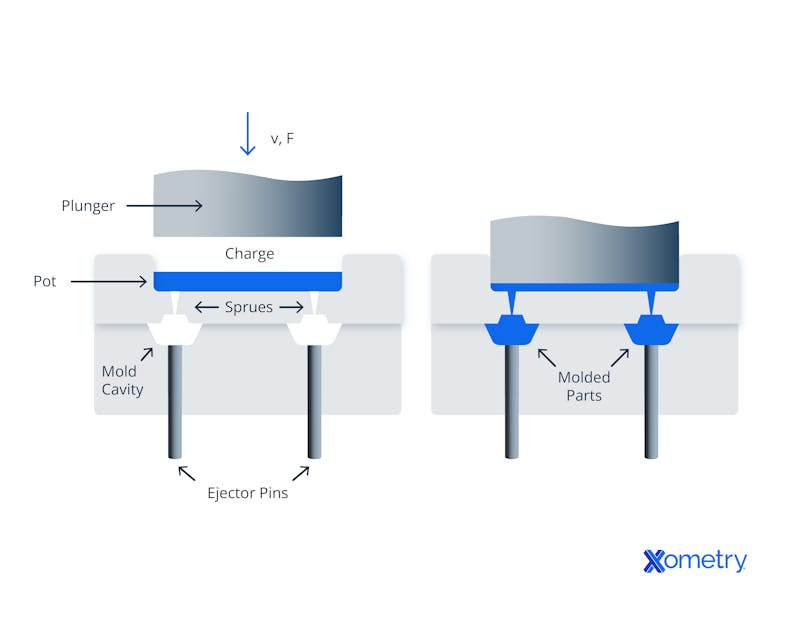
The Transfer Molding Process
Transfer molding is usually faster than compression molding but slower than injection molding. Of course, it all depends on what materials you’re working with and how complex the part is. The reason it typically has faster cycle times is that it injects the material into the mold with a higher pressure.
On the downside, you could waste material, especially during the prep and transfer stages. This could also contribute to a negative environmental impact. It also isn’t the quickest of molding methods because of the preparation involved, and it’s not unheard of to get air trapped in the mold during the transfer process. Needless to say, this can cause defects in your final product.
Transfer Molding vs. Resin Transfer Molding (RTM)
They sound very similar, but they’re not the same thing. Resin transfer molding injects liquid resin into a closed mold that contains dry fibers like glass or Kevlar. When the resin impregnates the fibers, the part is cured inside the mold and you have a solid composite part. Another type of RTM is high-pressure RTM (HP-RTM) which has higher injection pressures to speed things up. If you’re in a hurry, like those in the automotive industry tend to be, HP-RTM is the way to go. It has an impressive resin injection time of just 1–5 minutes, unlike the 30–60 minutes of RTM.
Transfer Molding vs. Injection Molding
This is another worthy comparison. Both of these methods are used to make plastic parts, but they have some differences. Unlike transfer molding, which involves feeding material into a heated chamber through a screw and then using a plunger to force it into a mold cavity, injection molding uses a reciprocating screw to melt and inject the material straight into the cavity. That’s why injection molding is usually better for larger production runs, as well as bigger parts with thin walls.
Transfer molding can work out more expensive and time-consuming, too, because most of the time, you have to prepare the raw material before having it forced into the mold. With injection molding, you don’t have this issue because it mixes and gets the material ready straight away. Whether you choose transfer molding or injection molding for your next project depends entirely on your preference, as well as your time frame and budget. To find out more about injected plastics, you can read our guide.
How Xometry Can Help
We recommend reaching out to one of Xometry’s representatives if you have any questions about transfer molding, or any type of molding for that matter. Xometry also provides an abundance of manufacturing services like CNC machining, 3D printing, laser cutting, and compression molding. You can request a free, no-obligation quote to get started right away.
Disclaimer
The content appearing on this webpage is for informational purposes only. Xometry makes no representation or warranty of any kind, be it expressed or implied, as to the accuracy, completeness, or validity of the information. Any performance parameters, geometric tolerances, specific design features, quality and types of materials, or processes should not be inferred to represent what will be delivered by third-party suppliers or manufacturers through Xometry’s network. Buyers seeking quotes for parts are responsible for defining the specific requirements for those parts. Please refer to our terms and conditions for more information.
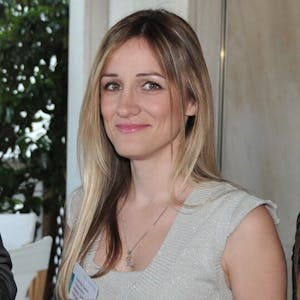