Force testing is widely used in many industries to determine how an object or material will react in different loading conditions. This is important information that engineers, product manufacturers, and designers can use to see whether a product will be able to withstand the conditions it will face. It can also help in making the right material selection for a specific function. Force testing is crucial for both quality control and safety purposes.
This article will take a closer look at force testing, its importance, purpose, testing methods, benefits, and challenges.
What Is Force Testing?
Force testing, also known as force measurement, is the simplest form of material testing assessment. It is a way of determining how an object will react under different forces or loads. Force testing is used in various industries for quality control, reliability, and safety of products, by determining how an object will react in different conditions, such as pulling and pushing actions. Force testing can involve different types of forces, such as: compression, tension, shear, and bending, depending on the specific application.
What Is the Purpose of Force Testing?
The main purpose of force testing is to determine how an object or material will react in different conditions, such as: being pulled, pushed, bent, or compressed. This will give product designers, engineers, and manufacturers a better idea of whether a product will function properly when in use and whether it is fit for its purpose. Force testing is therefore used for product quality control, performance evaluation, reliability, and safety purposes. It can also be used for material characterization, research and development, and material or product life-cycle analysis.
How Is Force Testing Done?
Force testing is performed differently depending on the parameter being measured. However, there are general steps in how force tests are performed that remain the same. Listed below are the general steps:
- Select the appropriate force-testing method, considering the material, type of force (tension, compression, shear, bending), and applicable standards. Specimens are then prepared according to these standards.
- The test machine, typically a universal testing machine (UTM), is set up with necessary fixtures and calibrated with a load cell to measure the force accurately.
- Securely mount the specimen in the machine.
- Apply force at a controlled rate.
- Collect the data throughout the test, measuring force, deformation, strain, and other necessary parameters.
How Important Is Force Testing in Manufacturing?
Force testing is very important in manufacturing mainly to ensure product quality and safety. It ensures that products or materials will be able to withstand the conditions they will be subjected to — which significantly reduces the chances of catastrophic failures. It also aids in material selection and product development, allowing manufacturers to choose appropriate materials and improve product designs. Additionally, force testing helps in cost reduction by identifying potential issues early and preventing costly rework and recalls.
What Are the Types of Force-Measurement Testing?
Many different types of force testing can be performed, each with its purpose. Some of the most common force-testing methods include:
1. Torque Testing
Torque testing is a method used to evaluate the reaction of an object when subjected to rotational force, or twisting, either during its normal operation or when twisted to the point of failure. This testing is crucial in determining how well an object can withstand being turned or twisted and is commonly applied in two scenarios: fastening tests of objects and testing rotating parts in an assembly.
There are two main types of torque measurement: reaction torque and in-line torque. Reaction torque measurement involves measuring the torque transferred through a stationary part while holding or reacting against the rotating part. In-line torque measurement, on the other hand, measures the torque transmitted along the rotating shaft. The application of the correct torque is critical in ensuring the proper functioning and assembly of parts. Incorrect torque can lead to failures, such as parts not being securely assembled or damage due to excessive torque, like stripped threads. Torque testing is particularly important in industries like automotive, in which it is used to ensure the correct assembly and functioning of various components, including bolts and engine parts.
To learn more, see our full guide on Torque Testing.
2. Compression Testing
In this mechanical test, a compressive load is applied to an object, and its deformation, or response, is recorded. It's similar to tensile testing but focuses on how materials behave under compressive forces (forces pushing toward each other). The resulting data helps in understanding the mechanical properties of materials, such as compressive strength, stiffness, ability to withstand loads without failing, and durability—which is important information for selecting appropriate materials for different applications, particularly in the construction and engineering fields.
During a compression test, a material sample is placed between two plates or jaws of a specialized testing machine. The machine then applies a compressive force to the sample. This force continues to be applied until the material either deforms to a certain extent or fractures. The amount of force and the corresponding deformation of the material are carefully measured, typically using devices like a deflectometer or an extensometer.
3. Tensile Testing
This type of testing involves applying a uniaxial load to a specimen, typically a test bar, and gradually increasing this load until the material breaks. During a tensile test, the specimen is stretched, and the amount of force applied is measured along with the extent of elongation of the material. An extensometer is usually used to measure this elongation. As the test progresses, the data collected, including the force applied and the corresponding elongation, is used to create a stress-strain curve. This curve is then used to analyze the tensile properties of the material, providing insights into its strength, ductility, yield point, and ultimate tensile strength.
Tensile testing is essential in determining how materials will behave when subjected to tensile forces in real-world applications. It is particularly important in industries in which materials are required to bear loads without breaking, such as: in construction, automotive, aerospace, and manufacturing.
4. Shear Testing
Shear testing is a method used to evaluate the shear strength of a material, which is its ability to resist forces that cause the internal structure of the material to slide against itself. The test is designed to determine how a material behaves when subjected to shear forces, which are forces applied in parallel but in opposite directions, often along a plane within the material.
During a shear test, a specimen of the material is subjected to a load that applies these opposing forces. The goal is to measure the force required to cause the material to fail or deform by shearing. Shear testing is widely used in industries such as: construction, manufacturing, and materials science. It's particularly important for materials that are used in applications in which shear forces are common, such as: in beams, shafts, and fasteners.
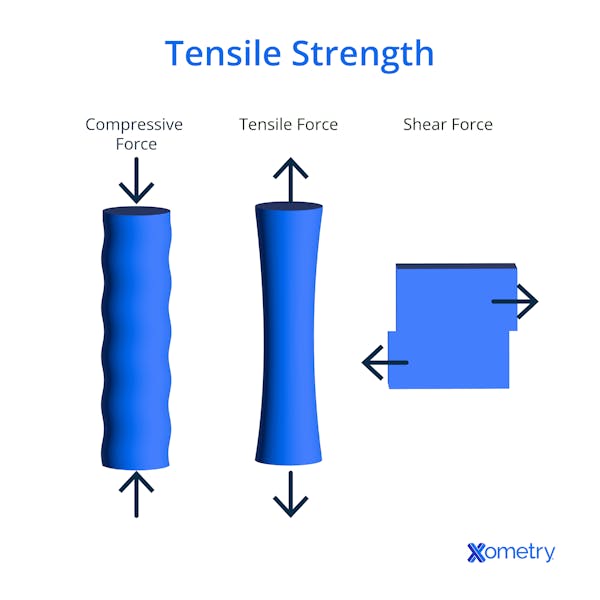
5. Hardness Testing
Hardness testing is a method used to evaluate the resistance of a material to deformation, particularly permanent deformation such as indentation or scratching. It's a measure of how well a material can withstand surface wear and penetration.
In a hardness test, a specific force is applied to an indenter (which could be a hard ball, diamond pyramid, or cone) that presses into the surface of the material being tested. The test measures the depth or size of the indentation made by the indenter under the applied force. There are several different hardness tests, including the Rockwell, Brinell, Knoop, Vickers, and Shore (durometer) tests, each using different indenters and methods of measuring the indentation.
6. Static Testing
Static testing is a type of force-measurement testing in which a constant or non-fluctuating load is applied to a material or component. Unlike dynamic testing, during which loads vary or are applied cyclically, static testing involves applying a steady force and observing the material's response under these sustained conditions.
The primary purpose of static testing is to evaluate the behavior and properties of materials when subjected to a continuous load or pressure. This can include assessing the material's strength, stiffness, and deformation under static conditions. It helps in understanding how the material will perform when used in applications in which it will be under a constant load or force, such as in structural components of buildings or bridges.
7. Fatigue Testing
Fatigue testing is a process employed to evaluate the durability of components and materials under repeated or fluctuating loads over time. This type of testing simulates the conditions that a material would experience in real-world applications in which it is subjected to continuous cycles of stress and strain. The primary aim of fatigue testing is to determine the material's fatigue life—the number of cycles it can endure before failing due to fatigue. However, other parameters, such as crack resistance and fatigue strength can also be obtained.
During fatigue testing, the material or component is subjected to cyclic loading, which can vary in amplitude, frequency, and pattern. The test continues until the specimen fails, or a predetermined number of cycles is reached. Cyclic fatigue tests produce repeated cycles of loading and unloading in compression, tension, torsion, bending, or combinations of these stresses. Fatigue testing is crucial in several industries, including, but not limited to, aerospace, automotive, construction and civil engineering, and medical devices.
8. Mechanical-Strength Testing
Mechanical-strength testing is a process used to determine the ability of a material or component to withstand various types of mechanical forces without failure. It’s a way of testing a material to obtain its mechanical properties. This type of testing assesses key properties like: tensile strength, yield strength, compressive strength, flexural strength, hardness, and impact resistance. The objective is to evaluate how materials behave under different stress conditions and to ensure they can endure the demands of their intended applications.
In mechanical-strength testing, materials are subjected to controlled forces that mimic the stresses they will face in real-life scenarios. Tests are conducted using specialized equipment — usually a UTM (universal testing machine) — designed to apply specific types of forces, such as: tension, compression, bending, and impact. For instance, a tensile-strength test measures a material's resistance to being pulled apart, while a compressive-strength test assesses its ability to withstand pressing or squeezing forces.
The data gathered from these tests helps in material selection, design optimization, and quality assurance, ensuring that products are safe, reliable, and fit for purpose. Mechanical strength testing is crucial across various industries, including: construction, automotive, aerospace, and consumer goods.
9. End-of-Line Testing
End-of-line testing is a quality control process conducted at the final stage of the manufacturing process (at the end of the production line), just before products are shipped or delivered to customers. This type of testing is designed to ensure that finished products meet all the required specifications, quality standards, and functional requirements.
In end-of-line testing, each unit of the product undergoes a series of checks and tests to identify any defects, malfunctions, or deviations from the intended design. The tests performed can vary depending on the product but typically include: functional tests, performance tests, safety tests, and visual inspections. The goal is to catch any issues that might have been missed in earlier stages of production.
10. Material Testing
Material testing is the process of evaluating the properties and behavior of materials to determine their suitability for specific applications. This type of testing is essential for understanding the physical, mechanical, thermal, electrical, and chemical characteristics of materials, such as: metals, plastics, composites, ceramics, and polymers. Properties that are typically measured during material testing include: compressibility/compactibility, abrasion, friction, hardness, flexibility/rigidity/stiffness, tensile strength/breaking strength/elongation, peel strength/seal strength, actuation forces, burst strength, and stickiness/adhesiveness.
The results of material testing provide crucial insights for material selection, product design, quality control, and compliance with industry standards and regulations. It helps manufacturers and engineers to ensure that materials will perform as expected under various conditions and that products made from these materials are safe, reliable, and of high quality. Material testing is widely used in industries like: construction, automotive, aerospace, electronics, and consumer goods to ensure that materials meet the demands of their intended applications.
11. Proof-Load Testing
Proof-load testing is a method used to verify the strength and structural integrity of a component or assembly by applying a specified load, known as the proof load. This load is typically set at or above the maximum operational load that the component is expected to encounter during its service life, but below the load that would cause permanent deformation or failure.
The purpose of proof-load testing is to ensure that the component can safely bear its intended load without experiencing any permanent damage or deformation. During the test, the component is loaded for a specific period (different for each component), and its behavior under this load is closely monitored. The component is then closely monitored for any signs of yielding, permanent deformation, or failure.
Proof-load testing is commonly used in industries such as: construction, aerospace, and automotive. This type of testing is particularly important for load-bearing components, fasteners, lifting equipment, and other structural elements.
What Are the Benefits of Force Testing?
Force testing offers several benefits, such as:
- Ensures that products meet required specifications and quality standards, reducing the risk of defects.
- Verifies that products are safe for use.
- Helps in selecting the right materials for specific applications and in optimizing product designs based on material properties.
- Identifies potential issues early in the manufacturing process.
- Essential in research and development for creating new products and enhancing existing ones.
- Assesses how products will perform over time—which helps to predict a product’s life span.
What Are the Challenges of Force Testing?
Despite its many benefits, force testing also has some challenges:
- Some tests, particularly those involving dynamic or cyclic loading, require sophisticated and sometimes custom test setups.
- Adhering to various industry standards and regulatory requirements can be complex.
- Extracting meaningful insights from test data requires expertise in material science and engineering.
- High-quality testing equipment can be expensive to purchase and maintain.
Why Do Different Manufacturing Sectors Follow Different Force-Testing Techniques?
Different manufacturing sectors use different force-testing techniques due to their products and materials' unique characteristics and requirements. Each material, whether metal, plastic, composite, or ceramic, has different properties that require specific testing methods. The nature and function of the product, such as aerospace components versus consumer electronics, significantly influence the choice of testing, as well as industry-specific standards and regulations. The type of loads a product will face, including tensile, compressive, and shear forces, and the environmental conditions it will encounter are also important in selecting the correct testing technique. Moreover, it is important to consider the potential failure modes of a product when choosing the right testing approach. All of these factors are important to consider in each manufacturing sector before selecting the appropriate force-testing technique.
What Factors Determine the Type of Force Testing To Be Used?
Several factors determine the type of force testing to be used in a given scenario. These are:
- The inherent characteristics of the material, such as: strength, ductility, hardness, and elasticity, should be considered when selecting the correct force-testing method.
- The design, intended use, and functional requirements of the product dictate the types of stresses it will encounter, which, in turn, influences the choice of force testing.
- The type of force-testing method is determined by the nature of the force (tension, compression, shear, bending, etc.) that the material or product will experience.
- Each industry has specific standards and regulations that outline the required testing procedures for different materials and products.
- Understanding how a material or product could potentially fail helps in choosing a testing method that can simulate those failure conditions.
- The goals of the testing, such as: quality control, research and development, or compliance, also influence the type of force testing used.
What Devices Are Used for Force Testing?
Force testing can be done using different devices. The type of device used will depend on the property to be measured. UTMs (universal testing machines) are very versatile machines that are often used for different force-testing measurements. They can be used for tests like: compression, tensile, and bending tests. Load cells are also commonly used to measure the force being applied to a specimen. Hardness tests are performed using instruments like Rockwell, Brinell, and Vickers testers. Other examples of devices that are commonly used for force testing are extensometers and deflectometers, which are used to measure deformation or strain in the material.
Is Force Testing Necessary in Manufacturing?
Yes, force testing is necessary in manufacturing. It ensures that products meet quality standards, comply with safety regulations, and perform as intended. This testing helps in material selection, product development, and identifying potential issues beforehand.
Summary
This article presented force testing, explained it, and discussed its purpose and various types of testing. To learn more about force testing, contact a Xometry representative.
Xometry provides a wide range of manufacturing capabilities and other value-added services for all of your prototyping and production needs. Visit our website to learn more or to request a free, no-obligation quote.
Disclaimer
The content appearing on this webpage is for informational purposes only. Xometry makes no representation or warranty of any kind, be it expressed or implied, as to the accuracy, completeness, or validity of the information. Any performance parameters, geometric tolerances, specific design features, quality and types of materials, or processes should not be inferred to represent what will be delivered by third-party suppliers or manufacturers through Xometry’s network. Buyers seeking quotes for parts are responsible for defining the specific requirements for those parts. Please refer to our terms and conditions for more information.
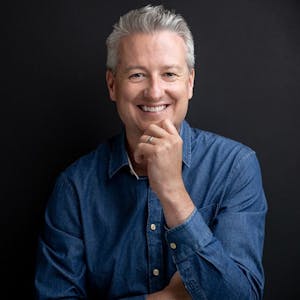