Compression testing is a widely used mechanical test that provides valuable insights into the behavior of materials when subjected to compressive loads. The test is essential in selecting the right material for various applications in industries such as aerospace, automotive, and construction. This article will delve into the definition, purpose, applications, and how compression testing works, as well as the steps involved in performing a compression test.
What Is a Compression Test?
A compression test is a mechanical test used to determine the behavior of materials when subjected to compressive loads. The data collected from compression tests gives helpful insights into the mechanical properties of different materials, which are invaluable in selecting the right material for different applications, especially in the construction and engineering industries.
How Does Compression Testing Work?
In a compression test, a sample of the material is placed between two plates or jaws of a testing machine. This can be in the form of a universal testing machine, with a load cell measuring the force applied. A compressive force is applied to the sample until it reaches a specific deformation or until it fractures. Additional devices such as a deflectometer or an extensometer, can be used to measure the deflection or compressive strain of the sample.
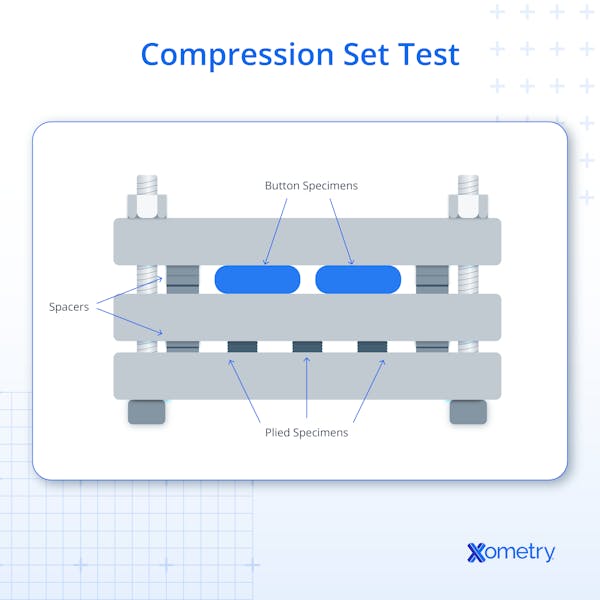
What Is the Purpose of Compression Testing?
Compression testing's objective is to ascertain a material's behavior or response to a compressive load by measuring key parameters such as strain, stress, and deformation. Compression testing allows for the determination of a material's compressive strength, maximum load-bearing capacity, yield strength, elastic modulus, and elastic limit among other properties.
Once these various factors and the values associated with a particular material are understood, it is possible to assess whether or not the material is suitable for a given application or whether it will fail under the given stresses.
When Are Compression Tests Used?
Compression tests are used to demonstrate how a material will respond to compression. They can be used to assess a material's plastic flow behavior and ductile fracture limits. They also determine how a material responds to crushing loads. Compression tests are crucial for assessing the elastic and compressive fracture characteristics of brittle or low-ductility materials.
The modulus of elasticity, compressive yield point, proportional limit, compressive strength, and maximum compressive strength can all be determined by compression experiments. These characteristics play a key role in figuring out if a material is suitable for a given application or will fail under a given set of stresses.
Where Are Compression Tests Applied?
There are several industries in which compression tests are used. Some of the main industries are listed below:
1. Aerospace and Automotive Industry
Compression tests are an essential part of the aerospace and automotive industry. They are used to measure the compressive strength of materials used in engine components, structural components, and other critical parts. For example, in the aerospace industry, compression tests are used to test the strength of materials used in the manufacturing of aircraft wings, fuselages, and engine parts. In the automotive industry, compression tests are used to test the strength of materials used in the manufacturing of engine blocks, crankshafts, springs, and other components.
2. Construction Industry
In the construction industry, compression tests are used to determine the compressive strength of concrete, cement, and other building materials. These tests are critical to ensure that the building materials meet the required strength standards and can withstand the weight and pressure of the structure. Compression testing is also used to measure the compressive performance of roofing panels, insulating boards, and sheet materials for building and to perform indentation testing for plasterboard, pipelines, and shotcrete.
3. Cosmetics Industry
Compression tests are an important part of the cosmetics industry, and are used in the following ways:
- Sprays and dispensing pumps are tested for actuator force.
- Lipstick, lip balm, and eyeliner break strength tests.
- Strength of eye shadows and powder compacts when compacted.
- Gauging the force required to distribute creams and lotions from bottles and sachets.
4. Electrical and Electronics Industry
In the electrical and electronics industry, compression tests are used to test the compressive strength of insulators, connectors, LCD screens, keypads, and other components. These tests are critical to ensure that the components can withstand the pressure and weight of other components and devices without breaking or degrading over time.
5. Medical Device Industry
The medical industry is another industry that has many uses for compression testing. Some of these include:
- The three-point bend test for needles.
- Metered-dose inhalers and pen injectors' actuator force tests.
- Scalpel and needle sharpness, insertion, and penetration force testing.
- Syringe plunger actuation and evaluation of "travel" force.
6. Packaging Industry
In the packaging industry, compression tests are used to test the compressive strength of cardboard, paperboard, and other packaging materials. These tests are critical to ensure that the packaging can withstand the weight and pressure of the products inside without breaking or tearing.
7. Paper and Board Industry
Compression tests are performed in the paper and board industry to test the compressive strength of cardboard.
8. Plastics, Rubber, and Elastomers Industry
Compression testing in the rubber, plastic, and elastomer industry mainly includes the identification of a polymer's compressive characteristics under load.
9. Safety, Health, Fitness, and Leisure Industry
Some of the applications of compression testing in the safety, health, fitness, and leisure industry include:
- Testing the effectiveness of tennis, golf, and cricket balls.
- Car seat safety harness compression testing.
How To Perform a Compression Test?
Compression testing works by subjecting a material to a compressive force until it reaches a specified deformation or fractures. The process typically involves the following steps:
- Preparation of the Sample: A sample of the material to be tested is selected and prepared according to the testing standard. The sample may be a cylindrical or cubical shape, depending on the requirements of the test.
- Mounting of the Sample: The sample is mounted between two plates or jaws of a testing machine. The machine may use hydraulic, pneumatic, or mechanical force to apply load to the sample.
- Application of Force: A compressive force is applied to the sample at a constant rate until it reaches a specified deformation or fractures. During the test, the applied force and the resulting deformation are measured and recorded.
- Analysis of the Results: The data collected during the test is used to calculate various properties of the material, including compressive strength, elastic modulus, and deformation characteristics.
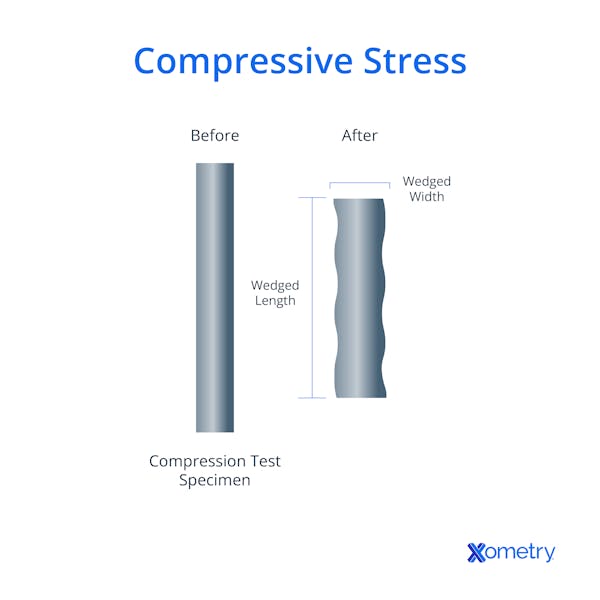
What Is the Compression Test Equipment?
Testing devices with universal compatibility are used for compression tests. With force capacities ranging from 0.02 N to 2,000 kN, these devices are typically offered in a wide range of sizes. A universal testing machine must be equipped with extensometers, application-specific platens, and testing software. A single machine may be adjusted to test any material within its force range by simply changing the fixturing, depending on the type of material being tested.
In a compression test, a sample of the material is sandwiched between two compression testing machine plates or jaws and compressed to a predetermined deformation or until it cracks.
What Are the Common Compression Testing Results
The compression testing results will vary from material to material, and also due to the desired properties for which the user is testing.
What Are the Types of Compression Testing?
The different types of compression testing are listed and discussed below:
1. Uniaxial Compression Test
Uniaxial compression testing is the most common and fundamental type of compression test. It involves applying a compressive load to a test specimen in a single axis, typically between two flat plates in a universal testing machine. This test is used to evaluate the compressive strength, modulus of elasticity, yield point, and deformation behavior of a wide variety of materials.
Uniaxial tests are particularly suitable for materials such as metals, plastics, ceramics, concrete, and composites. Specimens are usually cylindrical or cubical in shape, and the test is conducted at a controlled rate of deformation until failure or a specified strain is reached.
2. Spring Testing
Spring testing is a method of testing compression springs to measure their performance characteristics. A spring is placed in a compression test machine and compressed until all coils are touching, and the machine then determines the following characteristics:
- Solid Height: The height of the spring when fully compressed.
- Maximum Load: The amount of force required to fully compress the spring.
- Free Length: The length of the spring under no load.
- Spring Rate: The amount of force required to compress the spring a certain distance.
3. Top-load/Crush
Top-load testing is performed by applying a downward force to a specimen to measure how it resists crushing. This can be performed on any type of specimen but is commonly used in the packaging industry to test the crush resistance of containers such as plastic bottles, cartons, and jars.
What Are the Compression Testing Standards?
There are many industry standards for compression tests, maintained by different organizations, such as:
Metals
ASTM E9-89a – Standard Test Methods of Compression Testing of Metallic Materials at Room Temperature
Covers apparatus, specimens, and procedures for axial-load compression testing of metallic materials at room temperature.
Plastics
ISO 844:2021 – Rigid Cellular Plastics — Determination of Compression Properties
Specifies methods for determining compressive strength, stress at 10% relative deformation, and compressive modulus of rigid cellular plastics.
ISO 15527:2007 – Plastics — Compression-Moulded Sheets of Polyethylene (PE-UHMW, PE-HD) — Requirements and Test Methods
Specifies requirements and test methods for solid flat compression-moulded sheets of polyethylene without fillers or reinforcing materials.
ASTM D6713-01 – Standard Specification for Extruded and Compression Molded Shapes Made from Poly(Vinylidene Fluoride) (PVDF)
Covers requirements and test methods for extruded and compression molded shapes made from PVDF.
Rubber and Elastomers
ISO 7743:2008 – Rubber, Vulcanized or Thermoplastic — Determination of Compression Stress-Strain Properties
Specifies methods for determining the compression stress-strain properties of vulcanized or thermoplastic rubber using a standard test piece.
ASTM D575 – Standard Test Methods for Rubber Properties in Compression
Determines the compression-deflection characteristics of rubber compounds.
admet.com
ASTM C864-05 – Standard Specification for Dense Elastomeric Compression Seal Gaskets, Setting Blocks, and Spacers
Covers preformed dense elastomeric compression gaskets and accessories for use in sealing and glazing applications.
Paper and Board
ISO 9895:1989 – Paper and Board — Compressive Strength — Short-Span Test
Specifies a method for determining the compressive strength in the machine and cross directions of paper and board using a short-span compression tester.
Building Materials
BS EN 12365-2:2003 – Building Hardware — Gasket and Weatherstripping for Doors, Windows, Shutters and Curtain Walling — Part 2: Linear Compression Force Test Methods
Specifies test methods for determining the linear compression force of gaskets and weatherstripping used in building hardware.
What Are the Benefits of a Compression Test?
There are numerous benefits to compression testing, including:
- It is generally cost-effective when compared to other types of testing.
- It can be performed on a wide variety of materials.
- It is a well-established technique that can provide reliable results when performed correctly.
What Are the Limitations of a Compression Test?
There are some limitations to compression testing, including:
- Only gives information about a material’s compressive strength, and related properties, such as elastic modulus and yield point.
- It can be time-consuming.
- Testing specimens have to be prepared in a very specific way, which can be costly and affect the accuracy of the results.
- The accuracy of results can be affected by environmental factors, such as temperature, as well as operator error, such as loading the specimen incorrectly.
Are Compression Tests Accurate?
Yes, compression tests can be extremely accurate, as long as high-quality machines and testing procedures are used. There are various factors that can decrease the accuracy of tests though, such as inconsistent test setups, low-quality machines, or improperly calibrated machines. By mitigating these factors, it is possible to achieve very high accuracy with compression tests.
What Is the Difference Between Tension Testing and Compression Testing?
The difference between tension testing and compression testing is that with tension testing, a tensile stress, or pulling force, is applied. With compression testing, on the other hand, a compressive stress, or pushing force, is applied.
Summary
This article presented compression tests, explained what they are, and discussed their purpose and types. To learn more about compression tests, contact a Xometry representative.
Xometry provides a wide range of manufacturing capabilities, including 3D printing and other value-added services for all of your prototyping and production needs. Visit our website to learn more or to request a free, no-obligation quote.
Disclaimer
The content appearing on this webpage is for informational purposes only. Xometry makes no representation or warranty of any kind, be it expressed or implied, as to the accuracy, completeness, or validity of the information. Any performance parameters, geometric tolerances, specific design features, quality and types of materials, or processes should not be inferred to represent what will be delivered by third-party suppliers or manufacturers through Xometry’s network. Buyers seeking quotes for parts are responsible for defining the specific requirements for those parts. Please refer to our terms and conditions for more information.
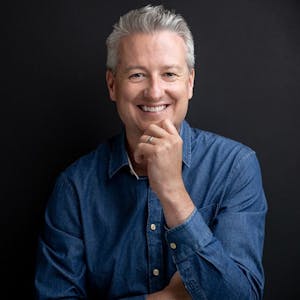