What Are Side Actions and Why Are They Needed?
Injection molding side actions are inserts (sometimes referred to as “features”) added to the mold in order to create undercut geometry. Undercut features are perpendicular to the main parting line and cannot be produced with a straight-pull mold, or in other words, by pulling apart the two halves of the mold and ejecting the part. When side actions are added to the mold, they allow material to flow around them to form the undercut feature. The side actions must then be removed manually or automatically to allow part ejection.
Side actions are beneficial because they increase the options for what part geometries your part can have. However, side actions can dramatically increase molding production costs, so it is helpful to consider whether you need them or whether you can avoid them by designing slot features.
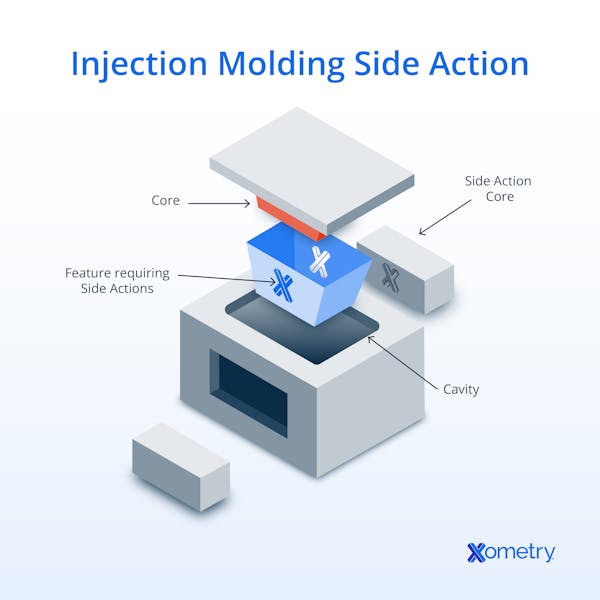
Injection molding side actions
Type of Side Action | Description | Use Case |
---|---|---|
Type of Side Action Slide | Description Slides create and release external undercut features by collapsing into place via a cam as the tool closes. It then pulls away as the tool opens. | Use Case Features on the outside of a part that are not formed with the main core and cavity of a tool |
Type of Side Action Lifter | Description Lifters create and release internal undercut features. Similar to slides, lifters move into place via a cam as the tool closes and move away as the tool opens. | Use Case Internal tab or overhanging features |
Type of Side Action Hand-loaded Core | Description Hand-loaded cores are substitutes for slides or lifters, and are manually placed features which are molded around and then manually removed from the part. These are replaced each cycle. | Use Case Hand loads are used for prototype and low-volume tooling as a cheaper alternative to automated slides and lifters. Hand loads can be adaptable to different part configurations in one tool. |
Type of Side Action Unscrewing Action | Description An unscrewing action is an automated motor or manual hand screwing that creates screw or threaded features. These actions prevent damage to the threads with careful unwinding between cycles. | Use Case These are necessary for consistent thread production. In low volumes, a hand-loaded core may be more cost effective. |
Type of Side Action Collapsible Core | Description Collapsible cores are mechanisms that release a circular undercut feature in a method similar to a lifter. These allow the actions to collapse inward, providing clearance for part ejection. | Use Case Features that have circular undercuts or large internal threads |
Injection Molding Resources
It should also be noted that because side actions do not follow the general tool direction, undercut features require draft angles specific to the action’s movement. For more design strategies, download our Injection Molding Design Guide.
You can also read our Ultimate Guide to Injection Molding to read about injection molding technology or view our plastic injection molding services page.
FREE Injection Molding Design Guide
