Tackling Drill Bits Part 02: Chipped Lips and Damaged Points
Have you or your loved ones been personally victimized by broken drill bits, bad tolerances or terrible finishes? In part 02 of tackling common drill bit issues machinists might run into, we look at chipped lips, damaged points, and more.
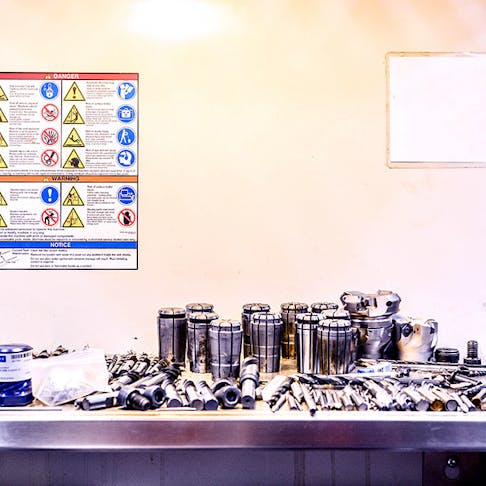
Have you or your loved ones been personally victimized by broken drill bits, bad tolerances or terrible finishes? In part 01 of our Tackling Drill Bits series, we looked at drill bit breakage, tool life, and oversized holes. In part 02 of tackling common drill bit issues machinists might run into, we look at chipped lips, damaged points, and more.
Fifth Issue: Broken Tang
A broken tang makes your drill bit about as useless as a screen door on a submarine. Check out the fit of your drill bit to be sure its seated real snug in the chuck, sleeve, or socket. If it is, you might be dealing with shank or socket damage, in which case you should look into replacement or repair of the injured party.
Sixth Issue: Damaged Point
Honestly, this one probably has to do with your drill bit handling. Maintain your perfect drill bit point by never using a hard object to tap your drill bit into the socket. Also make sure you are carefully removing and storing your drill bits after use. Always use a hammer made of soft lead, brass, plastic, etc. to secure your drill bit, and try to never drop or mishandle your drill bit. That perfect point is what keeps your tolerances tight, your holes even, and your workpiece immaculate, so it deserves a little coddling.
Seventh Issue: Rough Hole
If you’re ending up with a rough finish, you first need to be sure that you aren’t drilling with a dull point or (as always) the incorrect point grind. If you find you are, repointing or replacing are good friends of yours. You may also be pushing your workpiece or drill bit with an excessive feed, or possibly running your drill with insufficient or incorrect speed. All of these issues require some additional notes and calculation but are worth the time in the long run.
Eighth Issue: Web Splits
Not to put too fine a point on it, but if the center point of your drill is fracturing or splitting, you may just be dealing with a drill bit point that’s been thinned too much. It’s also possible that your drill bit is suffering from insufficient lip clearance. In both cases, a repoint or replace is in order. Also try recalculating and/or reducing your feed (do you see a pattern here?).
Tenth Issue: Broken Outer Corners
Like most other issues dealing with broken drill bits, excessive feed is a common culprit. If you’re sure you’ve got a well-regulated feed and aren’t pushing it too hard, take a good look at your coolant type and levels. Using the wrong coolant or not enough of it puts a lot of wear on your drill bit. The next place to look is the workpiece itself — sometimes scale or harder spots in your material can make a mess of your tools. If this is the case, there’s not a whole lot you can do with your actual tools to solve it. Our best advice is to maybe look on ProvenCut, and learn more about optimizing your setup for that specific project.
Hopefully, this short guide to drill bits has made your job(bers) easier to handle, or at least made it a tad easier to solve a few of those persistent machinist’s problems. As always, starting with quality tools is the first step to keeping your workplace efficient and issue-free — a major reason why we at Xometry supplies only keep the best quality equipment in stock. Calculating and regulating your speed and feed, and being sure that your equipment is clean are also easy ways to cut back on potential roadblocks.
If you happen to have more questions, or think of something you might want us to cover in future guides, always feel free to reach out to us at supplies@xometry.com.
Happy machining, y’all!
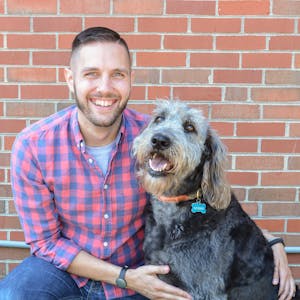