PEEK CNC Machining
Get instant quotes on custom PEEK machined parts with our Online CNC Machining Service. Make quick turn prototypes and production parts in days with free standard shipping on all US orders. ISO 9001:2015, ISO 13485, and AS9100D certified. ITAR registered.
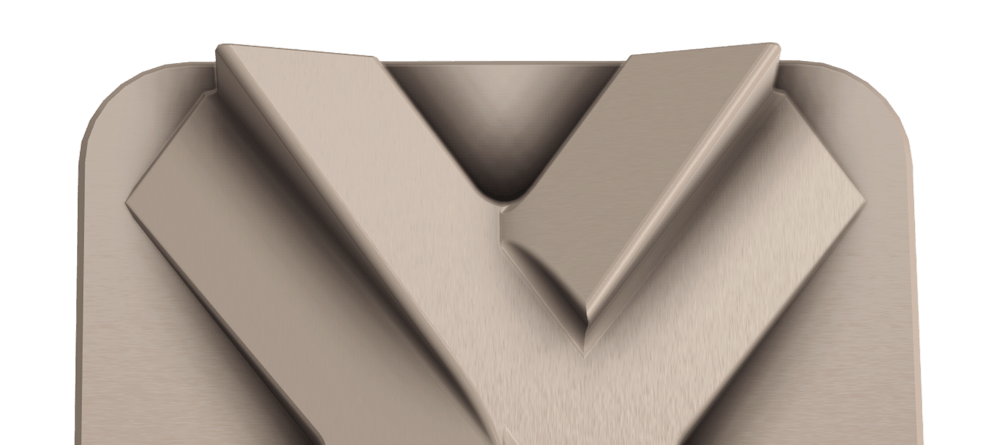
PEEK CNC Machining
PEEK or polyetheretherketone is an advanced engineering plastic with a long list of beneficial properties. These include resilience at high temperatures, abrasion resistance, biocompatibility, resistance to ultra-high vacuum, exceptional chemical resistance, and suitability for CNC machining.
PEEK is a semi-crystalline thermoplastic that can continuously operate at temperatures up to 260°C and is highly chemical resistant. It must be noted, however, that some acids like sulphuric acid will dissolve the material. CNC machining in PEEK is a common way to manufacture parts for use in extreme environments that require mechanical strength, chemical stability, and/or high-temperature resistance. Applications include components for the medical, aerospace, and automotive industries.
Application | Advantages | Disadvantages | Lead Time | Price | Tolerances |
---|---|---|---|---|---|
Application Bearings, washers and gears, spinal implants, surgical tools | Advantages Hydrophobic, minimal outgassing in high vacuum conditions, biocompatible | Disadvantages High cost, biocompatible but does not readily bond to bone | Lead Time Lead time for PEEK parts starts at 3 business days | Price High ($$$) | Tolerances Machining tolerances of +/- .001” (+/- 0.025 mm) are achievable |
Generic PEEK
Machining PEEK allows for a wide array of applications that take advantage of this material’s exceptional properties. PEEK has very few downsides when compared to other engineering plastics. One advantage that sets it apart is its heat resistance. It can operate at high temperatures for longer than most other plastics. Additionally, PEEK is hydrophobic, so it does not readily absorb water, and it also outgasses very little under vacuum conditions. This stability is a great asset. PEEK’s uses include medical applications for temporary implants all the way to aerospace components exposed to extreme vacuum.
Tensile Strength, Yield (MPa) | Elongation at Break (%) | Hardness (Shore D) | Heat Deflection Temperature (°C) | Glass Transition Temperature (°C) |
---|---|---|---|---|
Tensile Strength, Yield (MPa) 65-120 | Elongation at Break (%) 1.5-110 | Hardness (Shore D) 62-89 | Heat Deflection Temperature (°C) 182-210 | Glass Transition Temperature (°C) 143-155 |
USP Class VI PEEK (TECAPEEK)
PEEK rated for USP Class VI, such as TECAPEEK MT, are biocompatible variants specifically designed for use with medical technology. It is characterized by very high chemical resistance, resistance to various sterilization methods, and ability to retain its mechanical properties in high temperatures. Medical grade peek is often used for medical applications and devices where limited contact with skin and tissue will be needed. USP Class VI PEEK is also desirable for medical use due to its ability to sustain many sterilization cycles without degrading.
Tensile Strength, Yield (MPa) | Elongation at Break (%) | Hardness (Rockwell M) | Heat Deflection Temperature (°C) | Glass Transition Temperature (°C) |
---|---|---|---|---|
Tensile Strength, Yield (MPa) 96.5-110 | Elongation at Break (%) 30-50 | Hardness (Rockwell M) 94-99 | Heat Deflection Temperature (°C) 160 | Glass Transition Temperature (°C) 150 |
Peek GF30
PEEK GF30 is a 30% glass filled variant of PEEK. Compared to generic unfilled PEEK, GF30 has superior rigidity and increased mechanical strength. Glass reinforced PEEK also has increased dimensional stability and creep strength. This material is well suited for parts that experience high static loads in higher temperatures. PEEK GF30 is less suitable for bearing or wear applications due to the abrasive effect the glass fibers have on mating surfaces.
Tensile Strength, Yield (MPa) | Elongation at Break (%) | Hardness (Rockwell M) | Heat Deflection Temperature (°C) | Maximum Service Temperature (°C) |
---|---|---|---|---|
Tensile Strength, Yield (MPa) 101-157 | Elongation at Break (%) 2.2-5 | Hardness (Rockwell M) 103 | Heat Deflection Temperature (°C) 316 | Maximum Service Temperature (°C) 260-300 |
Finishes
PEEK parts are naturally an opaque grey or beige. Given PEEK’s polymeric structure, paints and coatings are difficult to bond to its surface. However, thanks to its inherent chemical resistance, it is often acceptable to leave parts as machined.
As Machined: PEEK is easily machined and can achieve smooth surface finishes. Xometry offers auto-quoting of surface roughnesses as small as 32uin Ra for PEEK but can quote even lower values with a manual review.
Bead Blast: Any undesirable tool marks may be removed by mechanically abrading the surface with glass beads.
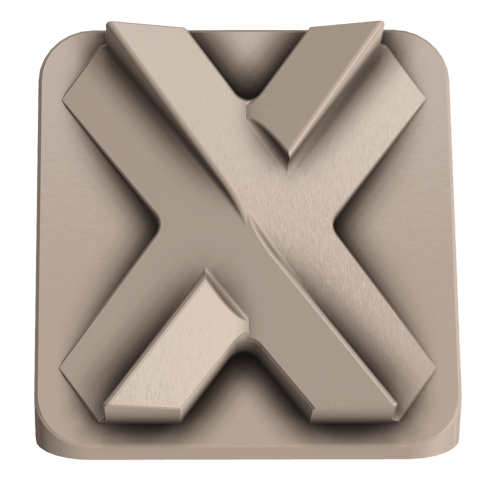
Cost-saving Design Tips
Due to the material’s high cost, manufacturing overhead costs must be minimized. One method to help manage the cost of CNC machining in PEEK is by requesting annealing during fabrication. This may reduce surface and internal cracking, which will reduce scrap rate and reduce overall costs for the manufacturer. Other design strategies can be found in our CNC Machining Design Guide.
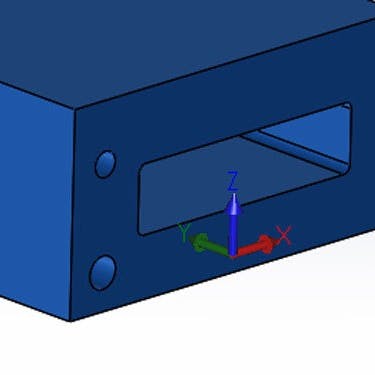