Phenolic Machining Services
Get instant quotes on custom phenolic parts with our Online Phenolic Machining Service. Make quick turn prototypes and production parts in days with free standard shipping on all US orders. ISO 9001:2015, ISO 13485, IATF 16949:2016, and AS9100D certified. ITAR registered. Subject to availability. Xometry doesn't guarantee that we can provide this service at any given time.
Xometry offers high quality phenolic machining services for a variety of materials and applications. Phenolics are materials made with layers of either paper, canvas, linen, or other woven fabric bound together with phenolic resin. Xometry offers custom fabrication of laminates made with phenolic resin, epoxy resin, and other fiber-reinforced composite blends. Phenolic material is non-metallic, insulative, strong, and is easily worked, making it ideal in machining applications. Phenolic materials are used for insulative or non-metallic structural components, terminal boards, high speed or high wear components, countertops, and much more.
What is Phenolic Resin?
Phenol-formaldehyde resin (phenolic resin, phenolic plastic, or uncommonly found as phenoplast) was one of, if not the first commercial synthetic polymer. It was developed by Dr. Leo Baekeland in 1907 under the name Bakelite®, where wood fiber was mixed with phenolic resin binder to create a tough, flame-resistant, and workable alternative to woods and metals.
Phenolic resin is created by reacting phenol (a benzene ring with an alcohol, or -OH group, attached) with formaldehyde under heat and pressure with a catalyst in a so-called condensation reaction. As its name implies, The reaction forms water when adjacent CH2OH groups “condense” to CH2 groups, kicking out water and thermosetting the polymer into a permanent interlinked 3D network of resin. The ratio of phenol to formaldehyde, along with variations to catalysts, working temperatures, and other reaction variables will change the molecular weight and crosslinking percentage, thereby affecting material properties.
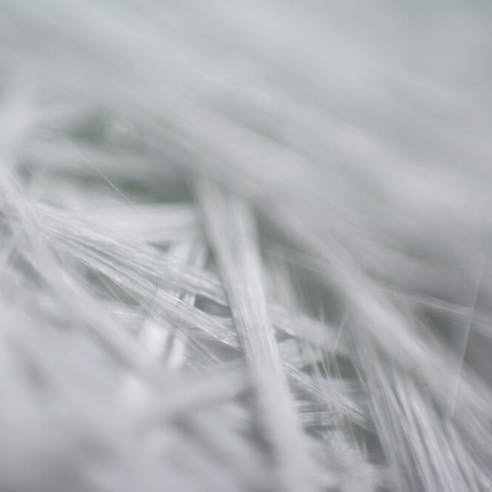
This reaction is used to make the phenolic resin binder that will glue sheets or fabric-like material together. These include paper, canvas, linen, fiberglass, wood fibers, and many other materials. This reaction can take place in molds so that the material thermosets these sheets into desirable stock shapes. Note that some phenolic grades are restricted to sheet stock and are not offered in other shapes due to its fabrication process or type of fabric.
Also note that there are other laminate composites that may not use phenolic resin but are commonly found alongside (and even wrongfully called) phenolic materials–for example, Garolite®, a brand name of laminated resin products, is commonly found using epoxy resin but is often sold alongside phenolic material despite most forms no longer containing the polymer. Norplex-Micarta, another laminate brand, produces its Micarta® products that come in dozens of grades where some are phenolic-based while others are silicone-based, melamine-based, epoxy-based, or based on some other thermoset material.
Types of Phenolic Grades
Phenolic material comes in a variety of types, or grades. Xometry offer phenolic machining in the following types:
- Paper Reinforced Phenolic
- Canvas Phenolic and Linen Phenolic
- N-1 (Nylon Reinforced Phenolic)
- G-3 (Glass reinforced Phenolic)
- Non-Phenolic Fiber-Reinforced Composites
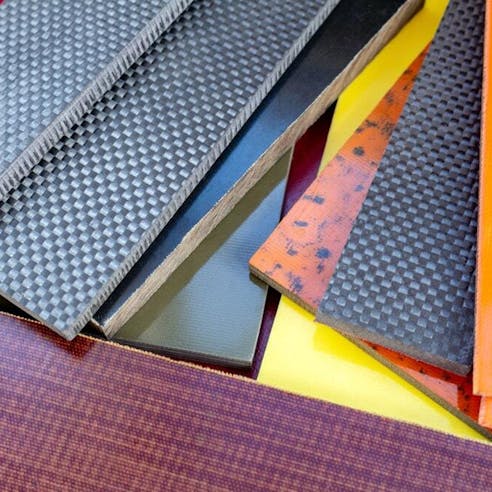
Paper Reinforced Phenolic
As its name suggests, paper reinforced phenolic is made using wood-fiber sheets layered in phenolic resin to create a strong, insulative, yet thin composite. While not typically suited for structural or weight-bearing components, paper phenolic is ideal for fireproof and insulative applications where a small profile counts. The National Electrical Manufacturers Association (NEMA) has several grades of general-use paper reinforced phenolics denoted by letter signifiers, where each signifier denotes a unique blend of mechanical, electrical, and chemical performance characteristics:
- X = Paper Phenolic Resin – Mechanical Grade
- XP = Paper Phenolic Resin – Mechanical Grade – Hot Punch-able Grade
- XPC = Paper Phenolic Resin – Mechanical Grade – Cold Punch-able Grade
- XX = Paper Phenolic – General Purpose Grade
- XXP = Paper Phenolic Resin – Mechanical Grade – Hot Punch-able
- XXX = Paper Phenolic Resin – Electrical Grade
Electrical grade paper reinforced phenolic material is ideal for printed circuit boards (PCBs) and electrical insulative components, where it is often clad with copper for integrated circuit logic and other materials that improve its performance in electronic applications. NEMA also has signifiers for grades of phenolic manufactured with flame-retardant additives to improve safety in electronics, symbolized with the “FR” signifier:
- FR-1 = Fire Retardant – Paper Phenolic – Mechanical Grade – Hot Punch-able
- FR-2 = Fire Retardant – Paper Phenolic – Electrical Grade – Cold Punch-able
There is also a paper-reinforced epoxy laminate similar to the above grades, but is technically not a phenolic material. Its NEMA designation is:
- FR-3 = Fire Retardant – Paper Epoxy – Electrical Grade
Canvas Phenolic and Linen Phenolic
Cloth reinforced phenolic is made using either canvas or linen fabric layered in phenolic resin to create an exceptionally durable composite for general purpose, machining, and flammable applications. Canvas and linen have better machining qualities, strength, moisture resistance, and create less noise than paper phenolics, and are less abrasive than fiberglass-based laminates. Linen phenolic is better suited towards fine-detail machining applications thanks to its finer fabric weave, but is also more expensive than canvas phenolic as a result. NEMA has designated several grades of canvas and linen phenolic material for machining, electrical, mechanical, and general-purpose applications each with their own unique blends of fabric type and material properties (where “L” denotes linen and “C” denotes canvas):
- L = Cotton Phenolic Resin – Machine-able Grade
- LE = Cotton Phenolic Resin – Electrical Grade
- C = Cotton Phenolic Resin – Mechanical Grade
- CE = Canvas Phenolic Resin – General Purpose Grade
The only major limitation with these kinds of phenolic are the large amount of foul-smelling dust released when machined, where this dust is a risk to operators if inhaled.
N-1 (Nylon Reinforced Phenolic)
Also found under its brand name NP101 by Norplex-Micarta, N-1 nylon reinforced phenolic is a composite made with spun nylon fabric bound with modified phenolic resin. This composite benefits from good electrical properties even in high humidity conditions and good impact resistance, and it meets the specification covering thermosetting plastic laminated insulation materials for mechanical and electrical military applications (Mil-I-24768/9). Its only major limitation is its tendency for creep/cold flow deformation.
G-3 (Glass reinforced Phenolic)
Also found as Micarta® NP-504, G-3 glass reinforced phenolic is made using woven glass fabric and high-temperature phenolic resin. As a material it has superior strength in compression, in tension, while flexing, and in impacts. It retains these qualities even at high temperatures, making it ideal for oven and structural applications where it will regularly experience harsh conditions. NEMA designates glass reinforced phenolic as:
- G-3 = Woven Glass – Phenolic Resin – General Purpose Grade.
Glass reinforced phenolic meets Mil-I-24768/18 specifications and is typically used for acid-resistant gaskets, high temperature components, and more. The only limitation of this material is its price and limited availability when compared to other grades.
Non-Phenolic Fiber-Reinforced Composites
Some materials are sold alongside phenolic material despite not actually having phenolic resin in their formulation. They are similar in characteristics and are often made by the same manufacturers.
G7 (Glass Reinforced Silicone)
G-7, or glass reinforced silicone resin-based laminate is a material made by layering continuous woven glass fabric in silicone resin. It is denoted by NEMA as:
- G7- Woven Glass Silicone Resin – General Purpose Grade
Exceptionally arc and temperature resistant, G-7 is ideal for high-temperature electrical applications, high-friction environments, heating/appliance insulation, electrical insulation, bushings, lock bolt washers, and more. It is self-extinguishing, moisture resistant to up to 428°F, and has good mechanical, electrical, and insulative properties. G-7 meets Mil-I-24768/17 specifications, and remains strong in high-temperatures for extended periods such as. Its only major downside is that it does not keep its strength over time in low temperature environments as well as other resin-based laminates.
G10 (Glass Reinforced Epoxy) & G11 (Glass Reinforced Epoxy)
Glass reinforced epoxy resin laminates are highly popular materials, and are more commonly known by their brand name Garolite®. They are made using fine-weave fiberglass cloth that is soaked in epoxy resin, stacked, and then compressed into sheets. These materials have extremely high strength and dimensional stability, where G-10 is slightly stronger than G-11 but G-11 is a better insulator and can withstand higher temperatures. They are some of the most common laminates used in manufacturing thanks to their impressive strength, low moisture absorption, insulative properties, and chemical resistances even at high temperatures. They are commonly used in electrical insulative applications in motors, housing, and more. NEMA has designated these materials with the generic name:
- G-10, & G-11 = Woven Glass – Epoxy Resin – Electrical Grade
These laminates were originally manufactured to replace phenolic material in PCBs, however the only issue with epoxy-based materials like these is their flammability risk, where they not only burn violently but also off gas toxic byproducts. This prevented G10 and G11 from being used in high risk electrical applications, and is why two fire-retardant grades were developed to meet this need. They are essentially the same as G10 and G11 but include flame retardants that prevent ignition risks. These grades are designated by NEMA as:
- FR-4, & FR-5 = Fire Retardant – Glass Epoxy Resin – Mechanical Grade
FR-4 and FR-5 are now the most common material used in PCB manufacturing, and are the thin green boards that most people think of when imagining circuit boards.
The main issue with these materials is that they are difficult to machine, requiring diamond or other hard-tipped bits to effectively cut. These materials also cannot be injection molded due to how it is manufactured, meaning designers are generally limited to machining when using this material.
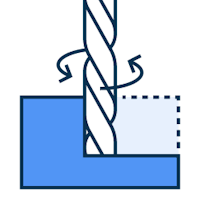
Ready to start making custom phenolic machined parts?
Advantages of Phenolic Machining with Xometry
Creating custom fabrications with phenolic machining at Xometry offers customers accurate, highly durable parts with short lead times and exceptional quality.
- Dimensional Stability
- Excellent Dielectric Strength
- Mechanical Strength
- Close Tolerances
- Long Run Production
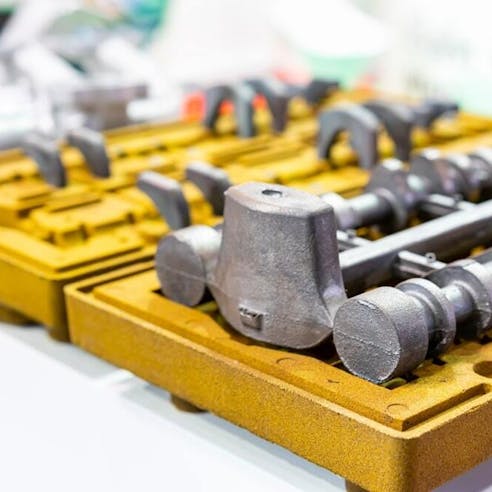
Dimensional Stability
Phenolic material remains dimensionally stable throughout machining. It does not burn or melt like plastic materials, and it retains its shape even when subjected to increased temperatures and humidity.
Excellent Dielectric Strength
Phenolic material will remain insulative for much longer than other materials, especially when experiencing large electric potentials. The dielectric strength of phenolic laminates is why they are so vital for electronics applications where short-circuiting and other issues must be minimized to increase effectiveness and safety.
Mechanical Strength
The mechanical properties of phenolics are such that they do not easily break when impacted, bent, or put under heavy loads. While pure phenolic can be quite brittle, specific grades such as canvas phenolic or glass-reinforced phenolic are strong, hard, and durable enough to be used in high wear components like gears and structural components.
Close Tolerances
Fine-weave phenolic material like linen phenolic can achieve a high level of detail and can achieve close tolerances.
Long Run Production
The stability and durability of phenolic makes it ideal for long production runs where multiple fabrication steps are performed on the same workpiece across manufacturing processes.
Types of Machining Processes used with Phenolic Materials
Phenolic can be used in a variety of machining processes to be brought to shape, and Xometry can provide both the material and the equipped technicians to bring your part to life
- Phenolic CNC Machining Services
- Phenolic Deburring
- Phenolic Grinding & Sanding
- Phenolic Laser Cutting Services
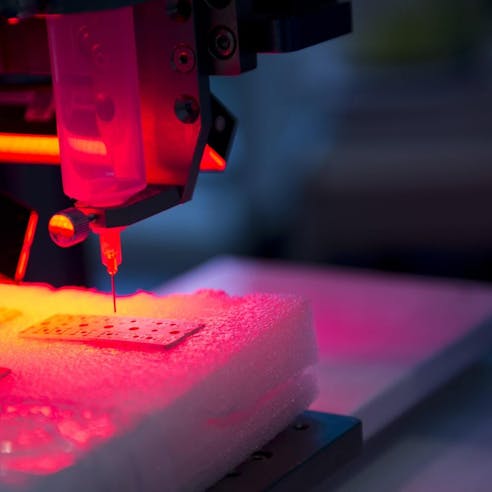
Phenolic CNC Machining Services
CNC machining services are the ideal manufacturing methods for this material. Phenolic is readily CNC machined without lubricants; this includes milling, turning, CNC cutting, and any other computer-controlled machining process. Some stronger types of phenolic require carbide or diamond tipped bits, as well as high spindle speed to achieve fine details and the right finish throughout production. Xometry’s manufacturing experts within our Manufacturing Supplier Network know the right tools and procedures to provide clean, highly accurate parts without compromising quality.
Phenolic Deburring
Unlike other materials, phenolic fabric fibers fray and leave a fuzzy burr on the cutting edge that can be tricky to remove. This type of burr must be removed with laborious hand-sanding, or cryogenic equipment/dry tumbling if in large production quantities. Xometry’s experts will ship out parts with clean and precise edges that match up to your specifications and our quality standards.
Phenolic Grinding & Sanding
Phenolic can be ground and sanded without lubricants. It can be dry-ground or sanded with belt, disc, or centerless tools, but note that it can take more time to polish phenolic than wood or metal. Also note that operators must wear proper PPE and clean workspaces regularly when grinding or sanding phenolic, as the generated dust is dangerous if inhaled.
Phenolic Laser Cutting Services
Phenolic can be laser cut, given the right powered laser, assist gas, cutting speeds, and the thickness of the material. Phenolic can experience charring, blistering, and heat-affected zones (HAZ) in suboptimal manufacturing set ups like those found in other resin and plastic materials. Xometry will ensure these defects do not occur by leveraging our Manufacturing Supplier Network for the right laser system and experienced technicians to provide the best possible quality laser cuts on phenolic material.
Common Uses and Products for Phenolic Machined Parts
Here are some common applications for machined phenolic parts in industry:
- Billiard Balls
- Countertops
- Printed Circuit Boards
- High-wear Components
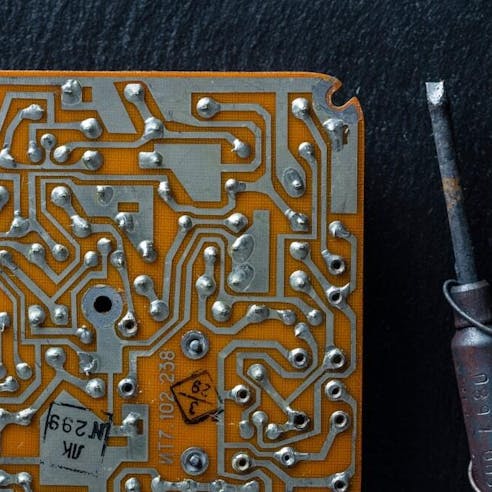
Billiard Balls
Professional billiard balls are made out of phenolic resin, as it is moldable, uniformly dense, and can achieve high gloss and vibrant colors.
Countertops
Phenolic countertops are tough. They will not be affected by hot or cold temperatures, are scratch, impact, and chemical resistant, and will not warp or stain. Phenolic countertops retain their aesthetics for much longer than other materials, and are ideal for scientific or industrial work surfaces that will experience harsh environments.
Printed Circuit Boards
Phenolic resin laminates are vital to the electronics industry, and are currently still one of the best materials for printed circuit boards thanks to their insulative properties and high dielectric strength.
High-wear Components
High strength phenolic materials like canvas and glass-reinforced phenolics are fantastic non-metal alternatives for gears, cams, and other high wear components. They can withstand both the repeated stresses and heat of these applications without risk of failure, and also offer insulative properties where large electrical potentials can risk damaging susceptible parts.
Alternatives to Phenolic Machining
If phenolic machining is not the right process for your project, Xometry offers a wide range of alternatives to choose from.
- Urethane Casting
- Custom Plastic Injection Molding
- Plastic 3D Printing
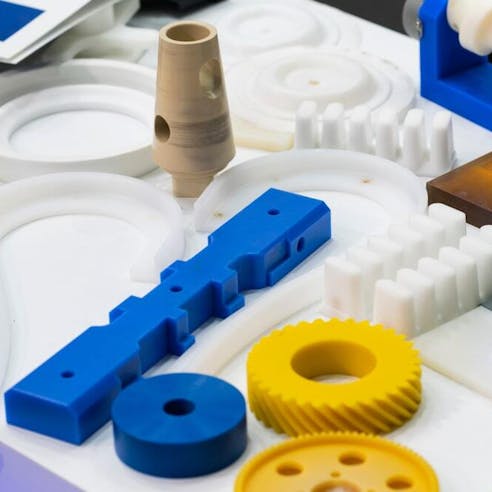
Urethane Casting
Urethane casting provides end-use, rigid, flexible, and rubber parts with production-level quality for low-volume production. Learn more by viewing Xometry’s Urethane Casting Service.
Custom Plastic Injection Molding
Injection molding is the most cost-effective way to make a plastic part at scale, quickly making hundreds or thousands of parts in a workday with consistent quality across every part. It has the widest variety of materials, colors, cosmetics, polishes, and surface textures when compared to CNC machining or even 3D printing. Learn more by viewing Xometry’s Custom Plastic Injection molding Service.
Plastic 3D Printing
Plastic 3D printing is one of the fastest and most cost-effective methods available for the iterative design, prototyping, and production of custom parts. Additive manufacturing allows for little to no loss in material and a massive range of engineering materials to choose from including fire-retardant and electrically insulative plastics. Learn more by viewing Xometry’s Plastic 3D Printing Service.
Why Choose Xometry for Phenolic Machining?
Endless Options
Choose from millions of possible combinations of materials, finishes, tolerances, markings, and certifications for your order.
Easy to Use
Get your parts delivered right to your door without the hassle of sourcing, project management, logistics, or shipping.
Quality Assurance
We are ISO 9001:2015, ISO 13485, IATF 16949:2016, and AS9100D certified.
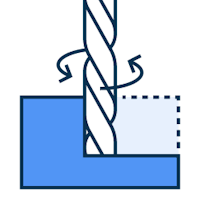