Production CNC Machining Services
High Quality production CNC Machined prototypes and production parts in days | AS9100D | ISO 9001:2015 | ISO 13485 | IATF 16949:2016 | ITAR Registered | Free standard shipping on all US orders
Production CNC machining is a cutting-edge manufacturing process that has changed the production of high-quality components for the better with its precision and efficiency. The importance of production CNC machining lies in its capacity to reliably produce high-quality parts, even when manufacturing large quantities. CNC machines can perform complex operations in a single setup, drastically reducing production time and costs. This efficiency not only streamlines the manufacturing process but also enables manufacturers to respond quickly to market demands, gain a competitive edge, and optimize their overall operations.
Production CNC Machining Process
Xometry’s production CNC machining process is a carefully structured and well-coordinated system that ensures the creation of high-quality components with precision and efficiency. By incorporating the latest technology, skilled expertise, and rigorous quality control measures, we guarantee the production of high-quality components that meet and exceed our client’s expectations. Whether for prototyping or large-scale production, our commitment to excellence ensures that our CNC machining services stand out in the competitive manufacturing landscape.
Starting from project planning and design, through programming and tooling, to full-scale production, each step is meticulously executed to meet the highest standards of quality.
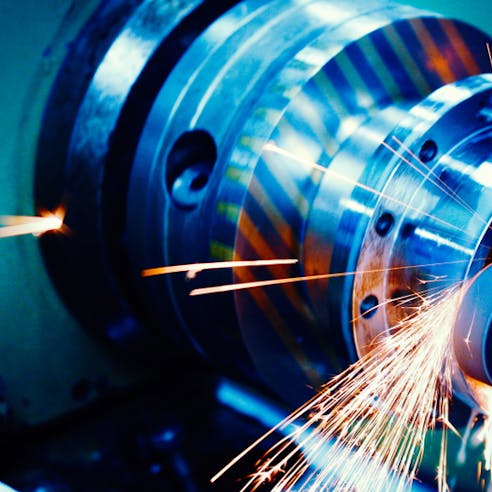
Materials and Technologies Used for Production CNC Machining
At Xometry, we offer a comprehensive and cutting-edge production CNC machining service that caters to a diverse range of industries and applications. Our expertise lies in utilizing advanced CNC machines, automation, and multi-axis capabilities to optimize the manufacturing process for both metals and plastics.
We understand the importance of material selection in CNC machining to meet specific project requirements. Our CNC machining service covers an extensive variety of materials, including metals (such as: aluminum, stainless steel, brass, copper, and titanium) and plastics (such as: ABS, polycarbonate, acrylic, nylon, and PEEK).
Our CNC machining service is powered by state-of-the-art CNC machines equipped with advanced automation features. The automation capabilities enable us to streamline the manufacturing process, reducing production time and cost significantly. Our CNC machines are also equipped with advanced multi-axis capabilities, including 3-axis, 4-axis, and 5-axis machining. These technologies allow us to achieve precise and intricate cuts, curves, and contours, delivering exceptional results that meet the most demanding design specifications.
Advantages of Production CNC Machining
Production CNC machining offers a multitude of advantages that make it a preferred manufacturing method for various industries. These benefits are listed below:
- Speed
- Accuracy
- Repeatability
- Cost-Effectiveness
- Versatility
- Flexibility
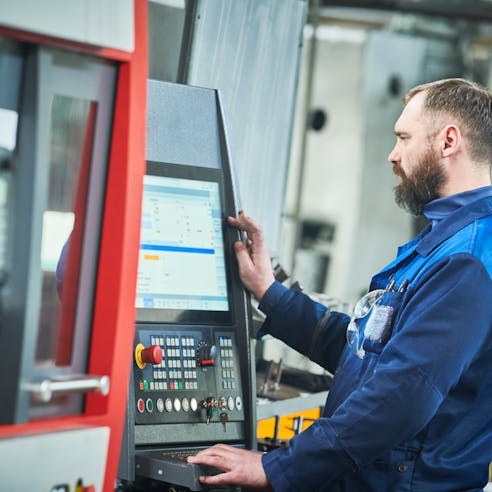
Speed
Computer-controlled machines can execute complex operations swiftly, significantly reducing production time compared to traditional manual machining methods. This increased speed allows for quicker project turnaround, meeting tight deadlines, and enabling businesses to respond rapidly to changing market demands.
Accuracy
The use of advanced computer control ensures that every cut, hole, or contour is executed with exceptional accuracy. The machines follow precise instructions from the programmed code, resulting in components with consistent and exact dimensions. This level of accuracy is crucial in industries in which tight tolerances are essential for proper fit and functionality.
Repeatability
CNC machining can reproduce multiple parts with the same high level of accuracy and precision repeatedly. This is particularly advantageous for large-scale production, as it ensures consistent quality across all units.
Cost-Effectiveness
Despite the initial investment in CNC machinery and programming, CNC machining proves cost-effective in the long run. Automation and precision reduce material wastage and minimize the need for manual labor. Moreover, the high-speed production capabilities result in higher output, driving down per-unit costs. The cost-effectiveness of CNC machining makes it a financially viable choice for both small-scale prototyping and large-scale production runs.
Versatility
Whether working with metals, plastics, or even composites, CNC machines can handle various materials with ease. Additionally, the multi-axis capabilities of CNC machines allow for the creation of intricate and complex shapes that may be challenging or impossible to achieve with traditional methods.
Flexibility
CNC machining flexibility extends to the ability to integrate with other manufacturing processes, such as additive manufacturing and finishing, to produce fully-finished and assembled components.
Disadvantages of Production CNC Machining
While production CNC machining offers numerous advantages, it is essential to also consider its potential disadvantages:
- High Initial Cost
- Limited Material Flexibility
- Long Setup Time
- Complex Geometries
- Maintenance and Training
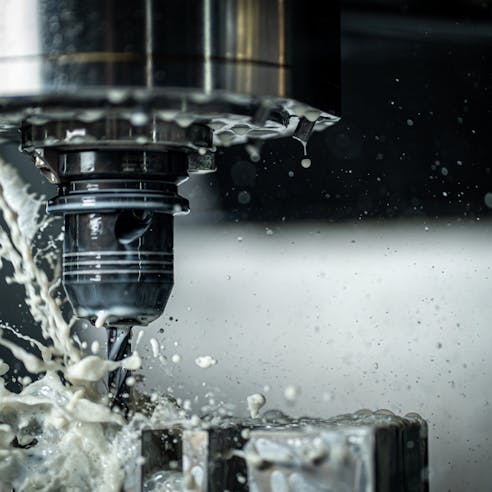
High Initial Cost
One of the primary disadvantages of CNC machining is the high initial cost of investment. Acquiring CNC machines and the necessary software can be expensive, especially for small businesses or startups. The capital expenditure required to set up CNC machining facilities might deter some companies from adopting this technology, particularly if they have limited budgets
Limited Material Flexibility
While CNC machining is versatile in handling various materials, it may still have limitations in terms of working with certain specialized materials or composites. Some high-performance materials or exotic alloys may pose challenges in the machining process due to their unique properties, such as high hardness or brittleness. In such cases, alternative manufacturing methods might be more suitable.
Long Setup Time
CNC machining often requires thorough planning and setup before the actual production can begin. Preparing the CNC machine, programming the code, selecting appropriate tools, and ensuring proper fixturing can be time-consuming, especially for complex components or small batch sizes. This setup time may not be as efficient for low-volume production or quick turnaround projects.
Complex Geometries
While CNC machines offer multi-axis capabilities and are highly precise, machining extremely intricate or complex geometries can be challenging and time-consuming. Some designs may require multiple setups or specialized tooling, which can increase production time and costs. In such cases, alternative manufacturing methods like additive manufacturing or casting may be more suitable for achieving complex shapes.
Maintenance and Training
Maintaining CNC machines and ensuring they operate at optimal performance requires regular maintenance and skilled personnel. The upkeep of CNC machines can add to the operational costs. Additionally, training operators and programmers to utilize CNC machines effectively requires time and investment in workforce development.
Production CNC Machining Industries
Xometry’s production CNC machining services cater to a wide range of industries such as:
- Aerospace
- Automotive
- Electronics
- Medical
- Industrial
- Defense and Military
- Robotics and Automation
- Energy and Renewable Energy
- Consumer Goods
- Telecommunications
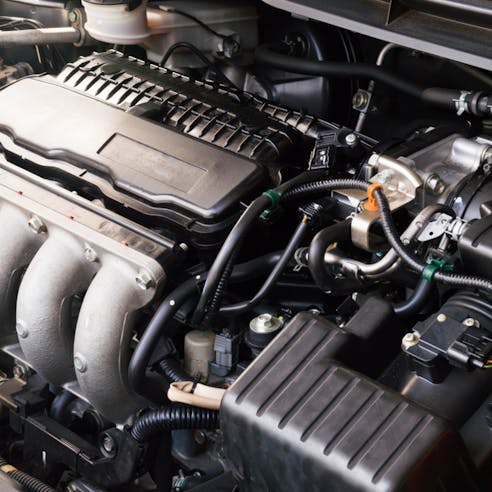
Aerospace
The aerospace industry demands precision and reliability in components, making CNC machining a natural fit. From engine parts and structural components to intricate aerospace prototypes, our CNC machining services ensure strict adherence to tight tolerances and deliver parts with excellent performance and durability.
Automotive
CNC machining plays a crucial role in the automotive sector, in which precision and efficiency are paramount. We can manufacture critical automotive components, such as engine parts, transmission components, chassis parts, and other intricate pieces that contribute to the overall performance and safety of vehicles.
Electronics
The electronics industry relies heavily on small, complex, and precise components. Our CNC machining services offer the capability to produce intricately designed electronic parts, including heat sinks, connectors, housings, and other components essential for electronics manufacturing.
Medical
In the medical industry, precision and quality are critical for devices and equipment. CNC machining allows us to manufacture medical components, such as: surgical instruments, implants, prostheses, and medical device parts, with the highest level of accuracy and consistency.
Industrial
The industrial sector encompasses a broad range of applications, and CNC machining is well-suited to meet diverse industrial needs. Our CNC machined parts find applications in industrial machinery, automation systems, tooling, and other equipment in which precision, reliability, and durability are vital.
Defense and Military
The defense and military industries require components that can withstand rigorous conditions. Our CNC machining services deliver high-quality parts that meet the stringent standards and durability requirements of military applications.
Robotics and Automation
With the growing emphasis on robotics and automation, CNC machining plays a significant role in producing components for robotic systems, sensors, actuators, and automation equipment.
Energy and Renewable Energy
CNC machining is vital in the energy sector, in which components for power generation, turbines, wind energy systems, and other renewable energy applications require precision and reliability.
Consumer Goods
From high-end consumer electronics to specialized tools and gadgets, CNC machining is essential for manufacturing intricate and high-quality components found in consumer goods.
Telecommunications
CNC machining aids in producing critical components for telecommunications infrastructure, including antennas, connectors, and other specialized parts.
Alternatives to Production CNC Machining
Xometry offers alternative processes to CNC machining that you can consider. These include:
- 3D Printing
- Traditional Machining
- Die Casting
- Injection Molding
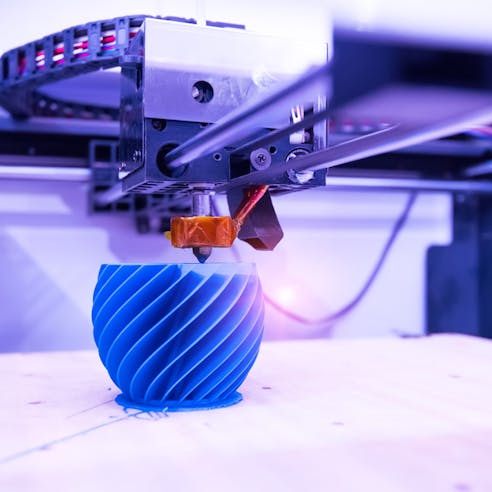
- 3D Printing: 3D printing or additive manufacturing, is a process that produces three-dimensional objects layer by layer. This method allows for incredible design flexibility. It is particularly advantageous for rapid prototyping, enabling designers to quickly iterate and test various designs before committing to large-scale production. However, it is worth noting that 3D printing may have limitations in material selection compared to traditional manufacturing methods and might not achieve the same level of surface finish as CNC machining.
- Traditional Machining: Traditional machining refers to subtractive manufacturing processes in which material is removed from a workpiece to create the desired shape and form. This time-tested method offers a wide range of material options. It is well-suited for small to medium-sized production runs and delivers consistent results. However, traditional machining may have longer lead times and setup times compared to some modern manufacturing methods, which could be a consideration for time-sensitive projects.
- Die Casting: Die casting is a metal casting technique in which molten metal is injected into a mold at high pressure. It is commonly used for mass production of metal parts with excellent surface finish and dimensional accuracy. The process enables the creation of intricate and thin-walled geometries. It is a cost-effective option for large production runs, as it allows the creation of multiple parts simultaneously. However, die casting has higher initial tooling and setup costs, making it less suitable for low-volume production scenarios. Additionally, it is limited to metal materials, which may not be ideal for certain applications that require different material properties.
- Injection Molding: Injection molding is a manufacturing process for producing parts by injecting molten material, typically plastic, into a mold. It is widely used for high-volume production of plastic parts with excellent surface finish and tight tolerances. The process offers fast production cycles and is particularly suitable for producing complex geometries and intricate designs. However, similar to die casting, injection molding may have higher initial tooling costs, which could make it less viable for low-volume production. Additionally, it is limited to plastics and may not be suitable for applications that require metal or other materials.
Why Choose Xometry for Production CNC Machining Services?
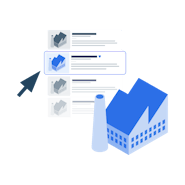
Endless Options
Choose from millions of possible combinations of materials, finishes, tolerances, markings, and certifications for your order.
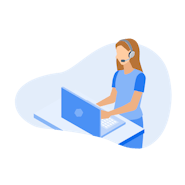
Easy to Use
Get started with our easy-to-use platform and let our experts take care of managing the project from locating the right manufacturing partner to delivery logistics.
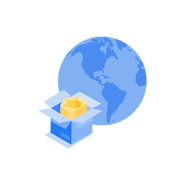
Vetted Network
We are ISO 9001:2015, ISO 13485, and AS9100D certified. Only the top shops that apply to become Suppliers make it through our qualification process.