Swiss Machining Services by Xometry
Xometry offers the highest quality Swiss Machining services and can assist in the production of parts with intricate and complex geometries and excellent surface finishes. Subject to availability. Xometry doesn't guarantee that we can provide this service at any given time.
Swiss machining is a material removal process that makes possible the rapid and accurate machining of small, complex parts. A rotating workpiece is held at one end to control both its longitudinal and rotational motion. Near the other end, the work is supported by a guide bushing. This allows cutting operations both along the axis of rotation and perpendicular to it, even on small diameter bar stock that might not be stiff enough for machining on a conventional lathe set-up. A wide range of plastics and metals can be processed on a Swiss machine.
Xometry offers the highest-quality CNC Swiss machining services for a variety of industries and applications. From the fabrication of surgical and dental instruments to the manufacture of pipe fittings and nozzles, Xometry’s extensive experience in the machining industry generally, and with Swiss machining in particular, ensures that your Swiss-machined parts are made to the highest standards of quality and excellence.
What Is Swiss Machining?
Swiss machining is a material removal process that uses an advanced CNC-controlled sliding-head lathe to perform cutting operations both along and perpendicular to the axis of rotation of the workpiece. In Swiss machining, only the portion of the bar stock currently being machined is exposed, unlike the case with traditional lathes where the majority of the bar stock is exposed and fixed on one or two ends. Additionally, the parts made and the machines themselves are often small. Thus, the cutting tool’s stick-out length is often minimized.
Minimal stick out of both the workpiece and tool enables both to be held securely which reduces vibrations and leads to higher precision and increased stability in Swiss machining. Moreover, Swiss lathes can complete multiple machining processes in a particular “zone” simultaneously and can cut features both along the axis of the workpiece and perpendicular to it. The ability to cut more complex parts, coupled with higher precision and efficiency, makes Swiss machining the right fabrication method for parts and components in numerous industries like automotive, medical, and aerospace.
Xometry’s Swiss machining capabilities are compatible with many different materials and are suitable for a variety of applications like surgical and dental instruments, bushings for connecting rods, turbine blades, and more. Our extensive network of partner manufacturers gives us the capability to supply the Swiss-machined parts you need, when you need them, anywhere in the world.
Materials That Can Be Swiss Machined
Practically any material that can be machined using a standard lathe or mill can be Swiss machined. Some examples of materials that can be used are listed below:
- Alloys
- Aluminum
- Brass
- Copper
- Stainless Steel
- Special Alloys
- Precision Steel
- Titanium
- PVC
- Acetal
- Nylon
- Delrin®
- PTFE
- UHMW
- Ultem®
- PEEK
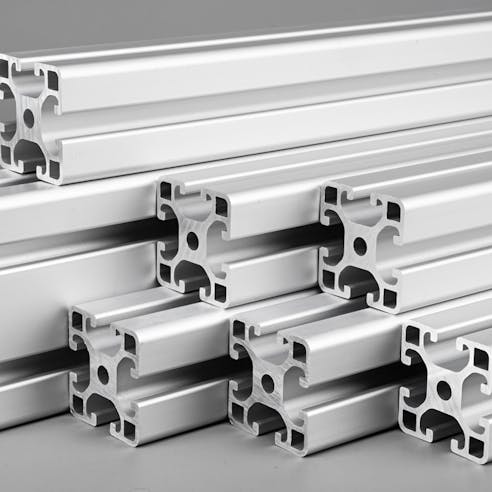
Alloys
Alloys of such metals as: aluminum, titanium, copper, iron, and nickel can easily be fabricated into parts using a Swiss lathe. Alloys are commonly used for various applications due to their improved mechanical properties compared to their pure metal counterparts. Swiss machining is a reliable method to fabricate complex parts out of various alloys.
Aluminum
Aluminum is a common workpiece material used in Swiss machining. It has a high machinability rating, making it a great choice. The process is often used to make aerospace parts out of aluminum. Parts such as engine components like fuel line fittings, cams, and more are often made from aluminum using Swiss machining processes.
Brass
Brass is commonly used in Swiss machining to make brass parts for hardware. Examples include: screws and washers, valve bodies, lock cylinders, electrical terminals, and more.
Copper
Copper is often used in Swiss machining to make parts for heat exchangers, bearings, electrical connectors, terminals, and more.
Stainless Steel
Stainless steel is used in numerous industries for its strength and corrosion resistance. Stainless steel parts often made by Swiss machining include: surgical and dental instruments, pipe fittings, nozzles, and bearings.
Special Alloys
Special alloys like Inconel®, Monel®, and Hastelloy can be used to make parts on a Swiss lathe. These alloys are often used for applications in extreme environments such as: jet engines, chemical processing equipment, gas turbines, and more. Swiss machining is a suitable process for minimizing material waste during the manufacture of precise, repeatable parts for critical components made of expensive materials.
Precision Steel
Precise steel parts are easily made by Swiss machining processes. Precision steel is a raw product that has been prepared to precise tolerances. Utilizing precise steel stock allows manufacturers to have a headstart on obtaining precise finished products. Using Swiss machining for precision steel, no matter the steel grade, helps ensure that precise finished products fabricate parts are the norm. From camshafts and crankshafts for the automotive industry to firearm components like barrels, precise steel is easily machined by Swiss lathes.
Titanium
Titanium is valued for its high strength-to-weight ratio and corrosion resistance. It is often used in applications where weight reduction is critical, such as in the automotive and aerospace industries. Parts like bushings for connecting rods, springs and shock absorbers, and landing gear components are all examples of parts that can be made from Swiss machining.
Titanium is also used in the medical industry for prosthetic implants for the same reason — high strength, lightweight, and biocompatibility. While titanium can sometimes be difficult to machine, Swiss machining can be used to convert titanium bar stock to safe and effective titanium parts.
PVC
Swiss machining is not limited to the use of metals. The process can also be used to machine thermoplastics such as PVC (polyvinyl chloride). PVC parts including bushings, rollers, and pipe fittings such as valves and couplings can easily be made.
Acetal
Acetal, also known as POM (polyoxymethylene), is another thermoplastic that can be Swiss machined. It is valued for its strength, toughness, and ability to be used at high temperatures. As with PVC, acetal Swiss-machined components include valves and fittings, but also gears, bearings, knobs, and more.
Nylon
Nylon is a thermoplastic valued for its strength, chemical resistance, and thermal stability. Nylon Swiss-machined components include: gears, bushings, seals, gaskets, rollers, and more.
Delrin®
Delrin® is DuPont’s trademark name for its version of acetal (POM). As with other acetal resins, Swiss machining can be used to make valves, fittings, gears, bearings, and knobs out of Delrin®.
PTFE
PTFE (polytetrafluoroethylene) is a type of polyester that is known for its chemical resistance, thermal and electrical insulation properties, UV (ultraviolet) light resistance, and low coefficient of friction. This makes PTFE ideal for parts such as electrical housings, insulation, bearings, and seals. Such components can be made profitably by Swiss machining.
UHMW
UHMW (ultra-high molecular weight polyethylene) is a thermoplastic known for its strength and durability. It is used to make parts like idler rollers, sprockets, chain guides, bearings, and more using Swiss machining.
Ultem®
Ultem® is a trademark polyetherimide resin manufactured by Sabic. Ultem® is valued for its excellent mechanical properties and dimensional stability even when exposed to extreme temperatures. Swiss machining is used to make Ultem® parts like medical instrument components, electrical connectors, and manifolds.
PEEK
PEEK (polyetheretherketone) is a high-performance thermoplastic that is renowned for its excellent mechanical properties, dimensional stability, ability to be used at high temperatures, and resistance to hydrolysis. Examples of Swiss-machined PEEK parts include: gears, rollers, bushings, seals, electrical connectors, and pump and valve components.
Benefits of Swiss Machining
There are many benefits and advantages to Swiss machining. These include:
- High Precision
- High Accuracy
- Tight Tolerances
- High Production Speed
- Versatility
- Durability
- Complex Components
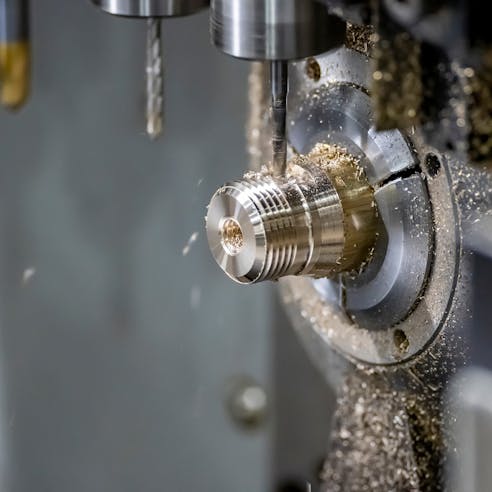
High Precision
In Swiss machining, the workpiece is firmly secured and only the portion of the workpiece where machining occurs is exposed. This reduces the moment arm and deflection experienced by the workpiece during machining. The stability offered by Swiss machining means both large and small parts can be repeatedly made to extremely tight tolerances, on the order of +0.001”.
High Accuracy
Swiss machining is a highly accurate machining process that can repeatedly (precisely) produce parts to the required dimensions due to the low vibrations and moments experienced during the machining process.
Tight Tolerances
Tight tolerances are the norm with Swiss machining processes. Short moment arms in both the tool and workpiece, in addition to reduced vibration and chatter, mean parts made are always made to tight tolerances. Tolerances in Swiss machining processes can be as low as +0.001”.
High Production Speed
Swiss machining offers exceptionally high production speeds because multiple machining processes can be completed simultaneously without the need for tool changes or downtime. Additionally, Swiss lathes have a high level of automation, including: automatic loading, feeding, and unloading. It can operate for an extended duration without the need for human intervention.
Versatility
Just as the ability to cut features simultaneously and on different planes enables a high production speed, it also provides the versatility to cut many different types of features into parts. Products such as: screws, prosthetic implants, and tiny watch gears can be made by Swiss machining.
Durability
CNC Swiss lathe tools and components are long-lasting because tool stick out is minimized and the vibration is reduced. As a result, tools need to be changed less frequently than tools and components on standard CNC lathes. Moreover, bar stock movement is facilitated by a sliding headstock rather than a belt drive which further increases the machine’s durability. These two things enable Swiss lathes to be cost-effective over the long term since highly precise parts can be made repeatably without the frequent need for tool changes.
Complex Components
Complex components can be easily made on a Swiss lathe. This is because features can be cut both axially and perpendicularly to the part’s rotational axis of symmetry, which provides the ability to cut complex features in a single operation. Complex parts like screws, surgical instruments, and small electronic components are effortlessly made by the Swiss machining processes.
Drawbacks of Swiss Machining
Swiss machining is not without its drawbacks. Some disadvantages are described below:
- Costly
- High Maintenance
- Part Size Restrictions
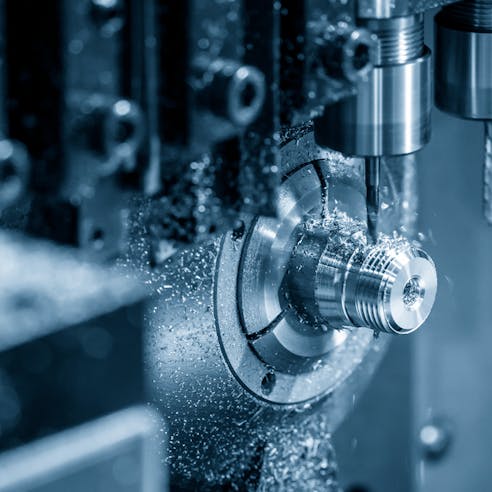
Costly
Upfront costs for Swiss lathes can be high, ranging from $20,000 to over $500,000. Consequently, obtaining machinery for a Swiss machining operation can be a huge barrier to small and medium manufacturers looking to expand their customer bases and production volumes.
High Maintenance
Swiss lathes require high maintenance to ensure good working order and operational efficiency. Cleaning filters and fans, ensuring proper oiling and lubrication of moving parts, and inspecting joints and fittings are all essential to ensuring the advantages offered by Swiss machining are consistently obtained.
Part Size Restrictions
Swiss machining is better suited for machining parts with a small footprint since the machines themselves are often small. Since both the machine’s and the part’s footprint are small, the tool stick-out and the amount of the workpiece protruding from the guide bushing are also small. While this is advantageous for reducing vibration and chatter and for achieving tighter tolerances, it is not good for cutting larger parts.
In need of swiss machining services?
Applications of Swiss Machining
Swiss-machined parts are common in numerous industries. Listed below are some of its applications:
- Aerospace Components
- Medical Components
- Optical Equipment
- Automotive
- Electronics
- Military
- Firearms
- Oilfield & Energy
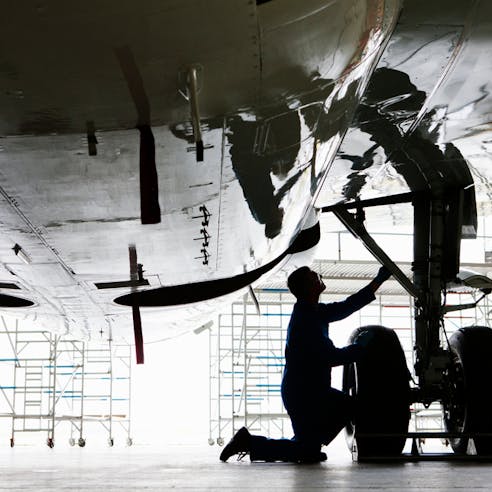
Aerospace Components
Swiss machining is great for creating small aerospace parts due to the machine’s ability to satisfy precise tolerances. Aerospace components like cams, springs and shock absorbers, bushings for connecting arms, and landing gear components are some examples.
Medical Components
Parts in the medical industry are often small and must be fabricated to precise tolerances for safety and ease of use. In the medical industry, Swiss machining is often used to make parts such as: surgical and dental instruments, prosthetic components, joint implants, and medical device components such as pacemakers or diagnostic machine parts.
Optical Equipment
Swiss machining can also be used to make components for optical equipment like cameras, microscopes, telescopes, and lasers. Examples of components produced are: lens casings, screws, optical transistors, and adapters.
Automotive
The automotive industry is one industry where Swiss machining is commonly used. It is used to make parts like: valve guides, camshafts, crankshafts, shock absorber springs, bushings for connecting rods, and more.
Electronics
Parts for electronics like terminals in semiconductors, electrical connectors, electrical terminals, and housings can be made by Swiss machining.
Military
Swiss machining for the military is often used to make many of the same parts manufactured for the civilian automotive, aerospace, electronics, and firearms industries. Components such as: firearm barrels and components, springs, screws, nozzles, landing gear components, bushings for connecting rods, gears, sprockets, and many more, are made using the Swiss machining process.
Firearms
The firearms industry commonly employs Swiss machining to fabricate parts like gun barrels, muzzles, safety selectors, and sights.
Oilfield & Energy
The oilfield and energy industries often use Swiss-machined components due to the process’s ability to produce small precise parts or parts that have a high length-to-diameter ratio. Examples of parts for the oilfield and energy industry include: gears, turbine blades, sprockets, valves, and nozzles.
Alternatives to Swiss Machining
Xometry offers some alternatives that can be used in place of Swiss machining. These include:
- 5-axis CNC Milling
- Conventional Lathe Machining
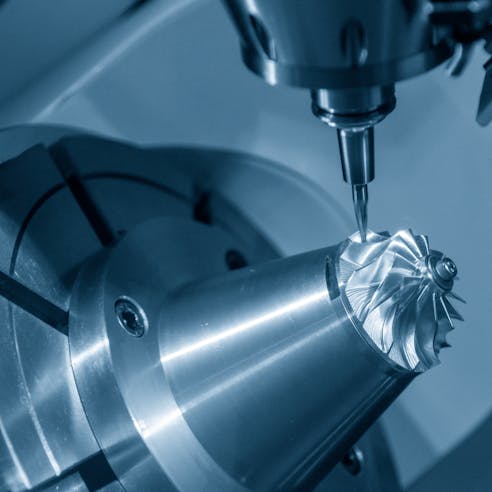
- 5-axis CNC Milling: 5-axis milling, like Swiss machining, can be used to fabricate complex parts to extremely precise tolerances at fast speeds. Although, the parts made by 5-axis milling are often larger than the parts fabricated using Swiss machining. Additionally, however, unlike Swiss machining where bar stock is automatically fed into the work area for machining, 5-axis milling typically requires more tool changes and downtime. Consequently, depending on the production volume and part geometry, Swiss machining is often a more efficient process.
- Conventional Lathe Machining: Conventional turning and facing operations using a traditional lathe may not be as efficient as Swiss machining but can still be a viable alternative. Certain factors may justify the decision to pick a conventional lathe over a Swiss lathe. Such factors include: the part being too large for Swiss machining, tolerances are not strict, or it is a one-off part. While CNC lathes are great for these operations, they require more downtime since cutting tools must be replaced more frequently and parts must be removed and adjusted more often.
Copyright and Trademark Notices
- Monel® and Inconel® are registered trademarks of Special Metals Corporation.
- Delrin® is a trademark of DuPont Polymers, INC.
- Ultem® is a registered trademark of SHPP GLOBAL TECHNOLOGIES B.V.
Why Choose Xometry for Swiss Machining Services?
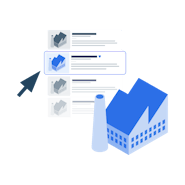
Endless Options
Choose from millions of possible combinations of materials, finishes, tolerances, markings, and certifications for your order.
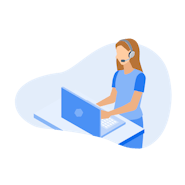
Easy to Use
Get started with our easy-to-use platform and let our experts take care of managing the project from locating the right manufacturing partner to delivery logistics.
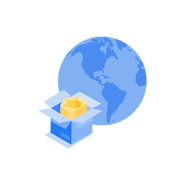
Vetted Network
We are ISO 9001:2015, ISO 13485, and AS9100D certified. Only the top shops that apply to become Suppliers make it through our qualification process.