Zinc Die-Casting Services
High Quality Die Cast Zinc Parts. Subject to availability. Xometry doesn't guarantee that we can provide this service at any given time.
Xometry provides access to up-to-the-minute die-casting equipment and capabilities, delivering part quality and time to market across all sectors.
Die-cast manufacture is the right choice for producing medium- to high-volume, complex metal parts. The results are accurate, repeatable, and cost-effective, only requiring secondary machining operations when tolerance demands are very high. The great strength of die casting is the ability to produce high-performing metal parts that are generally net-shape finished components in a single and rapid cycle operation.
Zinc Die-Casting Process
The most common die-casting method applied to zinc is gooseneck die casting, also known as hot chamber die casting. Die casting requires the fabrication of a mold tool or die. The molten metal injected into the die cavity takes the shape of the cavity and cools in place before removal.
The molten charge is stored in a holding pot. It is kept at the right temperature for casting either by internal or external heating. The gooseneck feeds fill from the holding chamber to the injection port of the cavity tool. A plunger on top of the chamber allows it to fill with molten metal from the holding pot. When the chamber is filled, molten material is forced up the gooseneck into the die cavity using the plunger. The mold is pressed closed under high hydraulic pressure during fill and solidification. Once the metal is cool enough, the dies open, and the casted piece is ejected.
In hot chamber die casting, the injection system is immersed in a pool of molten metal, which simplifies the equipment by eliminating the need for a separate heating stage. The stages of hot chamber die casting are: die preparation, melt preparation, injection, recharge, cooling and solidification, die opening and ejection, and trimming and finishing.
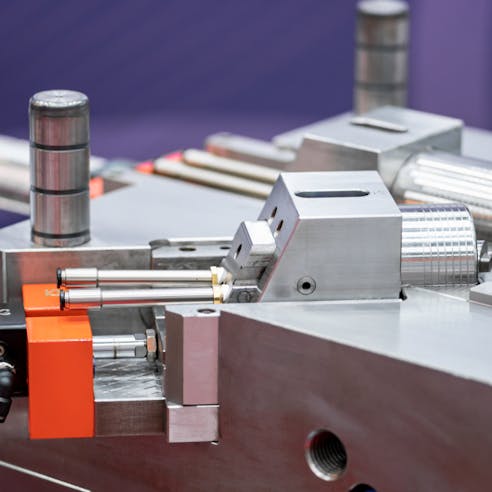
Zinc-Die-Casting Material Properties
Listed are some of the zinc-die-casting material properties:
- Hardness
- Strength
- Thermal and Electrical Conductivity
- Dimensional Stability
- Corrosion Resistance
- Thin Wall Capacity
- Recyclability
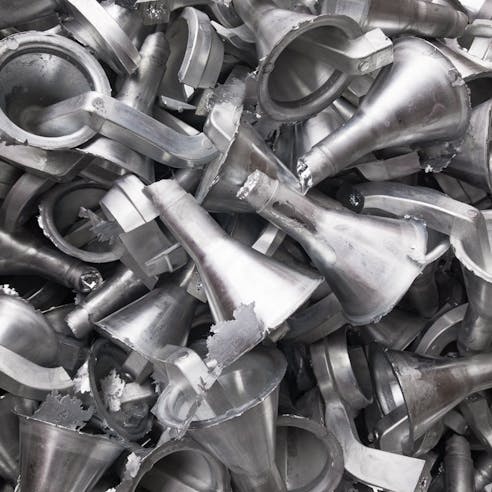
- Hardness: Typical ZAMAK materials processed in hot chamber die casting have hardnesses in the range of 80–130 on the Brinell hardness scale. Many zinc alloys exhibit some reduction of hardness over time, especially in components that have seen significant temperature cycling. This is referred to as aged hardness.
- Strength: The ultimate tensile strength (UTS) of hot chamber die-cast alloys lies in the range of 280–400 MPa, comparable with many aluminum alloys. The yield strength for most hot chamber cast alloys is in the range of 220–370 MPa, higher than many aluminum alloys. Izod impact strengths for these alloys are in the range of 13–65 J (joules), considerably higher than magnesium alloys. Shear strengths generally lie in the 215–317 MPa range.
- Thermal and Electrical Conductivity: Typical thermal conductivities for hot chamber die-cast alloys lie in the range of 110.8 to 126.8 W/m/K. Electrical conductivities are fairly low, at 25% IACS (international annealed copper standard).
- Dimensional Stability: The long-term dimensional stability of most die-cast parts is good to excellent, under nominal loading conditions. Some alloys suffer considerable creep, especially when loaded at elevated temperatures (200 °C is considered elevated for most alloys).
- Corrosion Resistance: Most zinc alloys acquire the corrosion resistance of their largest constituent. Zinc has high environmental stability and resistance to mild acids and alkalis. It is widely used in small components of wet systems such as ICE cooling circuits and thermostat housings.
- Thin Wall Capacity: Zinc alloy die casting allows the reliable formation of very thin walls. Sections as small as 0.4 mm will reliably fill over several centimeters run, and even thinner sections are possible in higher pressure casting, and over short sections joining thicker areas. This is a result of very low melt viscosity, which allows the charge to flow in restricted areas in a die without excessive turbulence.
- Recyclability: As alloys of various metals, zinc die-cast parts can be recycled indefinitely. However, some issues prevent this from being the norm. The raw materials are inexpensive, so the cost-benefit of recycling is small. The alloys are hard to identify, so a batch of recycled die-cast parts will have unknown constituents. While they can be tested, this is not a cost-practical step in a low-value recycling process. Die-cast volumes are large overall, but the typical parts are small and too sparsely distributed for the waste-collection process. On this basis, the economic separation and sorting of die-cast components are rarely performed. One exception is the automotive sector, particularly in Europe, where use-to-re-use closed-loop materials management is being developed by more advanced brands.
Advantages of Zinc Die Casting
Zinc die casting offers some huge advantages over other net-shape metal part manufacturing processes. These are listed below:
- Complex Shapes
- Design Flexibility
- Tough and Durable Parts
- Corrosion Resistance
- Thermal and Electrical Conductivity
- Low Cost
- Extended Die Life
- Good Quality Finish
- Environmentally Friendly Process
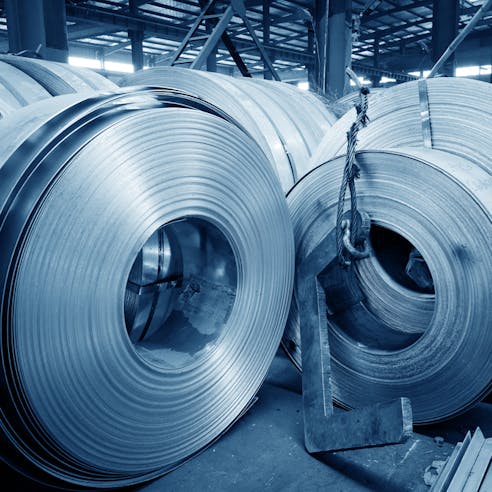
Complex Shapes
Zinc alloys facilitate casting with low viscosity and low erosion behavior in the melt, allowing for the casting of intricate and complex shapes with high precision and low tool erosion. Zinc-based alloys have excellent flow characteristics, enabling the filling of thin walls and tight tolerances.
Design Flexibility
The process simplifies the execution of complex geometries and finesse details, providing design flexibility to meet the bulk of specific application requirements. It can incorporate features such as thin walls, limited undercuts, and threads without additional machining, simplifying finishing and assembly.
Tough and Durable Parts
Die cast zinc alloy creates high-strength and durable parts, making them suitable for roles that require structural integrity and load-bearing capabilities. Such parts can be designed for a beneficial strength-to-weight ratio, providing robust components that serve admirably.
Corrosion Resistance
Such parts are inherently corrosion-resistant without any surface coatings, though corrosion performance can be further enhanced with various surface finishes, such as plating, painting, or powder coating. This makes zinc die castings suitable for applications exposed to harsh environments or corrosive elements.
Thermal and Electrical Conductivity
Die-cast alloys deliver good thermal and electrical conductivity, allowing for effective heat dissipation and electrical conductivity, where useful in resulting components. Applications in which thermal management or electrical conductivity is additionally required with other properties are often well solved with zinc alloy die-cast parts.
Low Cost
When volumes are high, zinc die casting provides the most cost-effective manufacturing process. It offers high production rates, reduced material waste, and shorter manufacturing cycles when compared with any other net-shape metal part process.
Extended Die Life
Extended tool life and high repairability of zinc-die-casting tools further contribute to cost savings. Zinc alloys are renowned for their low abrasion/erosion of tools. In addition, low operating temperatures add to the durability of dies, as stresses are reduced when compared with pressure die-casting in particular.
Good Quality Finish
Zinc die-cast parts typically have a smooth and uniform surface finish, requiring minimal post-processing operations. This saves time and cost in the production process.
Environmentally Friendly Process
While the recycling of the multitude of zinc alloy parts used in products is rare, the process wastage is minimal and all offcuts are immediately re-used. The hot chamber process itself has quite low energy demand, in comparison with most casting processes. The chamber is easy to keep at temperature and the volume of waste heat in the process is minimal, as the distance and complexity between the melt and the cavity is minimal.
Need custom zinc die cast parts?
Disadvantages of Zinc Die Casting
While zinc die casting offers numerous advantages, it also has a few disadvantages that should be considered. Some of the disadvantages of zinc die casting include:
- Limited Operating Temperature
- Higher Density
- Limited Alloy Options
- Shrinkage Porosity
- Brittleness
- Limited Size and Weight Range
- Environmental Considerations
- Higher Tooling Costs
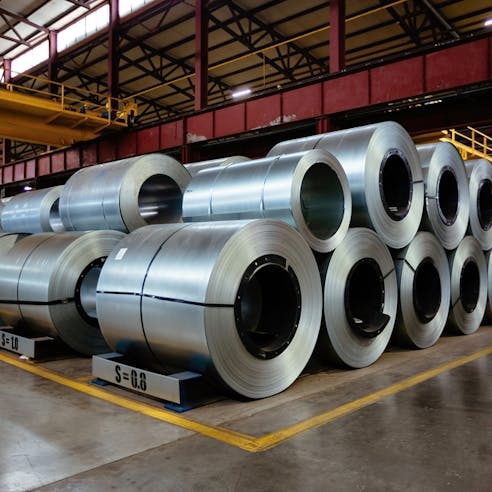
Limited Operating Temperature
Zinc has a relatively low melting point compared to other metals used in die casting, such as aluminum or magnesium. This lower melting point is a significant advantage in the manufacturing process but limits the suitability of zinc die casting for applications that suffer high operating temperatures.
Higher Density
Zinc has a very high density, nearly three times that of aluminum. Zinc die castings tend toward higher weight per application. For this reason, the material is unknown in the aerospace sector, despite its numerous advantages.
Limited Alloy Options
Compared to other die-casting materials, such as aluminum or magnesium, zinc alloys are much less diverse. This restricts the designer and manufacturer’s capability in tailoring the material properties to the specific demands of an application.
Shrinkage Porosity
The potential for surface defects in zinc die castings can be greater than for other materials/processes. Porosity or blistering can be more prevalent than with other die-casting materials. Minimizing these defects requires tight process control and careful/experienced design approaches.
Brittleness
Although zinc die castings exhibit good strength, they can be relatively brittle compared to other, more ductile die-casting materials. This brittleness limits the applicability of the parts for applications that require high-impact resistance or ductility.
Limited Size and Weight Range
Zinc die casting is not well-suited for large and heavy parts, which may require alternative casting methods. The tooling costs become very high, and it is common for larger parts to not require the production volumes that can amortize this. Additionally, most machines have an absolute maximum shot weight of between 500 and 750 grams.
Environmental Considerations
All metals used in manufacturing are finite resources. Mining and processing of zinc have significant environmental impacts, and proper recycling and waste management practices that might minimize virgin metal demand are rarely followed.
Higher Tooling Costs
Tooling costs for zinc-adapted dies are relatively high, compared to other die-casting materials due to the specific properties of zinc alloys and the design complexities associated with the process. This can affect the initial investment required for production, though it is countered by extremely high shot life—often as high as two million operations.
Applications of Zinc Die Casting
Listed below are some common applications of zinc die casting:
- Auto Components
- Door Locking and Cabinetry Hardware
- Fasteners
- Plumbing Components
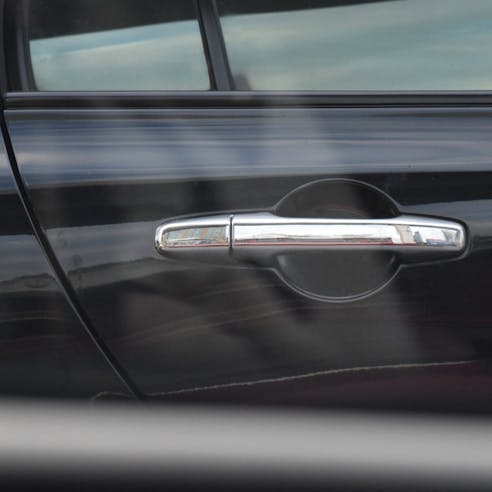
Auto Components
Zinc die casting is key to many aspects of the automotive sector, for a wide range of components, due to its unique properties and various advantages. The process provides excellent surface finish, dimensional accuracy, high strength-to-weight ratio, and good thermal conductivity. Some examples of its applications are:
- Door handles and knobs
- Seat adjusters
- Decorative trim pieces
- Oil pump housings
- Sensor components and housings
- Thermostat housings
- Steering wheel frames
- Valve bodies
- Shift forks
- Clutch and airbag components
Door Locking and Cabinetry Hardware
Zinc die casting is extensively used in the making of door and cabinetry hardware, due to its strength, versatility, durability, and cost-effectiveness. In addition, the finished product usually has good dimensional accuracy and excellent surface finish, making for long-lasting and appealing solutions. Some examples of its applications are:
- Door handles
- Knobs
- Levers
- Latches
- Hinges
- Keyhole escutcheons
- Striker plates
- Decorative covers
Fasteners
Zinc die casting is very widely applied to the manufacturing of fasteners, due to its high strength, dimensional accuracy, and low cost of parts when volumes are high. Some products that use die-casted zinc are:
- Coarse threaded screws and bolts.
- Hex nuts, wing nuts, and lock nuts.
- Anchors, including expansion, hammer, and drop-in anchors.
- Clips and clamps.
- Hooks and hangers.
Plumbing Components
Zinc die casting serves in making many plumbing components, due to excellent corrosion resistance, dimensional accuracy, and cost-effectiveness. Some common applications are in the production of the following parts:
- Faucet parts, including handles, spouts, escutcheons, and decorative trim pieces.
- Shut-off valves, pressure-reducing valves, and control valves.
- Pipe fittings, including elbows, tees, couplings, and connectors.
- Drain components such as drain grates, strainers, and pop-up assemblies.
- Components of showerheads, such as shower arms, showerhead housings, and spray nozzles.
Alternatives to Zinc Die Casting
Xometry offers various alternative materials and processes that can compete in some regards with zinc die casting, depending on the specifics of the application:
- Aluminum Die Casting
- Magnesium Die Casting
- Plastic Injection Molding
- Investment, or Lost Wax Casting
- Sand Casting
- Metal Injection Molding (MIM)
- CNC Machining
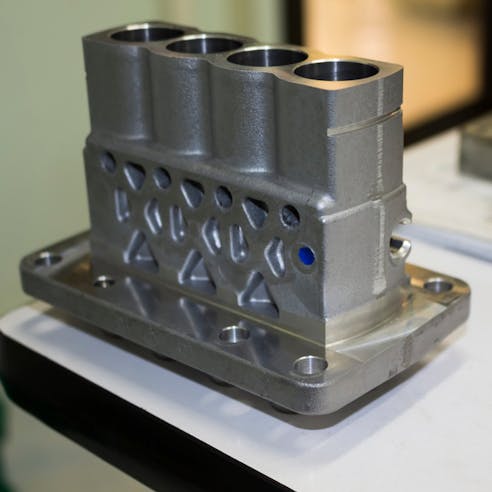
- Aluminum Die Casting: Offers many of the advantages of zinc die casting. Aluminum offers excellent strength-to-weight ratio, high thermal conductivity, and good corrosion resistance. Minor material property differences and much-reduced tool life influence the selection.
- Magnesium Die Casting: This is another practical alternative to zinc. The parts are much lighter, making this a preferred option in weight-sensitive equipment such as aerospace and sports equipment.
- Plastic Injection Molding: This is a versatile alternative to die casting. Plastic injection molding offers equal design flexibility, cost-effectiveness, and the ability to produce complex shapes and features, though the strength of equivalent parts is generally considerably lower.
- Investment, or Lost Wax Casting: This uses a wax pattern, coated with a ceramic shell and then melted out to create a mold cavity. Molten metal is then poured into the cavity to produce the final component. Investment casting is suitable for producing complex and high-precision parts in various metals, including stainless steel and bronze. However, it is not suited to mass production, unless the product value is very high.
- Sand Casting: This is a traditional casting process that involves creating a mold cavity by compacting sand around a pattern, which is charged with molten metal to form the part. Sand casting services are suitable for producing larger and more complex parts in almost all metals, but production is labor-intensive and slow unless very expensive automation is used.
- Metal Injection Molding (MIM): this combines elements of plastic injection molding and powdered metallurgy. It involves mixing metal powders with a polymer binder, injecting the mixture into a mold, and then burning out the binder and sintering the part to achieve the final metal component. MIM is suitable for producing small, intricate, and high-precision parts in various metals, including stainless steel and titanium.
- CNC Machining: this involves the use of computer-controlled machines to shape and cut almost any material. It is a versatile alternative that offers high precision, design flexibility, and the ability to produce complex parts. CNC machining is suitable for both prototype development and moderate-volume production.
Why Choose Xometry for Zinc Die Casting Services?
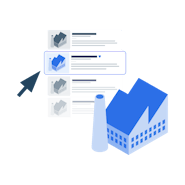
Endless Options
Choose from millions of possible combinations of materials, finishes, tolerances, markings, and certifications for your order.
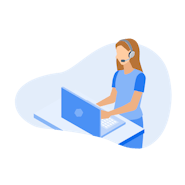
Easy to Use
Get started with our easy-to-use platform and let our experts take care of managing the project from locating the right manufacturing partner to delivery logistics.
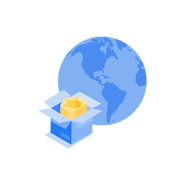
Vetted Network
We are ISO 9001:2015, ISO 13485, and AS9100D certified. Only the top shops that apply to become Suppliers make it through our qualification process.