Laser Heat Treating Services by Xometry
Xometry offers the highest quality laser heat treating services and can assist in the production of parts with intricate and complex geometries and excellent surface finishes.
Xometry offers the highest-quality laser heat treating services, which are primarily used for precision surface hardening of steel and cast iron components. These laser heat treating services hold advantages over other methods of industrial heat treating for hardness. Using laser heat treating allows for accurate control of the heated area, with limited penetration of the heat, which in turn minimizes distortion and can avoid the need for post-hardening machining or grinding.
Laser Heat Treating Process
Laser heat treating uses a high-power direct diode laser (HPDDL). This diode laser has a wavelength of approximately 1 µm, which is readily absorbed by metals such as carbon steel and cast iron. The position and path of the laser shining on the metal can be accurately and precisely controlled. The size of the laser incidence on the metal can be typically from 0.5" x 0.5" to 2" x 2".
The laser transfers its optical energy to the metal to heat it. The heat is transferred only to the surface of the workpiece, with a limited depth of penetration into the metal, as the energy is transferred only where the light of the laser impinges on the metal. As the temperature of the steel increases, it is converted to the austenitic phase. Rapid quenching (cooling) from this phase causes the martensitic phase to form. Martensite is a particular crystal structure that is known for its hardness. Hardening by heat treating therefore targets the formation of martensite on the surface of the workpiece.
With other types of heat treatment, quenching is typically done with water or oil. However, with laser heat treating, the metal “self-quenches”—because the heating occurs over a small, precise area with limited depth. So the moment the energy source is removed, that heat rapidly dissipates by conduction into the material’s thermal mass. Convection at the surface also removes heat.
In this way, surface hardening is achieved by using laser heat treatment to form martensite at the material’s surface.
Materials Suitable for Laser Heat Treating
Laser heat treating is most commonly applied to steels and cast irons for surface hardening. These materials readily absorb the energy from a diode laser of 1 µm wavelength. Heat treating works on ferrous metals to harden them by forming the martensite phase of iron-carbon alloys (steel and cast iron). Heat-treatable alloys include: gray cast iron, ductile iron, tool steel, and some 400-series stainless steels. Some titanium alloys, as well as some nickel alloys, can also be hardened by laser heat treatment.
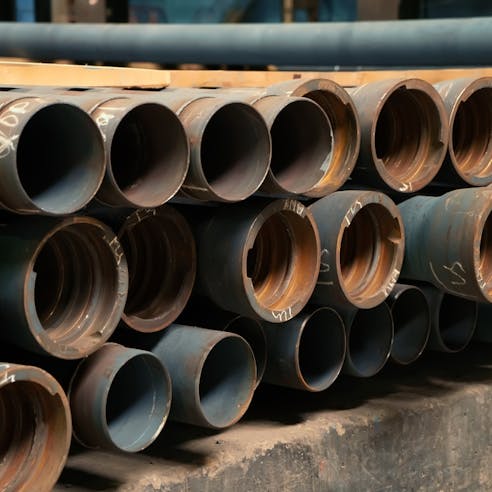
Advantages of Laser Heat Treating
There are several surface hardening benefits to using laser heat treatment. These laser heat treating advantages are explained further below:
Improved Surface Hardness
Laser heat treating is used for surface hardness enhancement primarily by causing martensite to form in the treated material. Martensite is a specific phase within alloys that is known for its hardness. The surface of the workpiece is heated by the laser’s optical energy until its temperature is high enough for the austenitic phase to form. Rapid cooling from this state causes rapid crystallization, which causes the body-centered cubic (bcc) tetragonal structure of martensite to form.
Enhanced Precision
Laser heating allows very high precision in selecting the area to be heat treated. The surface of the workpiece is heated optically where the laser is incident, and the position of the laser can be manipulated with an accuracy of microns. This accurate positioning (and path) of the laser provides precise surface hardening. This can be very useful for components with complex geometries.
Reduced Distortion
Laser heat treating allows for minimal distortion of the workpiece when compared with other heat treatment methods. Distortion is possible with heat treatment due to the high temperature required to change the material phase. However, with laser heat treatment, there is a very limited depth of heat penetration, as well as an accurate and limited application of heat. This gives some distortion control in heat treatment by laser.
Disadvantages of Laser Heat Treating
There are some drawbacks of laser heat treatment, some of which are listed and discussed below:
Potential Distortion
The high temperatures at the surface cause the material to expand, which can cause surface warping. In other heat treatment methods, the workpieces can be clamped during heating and quenching to limit distortion. However, since the heat is transferred optically during laser heat treatment, clamps have limited usefulness as they cannot be used directly in the targeted area, only nearby.
Limited Depth of Treatment
Laser heat treating by definition transfers heat to the material through optical energy. This energy is only incident on the visible surface of the workpiece. Therefore the surface is the hottest temperature, with some gradient into the body of the workpiece. There is a limited depth that the austenitic temperature reaches, and therefore at which hardening occurs. This shallow heat treatment is an inherent limitation of laser heat treating. It is therefore not well suited to applications in which a significant depth of hardening is targeted.
High Initial Equipment Cost
An industrial-scale laser heat treating setup have a high initial equipment investment. This high cost of laser heat treating machinery can be a barrier to adopting the process. As an example, for automotive dies, the financial benefit of shorter turnaround times and the savings of no post-hardening machining would need to justify the investment in laser heat-treating equipment. This justification will depend on several factors, such as the volume of dies produced.
In need of custom laser heat treating services?
Laser Heat Treating Applications and Industries Served
There are many laser heat treating applications, specifically for surface hardening uses. The advantages of this industrial heat treatment method are well suited to some varied areas of application below:
- Automotive Industry
- Aerospace Industry
- Tool and Die Manufacturing
- Medical Devices
- Metalworking
- Manufacturing
- Engineering
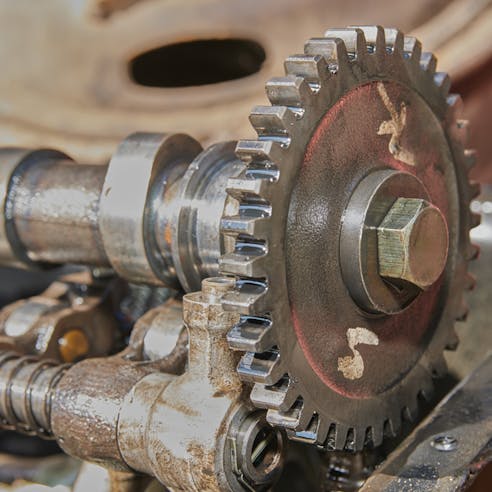
Automotive Industry
Laser heat treating is used for hardening components in the automotive industry. Automotive parts, particularly engine components such as camshafts, benefit from the precise hardening and limited distortion of using laser heat treating. Automotive dies are also increasingly being surface hardened by laser heat treating.
Aerospace Industry
Aerospace applications require precision. Laser heat treating in the aerospace industry is therefore popular, as it allows accurate hardening of components. It is widely used for hardening the working surfaces of aircraft components, including landing gear components and turbine blades.
Tool and Die Manufacturing
Laser heat treating for tooling is growing in application, particularly for surface hardening of industrial dies. Its advantages of precise heating and minimal distortion avoid the need for post-hardening machining. This saves cost and also decreases the turnaround time for a new die.
Medical Devices
Laser heat treatment for medical devices is a recent step forward in healthcare technology. The accuracy and precision of laser heat treating make it a good fit for the surface hardening of medical equipment such as surgical instruments and implanted devices. It is a significant advantage to be able to select certain areas for hardening while leaving other areas unaltered, with very little distortion, if any. Particularly for implants, this improves their success rate.
Metalworking
Laser heat treating has applications in the metalworking industry for metal surface hardening. Depending on the specific requirements for each component to be fabricated, the accurate hardening of specific areas for wear resistance may be necessary. Particularly complicated or sensitive components are well suited to the advantages of laser heat treating for hardening.
Manufacturing
The manufacturing sector is increasingly benefitting from the use of laser heat treatment for surface hardening molds, dies, tools, and other manufacturing devices. The finer control over the hardened surface and any distortion that may result provides more precise and robust tools for industrial manufacturing.
Engineering
In the engineering industry, certain complex engineering components require precise hardening. These can include: complex gears, turbine blades, or other key components in power generation and heavy industrial equipment. These engineering applications benefit from the lower cost and quicker turnaround time due to laser heat-treated components having limited or no distortion after hardening.
Alternatives to Laser Heat Treating
Xometry offers alternatives to laser heat treating for the hardening of steels. Some potential options are explained below.
Induction Hardening
Induction hardening is a heat treatment to harden the surface of a component. The process passes alternating electrical current through a copper ring to produce a magnetic field. The component to be hardened, typically a ferrous metal, is passed through this magnetic field, which in turn induces a magnetic field in the component. This creates eddy currents and high temperatures at the surface. The temperature of these areas rises to the material’s transformation temperature and then the target material is quickly quenched.
Induction hardening is an energy-efficient way of heating and also allows a targeted area to be heated—specifically only close to the surface of the component. It is most commonly used on rotationally symmetrical parts such as: gears, shafts, and axles.
Flame Hardening
Flame hardening uses the impingement of an open flame on the surface of a ferrous alloy to heat it to harden it. It is most common to use an oxyacetylene flame to heat the metal surface—which is rapidly quenched after heating.
One of the disadvantages of flame hardening is that it cannot be applied precisely, but only to broad areas. It is also possible to overheat an area and cause it to become brittle.
Case Hardening
Case hardening is an approach to hardening in which the external surface of a component is hardened. The interior material, however, remains relatively soft and ductile, therefore creating a hard case around the body of the component.
There are some different approaches and methods to accomplish case hardening. For some materials, such as low-carbon steels, the thin layer of hard material at the surface can be created by infusing carbon and nitrogen, such as in carburizing and carbonitriding. Flame hardening and induction hardening can also be employed to case harden a component.
Carbonitriding
Carbonitriding is a thermo-chemical process for the surface hardening (case hardening) of steels. A ferrous component is heated in a gaseous atmosphere that contains nitrogen and carbon. The nitrogen and carbon diffuse into the austenitic structure of the steel at the surface. The component is then rapidly quenched in oil or water.
Carbonitriding is carried out at lower temperatures and for shorter times than carburizing and therefore has a lower risk of distortion. It is typically applied to small, mass-produced components, with a case-hardening depth of less than 0.7 mm.
Why Choose Xometry for Laser Heat Treating Services?
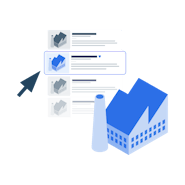
Endless Options
Choose from millions of possible combinations of materials, finishes, tolerances, markings, and certifications for your order.
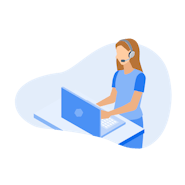
Easy to Use
Get started with our easy-to-use platform and let our experts take care of managing the project from locating the right manufacturing partner to delivery logistics.
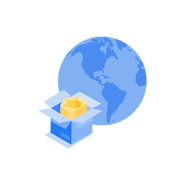
Vetted Network
We are ISO 9001:2015, ISO 13485, and AS9100D certified. Only the top shops that apply to become Suppliers make it through our qualification process.