Passivation Services by Xometry
Xometry offers the highest quality passivation services and can assist in the production of parts with intricate and complex geometries and excellent surface finishes. Subject to availability. Xometry doesn't guarantee that we can provide this service at any given time.
"Passivation" refers to a chemical metal finishing process that can remove metal contaminants and help to form a very thin, protective oxide layer on the surfaces of certain metals to enhance their corrosion resistance. The additional protection provided by passivation can significantly extend the life of a product exposed to a corrosive environment. Passivation has many applications such as surgical and dental instruments as well as food and beverage handling equipment.
Xometry offers passivation as a value-added, turnkey service to our primary manufacturing processes, including CNC, 3D printing, injection molding, casting, sheet cutting, etc. A product can be fully customized using the Xometry Instant Quoting Engine®. Xometry does not provide secondary processing or finishing to parts supplied by a third party, with few exceptions.
What Is Passivation?
Passivation is a chemical metal finishing process that is applied to the surface of a metal substrate to enhance its corrosion resistance properties. In passivation, a protective oxide layer is added onto the surface of a part which acts to dissolve the amount of free iron that is exposed to the environment. There are different techniques to complete passivation such as nitric acid passivation and citric acid passivation. However, each method requires extensive cleaning of the workpiece and the immersion of the metal workpiece in nitric acid or citric acid. Through a chemical reaction, the acid removes the free metal ions susceptible to reacting with oxygen in the atmosphere from the surface of the workpiece. This chemical reaction results in a passive oxide surface layer that is less likely to react with elements in the air. Passivation is a process most commonly associated with stainless steel, but it can also be used on aluminum, magnesium, and titanium.
The Passivation Process
The passivation process stars by first cleaning the surface of the workpiece to remove contaminants such as: oils, grease, dirt, and rust. After cleaning, the part must be rinsed with water. Next, the workpiece is immersed in a bath consisting of either citric or nitric acid and various other chemicals. Both citric and nitric acids are effective at removing the free metal on a material’s surface. Citric acid, while more expensive, is generally safer for the environment. After the part has been immersed for the required time, it must be rinsed with water. The parts should be allowed to dry naturally in the air. Immediately after immersion and up to 48 hours after, the passive oxide layer forms on the surface of the part. Finally, the part is subjected to various tests such as: salt spray tests, humidity tests, and copper sulfate tests to verify the effectiveness of the passivation layer.
Types of Passivation Processes
There are three main stainless steel passivation processes. Each type employs an acid to remove the free iron susceptible to reacting with the environment from the material’s surface and trigger the formation of a chromium-rich oxide. While each of the types is capable of creating corrosion-resistant surfaces, they each have advantages and disadvantages. The three main passivation processes are listed and described below:
Nitric Acid
Nitric acid passivation is a proven and established process that is the most commonly used passivation technique. In this process, the metal workpiece, typically stainless steel, is immersed in a bath of nitric acid. The nitric acid removes the free iron from the stainless steel’s surface and leaves a corrosion-resistant, chromium oxide layer (Cr2O3) of about 10-12.5% chromium.
Etching, or flash attack, is a common defect associated with passivation due to the chloride ion content in the passivation bath or on the metal’s surface. Etching is the cutting or altering of a material’s surface with a strong acid. Less corrosion-resistant grades of stainless steels are more susceptible to etching. Sometimes, flash attacks can affect some items in a passivation tank but leave others in the same batch unaffected. Higher nitric acid concentrations or higher nitric acid temperatures can reduce the likelihood of flash attacks due to the increased oxidizing potential of higher concentrations or temperatures.
Nitric Acid and Sodium Dichromate
The addition of sodium dichromate (a hexavalent chromium compound) to nitric acid passivation baths can help further enhance a material’s corrosion resistance and hasten the process. This is because sodium dichromate can increase the oxidizing potential of the passivation bath. For the same reason, sodium dichromate can also reduce the likelihood of flash attacks. The addition of sodium dichromate is preferred for less corrosion-resistant stainless steel grades like martensitic and ferritic stainless steels. However, adding sodium dichromate to a nitric acid solution increases the health risks to worker safety. since sodium dichromate is a known carcinogen. Sodium dichromate requires careful handling and proper disposal to limit worker exposure.
Citric Acid
Citric acid immersion is the third main passivation method. It offers a safer, faster, and more eco-friendly alternative to nitric acid passivation. Citric acid passivation involves a citric acid bath in which metal workpieces are immersed.
Citric acid is safer to handle than nitric acid, and its fumes do not pose a risk to workplace safety or the atmosphere.
Advantages of Passivation
There are many advantages of employing passivation methods for metal materials — from improved corrosion resistance to enhanced aesthetic appeal. The advantages of passivation are listed and described below:
Improved Corrosion Resistance
Improved corrosion resistance of materials is perhaps the biggest advantage of passivation. Passivation removes the free atoms susceptible to reacting with elements in the atmosphere from a material’s surface.
Uniform Appearance
Passivation has the ability to create uniform and aesthetically pleasing surface finishes on parts. Passivation removes an exceptionally thin amount of material on the workpiece’s surface and leaves an oxide layer roughly 0.00001” thick. As a result, passivated surfaces are often smooth and lustrous. Therefore, passivation is a great finishing process for parts used in applications where aesthetic appeal is important, such as: architectural trim pieces, home decor, kitchen appliances, and jewelry.
Cleanliness
For parts to be properly passivated, they must be thoroughly cleaned and free of contaminants. Once the passivation process is complete and the passive oxide layer forms, the clean and spotless surface is sealed underneath. Therefore, on a molecular level, passivation is a preferred method for removing surface contaminants without causing damage to the material.
Improved and Extended Life of Product
Passivation extends the lifespan of a product due to the process’s ability to make parts more resistant to corrosion over time. Consequently, parts require less frequent replacement and maintenance. Salt spray testing, copper sulfate testing, and humidity testing can be used to provide measurable results to prove passivation effectiveness.
In need of passivation services?
Disadvantages of Passivation
Passivation also has some drawbacks. These disadvantages are listed and described below:
Smoothness
Passivated parts have varying surface roughness which may not be suitable for all applications. For precision components or applications requiring a smooth surface finish, particularly in the medical industry, alternative corrosion mitigation methods like electropolishing may be required.
Time-Consuming
Passivation can be a time-consuming process. While the passivation process itself is long, the pre-cleaning operation for passivation can also be long. Consequently, passivation can be an inefficient bottleneck process for many manufacturers, which can lead to higher operating costs and longer lead times.
Applications of Passivation
Passivation is an important process step for protecting stainless steel parts from corrosion in a multitude of applications from food and beverage processing to industrial piping systems. Some typical applications of passivation are listed and described below:
- Filter Housings
- Food & Beverage Processing
- Forgings & Castings
- Stainless Steel Structural Parts
- Medical & Pharmaceuticals
- Pipes & Piping
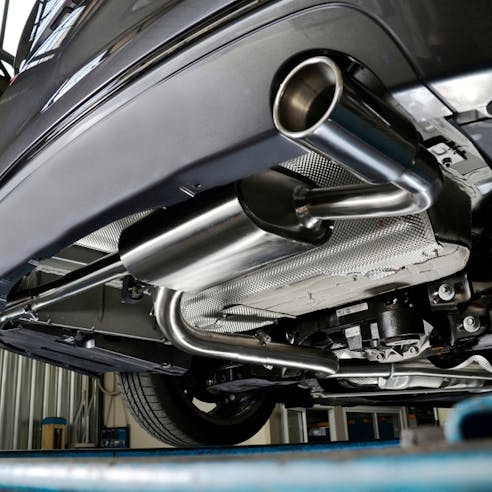
Filter Housings
Passivation is useful for filter housings, such as the dust collection systems used in the mining, plastics processing, food and beverage, and oil and gas industries. The filter housings act as shrouds for the cartridges or bags that collect and prevent abrasive nuisance and toxic dust from contaminating processes. Passivation of the filter housings helps ensure that the components have increased abrasion and corrosion resistance.
Food & Beverage Processing
Various processes for the preparation of food and beverages, such as pasteurization, fermentation, and sterilization, can all corrode components used in the industry. Therefore, components such as mixing blades, conveyor parts, and food processing mixing vessels are often passivated to improve corrosion resistance and increase service life.
Forgings & Castings
Passivation is great for forgings and castings used in a variety of industries such as electronics, and automotive. Many components in these industries, such as machinery control panels and car exhausts, are exposed to environmental conditions that can lead to part corrosion.
Stainless Steel Structural Parts
Passivation of the stainless steel framework commonly used in medical diagnostic equipment and food and beverage processing equipment is critical to ensuring the long life of these components. This is because parts in these environments are exposed to many corrosive chemicals, disinfectants, and elements that can degrade materials.
Medical & Pharmaceuticals
Surgical and dental instruments, medical equipment like stethoscopes, orthopedic implants, diagnostic equipment, work surfaces, containers, and more are all passivated to enhance corrosion resistance and increase part life.
Pipes & Piping
Stainless steel and pipings benefit greatly from passivation. Particularly in the oil and gas industry, harsh environmental conditions can hasten corrosion and lead to reduced service life of components. Passivation helps extend the lifespan of these pipes and associated fittings by minimizing the risk of corrosion-related failures.
Alternatives to Passivation
An alternative process to passivation exists if passivation is not a viable option whether due to dimensional or aesthetic requirements or stainless steel grade incompatibilities. Xometry offers an alternative metal finishing service called electropolishing.
Electropolishing is a metal finishing process that uses a combination of an electrical current and electrolytic chemicals to smooth, polish, and improve the surface finish and corrosion resistance of metal parts. A sound alternative to passivation, electropolishing is used in many industries - from aerospace and medical to electronics and food processing. Electropolishing is preferred over passivation for achieving desirable aesthetic qualities in a part.
Why Choose Xometry for Passivation Services?
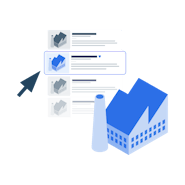
Endless Options
Choose from millions of possible combinations of materials, finishes, tolerances, markings, and certifications for your order.
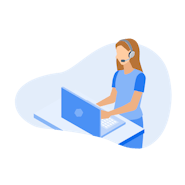
Easy to Use
Get started with our easy-to-use platform and let our experts take care of managing the project from locating the right manufacturing partner to delivery logistics.
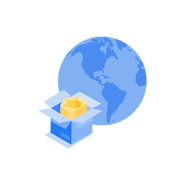
Vetted Network
We are ISO 9001:2015, ISO 13485, and AS9100D certified. Only the top shops that apply to become Suppliers make it through our qualification process.