Selective Laser Sintering (SLS) 3D Printing Service
Quality prototypes and production parts.
1-Day expedite. Free shipping on all US and international orders.
ISO 9001:2015, ISO 13485, IATF 16949:2016, and AS9100D certified.
What is SLS 3D Printing?
Selective laser sintering, SLS printing, is a powerful 3D printing, additive manufacturing, technology that produces highly accurate and durable parts capable of being used directly in end-use, low-volume production, or rapid prototyping. SLS is one of the most inexpensive options for industrial 3D printing services because it can build parts in bulk without support structures. SLS printing materials are primarily nylon and come with various infills that enhance material properties--from stiff carbon-filled to flame retardant properties.
An additive manufacturing layer technology, selective laser sintering involves the use of a high-power laser (for example, a carbon dioxide laser) to fuse small particles of plastic powders into a mass that has a desired three-dimensional shape. The laser selectively fuses powdered material by scanning cross-sections generated from a 3-D digital description of the part (for example from a CAD file or scan data) on the surface of a powder bed. After each cross-section is scanned, the powder bed is lowered by one layer thickness, a new layer of material is applied on top, and the selective laser sintering process is repeated until the part is completed.
SLS Materials
Material Name | Other Common Names | Shore Hardness | Elongation at Break (%) | Impact Strength, Notched (kJ/m²) | Data Sheets |
---|---|---|---|---|---|
Material Name Nylon 12 | Other Common Names Durable plastic, PA12, PA 2200 | Shore Hardness 75D | Elongation at Break (%) 18% | Impact Strength, Notched (kJ/m²) 4.8 kJ/m² | Data Sheets |
Material Name Nylon 12, Glass-filled (GF) | Other Common Names Stiff plastic, PA12 GF, PA 3200 GF | Shore Hardness 80D | Elongation at Break (%) 9% | Impact Strength, Notched (kJ/m²) 4.2 kJ/m² | Data Sheets |
Material Name Nylon 11 EX | Other Common Names Ductile plastic, PA11, Rilsan® Invent Natural | Shore Hardness 77D | Elongation at Break (%) 45% | Impact Strength, Notched (kJ/m²) No break | Data Sheets |
Material Name Nylon 12, Carbon-Filled (CF) | Other Common Names High-performance plastic, carbon-filled PA12, PA 602-CF, carbonmide | Shore Hardness N/A | Elongation at Break (%) 4% | Impact Strength, Notched (kJ/m²) 5.3 kJ/m² | Data Sheets |
Material Name Nylon 12, Aluminum-Filled (AF) | Other Common Names Metallic gray plastic, aluminum-filled PA12, alumide | Shore Hardness 76D | Elongation at Break (%) 3% | Impact Strength, Notched (kJ/m²) 4.6 kJ/m² | Data Sheets |
Material Name Nylon 12, Mineral-Filled (HST) | Other Common Names Heat-resistant plastic, mineral fiber-reinforced PA12, PA 620-MF | Shore Hardness 75D | Elongation at Break (%) 3-5% | Impact Strength, Notched (kJ/m²) N/A | Data Sheets |
Material Name Nylon 12, Flame Retardant (FR) | Other Common Names Meets the FAR 25.853 60 second burn specification, PA 606-FR | Shore Hardness 73D | Elongation at Break (%) 24% | Impact Strength, Notched (kJ/m²) N/A | Data Sheets |
Properties apply to US-based production. Not all options are available for Xometry's international economy option.
SLS Finishes at Xometry
Standard
SLS parts are de-powdered with a sandblasting process and manual powder removal. Internal holes may be drilled to size if accessible. The finish is white matte (fine sugar-cube).
Color Dyed
Color options of dye black, blue, green, red, or yellow. Batch to batch consistency may vary slightly with black being the most consistent. Dye penetrates ~0.010" deep.
Vapor Smoothing
An automated post-processing technology (AMT PostPro3D) that achieves a high-quality surface finish. Vapor smoothing brings most surfaces from a matte to a semi-gloss. Vapor smoothing also seals the surface, enhances mechanical properties, and provides a consistent cosmetic finish for production. Vapor smoothed parts can be dyed.
Media Tumbled
Standard finish with the addition of abrasive media tumbling. These parts will have reduced grow lines and sharp edges may be softened by the tumbling process. The parts are left with an eggshell finish.
Nickel Plating
Standard finish with a secondary copper + nickel plating processes adding 0.004"-0.006" nickel coating. Nickel plating adds durability, stiffness, and wear resistance but is not considered cosmetic. Finish is rough nickel.
Additional Finishes
Xometry provides additional SLS finishing and customization options upon request.
Vapor Smoothing SLS 3D Printed Parts
Xometry can vapor smooth 3D printed parts to achieve an exceptional surface finish. Vapor smoothing, performed through AMT PostPro3D's technology, is a batch-based automated smoothing process that achieves a high-quality surface. Combined with the low costs SLS, this surface finish can make parts competitive with injection molding from both form and function. Vapor smoothing creates a uniform, sealed surface with a semi-gloss appearance. SLS parts can be color-dyed. The enhanced surface also increases the overall performance of 3D printed parts including ultimate tensile strength, yield at flex, and percent elongation to break. Vapor smoothing can be applied to HP Multi Jet Fusion, selective laser sintering, and fused deposition modeling parts for both rigid plastics and elastomers.
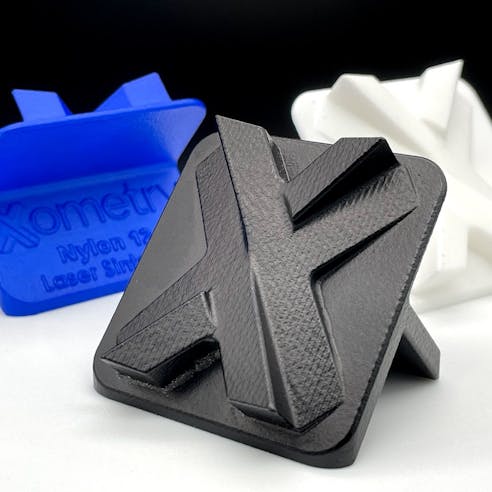
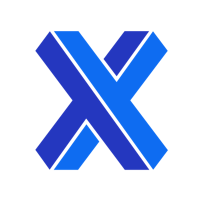
Ready to get started on your 3D printing quote?
Free shipping available for domestic 3D printing orders ; learn more!
Video: What is SLS 3D Printing?
Learn more about SLS 3D printing and how it works in this animation by Xometry:
Applications for Selective Laser Sintering
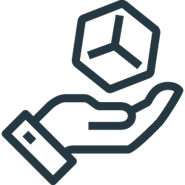
Concept Models
The speed and versatility of SLS printing lets product developers create physical snapshots of their designs through the iterative process.
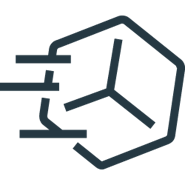
Rapid Prototyping
SLS prototyping can be used to create fully-functional prototypes, complete with moving parts, as well as all-in-one assemblies.
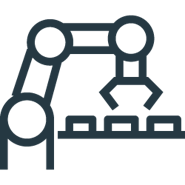
Direct Digital Manufacturing
The high accuracy and consistency of SLS makes it an ideal way to build large quantities of discrete or customized parts.
Advantages of SLS
Durability
Nylon is a durable material with great impact strength, medium flexibility, and high resistance to environmental factors.
Rapid Turnaround
Parts can typically be shipped in 3-4 days, allowing for faster design iterations and speed to market.
Parts Production
SLS is capable of producing end-use parts on-demand, increasing throughput.
Complex Geometry
Geometries can be built more easily due to the 3D printing process, adding complexity without additional cost.
Scalability
SLS can make a single part or component as easily as dozens of production pieces.
Precision
We use the latest generation of SLS technologies to meet tolerances of +/- 0.010” or +/- 0.002” per inch, whichever is greater. Please see our Manufacturing Standards for more details.
SLS General Tolerances
Description | Tolerance Notes |
---|---|
Description General Tolerances | Tolerance Notes SLS Nylon 12 and variants are ± 0.015”, or ± 0.002" per inch, whichever is greater.* SLS Nylon 11 and variants are ± 0.020”, or ± 0.003" per inch, whichever is greater.* *Results are typical. |
Description Build Area | Tolerance Notes Build area up to 13" x 13" x 20". Glass filled can extend up to 26" x 15" x 23". |
Description Minimum Feature Size | Tolerance Notes 0.030" or greater. |
Description Standard Layer Thickness | Tolerance Notes 0.12 mm / .0047" |
This table depicts the general tolerances for selective laser sintering. Stresses during the build and other geometry considerations may cause deviation in tolerances and flatness. Part designs with thicker geometries, flat or broad parts, and parts with uneven wall thicknesses may be prone to significant deviations or warp. Improved tolerances may be possible with a manual quote review, after successful completion of a prototype build, and must be approved on a case-by-case basis. General tolerances apply before secondary finishing or post-processing unless otherwise specified. Please check out Xometry's Manufacturing Standards for more information on tolerances per process.
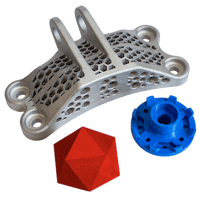
Need to Compare Printing Processes?
Our quick reference guides let you quickly compare different 3D printing processes!
Overview: What is SLS?
The Basics Of Selective Laser Sintering
Selective laser sintering (SLS) is a powder bed 3D printing technology that produces highly accurate and durable parts capable of being used directly in end-use, low-volume production. SLS is a newer 3D printing process that is often thought of as a cousin to the popular metal 3D printing technology direct metal laser sintering (DMLS). Both processes work by utilizing a laser to precisely fuse a bed of powder to construct a part from a 3D CAD file. SLS specializes in nylon or polyamide powder particles to create parts, while DMLS uses metal particles, and is extremely common for prototyping and low volume production.
The Benefits Of Working With Xometry's Selective Laser Sintering Service
Xometry can always help you find the ideal supplier for your specific SLS needs. Our wide network of vetted machine shops contains a wide range of dedicated quick turn SLS partners with a variety of high-quality finishing and material capabilities and many types of sintering systems. Finishing options available include color dyeing, sanding, painting, and plating to meet your needs. From low-volume prototyping to high-volume production, Xometry can always help you source the parts you need on time and at a competitive price, from the U.S. machine shops best suited to the job.
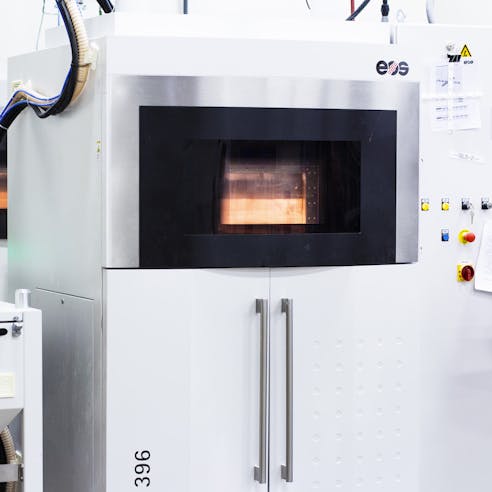
Benefits of SLS 3D Printing
It can be used to make parts using a variety of SLS materials, including plastic, metal, ceramic, or glass powder, making it a popular machining process. Since SLS doesn’t require a support structure like most other 3D printing tech, parts can be made in greater quantities, but with less labor and material expense. Additionally, because the support structure doesn’t need to be removed, there is less risk of damage to the complex internal geometries 3D manufacturing is capable of producing.
SLS can be useful for both rapid prototyping or low-volume production of functional end-use parts. Nylon, especially, is a durable material with great impact strength, medium flexibility, and high resistance to environmental factors. SLS nylon material is also FDA approved USP Class VI/121C certified for skin contact. This combination of complexity, design flexibility, material diversity, rapid turnaround, and overall durability makes SLS an increasingly popular choice in many industries.
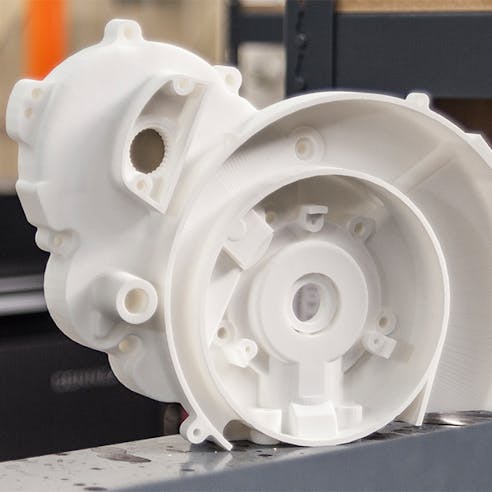
Why Choose Xometry's SLS Printing Service?
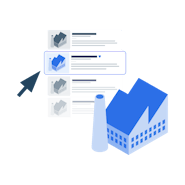
Endless Options
Choose from millions of possible combinations of materials, finishes, tolerances, markings, and certifications for your order.
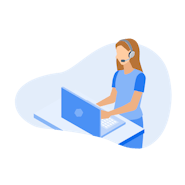
Easy to Use
Get your parts delivered right to your door without the hassle of sourcing, project management, logistics, or shipping.
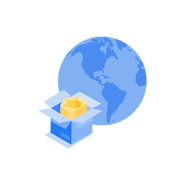
Vetted Network
We are ISO 9001:2015, ISO 13485, IATF 16949, and AS9100D certified. Only the top shops that apply to become Suppliers make it through our qualification process.