Laser-Cut Prototype Services by Xometry
Xometry offers the highest quality custom laser cut prototype services and can assist in the production of parts with intricate and complex geometries and excellent surface finishes.
Laser-cut prototypes are pre-production parts shaped by means of a concentrated beam of electromagnetic energy. Laser cutting is valued for its speed, precision, versatility, and scalability. Some disadvantages of laser cutting make it unsuitable for some applications: high energy consumption, emission of harmful fumes from the material vaporized during the process, and limitations on the thickness of the material that can be processed. However, laser cutting’s capability to quickly and repeatably cut both metals and nonmetals, such as plastics and paper, makes it a popular choice for the fabrication of parts in the aerospace, automotive, medical, and military industries, among others.
Xometry offers the highest quality laser-cut prototyping services. We can fabricate your pre-production components using any required material from aluminum to steel, from Delrin® to polypropylene, and more. Our extensive manufacturing experience makes Xometry a sought-after supplier in the contract manufacturing industry.
What Are Laser-Cut Prototypes?
Prototyping using laser cutting is the non-contact cutting process of using electromagnetic energy to create parts for design and functional verification prior to mass production. Laser cutting technology is made possible by the use of a focused, coherent beam of light that is conditioned by a series of mirrors and lenses to create a spot as small as one square micron. This highly concentrated electromagnetic energy melts and vaporizes the material to be cut along a pre-programmed path while disturbing the rest of the workpiece very little. Laser cutting is a CNC-automated process that requires little human intervention. For that reason, it produces highly repeatable, extremely precise cuts at rapid paces. This makes laser cutting a great choice for prototyping as it allows manufacturers to quickly generate new iterations of a part, verify functionality, and scale up to series production manufacturing.
Laser-Cut Prototype Materials
Many different materials can be used for making laser-cut prototypes. Listed below are some of the materials that can be used to fabricate laser-cut prototypes:
- Carbon-Fiber Composites
- Stainless Steel
- Aluminum
- Delrin®
- Mylar®
- PETG
- Polypropylene
- Styrene
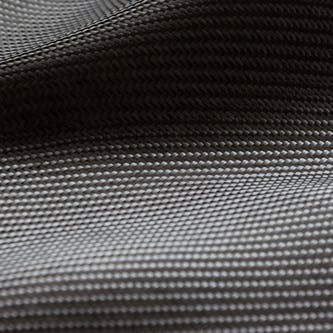
Carbon-Fiber Composites
Hybrid laser cutting machines, or machines that combine CO2 and fiber lasers together into a single laser, are best for cutting carbon-fiber composites. Carbon fiber is typically woven together into materials and then coated with a polymer matrix to secure the material together. The CO2 laser vaporizes the polymer matrix while the fiber laser cuts through the carbon fibers.
Stainless Steel
Stainless steel is a material commonly used for laser-cut prototypes. Stainless steel, along with most metals, can be difficult to cut using CO2 lasers because of its high reflectivity. Laser cutting stainless steel is most easily accomplished using a fiber laser. However, coating the workpiece with a metal marking paste to reduce its reflectivity makes it capable of being cut by a CO2 laser.
Aluminum
Aluminum is another material that is commonly used in laser-cut prototypes. As with stainless steel, aluminum’s reflectivity makes it difficult to cut using CO2 lasers unless its reflectivity is reduced with an appropriate surface treatment. Fiber lasers are the best option when laser cutting aluminum workpieces.
Delrin®
Delrin® is a type of polyoxymethylene (POM) or acetal resin that is trademarked by Dupont. Delrin® is often selected for its mechanical strength, stiffness, and ability for long-term use. Delrin can easily be cut by CO2 lasers to make prototype parts.
Mylar®
Mylar® is a polyester film trademarked by Dupont. Mylar is commonly used in both packaging and as electrical insulation. Mylar is exceptionally easy to laser cut due to its low thickness and low vaporization temperature. CO2 lasers can easily cut Mylar to create intricate prototypes and designs.
PETG
PETG (polyethylene terephthalate glycol) is a type of thermoplastic polyester that is commonly used in food and beverage containers, packaging, medical devices, and machine guards. Its low vaporization temperature makes it exceptionally easy to cut with any type of laser cutting system.
Polypropylene
Polypropylene is rigid and tough. It is often used in consumer products, food packaging, automotive parts, construction machinery components, and more.
Styrene
Styrene is a precursor to the more well-known material, polystyrene. Polystyrene, like other thermoplastics, can easily be processed by laser cutting machines due to its relatively low vaporization temperature compared to the temperatures that laser beams can generate.
Advantages of Laser-Cut Prototypes
There are several advantages of laser-cut prototypes which are listed and described below:
- Short Lead Times
- Innovative and Intricate Designs
- Precision
- Scalability
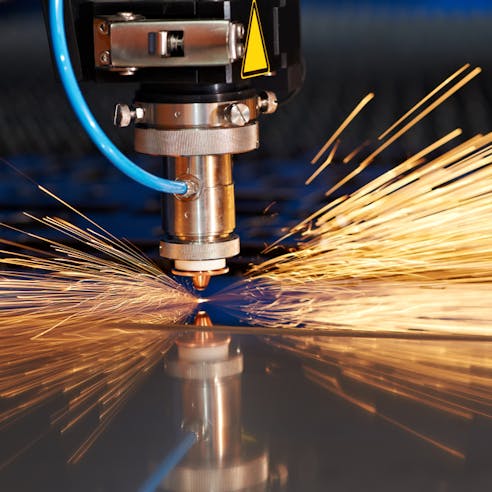
Short Lead Times
Short lead times are common with laser cutting provided that access to a capable laser-cutting machine is available. Additionally, since laser cutting requires no complex tooling, less time is spent curating specialized programs for manufacturing. Overall, this means less time is spent procuring, programming, and calibrating machinery and tooling. Once a part is designed, the lead time is only restricted by how fast the laser cutting machine can be set up.
Innovative and Intricate Designs
Laser cutting can be used to produce innovative and intricate designs. The process can be used to cut parts with complex geometric profiles or to engrave and mark parts with elaborate logos and images. The versatility of laser cutting is one of its biggest advantages compared to other 2D-cutting methods like waterjet cutting or stamping.
Precision
Laser cutting can be used to achieve exceptionally precise dimensions with tolerances of +0.004” (+0.1 mm). Since the process is automated, it is highly repeatable. Additionally, because it’s a non-contact cutting process, the workpiece does not distort due to mechanical or thermal forces and requires little post-processing to obtain finished parts.
Scalability
Prototype parts made by laser cutting can easily be scaled up to production volumes since the production process will be controlled by essentially the same CNC cutting program as was used to make the prototypes. Minor tweaks may need to be made to the laser cutter settings to optimize for material usage and for macro-heating throughout the workpiece. However, as long as the same laser cutting machine is used, laser cutting processes can easily be scaled from prototyping to production.
Disadvantages of Laser-Cut Prototypes
Laser cutting also has disadvantages when it comes to making prototypes which are listed and described below:
- Material Thickness
- Harmful Gasses and Fumes
- High Energy Consumption
- Upfront Costs
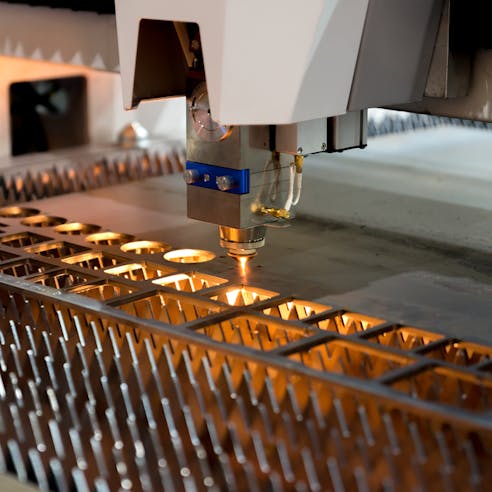
Material Thickness
Laser cutting is not suitable for cutting workpieces more than one inch thick. This is because thicker workpieces require exceptionally powerful laser cutting machines. Additionally, the highly concentrated light beam of a laser naturally diverges as it travels through space. This beam divergence reduces a laser’s cutting effectiveness as workpiece thickness increases.
Harmful Gasses and Fumes
Depending on the material being cut, harmful gasses and fumes can be released during laser cutting. This is commonly the case when cutting thermoplastics like Delrin® (POM) or fiberglass that release formaldehyde or cyanide, respectively. These fumes are toxic. Proper ventilation is required to remove them from the work area to maintain a safe environment for the operator. Although adequate monitoring and ventilation reduce the workplace concentrations of cyanide and formaldehyde to safe levels, their safe release into the atmosphere must also be considered. Regional regulations for air quality define allowable levels that can be released into the environment.
High Energy Consumption
Laser cutting machines consume more energy than other cutting tools. For instance, a 3-axis CNC machine will consume about 1/10th the power of a laser cutting machine when cutting 40 mm steel plate blanks. While laser cutting machines consume more energy than CNC machines, they often complete parts at a much faster pace which can make them more cost-effective for some projects. Still, parts will have different geometric profiles and requirements — and laser cutting machines will not always be advantageous compared to CNC machines in terms of energy consumption.
Upfront Costs
While there are several relatively cheap laser cutting machines available on the market (<$1,000), commercial and industrial-sized laser cutting machines suitable for both prototyping and production are significantly more expensive. A CO2 laser cutting machine can cost anywhere between $2,000 and $1,000,000 while a fiber laser cutting machine costs between $30,000 to $600,000. Compared to a 3-axis CNC mill that may cost anywhere between $60,000-$300,000, laser cutting machines can be expensive.
In need of custom laser-cut prototypes?
Industries Which Use Laser-Cut Prototype
A number of industries take advantage of laser cutting’s capabilities for prototyping. Some of the industries that use laser cutting for prototyping are listed and described below:
- Automotive
- Aerospace
- Heavy Equipment
- Military
- Medical
- Power Generation
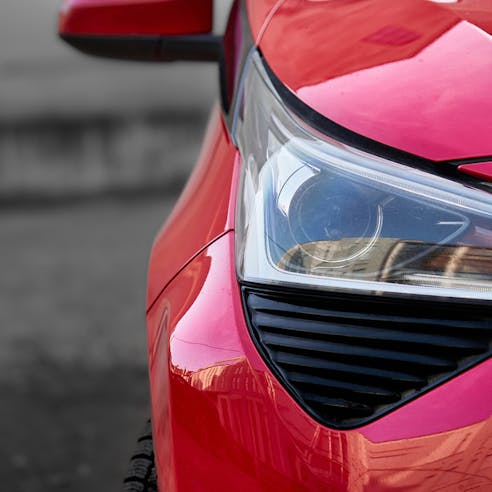
Automotive
Laser cutting’s flexibility and ability to fabricate precise shapes and designs make it a great manufacturing method for the automotive industry. Laser cutting in the automotive industry is commonly used to: create prototypes for, stampings, vehicle hoods, seat frames, brackets, fenders, and more.
Aerospace
Like the automotive industry, the aerospace industry makes use of laser-cut prototypes because the process can quickly and accurately produce complex shapes and can be used on many different types of materials. Aluminum and titanium are the two most commonly used materials in aerospace laser cutting. Examples of laser-cut prototypes in the aerospace industry include: avionics housings, wing assemblies, and more.
Heavy Equipment
Prototypes of components of the heavy equipment commonly used in mining, construction, agriculture, and similar industries often use laser cutting to develop prototypes. This is because of laser cutting’s ability to repeatedly produce highly precise parts at rapid paces. Parts like spreaders, chassis, and boom tube sections for cranes are all examples of parts that can be made by laser cutting.
Military
The military industry utilizes laser cutting for prototyping due to the process’s ability to repeatably produce high-quality, precise designs. Like the civil aerospace and automotive industries, the military industry uses laser cutting to develop prototypes for ground vehicle components and military aircraft components.
Medical
Medical devices and components must satisfy stringent dimensional tolerance requirements, or risk posing a danger to patient health. Because laser cutting is a precise and highly repeatable process, laser cutting is commonly employed in the medical industry. It is often used to make parts for pacemakers, catheters, stents, prosthetic components, and more.
Power Generation
The power generation industry cannot afford any interruptions to the electricity it supplies. Laser cutting’s speed, precision, repeatability, and scalability make it a great choice for power generation prototyping applications like turbine blades, solar panel components, battery housings, and more.
Alternatives to Laser Cut Prototypes
There are several alternatives to laser-cut prototypes if laser cutting is not viable. Xometry offers some alternatives to laser cut prototypes. The alternatives are listed below:
- Waterjet Cutting
- Plasma Cutting
- 3D Printing
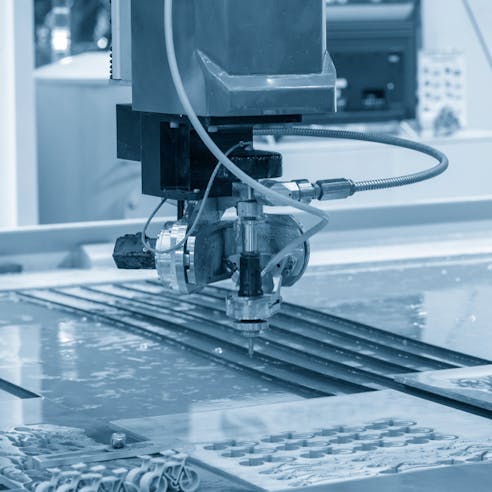
- Waterjet Cutting: Waterjet cutting utilizes high-pressure water (up to 60,000 psi) to cut parts. Abrasives such as garnet are commonly added to the waterjet to improve its ability to cut materials. Waterjet cutting levels of precision are similar to laser cutting. It can produce parts with tolerances as small as +0.02”. However, unlike laser cutting machines, waterjet cutting machines cannot be used to mark or engrave parts and can only be used for cutting entirely through the material.
- Plasma Cutting: Plasma cutting is a viable alternative to laser cutting for the fabrication of prototypes, but is limited to use on metallic workpieces. Plasma cutting uses a stream of hot charged particles called plasma to vaporize the workpiece surface. Plasma cutting is cheaper than laser cutting and can be used to cut thicker workpieces made of metal, but offers less dimensional accuracy and rough cut edges. Therefore, plasma cutting is often used for parts with higher tolerances. Additionally, post-processing is often required to obtain the desired appearance for cut edges.
- 3D Printing: 3D printing, or additive manufacturing (AM), is a viable alternative to laser-cut prototypes. There are some limitations on the kinds of parts that can be made with 3D printing. While the process is capable of printing both plastic and metal parts, it is not as efficient as laser cutting, since significant preparation and post-processing are required like creating parts from powder or filament or trimming away flash after printing. Still, 3D printing can fabricate parts with similar tolerances depending on the particular type of 3D printing used.
Copyright and Trademark Notices
- Delrin® is a trademark of DuPont Polymers, Inc.
- Mylar® is a registered trademark of the DuPont Teijin Corporation.
Why Choose Xometry for Laser-Cut Protoype Services?
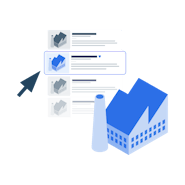
Endless Options
Choose from millions of possible combinations of materials, finishes, tolerances, markings, and certifications for your order.
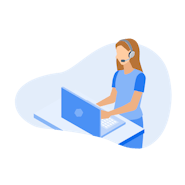
Easy to Use
Get started with our easy-to-use platform and let our experts take care of managing the project from locating the right manufacturing partner to delivery logistics.
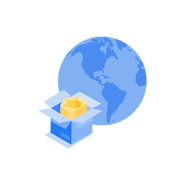
Vetted Network
We are ISO 9001:2015, ISO 13485, and AS9100D certified. Only the top shops that apply to become Suppliers make it through our qualification process.