Chipboard Laser Cutting Services by Xometry
Xometry offers the highest quality chipboard laser cutting services and can assist in the production of parts with intricate and complex geometries and excellent surface finishes.
Laser cutting of chipboard is commonly used in the production of custom furniture and cabinetry. It enables the creation of unique and precise components, enhancing their functionality and overall aesthetic value. Chipboard laser cutting is also invaluable for prototyping and model making, as it allows architects, designers, and engineers to bring their concepts to life with accurate and visually appealing models. The signage and display industry also benefits greatly from chipboard laser cutting. Chipboard laser cutting enables the creation of custom-shaped signs, decorative elements, and eye-catching displays. It provides flexibility in design and catering to both indoor and outdoor applications.
Xometry is a trusted provider of laser-cut chipboard services, offering top-notch cutting solutions for various applications. Laser cutting is a highly precise and efficient process that utilizes a focused light beam to cut through chipboard material with exceptional accuracy even for intricate details. With Xometry's laser-cut chipboard services, customers can expect excellent quality and craftsmanship for their laser-cutting needs in particle board materials.
What Is Laser-Cut Chipboard?
Laser cutting is an efficient method for processing large sheets of chipboard into a variety of shapes and sizes for various applications. Chipboard, also known as particle board or low-density fiberboard (LDF), is an engineered product. It is made from wood particles, such as: sawdust, fibers, or wood scraps bonded together by compressing and laminating them with an adhesive such as resin or glue. LDF sheets must be trimmed to achieve precise dimensions, resulting in a smooth and sanded surface that shows its open-grain texture. These sheets are not only eco-friendly but also free from natural defects, making them a reliable choice.
LDF sheets exhibit excellent resistance to warping and splintering, ensuring their durability and longevity in various applications. Chipboard is known to absorb water unless it is treated against it. This could make it unsuitable for some applications where the board is exposed to moisture. In these cases, plywood might be a better option. Plywood is a lot sturdier than chipboard and will keep its original characteristics in moisture variations, whereas chipboard will start to sag in the same environment.
Laser cutting is a technology that uses a high-powered laser beam to cut through various materials with great accuracy and detail. When applied to particle boards, it allows for the creation of intricate and precise designs, patterns, and shapes with clean edges. Laser-cut chipboard finds applications in various industries and projects, including: arts and crafts, model making, signage, architectural models, flooring, cabinetry, packaging, and prototyping.
Advantages of Laser-Cut Chipboard
Laser-cut chipboard offers several advantages that make it a preferred choice in various applications:
- Recyclable
- Easily Shaped
- Durable
- Cost Effective
- Precision
- Efficiency
- Clean Edges
- Repeatable Results
- Limits Material Waste
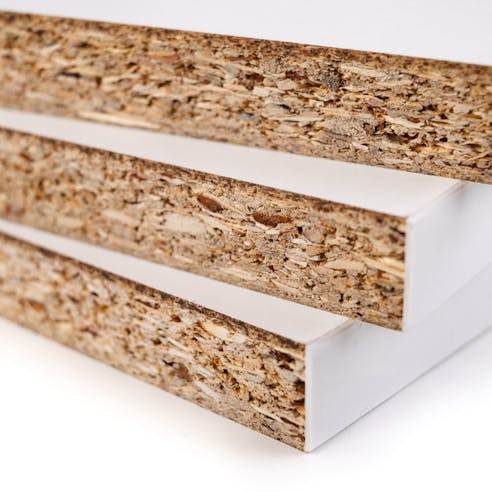
Recyclable
Chipboard is made from recycled wood fibers or particles, making it an environmentally friendly choice. It can be recycled after use, contributing to sustainable practices and reducing waste.
Easily Shaped
Chipboard is relatively easy to shape and work with, including by laser cutting. Its composition allows it to be cut, engraved, or shaped into various forms, making it highly versatile. It also allows for personalized touches, logos, or text to be added. Laser-cut chipboard can be used in various industries and projects, including: arts and crafts, model making, signage, architectural models, packaging, and more.
Durable
Despite being lightweight, chipboard exhibits durability and strength. It can withstand moderate impacts, making it suitable for applications where resilience is necessary. Laser cutting can add to the durability of chipboard. This is done by the clean edges which are produced by laser cutting chipboard. By not hollowing out the material in the middle of the board (between the top and bottom along the cut line), the integrity of the board is preserved.
Cost Effective
Chipboard is an affordable material compared to solid wood or other alternatives. This cost-effectiveness makes it a popular choice, especially for large-scale projects or applications where budget considerations are essential. Laser cutting adds to the cost-effectiveness of the material since it is a fast process that can cut time and ultimately result in time-related cost savings.
Precision
Laser-cutting technology allows for highly precise and intricate cuts, enabling the creation of complex designs and patterns with clean edges. This level of precision ensures the accurate replication of detailed shapes and enhances the overall quality of the final product.
Efficiency
Laser cutting is a fast and efficient process. It eliminates the need for manual cutting which can be time-consuming and less accurate.
Clean Edges
Laser cutting produces clean and precise edges on the chipboard. The process minimizes the need for additional finishing work. The smooth edges eliminate the risk of splintering and gouging out of particles, enhancing the overall appearance and safety of the final product.
Repeatable Results
Laser cutting chipboard produces repeatable results, making it suitable for projects that require identical or replicated components. This consistency, combined with a high level of dimensional accuracy, makes laser cutting an excellent mass-production process for LDF.
Limits Material Waste
Laser cutting chipboard limits material waste. The precise nature of laser cutting allows for the efficient utilization of LDF sheets, minimizing the amount of material that goes to waste. The focused laser beam cuts with high accuracy, reducing the need for large margins.
Disadvantages of Laser-Cut Chipboard
While laser cutting chipboard has many benefits, there are also a few disadvantages to consider:
- Moisture Retention
- Burned Edges
- Cracking
- Adhesive Issues
- Limited Thickness
- Odor and Fumes
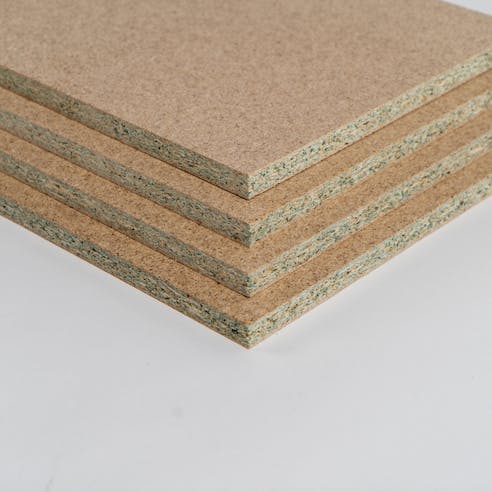
Moisture Retention
Chipboard is not suitable for all applications and environments. It is more susceptible to moisture and humidity than other materials like solid wood or plywood. Therefore, it may not be suitable for projects that require high resistance to moisture or outdoor exposure.
Burned Edges
Laser-cutting chipboard can result in burned edges due to the heat generated by the laser. This can affect the appearance of the final product, especially if the edges are meant to be exposed. Additional finishing or sanding may be required to mitigate the burned appearance.
Cracking
Chipboards, especially thinner sheets, can be prone to cracking during the laser cutting process, particularly if the design involves intricate or tight cuts.
Adhesive Issues
Chipboard contains adhesive agents used to bind the wood particles together. During laser cutting, the heat cause these adhesives to melt or release fumes, which can affect the quality of the cut.
Limited Thickness
Laser cutters may have limitations on the thickness of the chipboard that can be effectively cut. Thicker LDF sheets may require multiple passes or alternative cutting methods, which can increase production time and cost. However, multiple passes have a much higher chance of burned edges, which is something to consider before attempting to cut thicker sheets with a laser cutter.
Odor and Fumes
Laser cutting chipboard can produce odor and fumes due to the burning of the wood material and the adhesive. Adequate ventilation or air filtration systems is required to maintain a safe and comfortable working environment.
Laser-Cut Chipboard Applications
Laser-cut chipboard finds applications in various industries and projects, including:
- Arts and Crafts
- Prototyping
- Customization and Personalization
- Signage and Displays
- Packaging
- Home Decor and Furniture
- Educational Tools
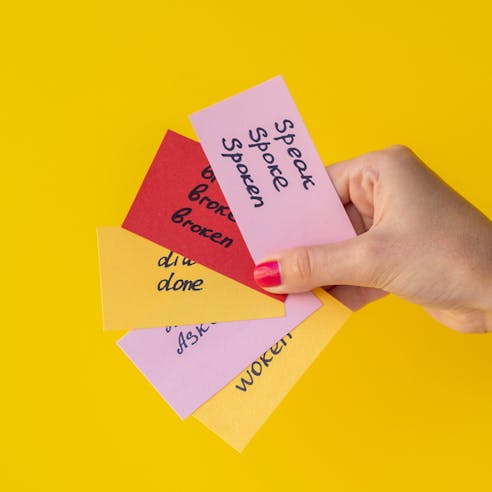
Arts and Crafts
Laser-cut chipboard is popular in the arts and crafts community. It can be used for creating intricate designs, decorative pieces, scrapbooking elements, and embellishments for cards, invitations, and other paper crafts.
Prototyping
Laser-cut chipboard is widely used in the prototyping phase of product development. It allows for quick and accurate fabrication of components or parts to see how the final product will look, check fit-up, and test some (not too many) aspects of function before moving to more expensive manufacturing processes.
Customization and Personalization
Laser cutting provides the ability to customize chipboard with unique designs, patterns, or text. It is a suitable process for creating personalized gifts, wedding favors, promotional items, and branding materials.
Signage and Displays
Laser-cut chipboard can be used for creating custom signage, nameplates, tags, and displays. Its versatility allows for the production of unique and eye-catching designs that can be used in retail settings, exhibitions, events, or interior decor.
Packaging
Chipboard is commonly used in packaging applications, and laser cutting adds a level of potential customization. It can be used to fabricate product packaging, gift boxes, point-of-sale displays, or custom inserts to securely hold items.
Home Decor and Furniture
Laser-cut chipboard can be incorporated into home decor and furniture pieces. It can be used for wall art, decorative panels, lampshades, clocks, room dividers, or even furniture components such as chair backs or table tops.
Educational Tools
Chipboard can be laser cut to create educational tools such as puzzles, flashcards, learning aids, or interactive displays for classrooms or educational institutions.
In need of custom chipboard laser cutting services?
Alternatives to Laser-Cut Chipboard
Here are some alternative services offered by Xometry that can be used instead of laser cutting to cut chipboard:
- Die Cutting
- CNC Routing
- Hand Tools
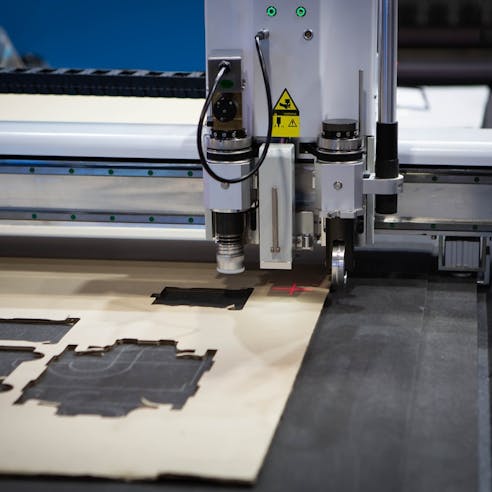
- Die Cutting: Die cutting involves using a custom-made die to cut chipboard into specific shapes or patterns. This method is commonly used in mass production and allows for consistent and efficient cutting. It is often utilized for creating packaging, displays, and paper-based products.
- CNC Routing: Computer Numerical Control (CNC) routers can precisely cut chipboard based on a programmed design. CNC routing machines use rotating cutting bits to achieve accurate and intricate cuts. This method is ideal for large-scale production or complex cutting patterns.
- Hand Tools: Traditional hand tools like hand saws, coping saws, or utility knives can also be used to cut chipboard. While these methods may not offer the same precision as power tools, they are suitable for small-scale projects.
Why Choose Xometry for Chipboard Laser Cutting Services?
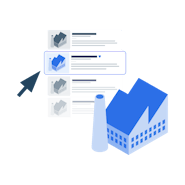
Endless Options
Choose from millions of possible combinations of materials, finishes, tolerances, markings, and certifications for your order.
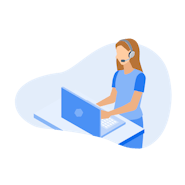
Easy to Use
Get started with our easy-to-use platform and let our experts take care of managing the project from locating the right manufacturing partner to delivery logistics.
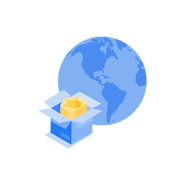
Vetted Network
We are ISO 9001:2015, ISO 13485, and AS9100D certified. Only the top shops that apply to become Suppliers make it through our qualification process.