Gas Welding Service by Xometry
High quality custom gas welding services available with a variety of materials, manufacturing processes, finishes, and more. Subject to availability. Xometry doesn't guarantee that we can provide this service at any given time.
Xometry, a leading manufacturing platform, offers the highest quality gas welding services to meet diverse welding needs. At Xometry we adhere to the strict guidelines and best practices of the welding industry, which is why we are both ISO 9001:2015 and AS9100D certified. Our extensive capabilities and comprehensive offerings position us as a leading welding service. Xometry's gas welding services guarantee precise components, fast turnaround times, and exceptional customer service.
Gas welding, also known as oxy-fuel welding, is a versatile process that utilizes a combination of fuel gas and oxygen to generate a flame for melting and joining metal parts. This welding technique provides numerous advantages, including its portability, simplicity of operation, and precise heat control. Gas welding finds application in a wide range of industries, with its top three applications being automotive repairs, metal fabrication, and maintenance work.
What Is Gas Welding?
Gas welding, also known as oxy-fuel welding or oxyacetylene welding, involves utilizing the heat produced by the combustion of fuel gas to effectively join or cut metals. The most commonly used fuel gas in gas welding is acetylene, although other gases like propane or natural gas can also be used. This welding technique holds significant importance due to its wide range of applications.
The process involves a welding torch that combines the fuel gas and oxygen in the correct proportions, creating a high-temperature flame. With a flame temperature reaching around 3,100 °C, gas welding possesses the capability to effectively melt and join steel as well as other metals. This flame is directed onto the metal workpiece, causing the metal to reach its melting point. As the metal becomes molten, it can be manipulated or joined with other metal parts to form a strong bond.
Different types of flames play a crucial role in determining the outcome and properties of a weld joint in gas welding. The profile of the flame can be adjusted by controlling the flow rates of the fuel gas and oxygen. The types of flames are listed below:
- Neutral Flame: A neutral flame is achieved when an equal volume of fuel gas and oxygen is used. This flame ensures complete combustion, minimizing smoke generation and preserving the properties of the weld metals. It consists of two zones: a white inner zone with a temperature of approximately 3,100 °C and a blue outer zone with a temperature of around 1,275 °C. The neutral flame is commonly preferred for welding metals like cast iron, mild steel, and stainless steel.
- Carburizing Flame: A carburizing or reducing flame is obtained by increasing the amount of fuel gas relative to oxygen. This flame produces smoke and chemically forms metal carbide. It is characterized by three zones: a white inner zone (around 2,900 °C), a red intermediate zone (approximately 2,500 °C), and a blue outer zone (about 1,275 °C). The carburizing flame is typically used for welding nickel, steel alloys, and non-ferrous metals.
- Oxidizing Flame: An oxidizing flame is created when there is an excess of oxygen compared to the fuel gas. This leads to higher flame temperatures as it exits the welding torch compared to the neutral flame. The oxidizing flame consists of two zones: a blue outer zone at around 1,275 °C and a white inner zone with a temperature of roughly 3,500 °C. It is suitable for welding metals such as brass, bronze, copper, and zinc.
Gas welding is versatile and finds extensive application in various industries, including: automotive, manufacturing, construction, and repair work. It is particularly valuable for welding thin metal sheets or components, as it allows for precise control of the heat input. Additionally, gas welding can be used for cutting metal by directing the intense flame onto a specific area, resulting in localized melting and severing of the metal.
Advantages of Gas Welding
Gas welding offers many advantages, such as:
- Different Types of Metals
- Does Not Require Electricity
- Cost Effective
- Portable Gear
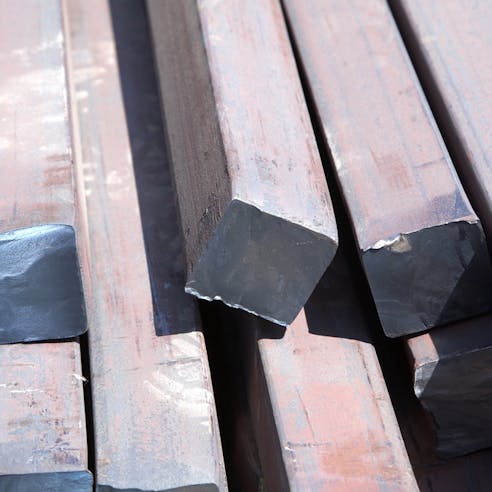
Different Types of Metals
Gas welding is versatile and can be used to weld a wide range of metals, including carbon steel, stainless steel, cast iron, copper, and aluminum. This flexibility makes it advantageous in industries in which various metal types need to be joined, such as automotive repair shops, plumbing, and metal fabrication.
Does Not Require Electricity
Gas welding does not rely on electricity or an external power source like arc welding. This makes it suitable for environments in which electricity is not available or poses a safety hazard.
Cost Effective
Gas welding is generally considered more cost-effective compared to certain high-end welding techniques, such as laser or electron beam welding. The initial investment required for gas welding equipment is relatively low, making it an affordable option for small-scale welding operations. The consumables used in gas welding are also relatively affordable, making it a preferred choice for projects with budget constraints.
Portable Gear
Gas welding equipment is relatively portable compared to other welding processes. The equipment consists of cylinders for fuel gas and oxygen, hoses, regulators, and a welding torch. This portability makes gas welding suitable for on-site repairs and applications in remote locations.
Disadvantages of Gas Welding
Gas welding, despite its advantages, does have some disadvantages that are important to consider. Here are three key drawbacks of gas welding:
- Low Surface Finish
- Not Suitable for Thick Materials
- Slow Rate of Heating
- Not Suitable for High-Strength Steel
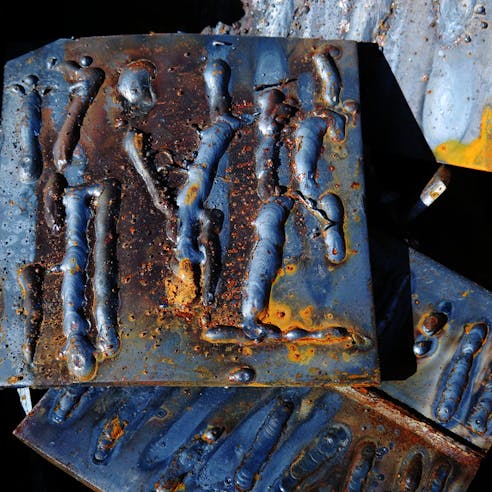
Low Surface Finish
Gas welding can result in a lower surface finish quality compared to other welding processes, such as TIG (Tungsten Inert Gas) welding or laser welding. The molten metal in gas welding tends to be more fluid, which can lead to greater weld bead irregularities, surface imperfections, and the need for additional post-welding finishing processes. This can be a disadvantage when aesthetics or precise surface smoothness are critical, such as in industries like aerospace or decorative metalwork.
Not Suitable for Thick Materials
Gas welding is generally not the preferred method for welding thick materials. It may struggle to provide sufficient heat input to achieve complete penetration and sound welds in thicker metal sections. As a result, gas welding is commonly limited to thinner materials, typically up to around 5–6 mm in thickness. When dealing with thicker metal components, processes like arc welding or submerged arc welding are typically more suitable.
Slow Rate of Heating
Gas welding has a relatively slow rate of heating compared to some other welding techniques. The heat transfer in gas welding relies on the combustion of the fuel gas and oxygen mixture, which can be slower compared to electric welding methods that utilize high-energy arcs or lasers. This can lead to longer welding cycle times and make gas welding less efficient for high-production welding operations.
Not Suitable for High-Strength Steel
Gas welding is not suitable for all high-strength steels due to its inherent characteristic of affecting the mechanical properties of the parent metals in the heated zone.
Applications and Industries of Gas Welding
Gas welding finds different applications in different industries. The different uses of gas welding and the different industries in which gas welding is useful are listed and defined in the sections below:
- Repair Works
- Fabrication of Sheet Metal
- Aircraft
- Automotive
- Joining High-Carbon Steel
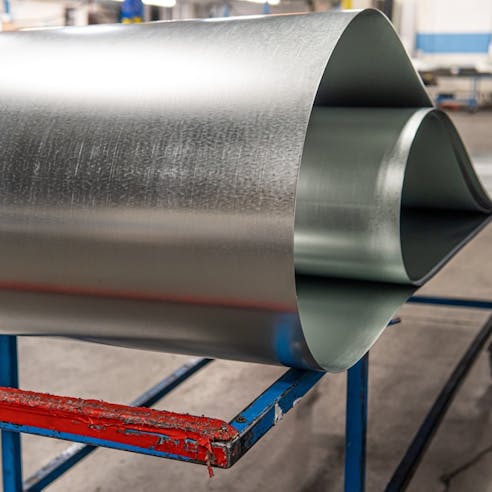
Repair Works
Gas welding is widely used in repair and maintenance work. It can be utilized to repair or join metal components in various industries such as: automotive, construction, plumbing, and manufacturing. Gas welding is particularly useful for repairing cracks, fractures, or worn-out sections in metal structures or equipment.
Fabrication of Sheet Metal
Gas welding is commonly used in the fabrication of sheet metal. It allows for precise control of heat and can effectively join thin metal sheets together. This application is relevant in industries such as: HVAC (heating, ventilation, and air conditioning), metal furniture manufacturing, and architectural metalwork.
Aircraft
Gas welding finds application in aircraft manufacturing and repair. It can be utilized for joining metal components in the construction of aircraft structures, such as fuselage frames or engine mounts. Gas welding offers good control over the heat input, which is crucial when working with lightweight and heat-sensitive aircraft materials.
Automotive
Gas welding has various applications in the automotive industry. It can be used for repairs, customizations, and fabrication of automotive components. Gas welding is often employed to join or repair exhaust systems, frame sections, and body panels in automotive repair shops and custom car shops.
Joining High-Carbon Steel
Gas welding is particularly suitable for joining high-carbon steel, which can be challenging to weld using other methods due to the risk of overheating and brittleness. Gas welding allows for controlled heat input, minimizing the potential for material distortion and preserving the strength of the weld joint.
Alternatives to Gas Welding
Xometry offers a wide range of top-quality welding and cutting services. Alternative welding services offered by Xometry include:
- Arc Welding
- Laser Welding

- Arc Welding: Arc welding encompasses various techniques such as shielded metal arc welding (SMAW), gas metal arc welding (GMAW), and tungsten inert gas welding (TIG). These methods utilize an electric arc between an electrode and the metal workpiece to generate the heat necessary for melting and joining metals.
- Laser Welding: This method uses an extremely concentrated laser beam to effectively melt and fuse metal parts together. This technique provides precise control, enables high welding speeds, and minimizes distortion, making it well-suited for a wide range of applications.
Why Choose Xometry for Gas Welding Services?
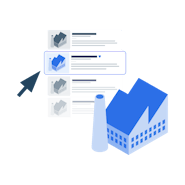
Endless Options
Choose from millions of possible combinations of materials, finishes, tolerances, markings, and certifications for your order.
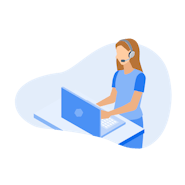
Easy to Use
Get started with our easy-to-use platform and let our experts take care of managing the project from locating the right manufacturing partner to delivery logistics.
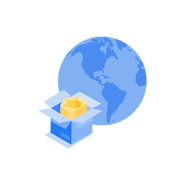
Vetted Network
We are ISO 9001:2015, ISO 13485, and AS9100D certified. Only the top shops that apply to become Suppliers make it through our qualification process.