CNC Turning Service
Instant quotes on custom metal and plastic turned parts | Quick-turn prototypes and production parts in days | Free standard shipping on all US orders | International prototype pricing includes tariffs | ISO 9001:2015, ISO 13485, IATF 16949:2016, AS9100D certified. ITAR registered.
CNC Turning with Xometry
With access to a network of over 10,000 shops, including those with CNC lathes and turning centers, Xometry provides you with the capacity and capabilities your project needs, while also delivering the most competitive pricing and lead times. Xometry's machine learning-trained technology platform also provides instant manufacturability feedback to ensure that your part is optimized for the CNC turning process and fits the requirements you need.
Our on-demand manufacturing platform can deliver high-quality metal and plastic CNC turning parts for rapid prototyping or low-to-high volume production runs. Get an instant quote from your 3D CAD file today. The price for your turned prototypes includes tariffs and shipping for standard parcels.
Xometry CNC Materials
Material | Available Varieties |
---|---|
Material Aluminum | Available Varieties Aluminum 5052, |
Material Brass/Bronze | Available Varieties Brass C360, |
Material Copper | Available Varieties EPT Copper C110, |
Material Plastics | Available Varieties ABS, |
Material Steel | Available Varieties Alloy Steel 4130, |
Material Titanium | Available Varieties Titanium Grade 2, |
Material Zinc | Available Varieties Zinc Sheet Alloy 500 |
Additional alloys and tempers are available upon request. We can source to your project specifications.
Custom Sourced Materials
Various CNC-turned metal and plastic part options are available for an instant online quote. If you do not see the material stock you are looking for, please choose "Other" under the material drop-down on your quote page and submit for an expert engineering review once you have specified features, tolerances, inspection needs, and quantities required.
Finishes
As-Milled
The finish option with the quickest turnaround. Parts are left with visible tool marks and potentially sharp edges and burrs, which can be removed upon request. Surface finish is comparable to 125 uin Ra finish.
Bead Blast
The part surface is left with a smooth, matte appearance.
Anodized (Type II Or Type III)
Type II creates a corrosion-resistant finish. Parts can be anodized in different colors—clear, black, red, and gold are most common—and is usually associated with aluminum.Type III is thicker and creates a wear-resistant layer in addition to the corrosion resistance seen with Type II.
Powder Coat
This is a process where powdered paint is sprayed onto a part which is then baked in an oven. This creates a strong, wear- and corrosion-resistant layer that is more durable than standard painting methods. A wide variety of colors are available to create the desired aesthetic.
Custom
Don’t see the finish you need? Submit an RFQ and we’ll look into a finishing process for process for your custom lathe work.
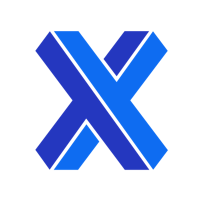
Ready to get started on your CNC turning quote?
Free shipping available for domestic CNC machining orders ; learn more!
Applications of CNC Turning
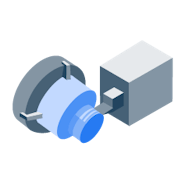
Rapid Tooling
Because CNC can be applied to virtually any material, it is perfect for rapid tooling, i.e., creating fixtures or molds.
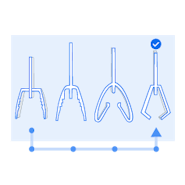
Rapid Prototyping
The range of materials available, low cost per unit, and speed of production makes CNC a great option for prototyping.

Serial Production
High-quality finish, vast material options, and precise tolerances have made CNC lathe turning a favorable technology for serial production parts.
Advantages of CNC Turning
Rapid Turnaround
Using the latest CNC machines, Xometry produces highly accurate, quick turn parts in as fast as 1 day.
Custom Finishes
Select from a variety of finishes on solid metal and plastic parts, built to precise design specifications.
Material Selection
Choose from over 50 metal and plastic materials. CNC Machining offers a wide variety of certified materials.
Precision
Offers high-precision tolerances ranging from +/-0.001″ – 0.005″, depending on customer specs.
Scalability
CNC Machining is perfect for production of 1-10,000 CNC machined parts.
CNC General Tolearances
Description | General Tolerance |
---|---|
Description Distance Dimensions | General Tolerance For features of size (Length, width, height, diameter) and location (position, concentricity, symmetry) +/- 0.005”. |
Description Orientation and Form Dimensions | General Tolerance 0-12" +/- 0.005", Angularity 1/2 degree. For 24" and beyond please consult Xometry's Manufacturing Standards. |
Description Edge Condition | General Tolerance Sharp edges will be broken and deburred by default. Critical edges that must be left sharp should be noted and specified on a print. |
Please check out Xometry's Manufacturing Standards for more information on tolerances per process. Unless we have agreed to other tolerances in your Quote, we will work to achieve and hold the tolerances noted.
Overview: What is CNC Turning?
The Basics Of CNC Lathes
A CNC lathe machine, also called live tooling lathes, is ideal for cutting any symmetrical cylindrical or spherical parts. Characteristically, a lathe spins a workpiece on a vertical or horizontal axis, while a fixed shaping instrument moves around it on a more or less linear path. The act of cutting a workpiece on a CNC lathe is called turning.
How CNC Turning Works
CNC lathes use a subtractive method to create the desired shape. With the G-Code created, a blank bar of stock material is loaded into the chuck of the lathe's spindle. The chuck holds the workpiece in place while the spindle spins. When the spindle is up to speed, a stationary cutting tool is brought into contact with the workpiece to remove material until the desired geometry is achieved.
There are many operations that can be performed on a live tooling lathe, including facing, threading, knurling, drilling, boring, reaming, and taper turning. Different operations require tool changes and can increase cost and set-up time.
When all machining operations are completed, the part is cut from the stock for further post-processing. The CNC lathe is then ready to repeat the operation with little-to-no set-up time in between.
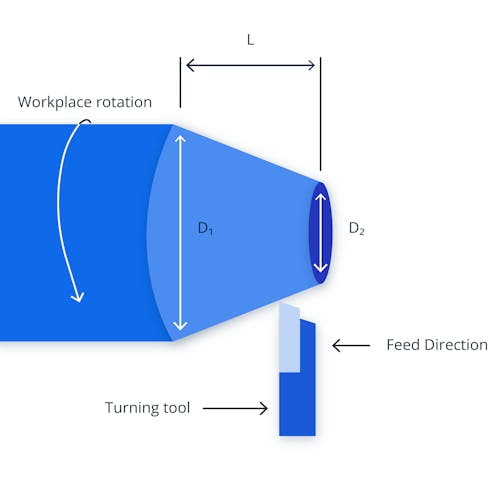
Types Of CNC Lathes
There are many types of lathes, but the most common are 2-axis CNC lathes and Swiss-type lathes. Swiss-type lathes are unique in that stock material is fed through a guide bushing, allowing the tool to cut nearer to the point of support, which makes them particularly useful for long, slender CNC lathe parts and micromachining. Some Swiss-type lathes also come equipped with a second tool head that operates as a CNC mill, allowing them to perform multiple machining operations without having to move the workpiece to a different machine. This makes Swiss-type lathes extremely cost-effective for complex turned parts with CNC lathe services.
Benefits Of CNC Turning
Like CNC mills, CNC lathes can be easily set up for high repeatability, which makes them great for everything from rapid prototyping to low and high-volume production. Multi-axis CNC turning centers and Swiss-type lathes allow for multiple machining operations in one machine. making them a cost-effective option for complex geometries that would otherwise require multiple machines or tool changes in a traditional CNC mill.
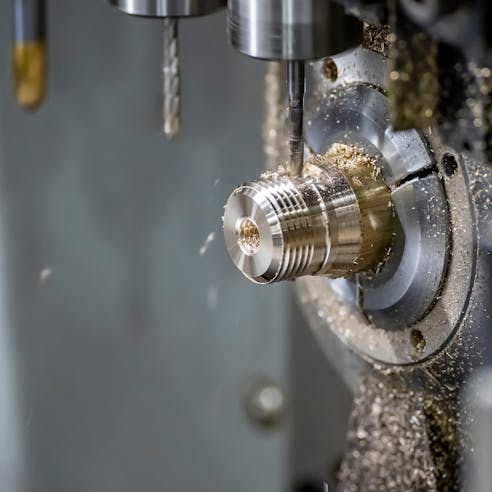
Instant Quote Demo
See how simple it is to get an instant quote for CNC turning using the Xometry Instant Quoting Engine®.
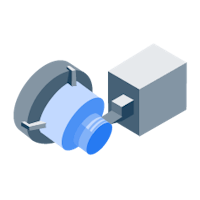