Design Guide: Stereolithography (SLA) 3D Printing
SLA 3D printing is a highly-versatile platform for making custom parts in prototype and production settings; often acting as a stand-in for injection molded plastic parts. Learn how you can apply SLA to your next project with our free guide.
Download the Guide
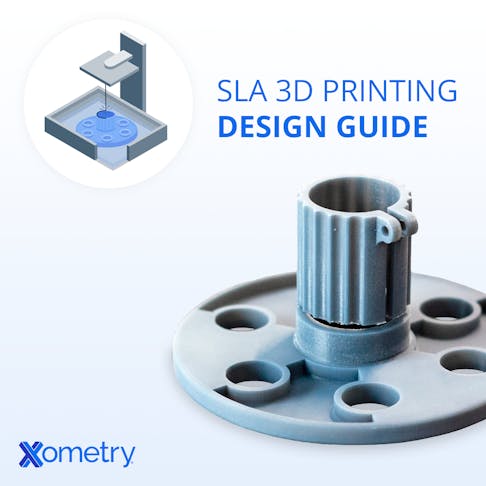
Explore Stereolithography (SLA) – an additive manufacturing process using UV light to solidify liquid resin. Learn about different SLA types (laser-based, mSLA, DLP) and its benefits: high detail, smooth finishes, and precision. Discover Xometry's SLA standards, tolerances, and design guidelines. Review available SLA materials and finishes.
An Inside Look at the Table of Contents
Introduction
- What is Stereolithography?
- Different Types of SLA
- SLA Manufacturing Standards
- General Manufacturing Standards
- Tolerances and Resolution
Design Guidelines
- Wall Thickness
- Holes & Gaps
- Wire Features
- Overhangs & Bridges
- Engravings & Embossing
- Fillets & Drafts
Materials
- General Purpose
- Durable
- Clear
- Highly Stiff
- Specialty
Finishes
- Matte & Natural
- Strip & Ship
- Quick Clear
Additional Resources
- Material Comparison Charts
- Xometry Resources
About Xometry
Stereolithography (SLA) is a powerful 3D printing technology that produces extremely accurate and high-resolution parts that are capable of being used directly in end-use, low-volume production, or for rapid prototyping. Stereolithography 3D printing is a highly versatile platform for making custom parts in prototype and production settings, often acting as a stand-in for injection-molded plastic parts.
Xometry offers both standard and high-resolution options for fine detail parts, and can also print larger-sized parts and products, offering up to a 29-inch build area. In addition, Xometry's manufacturing partner network allows us to offer a larger variety of materials than other 3D printing companies - we offer a wide range of Accura-, Somos-, and Formlabs-branded materials.
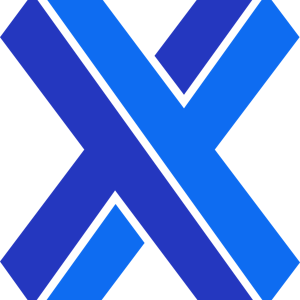