In recent years, traditional casting techniques have merged with 3D printing to create custom molds with detailed designs that were previously difficult (and sometimes impossible) to achieve. We’ll go over exactly how to create these casting molds with 3D printing, but first, we’ll offer a quick look at what they are, and their pros and cons.
What are 3D Molds for Casting?
3D molds for casting are essentially shapes or forms made using 3D printing technology. They are then used to create objects by pouring liquid materials like metal, plastic, or silicone into them (kind of like those ice trays that can create ice cubes in the shape of fruit or animals). Once the material hardens, the mold is removed to reveal the final product.
Pros and Cons
Because 3D printing makes items from a computer design created with 3D printing software, you can make complex and custom molds that would be practically impossible to create with traditional mold-making techniques. It’s a speedy process, churning out molds in no time, and if your mold doesn’t turn out as you’d hoped, you can easily tweak the design file and hit print again.
It also works out to be more cost-effective in the long run because you only need a digital design, a 3D printer, and the printing material — no expensive tooling necessary. It only uses the material it needs, so there won’t be much waste either.
For full transparency, buying a 3D printer, especially a fairly good one, can be expensive. The molds often need a little extra post-processing work, like sanding or sealing, to get the best quality, and sometimes the surface of a 3D-printed mold isn't as smooth as what you’d get from traditional methods.
Also, 3D-printed molds might not last as long as traditionally made ones, especially under high stress or temperatures. However, the only real aspect where traditional mold-making techniques beat 3D printing ones is the size of the molds you can make. With 3D printing, the mold’s size is restricted by the size of your 3D printer.
Guide to Making 3D Molds
As long as you know what you’re doing, it’s quite simple to make 3D-printed molds for casting, so we prepared some step-by-step instructions for you.
1. Design a CAD model
The first step is to design your mold using CAD (computer-aided design) software and create a 3D digital model of what you want to cast. Some popular CAD software options are Autodesk Fusion®, SolidWorks®, and Tinkercad®. Make sure you’ve got all the details down, including draft angles and parting lines to help you easily remove the final object from the mold.
You’ll also want to check the wall thickness to ensure the mold is strong enough for the casting material. You might want to include extra features like channels for pouring the material (runners or sprues) and vents to let air escape. Our top tips for this step are to keep the design simple, go for symmetrical designs, and avoid filled objects within hollow spaces.
2. Decide on a hollow or solid mold
You then have to decide if your model will be hollow or solid because the casting process is slightly different for each. Hollow models are slightly more complicated because they require an internal structure that needs to be removed after casting. Solid models don’t need internal support so are generally easier to make. If you’re making a solid model, you can skip ahead to step 4.
3. Design the inside structure
For hollow models, you’ll need to create an internal structure inside the mold. Your final piece will have a hole somewhere that’s large enough to allow the removal of the supporting material when the cured resin is stretched. You can make the solid block inside your hollow model using CAD software. Align this block within the hollow space, then add support pieces to keep the structure in place during casting (you’ll have to remove this later). This step basically ensures that the final cast doesn’t lose its shape when the mold is removed. An example is below:
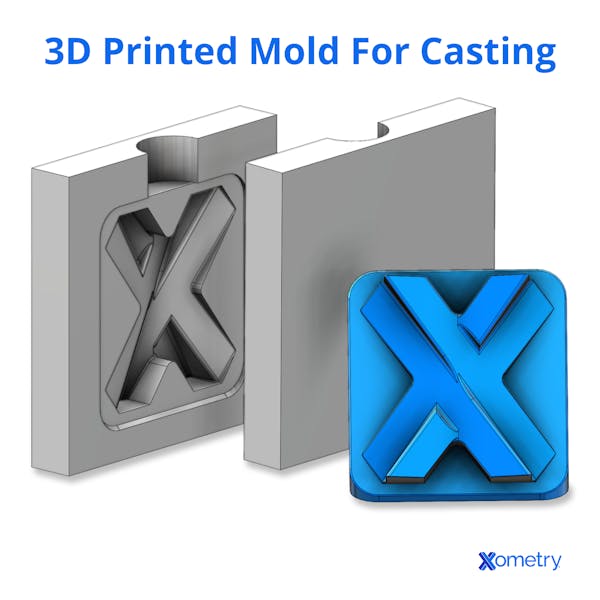
4. Create a solid block
To create a block around your model that will form the outer walls of the mold, you’ll need to make it watertight (if it isn’t already solid — if it is, go ahead and skip this step). Design a larger block around it to make sure the model is centered; the model should be surrounded by the block, with space between it and the block’s inner walls. Then combine the block and model into one object. Congratulations! You now have the block that will define the shape and size of your final cast.
5. Split the block
If you have a really complex model, you might need to split the block into two or more pieces to allow for easy removal after casting. Think about where it would be best to make the split so that it will make the process easier without damage. For example, if your model is ball-shaped, you’ll need at least one split along the middle so that you can easily pull the sections apart.
The splits will need to give you access to the inside of the model so that you don’t end up squishing or damaging it. Our top tip in this section is to avoid making wedges or shapes that would make the block difficult to remove. For smaller, simpler designs, you can likely skip this step.
6. Embed the model into solid blocks
Next, put your model inside the split blocks sideways so that it’s centered. This will ensure you get equal coverage on both sides when the blocks are put together. Make sure that the blocks fit snugly around the model when you bring them together and that you add alignment pins to help guide the mold halves together for a perfect fit.
You should also add a central channel to pour the material into, and this should be wide enough for the resin to flow smoothly, and prevent blockage, or air bubbles from forming. We recommend designing a chamber for extra resin that sits on top of the mold; gravity will help pull it down into the mold, and you can make it as big or small as you like to hold the exact amount of resin you need.
7. Start 3D Printing
This is the fun part — you can now start printing your mold. Make sure your 3D printer is ready, properly calibrated, and with the right material loaded, whether it’s pouring resin into the chamber or adding a spool of filament. Check that the printer bed is clean and level and that the printhead or extruder isn’t obstructed in any way. Use slicing software to prep your design for printing. This software tells the printer how to build the mold layer by layer (or one “slice” at a time), and gives it precise instructions on things like layer height, infill density, and print speed. When you’re done, hit print and keep an eye on the process to catch any issues early on.
8. Pour silicone into the 3D-printed mold
Once the mold is printed (and you’ve taken a few moments to admire your handiwork), it’s time to form the actual cast inside your 3D-printed mold. Mix the silicone according to the instructions on the pack, and pour it into the mold. Do this slowly and evenly from one end, allowing the silicone to properly fill the cavities, and taking care to avoid air bubbles. If bubbles do form, gently tapping or shaking the mold should get rid of them.
If air bubbles are the bane of your life, you can always get a vacuum chamber or a pressure pot designed especially for silicone casting to remove air bubbles easily. Allow the silicone to fully harden—the silicone’s instructions will tell you how long this will take—before you carefully remove the mold. If you have splits, you can separate the halves; otherwise, you can flex the mold to release the cast.
9. Trim away any excess
After the cast has cured and been removed from the mold, trim away any excess material that might have leaked out or formed around the edges with an appropriate tool, like a hobby knife or scissors. Do this slowly and carefully so you don’t accidentally cut into the actual cast.
How Xometry Can Help
Xometry offers a wide range of manufacturing services. We focus on on-demand precise manufacturing with methods such as die casting, urethane and silicone casting, injection molding, CNC machining, milling, turning, 3D printing, and sheet metal fabrication. To learn more, or get your free quote, please reach out to a Xometry representative.
Copyright and Trademark Notices
- Fusion®, Tinkercad®, and AutoCAD® are trademarks of Autodesk, Inc., and/or its subsidiaries and/or affiliates, in the United States
- SolidWorks® is a registered trademark of Dassault Systèmes SolidWorks Corp
- Rhino3D® is a registered trademark of Robert McNeel & Associates
Disclaimer
The content appearing on this webpage is for informational purposes only. Xometry makes no representation or warranty of any kind, be it expressed or implied, as to the accuracy, completeness, or validity of the information. Any performance parameters, geometric tolerances, specific design features, quality and types of materials, or processes should not be inferred to represent what will be delivered by third-party suppliers or manufacturers through Xometry’s network. Buyers seeking quotes for parts are responsible for defining the specific requirements for those parts. Please refer to our terms and conditions for more information.
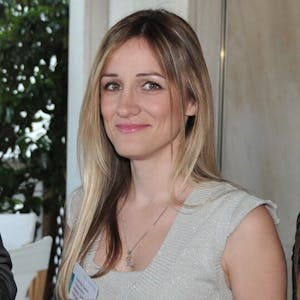