Fused Deposition Modeling (FDM) is a 3D printing technology that uses a polymer filament to ‘draw’ slices of a 3D file. It bonds the filaments to one another by partially melting them. PolyJet is also a 3D printing technology, but it works by inkjet-printing a ‘picture’ of each slice in modified acrylic resin. This picture is then fully cured using a UV light attached to the print head.
One big difference between FDM vs. PolyJet is the materials used. FDM uses filaments of common plastics while PolyJet simulates those materials using various resins. This results in a significant price difference between the two. FDM is also limited in resolution by filament diameter. PolyJet, however, is limited only by inkjet resolution, making its minimum feature size 5 to 20 times smaller than FDM. This article will further discuss the similarities and differences between FDM vs. PolyJet and provide alternatives to both.
FDM Definition and Comparison to PolyJet
FDM technology was first created in 1988 by Scott Crump. The process works by melting a plastic filament in the print head. The temperature is controlled so that it delivers plastic in a gel state that has enough energy to fuse, but not enough to flow. The printing head translates in the X-Y plane and extrudes this gel as a continuous strand. The strands fuse together, but even the best printers cannot prevent porosity or make the material homogeneous.
FDM prints successive 2D slices of a model to build a solid 3D representation of the file. The nozzle moves horizontally to pack strands neatly against the layer below. FDM offers two major advantages over PolyJet: material and machine costs. FDM material generally costs 1/10 as much per kilogram as PolyJet resin. The machines are also three to five times cheaper.
To learn more, see our article on the FDM Printing Process.
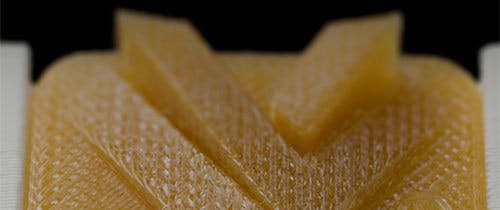
Advantages and Disadvantages of FDM Compared to PolyJet for Making Your Parts
Listed below are the advantages of FDM vs. PolyJet:
- FDM printing materials are cheaper than those for PolyJet.
- Faster builds are possible with FDM using low resolution.
- FDM wastes less material.
- FDM machines require less maintenance.
And here are some disadvantages of FDM vs. PolyJet:
- FDM has a poorer resolution along all three axes.
- FDM layers do not fully fuse, so they are weaker than PolyJet. This creates anisotropic strength in printed parts.
- FDM has a poorer resolution, so it is cosmetically inferior.
- Poorer resolution means some small model features will be blunted or left out of FDM models.
PolyJet Definition and Comparison to FDM
PolyJet modeling was developed in 1998 by Objet Geometries. The process makes a plastic 3D representation of a computer model by printing a layer of liquid photopolymer with an inkjet dispenser and curing the liquid during each print head pass. The inkjet process allows high resolution. Because each dot of liquid is small, PolyJet resolves fine details well. PolyJet can apply multiple resins in one pass. It can alter overall properties by proportioning rubber and rigid resin and can ‘overmold’ parts onto rigid structures all in one build.
Compared to FDM, PolyJet can print parts with smoother surfaces. It is also capable of printing fine details.
To learn more, see our guide on What is PolyJet.
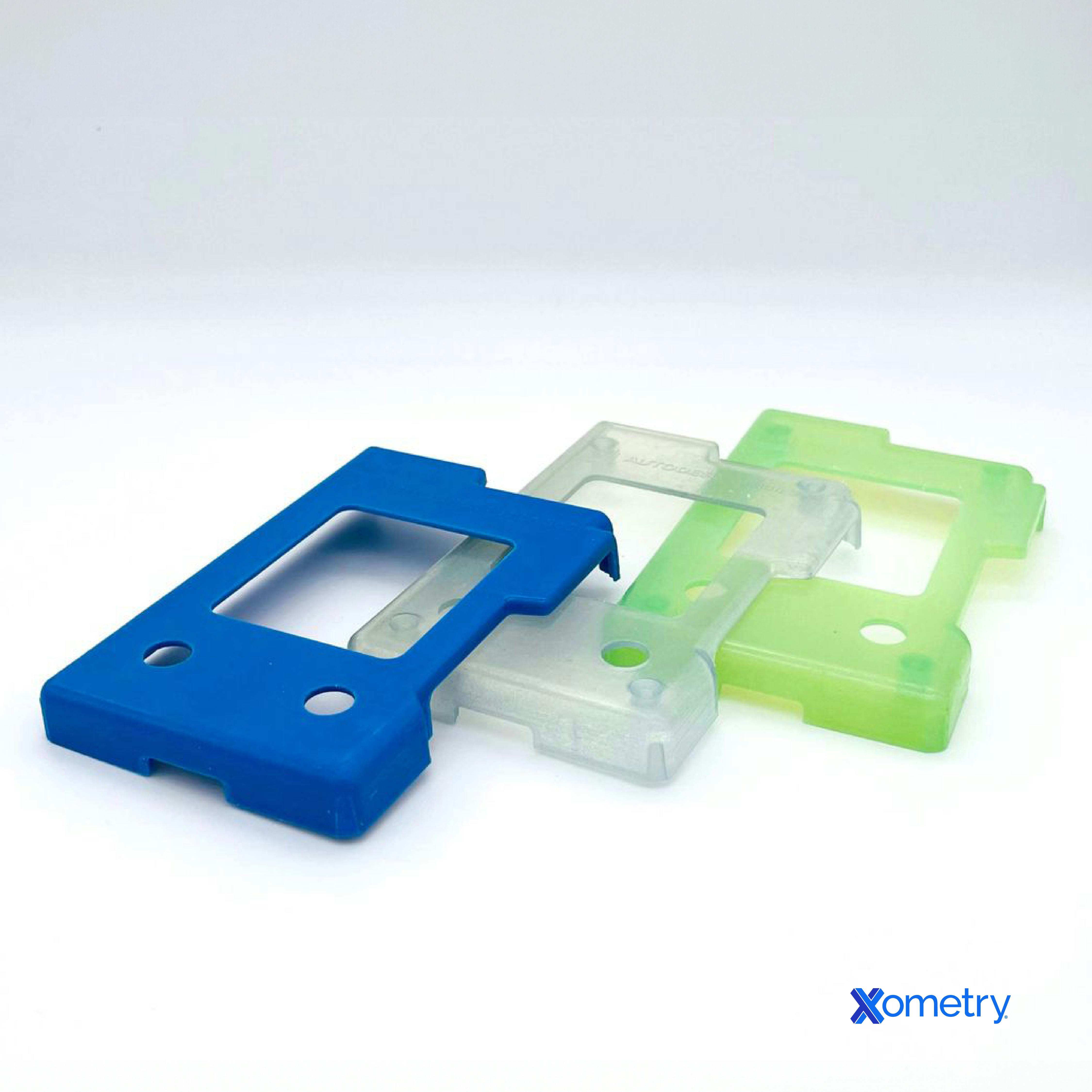
Advantages and Disadvantages of PolyJet Compared to FDM
PolyJet’s advantages over FDM include:
- PolyJet printed parts have considerably smoother surface finishes compared to FDM printed parts.
- PolyJet print heads accept a wide variety of material types. Multiple rigid, rubber, and lens/light pipe clear resins are available and can be employed in a single print session.
- PolyJet resolution is up to 10 times greater than FDM. This allows the printing of detailed features.
- PolyJet models are easy to repair using cyanoacrylate adhesives.
PolyJet has disadvantages compared to FDM, including:
- PolyJet machines are expensive to buy and hard to maintain.
- PolyJet materials are more expensive and much is wasted when cleaning the print head during and after builds.
- PolyJet prototypes generally cannot handle elevated temperatures and are prone to creep under load even at room temperature.
Attribute | FDM | PolyJet |
---|---|---|
Attribute Material costs | FDM $10/kg to $50/kg | PolyJet $200/kg to $500/kg |
Attribute Max print resolution | FDM 50 to 500 microns | PolyJet 16 to 45 microns |
Attribute Capital cost | FDM $50 to $250,000 | PolyJet $19,000 to $700,000 |
Attribute Can be easily maintained | FDM Yes | PolyJet No |
Attribute Capable of printing fine details | FDM No | PolyJet Yes |
Attribute Less wastage of materials | FDM Yes | PolyJet No |
Table. FDM vs. PolyJet Comparison
Comparisons to Consider When Considering FDM and Polyjet for Your Parts
Technology comparison: FDM is a simple process that delivers the general shape of 3D files. PolyJet, on the other hand, is a more intricate technology that delivers dimensionally accurate 3D representations, including fine details. FDM technology is nearing its upper limit of resolution because further improvements to single-point printing drive print times up to impractical levels. PolyJet has not reached its resolution limit and is still developing.
Material comparison: FDM prints using common polymers. A switch to a different material requires only a quick change in the printer’s settings, and raw material providers needn’t do anything special to it. Typically, FDM materials cost between $10 and $50 per kilogram. PolyJet materials, on the other hand, are complex, specialized resins. These materials may optimize strength, flexibility, transparency, and a range of other properties. PolyJet materials typically cost $200 to $500 per kilogram.
Applications comparison: FDM is the low-cost option that is suited to robust and simple components. Its models cannot be used for fine mechanical assessment, but the prints can be valuable as prototype representations of thicker, simpler parts. PolyJet is more expensive and is suited to engineering and cosmetic uses like: pre-tooling design checks, validation of grips/overmolds, tests of flexure, and assembly features. If hand-finished and painted, PolyJet parts can substitute for cosmetic and functional parts for trial and sales-sample builds.
Print volume comparison: The range of build volumes for FDM is impressive. The largest FDM machine (the Terabot) can print up to one cubic meter. The largest PolyJet machine has a 1000 x 800 mm table and a build height of 500 mm.
Surface finish comparison: FDM parts show visible layer steps in the Z-direction, each one generally 0.2 to 0.5 mm in height. This makes for a rough surface and is even more apparent on curved surfaces. PolyJet parts also show visible Z steps, but they are between 16 and 45 microns in height, less than 1/10th of FDM’s step size. Hand-finishing operations like sanding and even polishing can produce very smooth surface finishes (up to lens-level transparency).
Cost comparison: Both the equipment and printing material for FDM are cheaper by far than for PolyJet. The latter’s process also wastes as much as 20-40% of its resin. FDM parts are produced by many competing suppliers, so prices are consistently low. PolyJet parts, meanwhile, are more costly, making it a reasonable choice only when the highest quality or finest detail is necessary.
Similarities Between FDM and PolyJet
- FDM and PolyJet share the same principle of Z-axis layering using an orthogonal printer transport mechanism.
- Both offer a range of material properties that aim to represent those of manufactured parts. Thick FDM parts are strong in the X-Y axes but weaker in the Z direction due to imperfect intra-layer fusing. PolyJet parts are equally strong along all axes because of the nature of the material application.
- Both systems are office-friendly. The machines require a stable temperature environment and good ventilation.
Summary
Xometry provides a wide range of manufacturing capabilities including 3D printing services, injection molding, laser cutting, and sheet metal fabrication. Get your instant quote today.
Disclaimer
The content appearing on this webpage is for informational purposes only. Xometry makes no representation or warranty of any kind, be it expressed or implied, as to the accuracy, completeness, or validity of the information. Any performance parameters, geometric tolerances, specific design features, quality and types of materials, or processes should not be inferred to represent what will be delivered by third-party suppliers or manufacturers through Xometry’s network. Buyers seeking quotes for parts are responsible for defining the specific requirements for those parts. Please refer to our terms and conditions for more information.
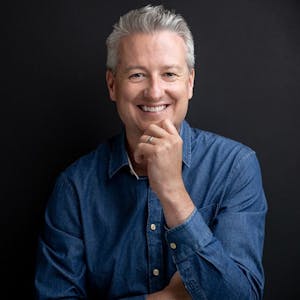