There is a simple divide in the 3D printer sector. The established market is mostly made up of machines that are carried within a motion system built into a frame or gantry, into which slide rails and drives are built. These are gantry machines. On the other hand, much of the industry favors larger-scale machines based on freestanding robot arms, which increase the potential build size while retaining a small footprint in the machine.
The benefit of robotic arm 3D printing only really shows up in larger builds, in which the build volume is defined by the reach of the arm rather than being confined within the rigid boundaries of a gantry. This article will further explore the differences between robotic arms vs gantry systems for 3D printing.
What Is a Robotic Arm for 3D Printing?
A robotic arm for 3D printing is a mechanical arm that differs significantly from the more common X-Y-Z orthogonal approach. Such an arm can be beneficial because the device is capable of moving in a wider range of directions and orientations. Therefore, this approach facilitates printing 3D objects using more degrees of freedom. For more information, see our 3D Printer Robotic Arm guide.
Figure 1 is an example of a robotic arm 3D printer:
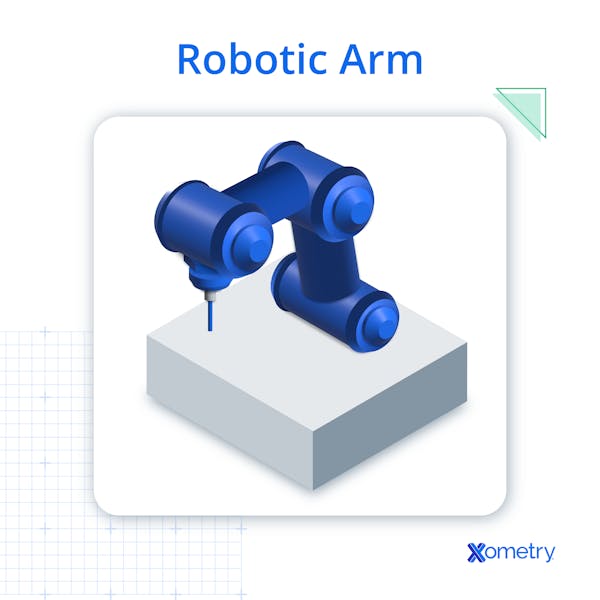
Robot arm 3D printing is not commonly used in making small parts. There are difficulties at a small scale that make orthogonal machines more practical. Robotic arms tend to be more costly than their gantry-based counterparts, especially at smaller scales.
In general, for printing larger parts in the automotive and aerospace sector, a robotic arm would be equipped with a 3D printing extruder printhead (FDM/FFF/FGF) or with a laser/TIG welder head.
Both of these can deposit material to create the final object. The arm is programmed to move the extruder in a precise pattern, depositing the material until the object is complete. However, an arm setup such as this can operate on an extrusion-based process that alters the layering to a more complex structure. This is because the extra degrees of freedom allow the arm to approach the print process in more complex ways (such as non-planar printing).
Robotic arm 3D printing can be used to print large objects and parts with complex geometries that would be difficult or impossible to create using orthogonal machines.
What Projects Can Robotic Arms Print?
Robot arm 3D printing adds degrees of flexibility that orthogonal machines cannot achieve. Some examples of what it can print are listed below:
- Large objects that are too big for typical 3D printers. Examples are large automotive parts, full-size furniture, architectural components, and entire buildings.
- By exchanging extruders, a robot arm printer can use multiple materials, different colors, or additives.
- Depending on the stiffness and quality of the device, robot arm printers can be highly precise in their movements. This maintains high precision while executing large or complex designs.
- Printing in unusual shapes and orientations is more achievable because of the extra degrees of freedom of motion. This can enable printing directly onto a curved surface (non-planar printing) or printing on the underside of builds.
- 3D printing with complex geometries is possible, as the arm can break off a material pass and continue from the other side of an obstruction. This allows the printing of interlocking objects that are often impossible to achieve with orthogonal 3D printing techniques.
The capabilities of robotic 3D printing are limited only by the size and stiffness of the arm, the accuracy and repeatability of its motion, and less by the complexity of the objects being printed.
What Are the Advantages of Robotic Arms for 3D Printing?
Various advantages of robot arm 3D printing over gantry/orthogonal machines are considered important, including:
- Print Area/Volume: This approach allows very large prints with a relatively small machine, limited only by the volume of its reach.
- Size: Smaller devices can deliver larger prints.
- Cost/size: While robot arms are not cheap, they are competitive with very large orthogonal printers of lesser capability.
- Geometry of Part: Robot arms offer much less restriction in build geometry because of their multi-axis access to the build.
- Anisotropic Control: The “grain” of the build can be selected by region, as strict uniaxial layering is not required. This allows part strength to be oriented variously for better overall robustness of prints.
What Are the Disadvantages of Robotic Arms for 3D Printing?
While robot arm 3D printing offers advantages over orthogonal printing methods, there are also disadvantages, including:
- Setting up robot 3D printing is expensive, the costs being prohibitive for smaller businesses or individuals.
- Robot 3D printing requires a considerably higher level of technical expertise than orthogonal/gantry printers, in terms of creating/executing print jobs and the initial hardware setup.
- Robots are not intrinsically guarded and can easily injure bystanders. Barriers and intrusion sensors must be used.
- Like all machines, robot arms require regular maintenance and occasional repairs. This is likely to be much more costly and time-consuming than for orthogonal/gantry 3D printers.
Does a Robotic Arm Have 6 Axes?
Yes, robot 3D printers often have six axes, but many robot arms have fewer degrees of freedom. A six-axis robot arm has six axes of movement: three rotational axes (roll, pitch, and yaw) and three translational axes (up-down, left-right, and forward-backward). Six-axis mobility is the norm in industrial robot arms that are used for 3D printing. Some robot 3D printers may have more than six axes (or fewer), depending on their intended application.
What Is a Gantry System for 3D Printing?
A gantry system for 3D printing is a structure consisting of beams and slide rails that support a printhead/extruder and guide its motion while transiting and printing. The critical functions are rigidity and precision, placing the print application point precisely within the build. The gantry system allows for a larger build height (and therefore volume) than delta or cartesian printers. Gantry systems are generally applicable to most 3D printing techniques. The Z-axis mechanism that allows for the print depth is either a result of a motion from the gantry, carrying a Z-axis mechanism—or from the movement of the build table on a separate mechanism.
Gantry systems are widespread in both industrial/professional and home/hobby machines because of their intrinsic stiffness and large build volume potential. Figure 2 is an example of a gantry system for 3D printing:

What Projects Can Gantry Systems Print?
Gantry-based printers can build most 3D models that will fit within their build volume, including:
- Some geometries, such as fully hollow structures with highly angled overhangs, can only be built by devices that include a removable support material option.
- Only one direction of the build is possible, as the roll/pitch/yaw capabilities of six-axis motion are not available, so material deposition is downwards only.
- Gantry-based 3D printers can tackle most builds if some post-print assembly is feasible.
Christian Tsu-Raun, a Team Lead, Manual Quoting here at Xometry, said, "In a gantry system, the axes are constrained to linear motion on rails, and the print is constrained to the volume created by the range of motion within that 'box'. Mechanical accuracy is defined by the step size of the motor, which is the same throughout the length of travel. In a robotic arm system, the print volume is dependent on the maximum hemispherical range of motion of the arm. Mechanical accuracy is defined by the angular change of the arm as the motors step, which results in larger inaccuracy as the print gets further from the arm itself. Both can print very large parts. Gantry printers are better suited for permanent equipment installation, as they need to be re-squared and recalibrated every time they are moved. Robotic arm printers are better for permanent print installation, as they can be moved to a location to print a part that is larger than the arm itself."
What Are the Advantages of Gantry Systems for 3D Printing?
Gantry-based systems have various advantages, including:
- Build volume is only limited by gantry size, which is only limited by stiffness. The same drive mechanisms can carry the same printhead over longer or shorter gantry arms with limited alteration.
- Size-up results in proportionately lower cost because the structure can be extended with little difficulty for larger machines.
- Setup and maintenance of gantry machines are relatively simple, as machine workings are well-exposed for access.
- Gantry-based machines offer a lower cost per build volume than other options.
What Are the Disadvantages of Gantry Systems for 3D Printing?
Gantry-based 3D printers have restrictions and weaknesses that must be considered, including:
- Machine stiffness can be limited, reducing accuracy, unless the machines are larger and heavier—i.e., with a full rectangular frame.
- Machine size is large compared with the build volume.
- The long, linear slide/drive systems are susceptible to wear and stretching, increasing the required maintenance.
- Unidirectional build orientation offers limited options in strength optimization.
Does a Gantry System Only Have 3 Axes?
For the most part, gantry-based systems have largely been limited to 3 axes. Recently there have been developments in adding additional axes to gantry-based 3D printers. Some feature a rotational 4th axis, while others have a tilting toolhead, enabling non-planar printing.
Common FAQs About Robotic Arms vs. Gantry Systems
What Is the Main Advantage of a Robotic Arm Over a Gantry System for 3D Printing?
The main advantage of the robotic arm over the gantry system for 3D printing is its long reach/large build volume in large prints. Moving a large orthogonal gantry printer to a building site will generally require it to be disassembled for transport, making site setup extremely challenging. A robot arm can retract to moderate size and be placed easily at the intended build location.
What Is the Main Advantage of a Gantry System Over a Robotic Arm for 3D Printing?
Gantry-based 3D printers cost less to purchase, operate, and maintain than robot arm-based machines.
Which 3D Printer Type Is Used for Construction?
Both gantry and robot arm 3D printer types are used for building construction, depending on a range of factors such as size. Build-in-place is more commonly performed by robot arm printers, whereas component manufacture at a fixed site is more practical using a gantry-based machine.
Which 3D Printer Type Is Used for Metal Printing?
Most metal 3D printers (especially those based on Powder Bed Fusion) utilize lasers and mirrors that rotate, directing the laser to the bed. They are neither robotic nor gantry-based systems. They generally operate in controlled environments with inert gases and are better suited for smaller parts.
However, certain metal-printing technologies, particularly those used for making larger parts, can use robotic arms. WAAM (Wire Arc Additive Manufacturing) systems often feature an arc welder mounted to a robotic arm.
The advantages of robot arm-based printing in larger machines make this a practical, but not common, option that the market is (and therefore machine manufacturers are) showing an increased interest in.
Do These 3D Printers Need Maintenance?
Yes, all 3D printers require extensive regular maintenance to deliver reliable precision. In some regards, 3D robot arm printers require less regular maintenance, but that maintenance is considerably more complex and expensive to perform.
Do These 3D Printers Have Limited Printable Area?
Most 3D printers have limitations in buildable areas, unless they have have mobility (such as the CyBe RT concrete 3D printer), or an “infinite” axis, in the form of a conveyor belt.
Can These 3D Printers Last Long?
Yes, 3D printers can last long if the maintenance is thorough and regular, and the required parts remain available. These machines will continue to function as long as they are cost-effective. Obsolescence comes quickly in this sector, as machines are surpassed in performance or undermined in print cost by new developments. So it is likely that the commercial viability of machines will be the deciding factor in their continued operation.
Summary
This article presented robotic arm vs. gantry systems in 3D printing, explained what each are, and discussed their various applications. To learn more about robotic arms and gantry systems, contact a Xometry representative.
Xometry provides a wide range of manufacturing capabilities, including 3D printing and other value-added services for all of your prototyping and production needs. Visit our website to learn more or to request a free, no-obligation quote.
Disclaimer
The content appearing on this webpage is for informational purposes only. Xometry makes no representation or warranty of any kind, be it expressed or implied, as to the accuracy, completeness, or validity of the information. Any performance parameters, geometric tolerances, specific design features, quality and types of materials, or processes should not be inferred to represent what will be delivered by third-party suppliers or manufacturers through Xometry’s network. Buyers seeking quotes for parts are responsible for defining the specific requirements for those parts. Please refer to our terms and conditions for more information.
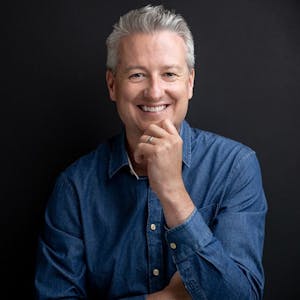